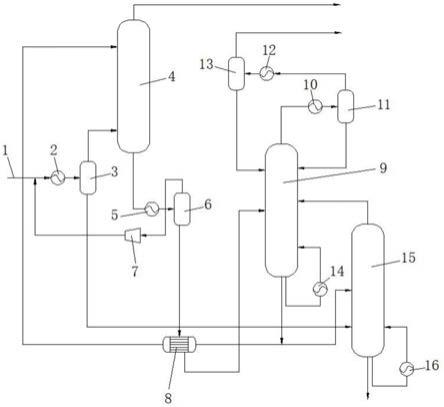
1.本发明属于粗合成气净化技术领域,具体涉及一种短流程的低温甲醇洗系统及其工艺。
背景技术:2.低温甲醇洗工艺在煤化工中广泛应用于煤制甲醇、煤制天然气、煤制合成氨的酸性气体脱除过程中,对二氧化碳和硫化物有着较好的选择性且处理量大、净化效率高。co2经过酸性气体脱除单元后,直接排放到环境中。甲醇是一种重要的基本化工原料,可用于合成烯烃、汽油、二甲醚等化工产品。近年来我国甲醇行业发展迅速,超过70%的甲醇来自于煤制甲醇工艺。目前煤制甲醇装置一般采用气化
→
水煤气变换
→
酸气脱除
→
甲醇合成的工艺流程。从煤炭元素的组成看,煤的氢/碳原子比为0.2~1.0,而甲醇合成所需合成气适宜氢碳比(简称h/c)约为2.1~2.2,所以煤制甲醇伴随着氢碳比的调整。为了调节h/c,需要通过变换单元将co和水转化成为co2和h2,该过程产生了大量的co2。传统煤制甲醇过程中,生产每吨甲醇需要排放2.66~3.56吨二氧化碳。巨大的碳排放不仅造成严重的环境污染,而且增加了企业碳税负担。
3.传统低温甲醇洗工艺主要包括原料气分离器、酸气吸收塔、co2富甲醇闪蒸塔、h2s富集塔、h2s解吸塔和甲醇水分离塔。传统低温甲醇洗工艺主要存在以下不足:
4.(1)全流程只用低温甲醇作为吸收剂,甲醇循环量大,造成整个系统公用工程用量大,并且用于循环的甲醇溶液冷却所需的冷量很大,能耗高,运行成本高;
5.(2)co2解吸塔能耗较高,为了降低co2解吸塔能耗,传统低温甲醇洗工艺co2解吸塔的解吸率不能设置过高,导致h2s富集塔塔顶尾气中的co2含量高,尾气排放至大气中造成co2的排放量高;
6.(3)汽提塔采用n2汽提,不仅增加了物耗,而且使废气中掺杂大量的n2,不利于co2的分离与回收。
7.综上所述,本发明开发了一种短流程的低温甲醇洗系统及其工艺,用于脱除粗合成气中含硫气体,并尽可能降低co2的脱除率,提高过程的碳元素利用率和经济效益。
技术实现要素:8.本发明所要解决的技术问题在于针对上述现有技术的不足,提供一种短流程的低温甲醇洗系统及其工艺,以解决上述背景技术中提出的问题。
9.为解决上述技术问题,本发明采用的技术方案是:一种短流程的低温甲醇洗系统,包括进气口和原料分离器,所述进气口连通有第一换热器,所述第一换热器与原料气分离器连通,所述原料分离器的气相出口与脱硫塔的底部相连,所述原料气分离器的液相出口与甲醇水分离塔相连;
10.所述的脱硫塔塔顶设置有净合成气出口,所述脱硫塔的塔釜通过第二换热器连通有第一闪蒸器相连,所述第一闪蒸器底部通过第三换热器连通有h2s解吸塔;
11.所述h2s解吸塔的塔顶设有回流流路,所述回流流路包括第四换热器、第二闪蒸器、第五换热器和第三闪蒸器,所述h2s解吸塔的塔顶连通有第四换热器,所述第四换热器连通有第二闪蒸器,所述第二闪蒸器分别与h2s解吸塔和第五换热器连通,所述第五换热器连通有第三闪蒸器,所述第三闪蒸器顶端设置有含硫气体出口,所述第三闪蒸器底部与h2s解吸塔连通;
12.所述甲醇水分离塔塔顶气相与h2s解吸塔相连,所述甲醇水分离塔塔底液相为废水口。
13.进一步的,所述第一闪蒸器顶部连通有压缩机,所述第一闪蒸器顶部通过压缩机与进气口连通。
14.进一步的,所述h2s解吸塔的塔底连通有第六换热器,所述甲醇水分离塔的塔底连通有第七换热器。
15.一种短流程的低温甲醇洗工艺,包括以下步骤;
16.s1、粗合成气通过进气口进入,经过第一换热器换热和原料分离器分离,进入脱硫塔底部,并与脱硫塔塔顶流下的低温甲醇逆流接触,其中的酸性气体被低温甲醇吸收,通过控制贫液甲醇循环量来控制含硫气体净化深度;
17.s2、脱硫塔塔顶采出净合成气,脱硫塔塔釜h2s甲醇富液经第二换热器冷却,减压后进入第一闪蒸器,经第一闪蒸器闪蒸分离出未被吸收的h2s气体循环至脱硫塔,液相则经过第三换热器后直接进入h2s解吸塔;
18.s3、h2s解吸塔塔顶蒸汽经过回流流路冷却、闪蒸后得到含硫混合气;
