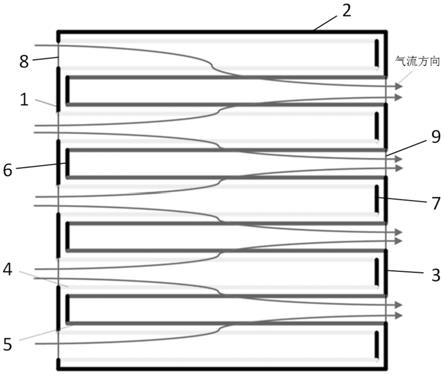
一种柴油机尾气处理用分面涂覆式sdpf系统及其制备方法
技术领域
1.本发明涉及动力机械及工程领域,具体涉及一种柴油机尾气处理用分面涂覆式sdpf系统及其制备方法。
背景技术:2.柴油发动机(柴油机)以其良好的动力性和经济性,广泛地应用于交通运输、农用机械和工程机械等领域。然而柴油机产生了较多颗粒物与氮氧化物(no
x
)排放,对大气环境造成了较大的污染,给居民身体健康也造成了较大的威胁。
3.柴油机颗粒物捕集器(dpf),能够将颗粒物捕集,阻止颗粒物排放到大气中。但dpf在使用过程中会不断地累积颗粒物,使排气背压上升,影响柴油机的正常工作。因此,一般会通过添加催化剂或喷油升温的方式,提高dpf中捕集的颗粒物温度,使颗粒物中的碳烟、有机物等可燃物质氧化,形成气体,排出大气。选择性催化还原器(scr),能够通过喷射的尿素分解出的氨气,通过催化剂选择性地催化还原no
x
,从而降低no
x
排放。由于轻型柴油车的空间限制,因此产生了sdpf——scr催化剂涂覆在dpf表面,从而有效利用了后处理器空间,降低了成本,但是这样的sdpf系统一般只能采用主动再生,会出现油耗增加,dpf的稳定性降低,尿素消耗量增加,减排成本提高等缺点。
技术实现要素:4.本发明的目的就是为了克服上述现有技术存在的缺陷而提供一种油耗低,dpf的稳定性高,尿素消耗量减少,减排成本下降的柴油机尾气处理用分面涂覆式sdpf系统及其制备方法。
5.本发明的目的可以通过以下技术方案来实现:
6.发明人发现,现有的sdpf系统中由于scr催化剂对no2的争夺,导致原本可用于dpf再生的no2被scr还原。这样一来,dpf被动再生温度提高,一般只能采用主动再生,增加了油耗并降低了dpf的稳定性;且消耗了更多的nh3来还原no2,导致尿素消耗量增加,减排成本提高,为解决上述问题采用如下具体方案:
7.一种柴油机尾气处理用分面涂覆式sdpf系统,该系统包括颗粒捕捉器以及设置在颗粒捕捉器上的至少两个进气口和至少一个出气口,所述的进气口与出气口之间沿尾气流动方向依次设有能拦截尾气中颗粒的入口面以及出口面;
8.所述的入口面上涂覆有dpf被动再生催化剂;所述的出口面上涂覆有scr催化剂。
9.这样一来,尾气中的no2会先与入口面上积累的颗粒物利用,在dpf被动再生催化剂的催化作用下起到促进dpf再生的作用后,尾气中的剩余no2再通过出口面中scr催化剂产生的nh3对no2进行还原,避免了no2的争夺问题,也充分利用了dpf中出口面与入口面的空间以涂覆更多的催化剂。
10.进一步地,所述的进气口依次阵列于颗粒捕捉器前侧,进气口之间采用前气体塞进行间隔;所述的出气口依次阵列于颗粒捕捉器后侧,出气口之间采用后气体塞进行间隔。
11.进一步地,所述的进气口数量比出气口数量多一个。
12.进一步地,最端部的前气体塞与后气体塞之间采用侧气体塞相连接。
13.进一步地,相邻的入口面之间采用防止尾气泄露的内后气体塞相连,该内后气体塞与后气体塞位于同侧。
