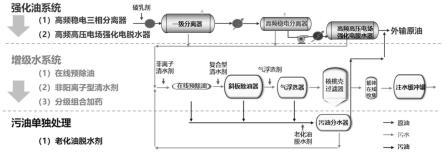
1.本发明涉及一种海上油田聚合物驱采出液一体化处理方法及装置,属于石油开发技术领域。
背景技术:2.聚合物驱是油田稳产增产最有效的技术手段之一,海上油田自2003年开展聚合物驱先导试验并规模化应用以来,取得了显著经济效益。聚合物驱采出液因驱油聚合物的部分产出,油水乳化程度加重,且形成的乳化油滴粒径小,上浮速度变慢;另一方面,产出聚合物吸附在油水界面处,使得油滴表面电负性增强,油滴间排斥力增大,界面膜强度升高,削弱了油滴聚集和聚并,综合因素导致采出液油水分离难度较水驱大幅增加,这是聚合物驱采出液处理难度大的本质原因,含聚采出液快速高效处理已成为海上油田聚合物驱大规模应用的最大障碍之一。
技术实现要素:3.本发明的目的是提供一种海上油田聚合物驱采出液一体化处理方法及装置,为一种“强化油系统、增级水系统、污油单独处理和分级组合加药”的一体化处理模式,具有油水处理剂用量少、油泥生成量少、后处理成本低等特点,能够有力保障了上平台地面处理流程正常运行。
4.本发明提供的海上油田聚合物驱采出液一体化处理方法,包括原油处理步骤、污水处理步骤和污油处理步骤;
5.所述原油处理步骤包括如下步骤:聚合物驱采出液经破乳后依次经油水分离、静电聚结脱水和高频高压电场强化电脱水,得到外输原油;
6.所述静电聚结脱水的条件为:电场频率为800~1100hz。
7.所述高频高压电场强化电脱水的条件为:输出电压为10kv~25kv,电场频率为500~5000hz;
8.所述污水处理步骤包括如下步骤:所述油水分离、所述静电聚结脱水和所述高频高压电场强化电脱水得到的污水混合后,依次经在线预除油、斜板除油、气浮选、过滤和絮体在线收集,实现对污水的长效净化处理;
9.所述污水处理步骤中,加入非离子型清水剂后进行所述在线预除油,加入复合型清水剂后进行所述斜板除油;
10.所述复合型清水剂为非离子型清水剂和两性离子型清水剂的混合物。
11.上述的一体化处理方法中,所述非离子型清水剂为非离子聚丙烯酰胺、聚乙烯亚胺作起始剂的环氧乙烷(eo)-环氧丙烷(po)嵌段共聚合物等;
12.所述两性离子型清水剂为两性离子聚丙烯酰胺或二甲基二烯丙基氯化铵-烯丙基磺酸钠共聚物;
13.所述非离子型清水剂的用量为10~150ppm;
0.1mpa,表示反应完全,制得ea-po型亲油性聚醚;
31.3)所述ea-po型亲油性聚醚与koh、环氧乙烷(eo)顺序加入至高压反应釜中,反应温度为100~120℃,反应压强为0.15~0.35mpa,持续反应,所述高压釜内压力逐渐减小,表压降至-0.1mpa时,表示反应完全,即得到所述儿茶素破乳剂;
32.具体地,将ea-po型亲油性聚醚与koh顺序加入至高压釜中,以相同的制备方式,缓慢、连续地通入一定质量的环氧乙烷(eo);由于eo活性高,控制压力低于0.3mpa、温度低于120℃;加料完成后反应釜压力压力降至-0.1mpa,表示反应完全。
33.即得到儿茶素破乳剂;
34.所述老化油脱水剂的用量为10~200ppm;
35.所述污油分水得到的油相作为外输原油;
36.所述污油分水得到的水相与所述油水分离、所述静电聚结脱水和所述电脱水得到的污水混合后进行污水处理。
37.本发明污水处理步骤得到的污油汇集单独处理(进行老化油独立高效脱水处理),从而保障原油处理系统脱水效果。通过该处理步骤,电脱水的效果提升,所述原油处理步骤中的电脱水温度可由81℃提升至87℃,油相含水由10~12%降至4~7%,为进一步提升聚合物驱采出液脱水效果奠定了坚实的基础。
