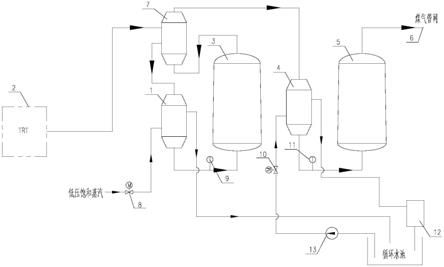
1.本实用新型属于高炉煤气精脱硫技术领域,具体涉及一种高炉煤气低温干法精脱硫系统。
背景技术:2.高炉炼铁是现代炼铁的主要方法,钢铁生产的重要环节。高炉在冶炼过程中将产生大量高炉煤气,高炉煤气的主要成分二氧化碳6-12%,甲烷0.2-0.5%,一氧化碳28-33%,氢气1-4%,氮气55-60%,热值780~980kcal/nm3;脱硫前h2s含量20-70mg/nm3,cos含量60-150mg/nm3。
3.高炉煤气作为炼铁过程中的二次能源,在钢铁企业中有着最为广泛的应用。高炉煤气直接作为燃料主要用于热风炉、炼焦炉、烧结、球团、石灰窑、轧钢、加热炉和高炉煤气发电等设施。高炉煤气中硫的存在有两种形态:有机硫(cos、cs2等)和无机硫(h2s),这两种形态的硫化物燃烧后会转化为so2和so3,形成酸雨,导致环境污染,使上述设施的排放不能达到国家排放标准。在没有高炉煤气精脱硫之前,一般上述设施会分别设置末端脱硫装置来达到国家排放标准,由于高炉煤气用户分布极为分散,上述设施采用末端脱硫装置,会造成投资大、占地多、建设难度大、运行成本高等问题。因此,采用高炉煤气源头精脱硫的方法,是解决上述问题的最佳方法。
4.为了解决末端脱硫装置治理上存在的问题,现有高炉煤气精脱硫方法,主要分湿法和干法二种:
5.如中国专利:cn110643395a“一种高炉煤气精脱硫工艺”,该专利所描述工艺路线为:高炉煤气除尘系统
→
有机硫水解转化
→
余压发电
→
湿法碱洗塔
→
煤气管网。该工艺存在以下不足:(1)有机硫水解转化置于余压发电之前,而湿法脱硫置于余压发电之后,水解转化后煤气中h2s含量将增大,这将加重余压发电设施及其附属管道的腐蚀或积盐;(2)采用湿法碱洗塔后会增加高炉煤气中的水分,降低高炉煤气的热値;(3)系统复杂,占地大,能耗高,运行成本较高。
6.如中国专利:cn110387270a“高炉煤气干法脱硫系统及方法”,采用的是中温精脱硫方法,该专利所描述工艺路线为:高炉
→
干法粗除尘器
→
前置粉料脱硫装置
→
干法精除尘器
→
有机硫转化塔
→
第二级干法脱硫装置
→
粉料补集器
→
trt余压发电。该工艺存在以下不足:(1)该工艺脱硫分两级,除尘三级,系统复杂,设备较多,投资较多。(2)该工艺的脱硫装置适应性有待验证,目前主要问题是:脱硫温度大于100℃,脱硫温度超过100℃后的脱硫催化剂产品还在研究中。
7.还有一种高炉煤气干法脱硫方法,采用的工艺路线为:高炉煤气除尘系统
→
trt余压发电
→
微晶吸附脱硫
→
煤气管网。该方法主要存在投资大、能耗高等不足。
技术实现要素:8.本实用新型的目的在于提供一种高炉煤气低温干法精脱硫系统,解决现有技术中
高炉煤气干法脱硫方法投资大、能耗高等技术问题。
9.本实用新型公开了一种高炉煤气低温干法精脱硫系统,包括第一换热器,所述第一换热器入口连接有第二换热器出口,所述第二换热器入口连接有trt,所述第一换热器出口连接有精除尘水解一体塔,所述精除尘水解一体塔的出口与所述第二换热器的换热介质入口连接,所述第二换热器的换热介质出口连接有冷却器入口,所述冷却器出口连接有脱硫塔入口,所述脱硫塔出口连接煤气管网。
10.工作原理:
