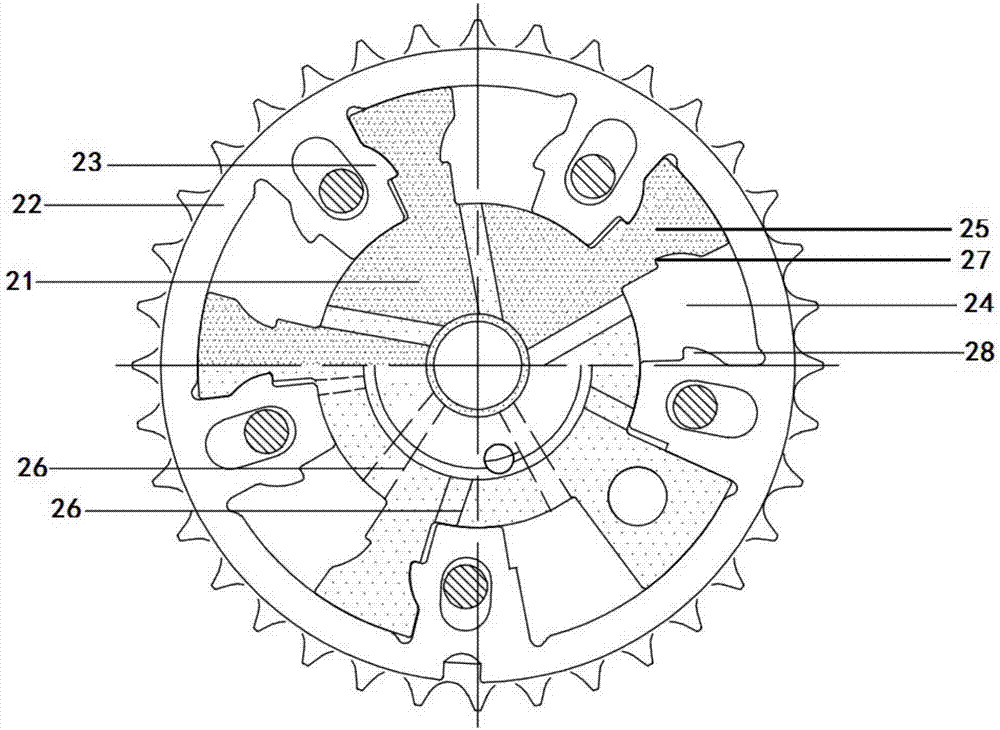
本发明涉及汽车vvt系统的
技术领域:
,更具体地说,本发明涉及一种可变气门正时系统装置。
背景技术:
:可变气门正时系统(vvt系统)在特定的发动机工况下,通过控制进气门开启角度提前和延迟来调节进排气量和时刻和改变气门重叠角的大小,来实现增大进气充量和效率,更好的组织进气涡流,调节气缸爆发压力与残余废气量,来获得发动机功率,扭矩,排放,燃油经济性,舒适性等综合性能的改善,从而解决传统固定配气相位发动机的各项性能指标之间相互制约的技术矛盾。可变气门正时系统一般由相位器和机油控制阀组成,而机油控制阀主要用于油的流量的精确控制,如此才能实现发动机凸轮相位的准确控制,为了保障机油控制阀的使用性能,通常会在机油控制阀的换向杆以及阀体的内部进行硬化和润滑处理,以防止磨损的颗粒尤其是金属或金属化合物颗粒进入电磁驱动器内导致控制稳定性和精度变差。在现有技术中,凸轮轴的进气、排气相位器的转子通常为密封片式或叶片式,它的设计零件多,装配复杂,同时由于转子与定子的结构摩擦大,存在响应速度慢,运转性能差的缺点。同时,在发动机不同转速凸轮轴的扭震状态下,相位器的定子与转子会随着扭震产生噪音,因此,相位器与凸轮轴的联接方式也需要得到改善。技术实现要素:为了解决现有技术中的上述技术问题,本发明的目的在于提供一种可变气门正时系统装置。本发明涉及一种可变气门正时系统装置,其包括排气相位器、进气相位器,排气相位器及进气相位器分别连接一机油控制阀;所述排气相位器包括转子和定子,所述定子的内侧上均匀间隔地设置有多个密封凸壁,在所述定子、转子之间的相邻的密封凸壁之间形成一个油压腔,而所述转子的外侧上均匀间隔地设置有多个油压臂,所述油压臂位于两个相邻的密封凸壁之间并将油压腔分隔成两个部分,所述油压臂的两侧均设有油路孔,油路孔分别与机油控制阀的开启油道及复位油道油路连接,所述的转子内设有连接槽,用于与齿轮连接的连接块卡接安装在连接槽内;所述进气相位器包括转子和定子,所述定子的内侧上均匀间隔地设置有多个密封凸壁,在所述定子、转子之间的相邻的密封凸壁之间形成一个油压腔,而所述转子的外侧上均匀间隔地设置有多个油压臂,所述油压臂位于两个相邻的密封凸壁之间并将油压腔分隔成两个部分,所述油压臂的两侧均设有油路孔,油路孔分别与机油控制阀的开启油道及复位油道油路连接,所述的转子内设有连接槽,用于与齿轮连接的连接块卡接安装在连接槽内。其中,所述转子的油压臂的两侧设置有缓冲槽,所述密封凸壁侧相对应地设置有与所述缓冲槽相配合的缓冲凸起。其中,所述机油控制阀,包括阀基座和阀体,所述阀体的后端固定安装在所述阀基座上;所述阀体内腔的前端上设置有复位弹簧,所述阀体的外壁上从前端至后端依次设置有开启油道、主油道和复位油道;所述阀体内腔中还设置有可沿所述内腔轴向移动的换向杆,所述换向杆上设置有与所述阀体内腔的壁之间滑动配合的凸环,所述凸环上涂覆低摩擦系数膜层,所述换向杆通过设置在所述阀基座内的电磁驱动器驱动。其中,所述低摩擦系数膜层为厚度为2.0~10μm的硼掺杂的碳氮化硅膜层。其中,所述硼掺杂的碳氮化硅膜层中以xps测量的硅:氮:碳:硼的摩尔比为100:85~120:12~35:5~12。