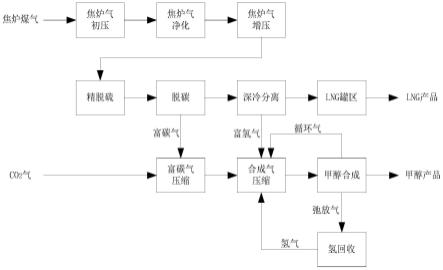
一种焦炉煤气补入co2制备甲醇和lng的工艺
技术领域
1.本发明属于焦炉煤气综合利用技术领域,特别涉及一种焦炉煤气补入co2制备甲醇和lng的工艺。
背景技术:2.焦炉煤气是焦化过程中的一种重要副产物,其气体组成主要是h2(50%~59%),ch4(20%~26%),以及少量n2(2%~4%)、o2(0.3%~0.8%)、不饱和烃类(2%~2.5%)、co(6%~12%)和co2(1.5%~4%)。既可作为燃料气使用,也可以作为化工生产中的原料气,具有很大的利用价值。
3.目前焦炉煤气综合利用技术,针对焦炉煤气的气体组成开发了不同的工艺生产路线,包括焦炉煤气制甲醇、液氨、lng、乙二醇、氢能源等产品路线。在已有的焦炉煤气制甲醇路线中,是将焦炉煤气中的ch4通过转化反应生成co和h2以适当调节氢碳比,进而合成甲醇产品。这一做法同样无法避免进入甲醇合成装置的氢碳比偏高的问题,因而又进一步开发了利用甲醇合成中的弛放气提取h2用来联产液氨的技术。在已有的焦炉煤气制lng路线中,一种是直接提取焦炉煤气中的ch4用来生产lng产品,另一种是利用甲烷合成技术,将co、co2和h2反应生成ch4以生产lng产品。
4.公开号为cn103435443a的中国专利,公开了一种焦炉煤气制甲醇过程的补碳工艺和装置,该装置能够在转化和合成工段均加入二氧化碳,以此提高甲醇产量。但该方案是将ch4转化为了co和h2,不生产lng产品。
5.公开号为cn104418703a的中国专利,公开了一种以焦炉气为原料的串联甲醇、甲烷合成工艺,该工艺能将生产完甲醇以后的气体进行深度冷冻,将气体中的甲烷,多碳烃液化分离出来。但该方法lng生产工序在甲醇合成装置之后,进入甲醇合成装置的新鲜气中含有大量的ch4,且氢碳比远高于甲醇合成的最佳氢碳比。
技术实现要素:6.本发明的目的在于提供一种焦炉煤气补入co2制备甲醇和lng的工艺,能够通过将焦炉煤气进行深冷分离,然后通过补入外部的co2气体、焦炉煤气脱除的co2和深冷分离的富氢气为原料制备甲醇,实现制备lng和甲醇,能耗低,环境友好,经济效益高;
7.为达到上述目的,本发明采用的技术方案是:
8.一种焦炉煤气补入co2制备甲醇和lng的工艺,包括以下步骤:
9.s1,焦炉煤气初压、净化和增压:将焦炉煤气通入焦炉煤气初压装置进行初压,焦炉煤气初压装置的焦炉煤气压力为0.003~0.03mpag,焦炉煤气初压出口的压力为0.3~0.7mpag,焦炉煤气初压出口气体送至焦炉煤气净化装置,脱除焦炉煤气中的杂质,净化后的焦炉煤气送至焦炉煤气增压装置进行增压,焦炉煤气增压装置的出口压力为2.0~4.0mpag;
10.s2,精脱硫:将焦炉煤气增压装置出口的焦炉煤气送至精脱硫装置,精脱硫装置脱
除焦炉煤气中的有机硫和无机硫;出精脱硫装置的焦炉煤气中总硫含量低于0.1ppm;
11.s3,脱碳:将脱硫后的焦炉煤气送至脱碳装置,对焦炉煤气中的co2进行脱除;
12.s4,深冷分离:将脱除co2后的焦炉煤气送至深冷分离装置,分离出ch4和富氢气,ch4为液相lng,送至lng罐;
13.s5,富碳气压缩:补入外部的co2气体,将外部co2和脱碳装置脱除的co2置入富碳气压缩装置,进行压缩;富碳气压缩装置的入口co2压力为0.01~0.03mpag,出口压力1.6~3.6mpag;
14.s6,合成气压缩:将新鲜气和循环气组成合成气,通入合成气压缩装置内进行压缩;新鲜气压力为1.6~3.6mpag,循环气压力4.2~8.2mpag,合成气压缩出口气体压力为5.0~9.0mpag;新鲜气由富碳气压缩后的co2和深冷分离出的富氢气组成,且新鲜气摩尔组成为(h
