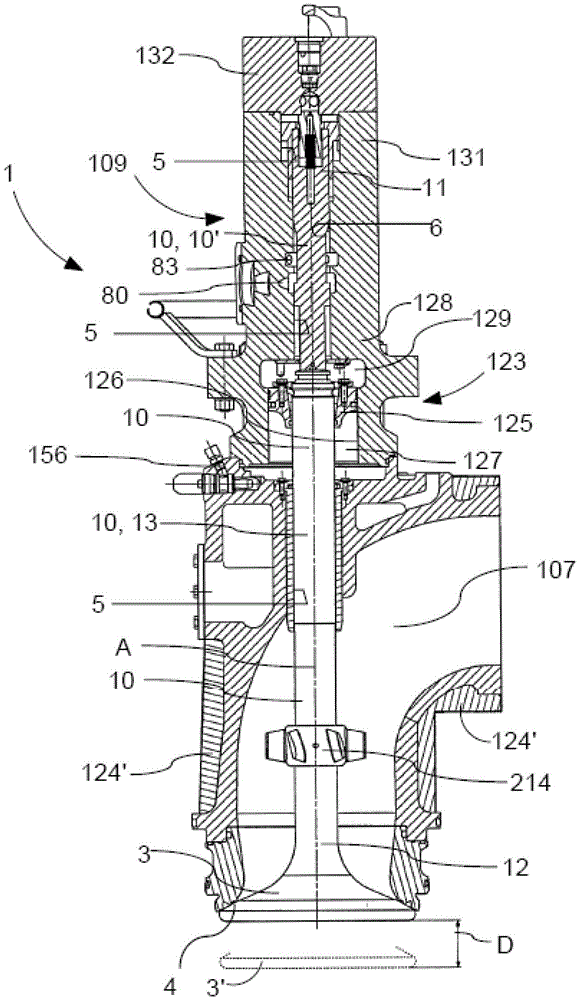
本发明涉及一种用于大型的慢速运行二冲程单流式十字头型柴油发动机的气体交换阀。更具体地,本发明涉及一种具有阀轴的气体交换阀,其在开阀过程中提供所述阀轴和制动机构的平衡定位。
背景技术:诸如船舶中使用的原动机这样的大型慢速运行二冲程单流式十字头型柴油发动机正变得越来越大。相应地,用于这种发动机的排气阀也变得越来越大。对这些较大的发动机而言,排气阀可为1-2米高。这种排气阀的阀轴可以有几百公斤重。排气阀必须在每个发动机循环中开启和关闭,目的是将发动机汽缸的燃烧室排空。对于正常工作的大型二冲程十字头型柴油发动机,其每分钟可以开启和关闭60-200次。为了避免由于紧靠在任何表面上的阀轴的较大重量而产生的损坏,阀轴的开启行程必须要在与任何这种停止表面发生任何接触之前被制动并慢慢停止。所以,通常在这种排气阀上设置开启阶段制动机构。这种开启阶段制动机构必须采取圆锥表面的形式,其形成于阀轴的一部分上,该圆锥表面与轴孔的一部分的侧壁配合,以关闭对致动室的液压流体供应。在JP2004084670中示出了这种机构的实例。这种圆锥表面必须具有在阀轴纵向上的延长部分,以便适当地工作,因此如果阀轴的温度发生变化,其可能引起阀轴长度发生很大变化,从而损失制动精度。由于例如发动机负载状态的不同,并且特别是在启动时发动机从冷的状态逐渐达到工作温度,发动机和排气阀部分的温度会产生变化。由于发动机中的这种温度差异,排气阀轴会膨胀和收缩,并且以不同于安装有该阀轴的外壳的比率发生膨胀和收缩。发动机越大,排气阀就越大,并且阀轴就变得越大。因此,阀轴的膨胀和收缩也较大,并可能对排气阀的工作状态产生冲击,如上文所解释。因此,圆锥表面越长,阀轴在开启阶段结束时的制动精度受到影响的风险就越大。JP200484670公开了根据权利要求1的前序部分的排气阀。
技术实现要素:在这一背景下,本发明的目的是提供一种具有制动机构的排气阀,该制动机构用于在阀的开启阶段结束时使排气阀的阀轴减速并停止;该排气阀的结构简单,在制造上具备成本效益,并且解决了现有技术中存在的问题。本发明的另一个目的是提供对现有的用于在阀的开启阶段结束时使排气阀的阀轴减速并停止的排气阀制动机构的替代方案。根据权利要求1,通过提供用于大型二冲程单流式十字头型柴油发动机的气体交换阀而实现了这一目的。试验和模拟已示出,狭缝的配置增加了用于在所有发动机工作温度下在阀的开启阶段结束时使排气阀的阀轴减速并停止的制动机构的精度。而且,已经示出了,由于当排气阀开启时阀轴的摆动减少了,用于使阀轴减速并停止的改进的制动机构还减少了振动。在一个实施例中,至少一个狭缝在阀轴的纵轴方向上具有逐渐增加的深度。在另一个实施例中,存在多个狭缝。所述多个狭缝中的每一个狭缝可以在阀轴的纵轴方向上具有相同的长度,或者所述多个狭缝可以具有不同的长度。在另一个实施例中,至少一个狭缝形成于轴的上部的下端处的外表面中。所述至少一个狭缝中的每一个狭缝可以具有上端和下端,并且朝着所述下端具有增加的深度,并且所述狭缝通向所述阀轴的上部的面朝下横档(downwardlyfacingledge)。在其它实施例中,可替换地,所述至少一个狭缝可形成于中心孔的中间部分的壁中。所述至少一个狭缝中的每一个狭缝具有上端和下端,并且具有朝着其上端和所述中间部分的上边缘增加的深度,并且所述狭缝通向所述中心孔中的第一变宽部分。