其中,所述凸环与所述低摩擦系数膜层之间涂覆厚度为0.10~1.0μm的铬铝硅打底层。其中,所述铬铝硅打底层中,铬的含量为10~25at%,硅的含量为15~35at%,余量为铝。本发明的可变气门正时系统装置具有以下有益效果:本发明的可变气门正时系统装置结构紧凑、装配简单、运转噪音。转子基座与油压臂是一体成型的结构,加工精度更高,可以避免分体装配存在的误差,无需外装密封机构,提高了工作精确性及使用寿命;定子与转子之间有缓冲结构,能够避免转子与定子之间产生直接撞击,消除了运转时的噪音。附图说明图1为本发明的可变气门正时系统装置的装配结构示意图。图2为本发明的可变气门正时系统装置中的相位器的结构示意图。图3为本发明的可变气门正时系统装置中的机油控制阀的结构示意图。图4为本发明的可变气门正时系统装置的示意图。各附图标记所表示的含义分别为:10-机油控制阀,11-阀基座,12-阀体,13-换向杆,14-复位弹簧,15-开启油道,16-主油道,17-复位油道,20-排气相位器,30-进气相位器,21-转子,22-定子,23-密封凸壁,24-油压腔,25-油压臂,26-油路孔,27-缓冲槽,28-缓冲凸起。具体实施方式以下将结合具体实施例对本发明所述的机油控制阀以及可变气门正时系统装置做进一步的阐述,以帮助本领域的技术人员对本发明的发明构思、技术方案有更完整、准确和深入的理解。如图1所示,本发明的可变气门正时系统装置,包括排气相位器20及进气相位器30。排气相位器20及进气相位器30分别连接有一个机油控制阀10。在本发明中,所述排气相位器20以及进气相位器30的结构相同。以下以排气相位器20的结构为例进行描述,如图2所示,所述排气相位器20包括转子21和定子22,所述定子22的内侧上均匀间隔地设置有多个密封凸壁23,在所述定子22、转子21之间的相邻的密封凸壁23之间形成一个油压腔24,而所述转子21的外侧上均匀间隔地设置有多个油压臂25,所述油压臂25位于两个相邻的密封凸壁23之间并将油压腔24分隔成两个部分,所述油压臂25的两侧均设有油路孔26,油路孔26分别与机油控制阀的开启油道15及复位油道17油路连接,所述的转子21内设有连接槽,用于与齿轮连接的连接块卡接安装在连接槽内。所述转子21的油压臂25的两侧设有缓冲槽27,密封凸壁侧相对应地缓冲凸起28。同样地,所述进气相位器包括转子和定子,所述定子的内侧上均匀间隔地设置有多个密封凸壁,在所述定子、转子之间的相邻的密封凸壁之间形成一个油压腔,而所述转子的外侧上均匀间隔地设置有多个油压臂,所述油压臂位于两个相邻的密封凸壁之间并将油压腔分隔成两个部分,所述油压臂的两侧均设有油路孔,油路孔分别与机油控制阀的开启油道及复位油道油路连接,所述的转子内设有连接槽,用于与齿轮连接的连接块卡接安装在连接槽内。所述转子的油压臂的两侧设置缓冲槽,密封凸壁侧相对应地设置缓冲凸起。如图3所示,所述机油控制阀10包括阀基座11和阀体12,所述阀体12的后端固定安装在所述阀基座11上;所述阀体内腔的前端上设置有复位弹簧14,所述阀体的外壁上从前端至后端依次设置有开启油道15、主油道16和复位油道17。所述阀体内腔中还设置有可沿所述内腔轴向移动的换向杆13,所述换向杆上设置有与所述阀体内腔的壁之间滑动配合的凸环,所述凸环上设置有低摩擦系数膜层。