2-co2)/(co+co2)=1.9~2.2;
15.s7,甲醇合成:将s6压缩后的合成气置入甲醇合成塔,在甲醇合成催化剂的作用下合成粗甲醇;甲醇合成压力为5.0~9.0mpag,在甲醇合成过程中得到的循环气置入合成气压缩装置;
16.s8,甲醇精馏:将甲醇合成塔出口的粗甲醇送入甲醇精馏塔,进行精馏,得到精甲醇。
17.优选的,在步骤s1中,焦炉煤气净化装置脱除焦炉煤气中的焦油尘、苯、萘杂质;焦炉煤气净化装置中设置焦油、苯、萘三个变温吸附段对其进行脱除,控制出焦炉气净化装置的焦油尘含量低于1mg/nm3,苯含量低于10mg/nm3,萘含量低于10mg/nm3。
18.优选的,在步骤s2中,精脱硫装置采用加氢转化法脱除焦炉煤气中的有机硫,采用氧化锌脱除焦炉煤气中的无机硫;其中,加氢转化法采用铁钼加氢催化剂,脱除焦炉煤气中的无机硫采用zno脱硫剂,zno脱硫剂中zno≥80%(wt%)。
19.优选的,在步骤s3中,采用变压吸附psa脱碳方法或mdea法对焦炉煤气中的co2进行脱除;脱碳装置出去的焦炉煤气中co2含量低于50ppm。
20.优选的,在步骤s4中,深冷分离装置采用阶式制冷循环、混合制冷剂循环或膨胀制冷循环技术提供冷量,将焦炉煤气温度降至-160
°
~-170
°
。
21.优选的,在步骤s5中,外部co2气体中co2含量≥95%(v%),外部co2的气量为进入合成气压缩总气量的5%~20%。
22.优选的,在步骤s7中,甲醇合成催化剂为铜锌系甲醇合成催化剂,甲醇合成塔为副产蒸汽型低压甲醇合成塔或副产热水型低压甲醇合成塔。
23.优选的,还包括以下步骤:
24.s9,氢回收:将s7中甲醇合成装置中的弛放气通入氢回收装置中,氢回收装置提取弛放气中的氢气,然后将氢气通入合成气压缩装置中的新鲜气中。
25.优选的,所述焦炉煤气初压装置为螺杆压缩机或往复式压缩机或离心式压缩机中的任意一种;焦炉煤气增压装置为往复式压缩机或离心式压缩机中的任意一种;所述焦炉煤气初压装置和焦炉煤气增压装置均通过电机或汽轮机驱动;
26.当焦炉煤气初压装置和焦炉煤气增压装置同为往复式压缩机时,焦炉煤气初压装置和焦炉煤气增压装置为同一装置。
27.优选的,所述富碳气压缩装置为离心式压缩机或往复式压缩机中的一种;所述合
成气压缩装置为离心式压缩机;所述富碳气压缩装置和合成气压缩装置均通过电机或汽轮机驱动。
28.本发明通过先将焦炉煤气脱硫和脱碳后,进行深冷分离,制备lng,然后通过收集外部的co2气体、焦炉煤气脱除的co2和深冷分离的富氢气为原料制备甲醇,使得进入甲醇合成塔内合成气的氢碳比为甲醇合成的最佳氢碳比,且通过收集外部的co2,对于实现节能降耗、资源综合利用具有十分重要的意义,具有综合能耗低,环境友好,经济效益高的优点。
附图说明
29.图1为本发明工艺流程图。
具体实施方式
30.以下结合附图和具体实施例,对本发明做进一步说明。
31.实施例1:
32.焦炉煤气中焦油尘总含量0.02g/nm3,苯含量2g/nm3,萘含量0.2g/nm3,硫化氢含量:30mg/nm3,有机硫含量:200mg/nm3,焦炉煤气的的气体组成如表1所示:
33.表1
34.组成h2coco2ch4n2c
mhn
o2∑含量(vol%)58.008.003.0024.004.002.500.50100.00
35.一种焦炉煤气补入co2制备甲醇和lng的工艺,如图1所示,包括以下步骤:
36.s1,焦炉煤气初压、净化和增压:将0.02mpag焦炉煤气通入焦炉煤气初压装置进行初压,焦炉煤气初压采用电机驱动的螺杆压缩机,将焦炉煤气加压至0.7mpag后送至焦炉气净化装置;焦炉气净化装置设置了三段变温吸附床层,分别对焦炉煤气中的焦油尘、苯、萘进行脱除,出焦炉气净化装置的焦油尘含量为1mg/nm3,苯含量为5mg/nm3,萘含量为5mg/nm3,净化后的焦炉煤气送至焦炉煤气增压装置;焦炉煤气增压装置采用电机驱动的离心式压缩机,将焦炉煤气加压至2.5mpag后送至精脱硫;