在其它实施例中,如上所述的狭缝可以既设置在阀轴上部的下端处的外表面又形成在中心孔的中间部分的壁中。在所有实施例中,所述气体交换阀特别适合于作为排气阀。根据本发明的排气阀的其它的目的、特点、优势和性能将从详细的描述中变得显而易见。附图说明在本说明书以下更详细的部分中,将参考附图中所示的典型实施例更详细地解释本发明,其中:图1以截面图示出了大型二冲程单流式十字头型柴油发动机的上部;图2以截面图示出了根据本发明的排气阀;图3以截面图示出了图2中排气阀上部的细节;图4以截面图示出了根据本发明的阀轴的延伸部分,其形成于图2和3中排气阀的上部内;图5以透视图示出了根据本发明的阀轴的上部;图6A-H以截面图例示了:在排气阀的开启和关闭循环中,在阀轴行程的不同阶段,排气阀的致动器部分中液压流体的流动;其中,图6A示出了当阀被关闭并准备开启时位于顶部位置中的阀轴;图6B示出了在阀轴向下运动期间阀轴的一部分;图6C示出了当阀轴进入其向下运动的制动阶段时阀轴的位置;图6D示出了处于延伸得最远的位置中的阀轴,即,当排气阀完全开启时的阀轴;图6E示出了在排气阀开始关闭时液压流体的流动;图6F示出了处于液压流体开始从制动室中流出的位置的阀轴,图6G示出了处于活塞被啮合的位置中的阀轴;并且图6H示出了返回至其最顶端位置的阀轴。具体实施例下面将联系排气阀对根据本发明的气体交换阀进行描述。将通过优选的实施例对根据本发明的气体交换阀进行描述。图1示出了用在大型的慢速运行二冲程单流式十字头型柴油发动机中的单流式汽缸100。大型的慢速运行二冲程单流式十字头型柴油发动机通常具有3-16个这种汽缸。汽缸100具有位于集气箱103中的扫气口102,向来自扫气贮气箱(未示出)的该集气箱103提供由例如涡轮增压器(未示出)增压的扫气。排气阀1被居中地安装在汽缸盖124’的汽缸顶部中。在发动机的膨胀冲程结束时,在发动机活塞105向下移动经过扫气口102前,排气阀1开启,由此在活塞105上方的燃烧室106中的燃烧气体通过排气通道107排出,所述排气通道107向外通向排气贮气箱108。在活塞105在可调时刻向上运动期间,排气阀1再次关闭;所述可调时刻可取决于例如用于后续燃烧的期望的有效压缩比。在关闭运动期间,通过气动弹簧123向上驱动排气阀1(使其远离燃烧室106)。借助于液压驱动致动器109来开启排气阀1。通过压力导管110提供液压流体,例如液压油;该压力导管110连接致动器109上的端口80,该致动器109具有由控制台113支撑的分电器112的顶部表面上的控制端口。控制台113被连接至高压导管114,以用于接收在一定压力下由共轨(commonrail)(未示出)提供的液压流体,所述压力可以例如在从200至500巴的范围内,比如300巴。所述共轨也可以用作燃料注射系统的高压流体源。共轨(commonrail)中的液压流体可以用于直接驱动阀致动器109,或通过压力放大器/分离器间接驱动阀致动器109,所述分离器从共轨(commonrail)中的液压流体(其可以为例如液压油)中分离用于阀致动器109的液压流体。共轨燃料系统中的压力不依赖于发动机的工作状态(比如运转速度和负载状态)而变化。典型地,大型二冲程柴油发动机的共轨燃料系统中的压力在800巴和2000巴之间变化。