38.本发明进一步提供了一种海上油田聚合物驱采出液一体化处理装置,包括原油处理结构、污水处理结构和污油处理结构;其特征在于:
39.所述原油处理结构包括依次连接的油水分离器、高频稳电三相分离器和高频高压电场强化电脱水器;
40.所述污水处理结构包括依次连接的在线预除油装置、除油器、气浮选器、过滤器和絮体在线收集装置;
41.所述油水分离器、所述高频稳电三相分离器和所述高频高压电场强化电脱水器的油相出口与所述在线预除油装置的入口连接;
42.所述污油处理结构包括污油分水器;
43.所述在线预除油装置(在线预除油装置实现水处理设施的“管式化”,快速完成大量生产水的预处理,保障原油处理的水力停留时间)、所述除油器和所述气浮选器的油相出口与所述污油分水器的入口连接;
44.所述污油分水器的油相出口与所述高频高压电场强化电脱水器的出口连接,水相出口与所述在线预除油装置的入口连接。
45.上述的一体化处理装置中,所述油水分离器可为一级油水分离器或二级油水分离器;
46.所述高频稳电三相分离器可为高频高压稳电聚结器、紧凑型静电聚结器、在线静电聚结器、容器内置式静电聚结器或低含水量聚结器;
47.所述高频稳电三相分离器能够增强所述油水分离器的脱水效果,使其出口原油含水<20%,满足所述电脱水器的入口指标,实现最终原油含水<1%;
48.所述除油器为斜板除油器;
49.所述过滤器为核桃壳过滤器。
50.上述的一体化处理装置中,所述在线预除油装置和所述除油器的入口端均设有旋
流混合加药装置,实现分级复合加药,通过物理技术尽可能多除油,使所述斜板除油器入口含油量尽量贴近其入口设计指标(含油量≤1500mg/l),从而减少药剂用量,并保障除油效果;
51.所述过滤器的出口依次连接絮体在线收集装置和注水缓冲罐。
52.本发明具有如下有益效果:
53.外输原油含水显著降低,聚合物保留率高,污泥产生量日均显著减少,淤堵结焦状况质变改观,危废处置费用降减明显,终端环保减排显著降压。
附图说明
54.图1为本发明海上油田聚合物驱采出液一体化处理装置的结构示意图。
55.图2为本发明海上油田聚合物驱采出液一体化处理方法的流程图。
56.图3为不同频率下乳状液稳定动力学参数。
57.图4为现场试验中高频稳电三相分离器的进液含水率和出口含水率。
58.图5为现场试验中不同加药方式的除油率。
59.图6为现场试验中加入不同清水剂得到的絮体状态。
60.图7为现场试验中污水处理步骤中各处理步骤后的实物图片。
61.图8为现场试验中污油处理步骤中加入不同药剂时的效果。
62.图9为采用本发明一体化处理方法后平台外输原油含水率。
63.图10为现场污油泥每日平均量(单位为吨)。
64.图11为现场平台缓冲罐油泥的状态(左图为现有处理方法得到的,右图为本发明一体化处理方法得到的)。
65.图1中各标记如下:
66.1油水分离器、2高频稳电三相分离器、3高频高压电场强化电脱水器、4在线预除油装置、5斜板除油器、6气浮选器、7核桃壳过滤器、8絮体在线收集装置、9注水缓冲罐、10污油分水器、11旋流混合加药装置。
具体实施方式
67.下面结合附图对本发明做进一步说明,但本发明并不局限于以下实施例。
68.如图1所示,为本发明提供的海上油田聚合物驱采出液一体化处理装置,为一种“强化油系统,增级水系统,污油单处理”的一体化处理系统,分别通过原油处理结构、污水处理结构和污油处理结构实现。