11.trt排出30℃~50℃的高炉煤气时,进入第二换热器与精除尘水解一体塔出口的70℃~90℃高炉煤气进行换热,第二换热器中换热后高炉煤气温度提升至55℃~70℃,然后高炉煤气进入第一换热器加热,然后进入精除尘水解一体塔进行除尘水解,精除尘水解一体塔排出的高炉煤气在第二换热器进行换热后温度降至55℃~60℃,然后进入冷却器冷却,将高炉煤气冷却至35℃~45℃,35℃~45℃高炉煤气进入脱硫塔,在塔内实现h2s向单质s的转化,并将单质s吸附脱出,达到脱硫的目的。脱硫塔净化处理后出口的高炉煤气送入煤气管网。通过将精除尘水解一体塔的出口与第二换热器的换热介质入口连接,精除尘水解一体塔出口70℃~90℃的高炉煤气可以充当第二换热器的换热介质,减少了能量的消耗,并能降低进入冷却器的煤气温度。通过设置第一换热器,对高炉煤气升温,高炉煤气温度由55℃~70℃提升至70℃~90℃,保证进入精除尘水解一体塔的煤气温度为70℃~90℃。精除尘水解一体塔除把煤气中有机硫转化为硫化氢外,还能进一步清除煤气中粉尘,保证煤气中粉尘含量小于5mg/nm3,可以保证下游用户(热风炉、加热炉、燃气炉等)燃烧后的粉尘含量小于5mg/m3达到排放要求,不需再上除尘设备。
12.进一步的,所述第二换热器为ggh换热器。
13.通过设置ggh换热器,trt排出的高炉煤气温度为30℃~45℃时,能够提高进入换热器的高炉煤气温度,节省换热器的低压饱和蒸汽耗量或高温热水耗量。
14.进一步的,所述第一换热器为螺旋翅片管碳钢换热器。
15.进一步的,所述第一换热器上设置有第一流量调节阀。
16.通过设置第一流量调节阀,根据进入第一换热器的煤气温度变化,调节低压饱和蒸汽的流量或高温热水流量控制进入精除尘水解一体塔的高炉煤气温度,使进入精除尘水解一体塔的煤气温度保持为70℃~90℃。
17.进一步的,所述第一换热器与所述精除尘水解一体塔之间设置有第一温度控制装置。
18.通过设置第一温度控制装置,可以监控进入精除尘水解一体塔的煤气温度,并根据第一温度控制装置反馈的温度调节第一流量调节阀进入换热器的低压饱和蒸汽的流量或高温热水流量,使进入精除尘水解一体塔的高炉煤气温度保持为70℃~90℃。
19.进一步的,所述精除尘水解一体塔内装填水解剂和除尘剂。
20.高炉煤气在精除尘水解一体塔内先进行除尘然后进行水解,高炉煤气中有机硫在水解剂的催化下转化为硫化氢。
21.进一步的,所述脱硫塔内填充脱硫剂。
22.高炉煤气中硫化氢在脱硫剂的催化下转化为单质硫并被吸附。
23.进一步的,所述冷却器为非金属防静电板式换热器。
24.进一步的,所述冷却器换热介质进口前设置有第二流量调节器。
25.通过设置第二流量调节器,根据煤气温度变化,调节循环水冷却水的流量控制进入脱硫塔的高炉煤气温度。
26.进一步的,所述冷却器与所述脱硫塔之间设置有第二温度控制装置。
27.通过设置第二温度控制装置,可以监控进入脱硫塔的煤气温度,并根据第二温度控制装置反馈的温度调节进入冷却器的循环水冷却水的流量,使进入脱硫塔前的高炉煤气温度保持为35℃~45℃。
28.进一步的,所述冷却器的换热介质出口连接有冷却塔,所述冷却塔为机械通风冷却塔。
29.进一步的,所述冷却器换热介质进口前设置有循环水泵,所述循环水泵为变频水泵。
30.采用变频调节,跟据热负荷的变化,调节循环水的总流量,节约用电。
31.一种高炉煤气低温干法精脱硫方法,包括以下步骤:
32.s1.高炉煤气输送至换热器进行换热,使高炉煤气温度在保持为70℃~90℃;
33.s2.换热后的高炉煤气先进行除尘再进行水解;
34.s3.将水解后的气体降温至35℃~45℃,送入进行脱硫,脱硫后进入煤气管网。
35.进一步的,所述水解后的气体先通入换热器充当换热介质,再进行冷却。