19.s4、h2s解吸塔塔底液相一部分循环至酸气吸收塔,另一部分则进入甲醇水分离塔,甲醇水分离塔塔顶温度为98.0℃,操作压力为0.3mpa,h2s解吸塔塔顶蒸汽进入h2s浓缩塔,h2s解吸塔塔釜分离出液相废水。
20.本发明与现有技术相比具有以下优点:
21.本发明粗合成气的净化过程侧重于脱硫,并尽可能降低co2的脱除率。降低了低温甲醇的循环量,使得循环甲醇溶液冷却所需的冷量显著降低。同时也显著降低了过程冷凝水、蒸汽和电等公用工程的使用,提高了能量效率,省去了吸收塔脱碳段、co2富甲醇闪蒸塔、co2解吸塔和h2s富集塔等设备,使得流程结构更加简单,投资费用和净化酸性气体的成本明显减少,降低了过程温室气体的排放,提高了碳利用率。
附图说明
22.图1是本发明流程示意图。
23.附图标记说明:
24.1-进气口;2-第一换热器;3-原料分离器;4-脱硫塔;5-第二换热器;6-第一闪蒸器;7-压缩机;8-第三换热器;9-h2s解吸塔;10-第四换热器;11-第二闪蒸器;12-第五换热器;13-第三闪蒸器;14-第六换热器;15-甲醇水分离塔;16-第七换热器。
具体实施方式
25.下面将结合本发明实施例中的附图,对本发明实施例中的技术方案进行清楚、完整地描述,显然,所描述的实施例仅仅是本发明一部分实施例,而不是全部的实施例。基于
本发明中的实施例,本领域普通技术人员在没有做出创造性劳动前提下所获得的所有其他实施例,都属于本发明保护的范围。
26.如图1所示,本发明提供一种技术方案:一种短流程的低温甲醇洗系统,包括进气口1和原料分离器3,所述进气口1连通有第一换热器2,所述第一换热器2与原料气分离器3连通,所述原料分离器3的气相出口与脱硫塔4的底部相连,所述原料气分离器3的液相出口与甲醇水分离塔15相连。
27.所述的脱硫塔4塔顶设置有净合成气出口,所述脱硫塔4的塔釜通过第二换热器5连通有第一闪蒸器6相连,所述第一闪蒸器6顶部连通有压缩机7,所述第一闪蒸器6顶部通过压缩机7与进气口1连通。
28.所述第一闪蒸器6底部通过第三换热器8连通有h2s解吸塔9,所述h2s解吸塔9的塔底连通有第六换热器14。
29.所述h2s解吸塔9的塔顶设有回流流路,所述回流流路包括第四换热器10、第二闪蒸器11、第五换热器12和第三闪蒸器13,所述h2s解吸塔9的塔顶连通有第四换热器10,所述第四换热器10连通有第二闪蒸器11,所述第二闪蒸器11分别与h2s解吸塔9和第五换热器12连通,所述第五换热器12连通有第三闪蒸器13,所述第三闪蒸器13顶端设置有含硫气体出口,所述第三闪蒸器13底部与h2s解吸塔9连通;
30.所述甲醇水分离塔15塔顶气相与h2s解吸塔9相连,所述甲醇水分离塔15塔底液相为废水口。
31.所述甲醇水分离塔15的塔底连通有第七换热器16。
32.上述的短流程的低温甲醇洗系统的低温甲醇洗工艺,包括以下步骤;
33.s1、粗合成气通过进气口1进入,经过第一换热器2换热和原料分离器3分离,进入脱硫塔4底部,并与脱硫塔4塔顶流下的低温甲醇逆流接触,其中的酸性气体被低温甲醇吸收,通过控制贫液甲醇循环量来控制含硫气体净化深度;
34.s2、脱硫塔4塔顶采出净合成气,脱硫塔4塔釜h2s甲醇富液经第二换热器5冷却,减压后进入第一闪蒸器6,经第一闪蒸器6闪蒸分离出未被吸收的h2s气体循环至脱硫塔4,液相则经过第三换热器8后直接进入h2s解吸塔9;
35.s3、h2s解吸塔9塔顶蒸汽经过回流流路冷却、闪蒸后得到含硫混合气;
36.s4、h2s解吸塔9塔底液相一部分循环至酸气吸收塔,另一部分则进入甲醇水分离塔15,甲醇水分离塔塔顶温度为98.0℃,操作压力为0.3mpa,甲醇水分离塔15塔顶蒸汽进入h2s解吸塔,甲醇水分离塔15塔釜分离出液相废水。
37.实验例1,17337.5kmol/h的粗合成气,其中co2和h2s气体的摩尔含量分别为32.859和0.289mol.%,经过低温甲醇洗工艺净化后,净合成气中h2s气体含量≤0.1ppm,co2含量不限定。