如图4所示,机油控制阀的换向杆由电子控制器ecu控制电磁驱动器驱动并在阀体内腔内沿着轴向移动,由进而使开启油道或复位油道或主油道与排气相位器连通,或者使开启油道或复位油道或主油道与进气相位器连通。排气相位器与进气相位器在工作时,刚好为相反设置,即进气相位器开启油道进行增加油压驱动油压臂,此时,排气相位器复位油道进行增加油压驱动油压臂,从而相互配对达到调节的效果。例如,开启油道连接油压臂左侧的油路孔,复位油道连接油压臂右侧的油路孔,当开启油道增加油压时,油压臂左侧收到油压驱动,转向右侧,此时右侧油腔内的油通过油路孔回到复位油道内,通过油路油压的调节改变转子的位置,从而进行调节发动机的进气效果。电子控制器ecu采集发动机转速、发动机载荷、凸轮轴位置传感器、曲轴位置传感器以及水温传感器的信号,并计算确定机油控制阀的输出占空比,驱动系统油路中的机油挤压转子并带动凸轮轴旋转,使凸轮轴相对于曲轴相位提前、滞后或者保持不变,实现正时。具体来说,所述电子控制器ecu由发动机转速和水温得到基本占空比,由凸轮轴目标相位(由发动机转速和发动机载荷确定)和凸轮轴实际相位的差值得到对基本占空比的修正值,然后确定机油控制阀的输出占空比。在本发明中,所述机油控制阀的阀体和换向杆由铝合金制成,例如可以采用6000系列的铝硅镁系铝合金。所述阀体的外壁上加工有油道,而换向杆上加工有与凸环,为了保证控制精度以及凸环与阀体内腔壁之间的滑动配合,所述阀体的内腔壁以及凸环的表面进行精加工,并且涂覆低摩擦系数膜层。由于铝合金的凸环与低摩擦系数膜层之间的热膨胀系数不匹配,首先在铝合金的凸环上涂覆形成铬铝硅打底层,以提高低摩擦系数膜层与凸环之间的结合强度。在涂覆铬铝硅打底层之前,首先对换向杆尤其是凸环部分进行碱洗以去除表面的氧化膜,碱洗后用水漂洗并干燥。然后,将换向杆放置于pvd镀膜设备中,在凸环表面上涂覆铬铝硅打底层,铬铝硅打底层的厚度为0.10~1.0μm,优选为0.20~0.50μm,铬铝硅打底层中,铬的含量为10~25at%,硅的含量为15~35at%,余量为铝。在铬铝硅打底层可采用常规的蒸镀、溅射、离子镀等pvd镀膜方法,优选采用离子镀工艺,在涂覆时作为镀膜对象的换向杆上施加有-300~-600v的偏压。在本发明中,所述低摩擦系数膜层为厚度为2.0~10μm(优选为2.5~8.0μm)的硼掺杂的碳氮化硅膜层,所述硼掺杂的碳氮化硅膜层中以xps测量的硅:氮:碳:硼的摩尔比为100:85~120:12~35:5~12。所述硼掺杂的碳氮化硅膜层是以sih4、n2、c2h2、b2h6作为供给气体,所述膜层可通过等离子增强化学气相沉积方法制备得到,镀膜温度为300~400℃。作为示例性的,首先在离子镀膜设备中在换向杆的凸环表面涂覆铬铝硅打底层,离子镀膜设备中的本底真空度为5×10-3pa,然后通入10~50sccm的氩气,并施加300~500v的直流电压以产生氩等离子进行预溅射以去除换向杆的凸环表面的氧化膜层。然后导入50~100sccm的氩气,并施加400v的直流电压以产生氩等离子体,设置铬铝硅复合靶的电离电压为80v,在换向杆的凸环表面涂覆铬铝硅打底层。