如果使用用于阀致动器109的专用共轨,则液压流体可通过泵站(未示出)而由储存槽(未示出)提供,且液压流体例如可以是标准液压油,但优选地使用发动机润滑油作为液压流体并且通过发动机的油槽供给该系统。内燃机可以是中速的四冲程柴油或燃气发动机,或低速的二冲程十字头型柴油发动机,其可以是轮船中的推进发动机或发电厂中的固定原动机。发动机的每个汽缸100可以与电子控制单元115连接,所述电子控制单元115通过电线116接收总的同步和控制信号,并且例如通过电线118将电子控制信号传输至控制阀117等,以及例如通过电线173将电子控制信号传输至气动弹簧123。每个汽缸可以有一个控制单元115,或若干个汽缸可以与同一个控制单元115连接。控制单元115也可以从所有汽缸公用的总控制单元接收信号。可选地(未示出),气动弹簧123和/或控制阀117可以由凸轮控制,即,机械-液压控制。控制阀117可以是任意常见类型。控制阀117的结构和运转本身是熟知的且不应需要在本文中进行进一步解释。当期望打开排气阀1时,来自控制单元115的控制信号启动控制阀117,使得高压液压流体可自由流向压力导管110并由此自由流向液压流体供应端口80。当排气阀1即将关闭时,控制阀117被启动,使得导管110中的高压通过与返回线路122的连接而被排出。由此,气动弹簧123将朝向排气阀的关闭位置而推动排气阀。图2更详细地示出了汽缸100的上部和排气阀1的截面。排气阀1为例如如图1所示的用于大型二冲程单流式十字头型柴油发动机的类型。排气阀1具有阀轴(或杆)10,其从阀碟3中笔直突出,具有底部或下端12、上端11和中心部分13。阀轴10为细长形并具有纵轴A。在图2中,通过以虚线示出的阀碟3’位于处于关闭位置的阀碟3的位置之下一定距离并与阀座4接触来表示排气阀的开启位置。轴10的中心部分13支撑弹簧活塞125,该弹簧活塞紧固地安装在轴10上,从而可在气动汽缸126中压力密封并纵向移动。在弹簧活塞125之下设有弹簧室127,其通过合适的阀156与增压空气供应(未示出)连接,所述阀156使弹簧室保持以预定的最小压力(例如4.5巴的过压)充有增压空气。由此设置气动弹簧123,该气动弹簧123在轴10上提供向上的偏置,并朝向阀座4推动阀碟3。也可使用其它的空气压力,比如从3至10巴的压力。根据期望的气动弹簧123的弹簧性能来选择该最小压力。有可能将若干个不同汽缸上的弹簧室127相互连接,但优选地,每个弹簧室127通过处于增压空气供应下的止回阀而被分别隔开。弹簧室127中的增压空气在弹簧活塞125上、并由此在轴10上产生持久的向上的作用力。因此持久地朝着阀座4、即以向上的方向推进阀碟3。当弹簧活塞125通过阀致动器109(见下文)而向下移动并压缩弹簧室127中的空气时,向下的作用力增加;该止回阀156避免弹簧室127中的空气流出。外壳128限定了围绕并位于气动弹簧123之上的腔129。所述腔被连接至排水管(未示出),使得所述腔具有大气压力。液压阀致动器109由致动器汽缸131和轴10的致动器部分10’构成。致动器汽缸131可以由外壳128的顶部支撑,或如所示,致动器汽缸131和外壳128形成为一个整体件。轴10的致动器部分10’被容纳在致动器汽缸131中的中心孔6(参见例如图3)内,致动器汽缸形成阀致动器109的固定外壳,中心孔6形成轴孔5的上部。