38.粗合成气进入脱硫塔4底部,并与塔顶流下的-15℃的低温甲醇逆流接触,其中的酸性气体co2和h2s等被低温甲醇吸收,通过控制贫液甲醇循环量来控制含硫气体净化深度。
39.脱硫塔4塔顶温度为-15℃,压力为5.54mpa,塔顶采出净合成气,脱硫塔塔釜h2s甲醇富液经第一换热器5冷却、减压后进入第一闪蒸器6,经第一闪蒸器6闪蒸分离出未被吸收的h2s气体循环至脱硫塔4,液相则经过第二换热器8后直接进入h2s解吸塔9;
40.h2s解吸塔9操作温度为95℃,压力为0.3mpa。
41.h2s解吸塔9塔顶蒸汽经过冷却、闪蒸后得到h2s的混合气。
42.h2s解吸塔9塔底液相一部分循环至酸气吸收塔,另一部分则进入甲醇水分离塔15,甲醇水分离塔15塔顶温度为98.0℃,操作压力为0.3mpa,甲醇水分离塔15塔顶蒸汽进入h2s解吸塔,甲醇水分离塔15塔釜则分离出液相废水。
43.其中,进气口、废水口、净合成气出口和含硫气体出口中的温度、压力、摩尔流量和各组分摩尔分数分析结果如下表所示:
[0044][0045]
对比例1,17337.5kmol/h的粗合成气,其中co2和h2s气体的摩尔含量分别为32.859和0.289mol.%进入酸气吸收塔底部。经过低温甲醇洗工艺净化后,净合成气中h2s气体含量≤0.1ppm,co2<5%。
[0046]
将粗合成气从塔底送入酸气吸收塔4中,并与塔顶流下的-53.5℃低温甲醇逆流接触,其中的酸性气体co2和h2s等被低温甲醇吸收,酸气吸收塔塔顶获得净合成气,净合成气的压力为2.86mpa,温度为-45℃,并直接输送出低温甲醇洗系统。
[0047]
酸气吸收塔4分为脱碳段和脱硫段,脱碳段底部得到富co2溶液,经过冷却器将物流冷却至-36.0℃,然后进入闪蒸塔中闪蒸,分离出未被低温甲醇吸收的酸性气体循环至酸气吸收塔,液相则进入闪蒸塔中分离出co2气体,液相则进入后续的co2解吸塔12和h2s富集塔。脱硫塔底部h2s富甲醇溶液温度为-47.0℃,经过换热器换热后温度为-28.0℃。
[0048]
h2s富甲醇闪蒸塔操作压力为1.3mpa,气相循环至酸气吸收塔,液相则进入co2解吸塔,解吸塔流股进入闪蒸塔,闪蒸塔塔顶得到0.05mpa、-51.0℃的co2产品气,co2浓度可达到98.036mol.%。co2解吸塔塔釜液相进入h2s富集塔,h2s富集塔操作温度为-37.0℃,压力为0.03mpa,塔顶气体进入尾气处理系统进行处理,塔釜得到的富含硫甲醇溶液进入h2s解吸塔。h2s解吸塔操作温度为95.0℃,压力为0.31mpa。h2s解吸塔塔顶蒸汽经过冷却、闪蒸后得到h2s的混合气。h2s解吸塔塔底液相一部分循环至酸气吸收塔,另一部分则进入甲醇水分离塔24,甲醇水分离塔操作条件同实施例1。其中的温度、压力、摩尔流量和各组分摩尔分数分
析结果如下表所示,1为粗合成气,27为净合成气,28为co2气体,29为尾气,30为含硫气体,31为废水:
[0049][0050]
对比可以发现,实验例1中co、co2和h2流量分别为3540.183、3987.900和7965.530kmol/h,对比例1净合成气中co、co2和h2流量分别为3414.822、322.318和7871.808kmol/h。
[0051]
实验例1和对比例1中有效气(co+co2+h2)摩尔流量分别为15493.61kmol/h和11608.95kmol/h,实验例1较对比例1有效气流量增加约33.46%。
[0052]
经计算,实验例1中进入脱硫塔4的贫液甲醇用量为5737kmol/h,
[0053]
对比例1中进入酸气吸收塔4的贫液甲醇用量为15100kmol/h,实施例1较对比例1贫液甲醇用量降低约62.01%。
[0054]
实验例2,粗合成气流量为6616.3kmol/h,其中co2和h2s气体的摩尔含量为18.62和0.085mol.%,实验例2具体详细描述同实验例1。进气口、废水口、净合成气出口和含硫气体出口中的温度、压力、摩尔流量和各组分摩尔分数分析结果如下表所示:
[0055][0056]