36.进一步的,所述水解使用的水解剂为氧化铝基材的低温催化剂。
37.有机硫转化原理:cos+h2o=h2s+co2,cs2+2h2o=2h2s+co2,水解效率≥95%。使用后的铝基基材水解剂,经磨粉后成为水泥原料,实现循环利用。
38.进一步的,所述脱硫使用的脱硫剂为活性炭基材附着催化剂。
39.脱硫剂适应温度区间为35℃~45℃,为低温脱硫剂,硫容量高达300mg/g。脱硫剂附着催化剂把硫化氢转化为单质硫,活性炭吸附转化后的单质硫,硫化氢脱除原理:2h2s+o2=2s+2h2o。脱硫效率≥98%,从而达到脱硫的目的。
40.本实用新型的有益效果为:
41.1.本干法精脱硫系统所以设备均在trt后布置,相较于trt前布置压力大于0.1mpa需要按压力容器进行设计、制造、验收,系统压力小于30kpa属于常压容器,投资成本较低,煤气泄露危险性也更低,对trt运行影响较小;
42.2.能够灵活适应trt后的煤气温度30-120℃全区间;
43.3.采用精除尘水解一体塔,转化有机硫为硫化氢的同时进一步降低煤气含尘量,可以保证下游用户(热风炉、加热炉、燃气炉等)燃烧后的粉尘含量小于5mg/m3达到排放要求,不需再上除尘设备;
44.4.全程采用干法,无水进入煤气系统,不降低煤气热值;
45.5.脱硫塔前煤气降温至35℃~45℃,煤气中水析出,通过排水器排出,降低煤气含水率低,提高煤气热值;
46.6.使用后的水解剂和脱硫剂,不属于危废,可再利用,实现闭环环保。
附图说明
47.为了更清楚地说明本实用新型实施方式的技术方案,下面将对实施方式中所需要
使用的附图作简单地介绍,应当理解,以下附图仅示出了本实用新型的某些实施方式,因此不应被看作是对范围的限定,对于本领域普通技术人员来讲,在不付出创造性劳动的前提下,还可以根据这些附图获得其他相关的附图。
48.图1是本实用新型高炉煤气低温干法精脱硫系统结构示意图。
49.上述附图中,各个标记所表示的含义为:1-第一换热器,2-trt,3-精除尘水解一体塔,4-冷却器,5-脱硫塔,6-煤气管网,7-第二换热器,8-第一流量调节阀,9-第一温度控制装置,10-第二流量调节器,11-第二温度控制装置,12-冷却塔,13-循环水泵。
具体实施方式
50.下面结合实施例和附图对本实用新型作进一步详细说明。
51.一种高炉煤气低温干法精脱硫方法,包括以下步骤:
52.s1.高炉煤气输送至换热器进行换热,使高炉煤气温度在保持为70℃~90℃;
53.s2.换热后的高炉煤气先进行除尘再进行水解,水解使用的水解剂为氧化铝基材的低温催化剂;
54.s3.将水解后的气体先通入换热器充当换热介质,再进行冷却,降温至35℃~45℃,送入进行脱硫,脱硫后进入煤气管网,脱硫使用的脱硫剂为活性炭基材附着催化剂。
55.有机硫转化原理:cos+h2o=h2s+co2,cs2+2h2o=2h2s+co2,水解效率≥95%。使用后的铝基基材水解剂,经磨粉后成为水泥原料,实现循环利用。
56.脱硫剂适应温度区间为35℃~45℃,为低温脱硫剂,硫容量高达300mg/g。脱硫剂附着催化剂把硫化氢转化为单质硫,活性炭吸附转化后的单质硫,硫化氢脱除原理:2h2s+o2=2s+2h2o。脱硫效率≥98%,从而达到脱硫的目的。
57.实施例1
58.使用上述方法的一种高炉煤气低温干法精脱硫系统,其具体结构如图1所示,包括第一换热器1,所述第一换热器1入口连接有第二换热器7出口,所述第二换热器7入口连接有trt2,所述第一换热器1出口连接有精除尘水解一体塔3,所述精除尘水解一体塔3的出口与所述第二换热器7的换热介质入口连接,所述第二换热器7的换热介质出口连接有冷却器4入口,所述冷却器4出口连接有脱硫塔5入口,所述脱硫塔5出口连接煤气管网6。
