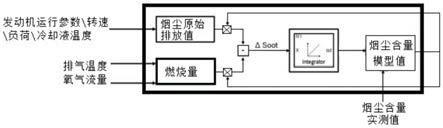
[0001]
本发明涉及汽车控制技术领域,特别涉及一种汽油颗粒过滤器的烟尘含量模型值建立方法和系统。
背景技术:[0002]
在汽车发动机中,改进喷射方式(如pdi双喷、pfi高压喷射等)、优化发动机标定等机内净化措施可以保证发动机pn排放符合当前cn6b法规要求,但是当发动机老化或法规加严后这些措施可能会不满足排放要求,比如发动机积炭、比较激进的驾驶循环或包含冷机排放的rde。汽油发动机的颗粒过滤器(gpf)是汽油发动机的颗粒物捕集装置,其基本原理是当发动机排气经过迷宫式载体时捕获排气中的颗粒物(如图1所示),捕集效率可以达到60~90%,因此gpf可以提高颗粒物排放的鲁棒性,同时gpf带有涂覆,具备一定的气态排放物转化能力,可以降低气体排放。
[0003]
当gpf中累积的颗粒物达到一定程度后排气背压会升高,背压升高到对发动机动力、经济性和安全性产生明显负面影响时需要再生,即烧掉(或氧化)gpf中的以烟尘(soot)为主的颗粒物。再生通常可以分为被动再生和主动再生,主动再生是通过推迟点火等措施来提高排气温度并采用稀燃的方式增加含氧量来实现的。主动再生开始的前提是发动机控制器(ecu)要获取gpf中soot含量这一关键信息,如果计算的soot模型值偏小,那么再生时gpf内部温度超高就有可能烧毁gpf,而如果soot模型值偏大,那么会出现频繁的主动再生,影响油耗或驾驶性能,同时如果再生周期小于4000km就会被认定为周期性再生,对气态排放物指标也是不利的,因此在gpf项目上需要获得较为准确的soot值。
技术实现要素:[0004]
本发明的目的在于提供一种汽油颗粒过滤器的烟尘含量模型值建立方法和系统,以解决现有的烟尘含量模型不正确带来的烧毁颗粒过滤器或影响油耗和驾驶性能的问题。
[0005]
为解决上述技术问题,本发明提供一种汽油颗粒过滤器的烟尘含量模型值建立方法,所述汽油颗粒过滤器的烟尘含量模型值建立方法包括:
[0006]
通过在发动机的台架或转毂上测量得到烟尘原始排放值;
[0007]
根据发动机传感器测量得到烟尘燃烧速率,所述烟尘燃烧速率乘以燃烧时间得到燃烧量;
[0008]
所述烟尘原始排放值和所述燃烧量相减并积分得到烟尘含量模型值;
[0009]
测量烟尘燃烧消耗氧气量,根据所述烟尘燃烧消耗氧气量,结合燃烧消耗氧气的物理模型,得到烟尘含量实测值;
[0010]
将所述烟尘含量实测值与所述烟尘含量模型值进行比较,并根据所述烟尘含量实测值修正所述烟尘含量模型值。
[0011]
可选的,在所述的汽油颗粒过滤器的烟尘含量模型值建立方法中,所述测量烟尘燃烧消耗氧气量包括:
[0012]
第一氧传感器测量所述汽油颗粒过滤器入口排气的氧含量,得到第一氧气含量值;
[0013]
第二氧传感器测量所述汽油颗粒过滤器出口排气的氧含量,得到第二氧气含量值;
[0014]
在汽油颗粒过滤器再生起始时刻和汽油颗粒过滤器再生结束时刻之间,对第一氧气含量值与第二氧气含量值的差值进行积分,得到所述烟尘燃烧消耗氧气量。
[0015]
可选的,在所述的汽油颗粒过滤器的烟尘含量模型值建立方法中,通过在发动机的台架或转毂上测量得到烟尘原始排放值包括:输入发动机运行参数、转速、负荷和冷却液温度,并根据发动机运行参数、转速、负荷和冷却液温度计算所述烟尘原始排放值。
[0016]
可选的,在所述的汽油颗粒过滤器的烟尘含量模型值建立方法中,根据发动机传感器测量得到烟尘燃烧速率包括,根据发动机中的温度传感器获得排气温度,根据发动机中的氧传感器获得氧气流量,根据所述排气温度和所述氧气流量计算得到烟尘燃烧速率。