采用本发明的铬铝硅打底层与换向杆以及硼掺杂的碳氮化硅膜层之间均表现出良好的匹配性,尤其是在热处理后能够获得良好的结合强度。硼掺杂的碳氮化硅膜层在安装有远程等离子体发生器的等离子增强化学气相沉积装置中涂覆得到,采用的射频电源的频率为13.56mhz,功率为1000w。将镀覆有铬铝硅打底层的换向杆放入沉积装置的镀膜腔之后抽真空至10-5pa,然后通入50~100sccm的氩气,并施加400v的直流电压以产生氩等离子进行预溅射5分钟。然后通入氩气以及反应气体,其中氩气的流量为50~100sccm,sih4的流量为50~200sccm,n2的流量为50~100sccm,c2h2的流量为12~25sccm,b2h6的流量为3~10sccm,镀膜室内压力为0.5~2.5pa,沉积温度为350℃,对换向杆施加的偏压为-400v;沉积后在氩气气氛中进行退火热处理,热处理温度为400℃,时间为30分钟。通过调节各前体的流量,以及涂覆时间等参数可以控制膜层中的si、n、c和b的摩尔比以及膜层的厚度。本发明采用的低摩擦系数膜层通过掺杂适量的硼原子,可显著降低膜层表面的粗糙度,提高耐磨性,而且也不影响膜层与工件之间的结合强度,而且本发明的低摩擦系数膜层中不含金属元素组分,磨损的颗粒进入油中也不会对机油控制阀的控制产生明显影响。在本发明中,当掺杂的硼原子含量超过上限时,不仅对降低膜层的粗糙度无益处,而且还会影响与换向杆凸环之间的结合强度,从而表现出差的耐磨性。而当掺杂的硼原子低于下限时同样表现出差的耐磨性。表1示出了不同厚度和组成(通过x射线光电子能谱xps分析)的实施例和对比例。表1采用nanotest600测试硬度(berkovitch型锥型金刚石压头)以及摩擦系数(摩擦对象为半径为5μm的不锈钢球,载荷为8mn,滑动速率为100nm/s)、参照gb/t1031-2009测量膜层的表面粗糙度ra,参照德国工程师手册(vdi3198)压入法测量膜层的结合强度,参照标准dinen1071-6:2006-01测量膜层的耐磨性,其结果如表2和3所示。表2实施例1实施例2实施例3实施例4实施例5实施例6硬度(gpa)15.515.115.315.315.816.8摩擦系数μ0.040.040.040.040.040.05粗糙度ra(μm)0.0350.0380.0250.0250.0320.042结合强度hf1hf1hf1hf1hf1hf1磨损量(m3m-1n-110-15)0.50.50.30.30.50.6表3对比例1对比例2对比例3对比例4对比例5对比例6硬度(gpa)15.813.215.715.816.213.6摩擦系数μ0.040.080.040.040.060.06粗糙度ra(μm)0.0320.0750.0300.0330.0720.065结合强度hf4hf4hf2-3hf2-3hf1hf2-3磨损量(m3m-1n-110-15)剥离剥离大于5大于10大于5大于10对于本领域的普通技术人员而言,具体实施例只是对本发明进行了示例性描述,显然本发明具体实现并不受上述方式的限制,只要采用了本发明的方法构思和技术方案进行的各种非实质性的改进,或未经改进将本发明的构思和技术方案直接应用于其它场合的,均在本发明的保护范围之内。当前第1页12