中心孔6通过顶部罩132而在致动器汽缸131的顶部闭合,并对致动器汽缸131的底部开启,使得中心孔6与轴孔5的剩余部分连通。中心孔6与轴孔5同轴地配置在外壳128中,并进一步被配置在排气阀1的下部中。现在参考图4,其示出了排气阀1的阀致动器109的顶部的特写,致动器汽缸131的中心孔6被分成具有不同直径(或横截面积)的同轴部分:最上部分6’具有最大直径,中间部分6’’具有中间直径,最下部分6’’’具有最小直径。在最上部分6’和中间部分6’’之间形成第一面朝上横档(upwardlyfacingledge)7。在中间部分6’’和最下部分6’’’之间形成第二面朝上横档8。如例如图3和6A所示,中心孔6的最下部分6’’’延伸至阀致动器109的底端,其中阀致动器109被连接至气动弹簧123。中心孔6的最下部分6’’’通过底罩133闭合(参见图3)。底罩133具有孔,其容纳轴10的致动器部分10’的下部的第二缩径段(reduceddiametersection)16’’。参考图3,在中心孔6的最下部分6’’’中形成有两个室。所述室以中心孔6的最下部分6’’’的第一变宽部分65’和中心孔6的最下部分6’’’的第二变宽部分65’’的形式存在。第一变宽部分65’形成在第二变宽部分65’’之上。第一变宽部分65’通过端口83与通道85连通,通道85形成在致动器汽缸131中。第二变宽部分65’’通过端口80与压力导管110连通。在第一变宽部分65’和第二变宽部分65’’之间形成中间部分66,该中间部分66为中心孔6的最下部分6’’’的一部分,并具有相同的直径或横截面积。中间部分66具有上边缘66’(参见图6A)、壁66’’(其具有平行于中心孔6的最下部分6’’’的表面的表面)以及下边缘66’’’。如从图5中可以理解的是,轴10的致动器部分10’具有上部14。上部14具有直径d1。直径d1适合于在中心孔6的最下部分6’’’中滑动。致动器部分10’还具有下部,其被分成三段:第一缩径段(reduceddiametersection)16’,具有与上部14相同直径d1的密封段16,以及在密封段16之下的第二缩径段16’’。第一缩径段16’和第二缩径段16’’可具有相同直径(或横截面积,如果不是圆柱体);或其可以具有不同的直径,但是其两者都小于上部14和密封段16的直径。位置最低的第二段16’’在气动弹簧123中与轴10的中心部分13连接。密封段16(与底罩133一起)密封中心孔6,以避免液压油渗漏到室(chamber)或腔(cavity)129(其中大气压力占优势)中。上部环形表面15形成在轴10的致动器部分10’的上部14的上端14’处。面朝下横档18形成在上部14的下端14’’和第一缩径段16’之间。面朝上横档17形成在第一缩径段16’和段16之间。面朝下横档17’形成在段16和第二缩径段16’’之间。至少一个狭缝19形成于上部14的下端14’’处的外表面中。狭缝或多个狭缝19是细长的,其纵向平行于阀轴10的纵轴A,并且所述狭缝形成为上部14的下端14’’中的凹陷或凹槽。每个狭缝19具有上端19’和下端19’’。每个狭缝19具有朝着其下端19’’和所述面朝下横档18增加的深度,并且所述狭缝19通向(openinto)所述面朝下横档18。可以设置一个狭缝,或可以围绕上部14的周缘配置一组狭缝。优选地,设置3-20个狭缝19。