37.s2,精脱硫:将焦炉煤气增压装置出口的焦炉煤气送至精脱硫装置,精脱硫装置采用两级加氢转化法脱除焦炉煤气中的有机硫,再采用氧化锌脱除焦炉煤气中的无机硫;加氢转化法中采用铁钼加氢催化剂,铁钼加氢催化剂的主要成分为:fe2o3:1~3%(wt%),moo3:2~10%(wt%)、al2o3:0~70%(wt%);脱除焦炉煤气中的无机硫采用zno脱硫剂,zno脱硫剂中zno≥80%(wt%);出精脱硫装置的焦炉煤气中总硫含量为0.1ppm,然后将焦炉煤气送至脱碳;
38.s3,脱碳:将脱硫后的焦炉煤气送至脱碳装置,脱碳装置采用mdea脱碳法对焦炉煤气中的co2进行脱除;焦炉煤气和mdea溶液在吸收塔内逆流接触,焦炉煤气中的co2被mdea溶液吸收进入液相,脱除co2后的焦炉煤气从吸收塔顶送至合成气压缩装置,co2含量由3%降至20ppm;吸收了co2的mdea溶液再生后循环使用,再生释放出的co2气,压力20kpag,将释放出co2置入富碳气压缩;
39.s4,深冷分离:将脱除co2后的焦炉煤气送至深冷分离装置,深冷分离装置采用混合制冷剂循环来提供冷量,将焦炉煤气的温度降至-165℃,分离出ch4和富氢气,分离出的ch4作为液相lng产品送往lng罐区;分离出的富氢气送至合成气压缩装置;深冷分离装置中
ch4的回收率为98.5%,h2的回收率为98%;
40.s5,富碳气压缩:补入外部的co2气体,将外部co2和脱碳装置脱除的co2置入富碳气压缩装置,富碳气压缩装置采用电机驱动的离心式压缩机进行压缩;富碳气压缩装置的入口co2压力为0.02mpag,出口压力2.0mpag;其中补入外部的co2气体时,外部co2气体中co2含量≥95%(v%),外部co2的气量为进入合成气压缩总气量的14%,其中外部的co2气体可以为其他工艺过程排出的co2也可以是收集空气中或者是烟道气中的co2。
41.s6,合成气压缩:合成气压缩装置采用新鲜气和循环气联合压缩的离心式压缩机,汽轮机驱动;将新鲜气和循环气组成合成气,通入合成气压缩装置内进行压缩;新鲜气由富碳气压缩后的co2、深冷分离出的富氢气和来自氢回收的氢气组成;新鲜气摩尔组成(h2-co2)/(co+co2)=2.1;新鲜气压力为2.0mpag,循环气压力7.2mpag,合成气压缩出口气体压力为8.0mpag;然后将合成气压缩装置出口的合成气送至甲醇合成。
42.s7,甲醇合成:将s6压缩后的合成气置入甲醇合成塔,甲醇合成采用低压法甲醇合成技术;甲醇合成压力8.0mpag,甲醇合成塔采用副产蒸汽型低压甲醇合成塔,甲醇合成塔内装填有适用于高co、高co2含量的甲醇合成铜锌系甲醇合成催化剂;合成的粗甲醇送往甲醇精馏塔,在甲醇合成过程中得到的循环气置入合成气压缩装置,弛放气送至氢回收。
43.s8,甲醇精馏:将甲醇合成装置出口的粗甲醇送入甲醇精馏塔,进行精馏,得到精甲醇;
44.本实施例中,还包括以下步骤,
45.s9,氢回收:将s7中甲醇合成塔中的弛放气通入氢回收装置中,氢回收装置采用膜分离提氢技术;弛放气进入膜分离后,绝大部分的氢被回收,氢气的回收率为90%,回收的氢气送至合成气压缩装置中的新鲜气中;未被回收的气体作为燃料气,送至燃料气管网。
46.其中,需要说明的是,加氢转化法脱除有机硫、氧化锌脱除无机硫、变压吸附psa脱碳方法、mdea脱碳法、阶式制冷循环、混合制冷剂循环、膨胀制冷循环技术和低压法甲醇合成技术均为现有技术。