59.工作原理:
60.trt2排出30℃~50℃的高炉煤气时,进入第二换热器7与精除尘水解一体塔3出口的70℃~90℃高炉煤气进行换热,第二换热器7中换热后高炉煤气温度提升至55℃~70℃,然后高炉煤气进入第一换热器1加热,然后进入精除尘水解一体塔3进行除尘水解,精除尘水解一体塔3排出的高炉煤气在第二换热器7进行换热后温度降至55℃~60℃,然后进入冷却器4冷却,将高炉煤气冷却至35℃~45℃,35℃~45℃高炉煤气进入脱硫塔5,在塔内实现h2s向单质s的转化,并将单质s吸附脱出,达到脱硫的目的。脱硫塔5净化处理后出口的高炉煤气送入煤气管网6。通过将精除尘水解一体塔3的出口与第二换热器7的换热介质入口连接,精除尘水解一体塔3出口70℃~90℃的高炉煤气可以充当第二换热器7的换热介质,减少了能量的消耗,并能降低进入冷却器4的煤气温度。通过设置第一换热器1,对高炉煤气升温,高炉煤气温度由55℃~70℃提升至70℃~90℃,保证进入精除尘水解一体塔3的煤气温度为70℃~90℃。精除尘水解一体塔3除把煤气中有机硫转化为硫化氢外,还能进一步清除
煤气中粉尘,保证煤气中粉尘含量小于5mg/nm3,可以保证下游用户(热风炉、加热炉、燃气炉等)燃烧后的粉尘含量小于5mg/m3达到排放要求,不需再上除尘设备。
61.实施例2
62.在本实施方式作为本实用新型的一较佳实施例,具体结构如图1所示,其在实施方式1的基础上公开了如下改进,所述第二换热器7为ggh换热器。
63.通过设置ggh换热器,trt排出的高炉煤气温度为30℃~45℃时,能够提高进入换热器的高炉煤气温度,节省换热器的低压饱和蒸汽耗量或高温热水耗量。
64.实施例3
65.在本实施方式作为本实用新型的一较佳实施例,具体结构如图1所示,其在实施方式2的基础上公开了如下改进,第一换热器1上设置有第一流量调节阀8,第一换热器1与精除尘水解一体塔3之间设置有第一温度控制装置9,精除尘水解一体塔3内装填水解剂和除尘剂,脱硫塔5内填充脱硫剂,冷却器4换热介质进口前设置有第二流量调节器10,冷却器4与脱硫塔5之间设置有第二温度控制装置11,冷却器4的换热介质出口连接有冷却塔12,冷却塔12为机械通风冷却塔12,冷却器4换热介质进口前设置有循环水泵13,循环水泵13为变频水泵。
66.通过设置第一流量调节阀8,根据进入第一换热器1的煤气温度变化,调节低压饱和蒸汽的流量或高温热水流量控制进入精除尘水解一体塔3的高炉煤气温度,使进入精除尘水解一体塔3的煤气温度保持为70℃~90℃。
67.通过设置第一温度控制装置9,可以监控进入精除尘水解一体塔3的煤气温度,并根据第一温度控制装置9反馈的温度调节第一流量调节阀8进入换热器的低压饱和蒸汽的流量或高温热水流量,使进入精除尘水解一体塔3的高炉煤气温度保持为70℃~90℃。通过设置第二流量调节器10,根据煤气温度变化,调节循环水冷却水的流量控制进入脱硫塔5的高炉煤气温度。
68.通过设置第二温度控制装置11,可以监控进入脱硫塔5的煤气温度,并根据第二温度控制装置11反馈的温度调节进入冷却器4的循环水冷却水的流量,使进入脱硫塔5前的高炉煤气温度保持为35℃~45℃。
69.表1实施例3与不使用ggh换热器能耗对比表
[0070][0071]
从表1中可以看出,本实用新型可以节约企业生产成本,减少能耗,促进绿色发展。