当存在多于一个的狭缝19时,所有狭缝可具有相同的长度(在轴A的方向上从上端19’到下端19’’)。在可替换实施例中(未示出),狭缝19具有不同的长度。在另一个实施例中(未示出),可替换地,狭缝19可形成于中间部分66的壁中,所述中间部分66为中心孔6的最下部分6’’’的一部分。狭缝或多个狭缝19是细长的,其纵向平行于轴10的纵轴A,并且所述狭缝形成为中间部分66中的凹陷或凹槽。每个狭缝19具有上端19’和下端19’’。每个狭缝19具有朝着其上端19’和中间部分66的上边缘66’增加的深度,并且所述狭缝19通向(openinto)所述第一变宽部分65’。可以设置一个狭缝,或可以围绕中间部分66的周缘配置一组狭缝。优选地设置3-20个狭缝19。当存在多于一个的狭缝19时,所有狭缝可以具有相同的长度(在轴A的方向上从上端19’到下端19’’)。在可替换实施例中(未示出),狭缝19具有不同的长度。在另一个实施例中(未示出),狭缝19如上所述地形成在中间部分66中以及轴10的上部14的下端14’’中。在该应用中,通过凹槽和凹陷,狭缝被理解为是具有相对于另一个表面而压制形成的底面的构造。这里,另一个表面是轴10的圆柱形上部14的外表面。在狭缝19形成于中心孔6的最下部6’’’的中间部分66中的情况下,另一个表面为该位置处的孔6的壁。活塞90可滑动地配置在中心孔6(形成轴孔5的上部)中。活塞90具有汽缸主部91和配置在主部91之上的套管92。活塞90具有中心孔90’,其适于在其上端11处可滑动地容纳轴10的上部14。套管92具有比活塞90的主部91更大的直径(或横截面积)。主部91的直径与微小的空隙相适配,从而可滑动地配置在中心孔6的中部6’’(也可称为中间部分6’’)中。套管92的直径与微小的空隙相适配,从而可滑动地配置在中心孔6的最上部分6’中。在套管92和主部91之间,面朝下内部横档93形成于活塞90的中心孔90’中。内部横档93适于与轴10的上部环形表面15的至少外部配合。活塞90还具有形成在套管92上的面朝上上部表面94。套管92上的该上表面94为环形,类似于轴10的上部环形表面15。然而,上表面94的表面积比轴10的上部环形表面15的面积大得多。面朝下外部横档95形成在套管92和活塞90的外部表面上的主部91之间。主部91还具有下表面96。该下表面96为环形(ring)或环纹形(annular)。阻尼室81形成在顶部罩132中,该阻尼室81通向(openinto)中心孔6的最上部分6’。阻尼室81在排气阀1开启阶段期间提供液压流体入口,在排气阀1关闭期间提供液压流体出口,并且其对轴的向上运动进行制动,进一步参见下文。阻尼室81通向致动器汽缸131内的中心孔6。如上所述,活塞90可相对于轴10的上端11处的上部14、并相对于中心孔6的部分6’、6’’和6’’’滑动。可变体积阀致动室60被限定在中心孔6的上部6’、顶部罩132的面朝下表面132’、阻尼室81、活塞90的面朝上顶部表面和轴10的上部11之间。可变体积阀致动室60也包括阻尼室81。优选地,中心孔6的上部6’和阻尼室81通过圆锥表面32的最下部分和阻尼室81的壁之间的微小空隙形成永久的流体连通。可替换地或另外地,一组狭缝39容许中心孔6的上部6’和阻尼室之间形成永久的流体连通。如所提到的,通过端口80将液压流体提供至阀致动器109并将其从阀致动器109排出。