69.其中,原油处理结构包括依次连接的油水分离器1、高频稳电三相分离器2和高频高压电场强化电脱水器3,高频高压电场强化电脱水器3的油相出口连接原油外输管路。
70.其中,污水处理结构包括依次连接的在线预除油装置4、斜板除油器5、气浮选器6、核桃壳过滤器7、絮体在线收集装置8和注水缓冲罐9,油水分离器1、高频稳电三相分离器2和高频高压电场强化电脱水器3的油相出口与在线预除油装置4的入口连接,以将原油处理得到的污水进行处理。另外,在线预除油装置4和斜板除油器5的入口端均设有旋流混合加药装置11,实现分级复合加药,通过物理技术尽可能多除油,使斜板除油器5的入口含油量尽量贴近其入口设计指标(含油量≤1500mg/l),从而减少药剂用量,并保障除油效果。
71.其中,油处理结构包括污油分水器10,污油分水器10的入口端设有老化油脱水剂加入口。污油分水器10的油相出口与高频高压电场强化电脱水器3的出口连接,以对污油进行处理,污油分水器10的水相出口与在线预除油装置4的入口连接,以对污水进行处理。
72.本发明一体化处理装置中,油水分离器1可为一级油水分离器或二级油水分离器;高频稳电三相分离器2可为高频高压稳电聚结器、紧凑型静电聚结器、在线静电聚结器、容器内置式静电聚结器或低含水量聚结器,高频稳电三相分离器能够增强所述油水分离器的脱水效果,使其出口原油含水<20%,满足电脱水器的入口指标,实现最终原油含水<1%。
73.在海上油田聚合物驱采出液一体化处理装置的基础上,本发明提供的一体化处理方法包括如下步骤:
74.如图2所示,包括原油处理步骤(强化油系统)、污水处理步骤(增级水系统)和污油处理步骤(污油单独处理)。
75.其中,原油处理步骤包括如下步骤:聚合物驱采出液经破乳后依次经油水分离、静电聚结脱水和电脱水,得到外输原油;污水处理步骤包括如下步骤:油水分离、静电聚结脱水和高频高压电场强化电脱水得到的污水混合后,依次经在线预除油、斜板除油、气浮选、过滤和絮体在线收集,实现对污水的净化处理;污油处理步骤包括如下步骤:在线预除油、斜板除油和气浮选得到的污油混合后,经污油单独分水,得到的油相作为外输原油,水相进入污水处理步骤。
76.在原油处理步骤中,破乳采用的破乳剂为多支化稠环酚聚醚类破乳剂或聚氨酯类破乳剂,其用量为10~200ppm。
77.在原油处理步骤中,本发明通过稳定动力学参数法(tsi)优化出最优电场频率为800~1100hz,如图3所示,在电极间提供稳定的高强电场,微水滴瞬时极化变形、聚并,加速粒径变大,加快原油脱水。
78.本发明进行现场试验,在上述确定的最优电场频率(800~1100hz)下进行,高频稳电三相分离器2的进液含水率和出口含水率如图4所示,可以看出,对于其含水高达90%的含聚采出液,高频稳电三相分离器2出口含水可降至5%。
79.本发明进行现场试验,控制高频高压电场强化电脱水的条件为:输出电压为10kv~25kv,电场频率为500~5000hz,该条件下能够提供稳定的高强电场,微水滴瞬时极化聚并,加快原油脱水;其中,当输出电压为20kv,电场频率为3000hz时,入口含水为5~30%,出口含水能够降低至2%左右。
80.在污水处理步骤中,加入非离子型清水剂后进行在线预除油,加入复合型清水剂后进行斜板除油,复合型清水剂为非离子型清水剂和两性离子型清水剂的混合物,其中,非离子型清水剂为非离子聚丙烯酰胺,两性离子型清水剂为两性离子聚丙烯酰胺,总用量为300ppm。