对比例2对比例2中粗合成气进料条件和组成同实验例2,对比例2具体详细描述同
对比例1,1为粗合成气,27为净合成气,28为co2气体,29为尾气,30为含硫气体,31为废水,其中的温度、压力、摩尔流量和各组分摩尔分数分析结果如下表所示:
[0057][0058][0059]
对比可以发现,实验例2中co、co2和h2流量分别为1834.140、1123.991和3470.677kmol/h,对比例2中co、co2和h2流量分别为1841.773、0.048和3480.128kmol/h。实验例2和对比例2净合成气中有效气(co+co2+h2)摩尔流量分别为6428.81kmol/h和5320.95kmol/h,实验例2较对比例2有效气流量增加约20.80%。
[0060]
经计算,实验例2中进入脱硫塔4的贫液甲醇用量为2256kmol/h,
[0061]
对比例2中进入酸气吸收塔4的贫液甲醇用量为6485kmol/h,实验例2较对比例2贫液甲醇用量降低约65.21%。
[0062]
实验例3粗合成气流量为9841.30kmol/h,co2和h2s气体的摩尔含量分别为4.03和0.10mol.%,实验例3具体详细描述同实验例1。进气口、废水口、净合成气出口和含硫气体出口中的温度、压力、摩尔流量和各组分摩尔分数分析结果如下表所示;
[0063][0064]
对比例3,对比例3中粗合成气进料条件和组成同实验例3,对比例3具体详细描述同对比例1,1为粗合成气,27为净合成气,28为co2气体,29为尾气,30为含硫气体,31为废
水,其中的温度、压力、摩尔流量和各组分摩尔分数分析结果如下表所示:
[0065]
流股12728293031温度(℃)12.22-45.0-51.0-37.077.3139.1压力(mpa)3.102.860.050.030.20.25摩尔分数(%)
ꢀꢀꢀꢀꢀꢀ
n20.580.6482.57865.49210.2920co62.6570.0901.2780.0170.5760co24.030.00194.04722.97248.6210h2s0.1000040.5110h226.1329.2152.096000ch3oh000000.01h2o6.51002.455957099.99摩尔流量(koml/h)9841.308794.15110.71221.5224.29610.73
[0066]
对比可以发现,实验例3中co、co2和h2流量分别为6176.312、281.854和2577.466kmol/h,对比例3中co、co2和h2流量分别为6163.820、0.0880和2569.211kmol/h。实验例3和对比例3净合成气中有效气(co+co2+h2)摩尔流量分别为9035.63kmol/h和8733.09kmol/h,实验例3较对比例3有效气流量增加3.46%。
[0067]
经计算,实验例3中进入脱硫塔4的贫液甲醇用量为3151kmol/h,对比例3中进入酸气吸收塔4的贫液甲醇用量为9592kmol/h,实验例3较对比例3贫液甲醇用量降低约67.15%。
[0068]
处理一吨粗合成气,本发明的短流程低温甲醇洗工艺装置较传统低温甲醇洗工艺装置冷、热公用工程消耗降低40~70%,处理单位粗合成气固定投资降低30~60%。
[0069]
需要说明的是,在本文中,诸如第一和第二等之类的关系术语仅仅用来将一个实体或者操作与另一个实体或操作区分开来,而不一定要求或者暗示这些实体或操作之间存在任何这种实际的关系或者顺序。而且,术语“包括”、“包含”或者其任何其他变体意在涵盖非排他性的包含,从而使得包括一系列要素的过程、方法、物品或者设备不仅包括那些要素,而且还包括没有明确列出的其他要素,或者是还包括为这种过程、方法、物品或者设备所固有的要素。
[0070]
尽管已经示出和描述了本发明的实施例,对于本领域的普通技术人员而言,可以理解在不脱离本发明的原理和精神的情况下可以对这些实施例进行多种变化、修改、替换和变型,本发明的范围由所附权利要求及其等同物限定。