端口80与压力导管110连接,压力导管的端部110’可参见图6A。通过控制阀117,经由压力导管110将端口80交替地连接至高压源和返回线路122。可变体积阀致动室60经由阻尼室81中的端口82、经由导管85(参见图6A)和端口83连接至第一压力室65。第一压力室65被限定在-中心孔6的最下部分6’’’,-轴10的上部10’的部分14,-中心孔6的第一变宽部分65’,-中心孔6的第二变宽部分65’’,和-形成于轴10的上部缩径段16’和下部缩径段16’’之间的、轴10的密封段16,之间。供给端口80连接至第二变宽部分65’’。第二变宽部分65’’通过中心孔6的部分6’’’’(参见图3)连接至第一变宽部分。至少一个端口83将第一变宽部分65’连接至通道85(每个端口83一个通道85)。每个通道85通过通道85和阻尼室81之间的端口82连接至阻尼室81。再次参考图4,滑块30形成于轴的上端11内的孔20中,该滑块通过弹簧40向上偏置,并可在孔20的长度方向上(平行于轴A)滑动。滑块30具有面朝上表面31和圆锥表面32(参见图5),该圆锥表面适于与上述阻尼室81配合,以便在排气阀关闭过程中对轴10的向上行程进行制动。滑块30用作阀轴长度调节机构。在其它实施例中,可替换地,可形成轴10的上端11而不具有该阀轴长度调节机构,使得轴具有固定长度。在这种情况下(未示出),面朝上表面31可以与环形表面15齐平,相应的圆锥表面32直接形成在轴10上部14上的上端上。参考图6A-H,其将描述排气阀的开启和关闭循环。当排气阀即将开启从而从燃烧室106中排空燃料气体或废气时,燃烧室106中的压力非常高。因此,在阀碟3和阀轴10初始向下行进期间,需要较大的力开启排气阀1。如下文将描述的,通过增加阀致动器109的压力表面的有效面积,活塞90将有助于该初始阶段。为了开启排气阀1,控制阀117提供高压流体至端口80,且该液压流体对第一压力室65和可变体积阀致动室60加压(经通道85)。流动由图6A中的箭头301表示。在第一压力室65中,液压流体作用在位于轴10的上部缩径段16’和段16之间的面朝上横档17上。下面将提供关于第一压力室65和其功能的更多细节。通过由通道85提供的流体连接而流入的液压流体将增大可变体积阀致动室60中的压力,该可变体积阀致动室60由阻尼室81和中心孔6的最上部分6’组成。压力作用在滑动块30的表面31上、轴10的上表面15上和活塞90的上表面94上,从而以向下方向一起移动轴10与活塞90。图6B中的箭头302表示存在流入第一压力室65的液压流体,其增大了压力室中的压力。该压力作用于轴段16上的面朝上横档17上,从而以向下方向推动轴,以便开启排气阀1。液压流体增加了可变体积阀致动室60中的压力,该压力作用在轴90的上表面94上、上部环形表面15上和轴10的上部11的上表面31上(以及面朝上横档17上)。面朝下内部横档93紧靠在轴10的上环形表面15的一部分上,这将以向下方向推动轴10和活塞90(参见图6B)。在以向下的方向运行一定距离后,在紧靠在介于中心孔6的最上部和中间部分6’、6’’之间的面朝上横档7上之前,活塞90的面朝下外部横档95将到达并停止,参见图6B。凹槽99(参见图4)形成为中心孔6的孔最上部分6’’中的细长凹陷,并平行于伸长轴B,该凹槽容许液压流体在活塞90之上的空间和活塞90之下的空间之间通过。