[0017]
可选的,在所述的汽油颗粒过滤器的烟尘含量模型值建立方法中,结合燃烧消耗氧气的物理模型,得到烟尘含量实测值包括,碳加氧气生成二氧化碳,所述烟尘含量实测值等于所述烟尘燃烧消耗氧气量乘以3/8。
[0018]
本发明还提供一种汽油颗粒过滤器的烟尘含量模型值建立系统,所述汽油颗粒过滤器的烟尘含量模型值建立系统包括烟尘原始排放值计算模块、发动机传感器和烟尘燃烧消耗氧气量测量模块,其中:
[0019]
所述烟尘原始排放值计算模块在发动机的台架或转毂上测量得到烟尘原始排放值;
[0020]
所述发动机传感器测量得到烟尘燃烧速率,所述烟尘燃烧速率乘以燃烧时间得到燃烧量;
[0021]
所述烟尘原始排放值和所述燃烧量相减并积分得到烟尘含量模型值;
[0022]
所述烟尘燃烧消耗氧气量测量模块测量烟尘燃烧消耗氧气量,根据所述烟尘燃烧消耗氧气量,结合燃烧消耗氧气的物理模型,得到烟尘含量实测值;
[0023]
将所述烟尘含量实测值与所述烟尘含量模型值进行比较,并根据所述烟尘含量实测值修正所述烟尘含量模型值。
[0024]
可选的,在所述的汽油颗粒过滤器的烟尘含量模型值建立系统中,所述烟尘燃烧消耗氧气量测量模块包括第一氧传感器和第二氧传感器,其中:
[0025]
所述第一氧传感器测量所述汽油颗粒过滤器入口排气的氧含量,得到第一氧气含量值;
[0026]
所述第二氧传感器测量所述汽油颗粒过滤器出口排气的氧含量,得到第二氧气含量值;
[0027]
在汽油颗粒过滤器再生起始时刻和汽油颗粒过滤器再生结束时刻之间,对第一氧气含量值与第二氧气含量值的差值进行积分,得到所述烟尘燃烧消耗氧气量。
[0028]
在本发明提供的汽油颗粒过滤器的烟尘含量模型值建立方法和系统中,通过测量烟尘燃烧消耗氧气量,根据所述烟尘燃烧消耗氧气量,结合燃烧消耗氧气的物理模型,得到烟尘含量实测值,将所述烟尘含量实测值与事先得到的烟尘含量模型值进行比较,并根据所述烟尘含量实测值修正所述烟尘含量模型值,可以实现在实际使用过程中修正烟尘含量
模型值,避免频繁再生增加油耗或者再生过迟带来的安全风险,解决了现有的烟尘含量模型不正确带来的烧毁颗粒过滤器或影响油耗和驾驶性能的问题。
附图说明
[0029]
图1是现有的汽油颗粒过滤器示意图;
[0030]
图2是本发明一实施例的汽油颗粒过滤器的烟尘含量模型值建立方法示意图;
[0031]
图3是本发明另一实施例的汽油颗粒过滤器的烟尘含量模型值建立系统示意图;
[0032]
图4是本发明另一实施例的汽油颗粒过滤器的烟尘含量模型值建立方法示意图;
[0033]
图5是本发明另一实施例的汽油颗粒过滤器的烟尘含量模型值建立方法示意图;
[0034]
图中所示:10-汽油颗粒过滤器;20-第一氧传感器;30-第二氧传感器。
具体实施方式
[0035]
以下结合附图和具体实施例对本发明提出的一种汽油颗粒过滤器的烟尘含量模型值建立方法和系统作进一步详细说明。根据下面说明和权利要求书,本发明的优点和特征将更清楚。需说明的是,附图均采用非常简化的形式且均使用非精准的比例,仅用以方便、明晰地辅助说明本发明实施例的目的。
[0036]
本发明的核心思想在于提供一种汽油颗粒过滤器的烟尘含量模型值建立方法和系统,以解决现有的烟尘含量模型不正确带来的烧毁颗粒过滤器或影响油耗和驾驶性能的问题。
[0037]