47.实施例2:
48.焦炉煤气中焦油尘总含量0.1g/nm3,苯含量3g/nm3,萘含量0.3g/nm3,硫化氢含量:20mg/nm3,有机硫含量:250mg/nm3,焦炉煤气的的气体组成如表2所示:
49.表2
50.组成h2coco2ch4n2c
mhn
o2∑含量(vol%)58.0110.603.8321.773.452.080.26100.00
51.一种焦炉煤气补入co2制备甲醇和lng的工艺,包括以下步骤:
52.s1,焦炉煤气初压、净化和增压:将0.005mpag焦炉煤气通入焦炉煤气初压装置进行初压,焦炉煤气初压采用电机驱动的离心式压缩机,将焦炉煤气加压至0.4mpag后送至焦炉气净化装置;焦炉气净化装置设置了三段变温吸附床层,分别对焦炉煤气中的焦油尘、苯、萘进行脱除,出焦炉气净化装置的焦油尘含量为1mg/nm3,苯含量为10mg/nm3,萘含量为10mg/nm3,净化后的焦炉煤气送至焦炉煤气增压装置;焦炉煤气增压装置采用电机驱动的离心式压缩机,将焦炉煤气加压至2.8mpag后送至精脱硫;
53.s2,精脱硫:将焦炉煤气增压装置出口的焦炉煤气送至精脱硫装置,精脱硫装置采用两级加氢转化法脱除焦炉煤气中的有机硫,再采用氧化锌脱除焦炉煤气中的无机硫;加
氢转化法中采用铁钼加氢催化剂,铁钼加氢催化剂的主要成分为:fe2o3:1~3%(wt%),moo3:2~10%(wt%)、al2o3:0~70%(wt%);脱除焦炉煤气中的无机硫采用zno脱硫剂,zno脱硫剂中zno≥80%(wt%);出精脱硫装置的焦炉煤气中总硫含量为0.08ppm,然后将焦炉煤气送至脱碳;
54.s3,脱碳:将脱硫后的焦炉煤气送至脱碳装置,脱碳装置采用变压吸附脱碳技术对焦炉煤气中的co2进行脱除;焦炉煤气中co2在脱碳吸附塔内被吸附,未被吸附的焦炉煤气从塔顶送至合成气压缩装置,co2含量由3.83%降至50ppm;吸附了co2吸附塔再生出的co2气,压力20kpag,将释放出co2置入富碳气压缩;
55.s4,深冷分离:将脱除co2后的焦炉煤气送至深冷分离装置,深冷分离装置采用混合制冷剂循环来提供冷量,将焦炉煤气的温度降至-165℃,分离出ch4和富氢气,分离出的ch4作为液相lng产品送往lng罐区;分离出的富氢气送至合成气压缩装置;深冷分离装置中ch4的回收率为98%,h2的回收率为98%;
56.s5,富碳气压缩:补入外部的co2气体,将外部co2和脱碳装置脱除的co2置入富碳气压缩装置,富碳气压缩装置采用电机驱动的离心式压缩机进行压缩;富碳气压缩装置的入口co2压力为0.01mpag,出口压力2.3mpag;其中收集外部的co2气体时,外部co2气体中co2含量≥95%(v%),外部co2的气量为进入合成气压缩总气量的11%。
57.s6,合成气压缩:合成气压缩装置采用新鲜气和循环气联合压缩的离心式压缩机,电机驱动;将新鲜气和循环气组成合成气,通入合成气压缩装置内进行压缩;新鲜气由富碳气压缩后的co2、深冷分离出的富氢气组成;新鲜气摩尔组成(h2-co2)/(co+co2)=2.05;新鲜气压力为2.2mpag,循环气压力7.2mpag,合成气压缩出口气体压力为8.0mpag;然后将合成气压缩装置出口的合成气送至甲醇合成。
58.s7,甲醇合成:将s6压缩后的合成气置入甲醇合成塔,甲醇合成采用低压法甲醇合成技术;甲醇合成压力8.0mpag,甲醇合成塔采用副产蒸汽型低压甲醇合成塔,甲醇合成塔内装填有适用于高co、高co2含量的甲醇合成铜锌系甲醇合成催化剂;合成的粗甲醇送往甲醇精馏塔,在甲醇合成过程中得到的循环气置入合成气压缩装置,弛放气送至燃料气管网。
59.s8,甲醇精馏:将甲醇合成装置出口的粗甲醇送入甲醇精馏塔,进行精馏,得到精甲醇。