由于活塞90被向下推动(下表面95的面积小于面朝上表面94的面积),液压流体从活塞90的下方移动至活塞90上方。该凹槽或多个凹槽99在形成于中心孔6的最上部分和中间部分6’、6’’之间的横档7之上的一定距离处终止。当活塞90的面朝下外部横档95经过该凹槽或多个凹槽99的底部时,液压流体无法从活塞90之下的空间移动至上方空间。这会引起活塞90之下的空间中的压力的增加,该活塞的向下运动会减慢并最终停止。由此,形成了小的液压流体压力室,以用于对活塞90的向下行进进行制动,这种小的液压流体压力室起到类似液压弹簧的作用。因此,当轴10继续其向下运动时,活塞90停止向下运动,参见图6C。而且,这避免了活塞的向下行进。在图6C中,当轴10继续其向下运动时,活塞90仍然通过面朝上横档7而静止。致动器部分10’的上部14已经相对于活塞90向下移动。因此,活塞90为可变体积阀致动室60中的压力提供更大面积,以便在开启排气阀期间作用于其上,由此起到加速机构的作用,并有助于抵抗燃烧室106的高压而开启排气阀。一旦已将阀碟3从阀座4移开,由于燃烧气体经过排气导管107离开室106,燃烧室106中的压力降低。因此,为了保持排气阀1的向下移动从而完全开启排气阀,需要比最初开启时更小的力。因此,在活塞90停止后,可变体积阀致动室60中的压力会只作用在上部环形表面15上以及轴10的上部11的上表面31上(这里的上表面31被设置在滑块30上)。由此,轴10会继续其向下的运动,直至轴10的上部14上的面朝下横档18切断液压流体至可变体积阀致动室60的流动,并且轴10开始减速并停止。将在下面对其进行更详细的解释。在排气阀1开启阶段中,在轴10向下行进期间,轴10的上部14上的面朝下横档18会经过形成于上部和下部变宽部分65’和65’’之间的中心孔的中间部分66上的上边缘66’。这种情况如图6C例示。面朝下横档18经过上边缘66’将开始切断流向通道85的流动,并由此切断流向可变体积阀致动室60的流动。形成于轴10的上部14的下端中的狭缝或多个狭缝19将容许流体流至可变体积阀致动室60,直至狭缝19的上端19’已通过中心孔的中间部分66上的上边缘66’。因此,从狭缝19的下端19’’至上端19’,狭缝19提供流至可变体积阀致动室60的逐渐缩小的流动面积。在图6C中,这通过缩短的箭头303例示。流至可变体积阀致动室60的这种逐渐减少的流动将引起对轴10的向下运动的制动,因为可变体积阀致动室60中的压力是通过由气动弹簧123提供的、以向上方向作用的压力来平衡的。在图6D中示出了狭缝19的上端19’已经通过上边缘66’。不存在流至可变体积阀致动室60的流动。而且,轴10已经进一步向下行进了较短的距离,使得轴10的段16上的面朝下横档17’近靠(closetoabutmenton)在底罩133上。轴10已被制动并慢慢停止。压力仍然作用在横档17上(如在图6D中由箭头304表示)和可变体积阀致动室60中,以平衡由气动弹簧123提供的压力,并保持排气阀1开启,直至燃烧室106已被完全排空。已示出了狭缝19以对现有技术中用于在排气阀1开启过程中对轴的向下运动进行制动的解决方案提供巨大的改进。使用狭缝19而不是圆锥面已进一步降低了排气阀1处于完全开启位置时的振动。为了关闭排气阀1,当燃烧室106被排空时,通过控制阀117将端口80的连接从高压源改变至返回线路122并且通过容许液压流体经由端口80流返,液压流体供应的压力被切断。