为实现上述思想,本发明提供了一种汽油颗粒过滤器的烟尘含量模型值建立方法和系统,所述汽油颗粒过滤器的烟尘含量模型值建立方法包括:通过在发动机的台架或转毂上测量得到烟尘原始排放值;根据发动机传感器测量得到烟尘燃烧速率,所述烟尘燃烧速率乘以燃烧时间得到燃烧量;所述烟尘原始排放值和所述燃烧量相减并积分得到烟尘含量模型值;测量烟尘燃烧消耗氧气量,根据所述烟尘燃烧消耗氧气量,结合燃烧消耗氧气的物理模型,得到烟尘含量实测值;将所述烟尘含量实测值与所述烟尘含量模型值进行比较,并根据所述烟尘含量实测值修正所述烟尘含量模型值。
[0038]
<实施例一>
[0039]
目前主要由烟尘原始排放值积分来计算烟尘含量,如图2所示,该方法通过在台架或转毂上测量得到烟尘原始排放值(输入是发动机运行参数,如转速、负荷、冷却液温度等),并根据排气温度和氧气流量实测得到烟尘燃烧速率,烟尘原始排放量(soot emission)和燃烧量(soot burn-off)两者相减并积分得到烟尘含量模型值。该方法需要占用大量的台架和转毂资源,且根据已有项目经验该方法的计算精度约+/-50%,精度不高。
[0040]
为了解决上述问题,本实施例提供一种汽油颗粒过滤器的烟尘含量模型值建立方法,如图5所示,所述汽油颗粒过滤器的烟尘含量模型值建立方法包括:通过在发动机的台架或转毂上测量得到烟尘原始排放值;根据发动机传感器测量得到烟尘燃烧速率,所述烟尘燃烧速率乘以燃烧时间得到燃烧量;所述烟尘原始排放值和所述燃烧量相减并积分得到烟尘含量模型值;测量烟尘燃烧消耗氧气量,根据所述烟尘燃烧消耗氧气量,结合燃烧消耗氧气的物理模型,得到烟尘含量实测值;将所述烟尘含量实测值与所述烟尘含量模型值进行比较,并根据所述烟尘含量实测值修正所述烟尘含量模型值。
[0041]
具体的,如图3所示,在所述的汽油颗粒过滤器的烟尘含量模型值建立方法中,所述测量烟尘燃烧消耗氧气量包括:第一氧传感器20测量所述汽油颗粒过滤器10入口排气的氧含量,得到第一氧气含量值;第二氧传感器30测量所述汽油颗粒过滤器10出口排气的氧含量,得到第二氧气含量值;图4是汽油颗粒过滤器在再生时刻前后空燃比变化示意图,如图4所示,在汽油颗粒过滤器再生起始时刻和汽油颗粒过滤器再生结束时刻之间,对第一氧气含量值与第二氧气含量值的差值进行积分,得到所述烟尘燃烧消耗氧气量。
[0042]
另外,如图5所示,在所述的汽油颗粒过滤器的烟尘含量模型值建立方法中,通过在发动机的台架或转毂上测量得到烟尘原始排放值包括:输入发动机运行参数、转速、负荷和冷却液温度,并根据发动机运行参数、转速、负荷和冷却液温度计算所述烟尘原始排放值。根据发动机传感器测量得到烟尘燃烧速率包括,根据发动机中的温度传感器获得排气温度,根据发动机中的氧传感器获得氧气流量,根据所述排气温度和所述氧气流量计算得到烟尘燃烧速率。结合燃烧消耗氧气的物理模型,得到烟尘含量实测值包括,碳加氧气生成二氧化碳,所述烟尘含量实测值等于所述烟尘燃烧消耗氧气量乘以3/8。
[0043]
综上,上述实施例对汽油颗粒过滤器的烟尘含量模型值建立方法和系统的不同构型进行了详细说明,当然,本发明包括但不局限于上述实施中所列举的构型,任何在上述实施例提供的构型基础上进行变换的内容,均属于本发明所保护的范围。本领域技术人员可以根据上述实施例的内容举一反三。
[0044]
<实施例二>
[0045]