60.实施例3:
61.焦炉煤气中焦油尘总含量0.1g/nm3,苯含量3g/nm3,萘含量0.3g/nm3,硫化氢含量:20mg/nm3,有机硫含量:250mg/nm3,焦炉煤气的的气体组成如表3所示:
62.表3
63.组成h2coco2ch4n2c
mhn
o2∑含量(vol%)58.0110.603.8321.773.452.080.26100.00
64.一种焦炉煤气补入co2制备甲醇和lng的工艺,包括以下步骤:
65.s1,焦炉煤气初压、净化和增压:焦炉煤气初压装置和焦炉煤气增压装置采用合并的往复式压缩机,由电机驱动;将0.006mpag焦炉煤气通入往复式压缩机,然后从往复式压缩机的二段出口抽出,送至焦炉气净化装置,净化后返回往复式压缩机,升压至3.0mpag送往精脱硫装置;
66.焦炉气净化装置设置了三段变温吸附床层,分别对焦炉煤气中的焦油尘、苯、萘进
行脱除,出焦炉气净化装置的焦油尘含量为1mg/nm3,苯含量为10mg/nm3,萘含量为10mg/nm3;
67.s2,精脱硫:将焦炉煤气增压装置出口的焦炉煤气送至精脱硫装置,精脱硫装置采用两级加氢转化法脱除焦炉煤气中的有机硫,再采用氧化锌脱除焦炉煤气中的无机硫;加氢转化法中采用铁钼加氢催化剂,铁钼加氢催化剂的主要成分为:fe2o3:1~3%(wt%),moo3:2~10%(wt%)、al2o3:0~70%(wt%);脱除焦炉煤气中的无机硫采用zno脱硫剂,zno脱硫剂中zno≥80%(wt%);出精脱硫装置的焦炉煤气中总硫含量为0.1ppm,然后将焦炉煤气送至脱碳;
68.s3,脱碳:将脱硫后的焦炉煤气送至脱碳装置,脱碳装置采用变压吸附脱碳技术对焦炉煤气中的co2进行脱除;焦炉煤气中co2在脱碳吸附塔内被吸附,未被吸附的焦炉煤气从塔顶送至合成气压缩装置,co2含量由3.83%降至50ppm;吸附了co2吸附塔再生出的co2气,压力20kpag,将释放出co2置入富碳气压缩;
69.s4,深冷分离:将脱除co2后的焦炉煤气送至深冷分离装置,深冷分离装置采用混合制冷剂循环来提供冷量,将焦炉煤气的温度降至-165℃,分离出ch4和富氢气,分离出的ch4作为液相lng产品送往lng罐区;分离出的富氢气送至合成气压缩装置;深冷分离装置中ch4的回收率为98%,h2的回收率为98%;
70.s5,富碳气压缩:补入外部的co2气体,将外部co2和脱碳装置脱除的co2置入富碳气压缩装置,富碳气压缩装置采用电机驱动的离心式压缩机进行压缩;富碳气压缩装置的入口co2压力为0.03mpag,出口压力2.4mpag;其中收集外部的co2气体时,外部co2气体中co2含量≥95%(v%),外部co2的气量为进入合成气压缩总气量的12%。
71.s6,合成气压缩:合成气压缩装置采用新鲜气和循环气联合压缩的离心式压缩机,电机驱动;将新鲜气和循环气组成合成气,通入合成气压缩装置内进行压缩;新鲜气由富碳气压缩后的co2、深冷分离出的富氢气组成;新鲜气摩尔组成(h2-co2)/(co+co2)=2.1;新鲜气压力为2.4mpag,循环气压力6.2mpag,合成气压缩出口气体压力为7.0mpag;然后将合成气压缩装置出口的合成气送至甲醇合成。
72.s7,甲醇合成:将s6压缩后的合成气置入甲醇合成塔,甲醇合成采用低压法甲醇合成技术;甲醇合成压力7.0mpag,甲醇合成塔采用副产热水型低压甲醇合成塔,甲醇合成塔内装填有适用于高co、高co2含量的甲醇合成铜锌系甲醇合成催化剂;合成的粗甲醇送往甲醇精馏塔,在甲醇合成过程中得到的循环气置入合成气压缩装置,弛放气送至燃料气管网。
73.s8,甲醇精馏:将甲醇合成装置出口的粗甲醇送入甲醇精馏塔,进行精馏,得到精甲醇。