81.本发明考察了不同清水剂的清水效果,考察了不同清水剂配合的效果:两性离子型清水剂(两性离子聚丙烯酰胺)、非离子型清水剂(非离子聚丙烯酰胺)、阳离子型清水剂(阳离子聚丙烯酰胺)、两性离子型清水剂与非离子型清水剂的混合物,总用量为300ppm。
82.采用上述不同加药方式进行现场试验(在上述确定的最佳条件下进行原油处理:破乳剂为聚氨酯类破乳剂,其用量为100ppm,静电聚结的电场频率为1000hz,对原油处理得到的水相进行处理水处理),除油效果如图5所示,可以看出,两性与非离子型清水剂组合使
用,同等用量下,相对于单独采用阳离子型清水剂除油率提升10%,且无粘性絮体产生,如图6所示(左图为采用阳离子型清水剂得到的絮体状态,右图为采用复合型清水剂得到的絮体状态);且分级加药方式有效利用率(达到效果时药剂用量减少的比例)较第一种(即同时加入非离子型清水剂和复合型清水剂的管式加药方式)提升35%。
83.本发明采用旋流混合加药的方式加入非离子型清水剂和复合型清水剂,以提高混合效果。
84.在污水处理步骤中,气浮选采用的浮选剂为季铵盐类小分子表面活性剂、聚胺盐类表面活性剂或阳离子型聚丙烯酰胺;
85.采用上述污水处理步骤进行现场试验,除油效果如图7所示,从左至右依次为污水来液、斜板出口液、气浮出口液和过滤出口液,证明了本发明污水处理的效果。
86.在污油处理步骤中,老化油脱水采用的老化油脱水剂为儿茶素破乳剂,其用量为10~200ppm,按照下述方法制备:1)取62g表没食子儿茶素没食子酸酯(egcg)溶于甲醇,将其加入到154g四乙烯五胺中,旋转蒸发除去甲醇,得到深棕色粘稠液体;将其加入到三口瓶中,向三口瓶中滴加66g甲醛水溶液,滴加结束后升温至80℃反应10h。旋蒸后,50℃真空干燥48h,得到起始剂eapa(黑褐色黏稠液体);2)将起始剂eapa和koh依次加入至高压反应釜中,密闭检漏后升温,并减压至-0.1mpa。当升温至70℃时开始抽真空,持续至100℃。当温度接近120℃时,按照一定的质量比缓慢、连续地通入环氧丙烷(po),控制反应釜压力低于0.4mpa。加料结束后,po持续反应,高压釜内压力逐渐减小,表压降至-0.1mpa,表示反应完全,制得ea-po型亲油性聚醚;3)将ea-po型亲油性聚醚与koh顺序加入至高压釜中,以相同的制备方式,缓慢、连续地通入一定质量的环氧乙烷(eo);由于eo活性高,控制压力低于0.3mpa、温度低于120℃;加料完成后反应釜压力压力降至-0.1mpa,表示反应完全即得。
87.现有油水处理是闭路循环,污油转回原油处理系统,严重降低了处理效能,造成外输原油含水高且波动大。本发明提供了污油单独处理的工艺。
88.现场破乳(渤海sz36-1油田)试验结果如图8所示,其中,采用的破乳剂为儿茶素破乳剂,选择现场使用的正常原油破乳剂(bh123)作为对照,破乳剂浓度为100mg/l。结果表明,10min以内脱水率80%,40min脱水率95%。污油系统老化油含水36%以上,每天800~1000方,使用污油单独处理工艺,平台原油含水整体可由10%降至4%。
89.本发明污水处理步骤得到的污油汇集进行单独高效脱水处理后外输。
90.原油处理步骤中的电脱水温度可由81℃提升至87℃,提升了设备处理效率,为进一步提升聚合物驱采出液脱水效果奠定了坚实的基础。
91.采用本发明采出液处理一体化后,油相含水由10~12%降至3%(图9),绥中36-1终端处理厂污油泥量由约120吨/天降低至30吨/天左右(如图10所示);平台缓冲罐油泥由粘弹性棉被状变为可流动状态,由量多变为量少,可用泵抽(如图11所示),油泥处理难题实现根本性扭转。