本发明还提供一种汽油颗粒过滤器的烟尘含量模型值建立系统,所述汽油颗粒过滤器的烟尘含量模型值建立系统包括烟尘原始排放值计算模块、发动机传感器和烟尘燃烧消耗氧气量测量模块,其中:所述烟尘原始排放值计算模块在发动机的台架或转毂上测量得到烟尘原始排放值;所述发动机传感器测量得到烟尘燃烧速率,所述烟尘燃烧速率乘以燃烧时间得到燃烧量;所述烟尘原始排放值和所述燃烧量相减并积分得到烟尘含量模型值;所述烟尘燃烧消耗氧气量测量模块测量烟尘燃烧消耗氧气量,根据所述烟尘燃烧消耗氧气量,结合燃烧消耗氧气的物理模型,得到烟尘含量实测值;将所述烟尘含量实测值与所述烟尘含量模型值进行比较,并根据所述烟尘含量实测值修正所述烟尘含量模型值。
[0046]
如图3所示,在所述的汽油颗粒过滤器的烟尘含量模型值建立系统中,所述烟尘燃烧消耗氧气量测量模块包括第一氧传感器20和第二氧传感器30,其中:所述第一氧传感器20测量所述汽油颗粒过滤器10入口排气的氧含量,得到第一氧气含量值;所述第二氧传感器30测量所述汽油颗粒过滤器10出口排气的氧含量,得到第二氧气含量值;在汽油颗粒过滤器10再生起始时刻和汽油颗粒过滤器10再生结束时刻之间,对第一氧气含量值与第二氧气含量值的差值进行积分,得到所述烟尘燃烧消耗氧气量。
[0047]
如图4所示,t1是汽油颗粒过滤器10再生起始时刻,在汽油颗粒过滤器10再生前,汽油发动机排气中几乎没有多余的氧气,汽油颗粒过滤器10进出口的氧气含量值是相等的,当发生再生时,排气中有过量的氧气,氧气和汽油颗粒过滤器10中的烟尘发生反应会消耗一部分氧气,这样汽油颗粒过滤器10出口的氧气含量值和入口的氧气含量值出现偏差,出口的氧气含量值小于入口的氧气含量值。
[0048]
进一步的,t2表示汽油颗粒过滤器10再生结束时刻,再生结束后汽油颗粒过滤器10进出口的氧气含量值又保持一致。根据如下公式
[0049][0050]
可得到一次再生所消耗的氧气量,其中,lambda1为第一氧气含量值,lambda2为第二氧气含量值,m
o2
为烟尘燃烧消耗氧气量,再根据公式
[0051]
c+o2→
co2ꢀꢀ
(2)
[0052]
烟尘完全反应公式(氧气过量且排气流速较慢,比如断油被动再生工况,比如二次空气喷射再生工况),可以得到烟尘含量实测值:
[0053][0054]
其中,m
soot
为烟尘含量实测值,得到烟尘含量实测值后去修正模型,最终得到精度更高的烟尘含量模型值。
[0055]
在本发明提供的汽油颗粒过滤器的烟尘含量模型值建立方法和系统中,通过测量烟尘燃烧消耗氧气量,根据所述烟尘燃烧消耗氧气量,结合燃烧消耗氧气的物理模型,得到烟尘含量实测值,将所述烟尘含量实测值与事先得到的烟尘含量模型值进行比较,并根据所述烟尘含量实测值修正所述烟尘含量模型值,可以实现在实际使用过程中修正烟尘含量模型值,避免频繁再生增加油耗或者再生过迟带来的安全风险,解决了现有的烟尘含量模型不正确带来的烧毁颗粒过滤器或影响油耗和驾驶性能的问题。
[0056]
本发明用于提高基于原始排放计算烟尘含量模型值的模型精度,较为准确地得到实测烟尘量,并与模型进行比较,然后修正模型值,最终使得模型值逼近实测值。而烟尘实测值来自于烟尘燃烧消耗氧气的物理模型,本方案中氧气的消耗量由氧传感器测量得到,任何通过测量烟尘燃烧消耗的氧气量进而来修正烟尘模型的方案都可以视为本方案的变通设计。
[0057]
本说明书中各个实施例采用递进的方式描述,每个实施例重点说明的都是与其他实施例的不同之处,各个实施例之间相同相似部分互相参见即可。对于实施例公开的系统而言,由于与实施例公开的方法相对应,所以描述的比较简单,相关之处参见方法部分说明即可。
[0058]
上述描述仅是对本发明较佳实施例的描述,并非对本发明范围的任何限定,本发明领域的普通技术人员根据上述揭示内容做的任何变更、修饰,均属于权利要求书的保护范围。