气动弹簧123会向上推动轴10,由此开始将上述第二压力室65和可变体积阀致动室60中的液压流体压出。图6E示出了压力被中断的瞬间以及恰好在轴由于气动弹簧123所提供的压力而将启动其向上运动之前的情况。横档17上的压力被减小。轴10的上部14仍阻挡室65’,由此仍可避免可变体积阀致动室60和端口80之间的流动。当气动弹簧123已将轴10向上移动较小距离时,狭缝19的上端19’移动经过形成于上部和下部变宽部分65’和65’’之间的中心孔的中间部分66的上边缘66’。由此,由于狭缝或多个狭缝19朝着面向下横档18具有增加的深度,端口80和通道85(且由此和可变体积阀致动室60)之间的流体连接逐渐开始开启。该流体连接的开启将容许可变体积阀致动室60中的液压流体经由通道85朝着端口80流动。这将引起可变体积阀致动室60中形成进一步的压差,该压差将进一步抵消与由气动弹簧123提供的压力的平衡,并由此使轴的向上运动加速。在图6F中,当该流体连接刚开启时,以短箭头305表示通过通道85的较小流动。在图6G中,横档18已从室65’中移出,该室65’提供用于从可变体积阀致动室60流出的完整通路,如由附图(图6G)中较长的箭头306所表示的。在图6F所示的情况下,只有轴10本身向上移动,活塞90仍然通过面朝上横档7而静止。因此,只有上表面31和环形表面15推动液压流体从可变体积阀致动室60中流出。当轴10向上移动时,如图6G所示,轴10的上部环形表面15会最终紧靠于活塞90的面朝下内部横档93,且推动活塞90与轴10一同从其下端静止位置(其中活塞90的外部横档95通过面朝上横档7而静止)向上移动。由于活塞上表面94大于组合表面15和31,大得多的表面面积此时将作用于可变体积阀致动室60中的液压流体上。这将引起对轴10的向上行进的制动。当轴10的上部11的顶部处的圆锥面32进入阻尼室81时,轴10的向上运动将制动并最终停止,并逐渐关闭中心孔6的上部6’和阻尼室81之间的流体连接。当圆锥面32插入阻尼室中时,通过迫使液压流体经端口80离开阻尼室,大多数残余动能被吸收,且轴10的上部11的上表面33轻轻地靠在顶部罩132的面朝下表面132’上。图6H示出了轴10已到达其顶部位置时的情况,排气阀1关闭并准备开始新的开启和关闭循环。当废气流动经过排气导管107时,即,当排气阀1开启时,位于排气导管107中的阀轴10的一部分上的一组叶片214推动轴10转动。由此,对于排气阀的每一次开启,轴10会至少转动一点。因此,防止了阀碟3、阀座4以及轴10和轴孔5的邻接横档产生更多磨损。上述气动弹簧123可以由返回冲程压力室和活塞表面面积替代,其推动第一活塞到达缩回位置。该实施例(未示出)需要略微改变的控制阀,该控制阀能够将增压液压流体提供至该压力返回冲程室,以用于将活塞推动至缩回位置。如上所述的相同原理可以用于相对于第一活塞的位置而控制返回冲程压力室中的压力。尽管已详细描述了本申请的教导以用于例示的目的,应该理解的是这些细节只用于该目的,且在不背离本申请的教导范围的情况下,本领域技术人员可对其作出改变。在权利要求中使用的术语“包括”不排除其它元件或步骤。权利要求中使用的术语“一”或“一个”不排除多个。单独的处理器或其它单元可以实现权利要求中引述的若干装置的功能。