14.进一步地,相邻的出口面之间采用防止尾气泄露的内前气体塞相连,该内前气体塞与前气体塞位于同侧。
15.进一步地,所述的dpf被动再生催化剂包括贵金属pt,所述的scr催化剂包括分子筛或钒基催化剂。
16.一种如上所述的柴油机尾气处理用分面涂覆式sdpf系统的制备方法,该方法包括以下步骤:
17.(1)制备dpf被动再生催化剂涂覆浆液:将dpf被动再生催化剂与去离子水搅拌均匀,研磨至浆液的颗粒度d90为2
‑
20μm,再加入去离子水搅拌均匀,获得浆液;
18.(2)涂覆dpf被动再生催化剂:将入口面竖直放置于定量涂覆专机的涂覆腔处,再将dpf被动再生催化剂涂覆浆液加入到定量涂覆专机的浆料盘中,进行涂覆,后经烘干和焙烧,得到涂有dpf被动再生催化剂的入口面;
19.(3)制备scr催化剂涂覆浆液:将scr催化剂与去离子水搅拌均匀,研磨至浆液的颗粒度d90为2
‑
18μm,再加入去离子水搅拌均匀,获得浆液;
20.(4)涂覆scr催化剂:将出口面竖直放置于定量涂覆专机的涂覆腔处,再将scr催化剂涂覆浆液加入到定量涂覆专机的浆料盘中,进行涂覆,后经烘干和焙烧,得到涂有scr催化剂的出口面。
21.进一步地,步骤(1)中所述的研磨采用行星式球磨机,其转速为250
‑
380r/min,运行时间为3
‑
6h;步骤(2)中所述的烘干温度为100
‑
150℃,烘干时间为3
‑
6h;焙烧温度为450
‑
550℃,焙烧时间为1
‑
2h。
22.进一步地,步骤(3)中所述的研磨采用行星式球磨机,其转速为260
‑
390r/min,运行时间为4
‑
7h;步骤(4)中所述的烘干温度为110
‑
160℃,烘干时间为3
‑
6h;焙烧温度为450
‑
550℃,焙烧时间为1
‑
2h。
23.与现有技术相比,本发明具有以下优点:
24.(1)催化剂可涂覆面积增大,由于采用了分面涂覆,可涂覆面积变成了传统sdpf的两倍,在同样的催化剂负载率下,减少了催化剂聚集的概率,提高sdpf耐久性能;
25.(2)由于消除了scr催化剂对no2的竞争效果,sdpf颗粒物起燃温度低。
附图说明
26.图1为实施例中sdpf系统的结构示意图;
27.图中标号所示:前气体塞1、侧气体塞2、后气体塞3、入口面4、出口面5、内前气体塞6、内后气体塞7、进气口8、出气口9。
具体实施方式
28.下面结合附图和具体实施例对本发明进行详细说明。
29.实施例
30.一种柴油机尾气处理用分面涂覆式sdpf系统,如图1,该系统包括颗粒捕捉器以及设置在颗粒捕捉器上的5个进气口8和4个出气口9,进气口8与出气口9之间沿尾气流动方向依次设有能拦截尾气中颗粒的入口面4以及出口面5;入口面4上涂覆有dpf被动再生催化剂;出口面5上涂覆有scr催化剂。
31.这样一来,尾气中的no2会先与入口面4上积累的颗粒物利用,在dpf被动再生催化剂的催化作用下起到促进dpf再生的作用后,尾气中的剩余no2再通过出口面5中scr催化剂产生的nh3对no2进行还原,避免了no2的争夺问题,也充分利用了dpf中出口面5与入口面4的空间以涂覆更多的催化剂。
32.进气口8依次阵列于颗粒捕捉器前侧,进气口8之间采用前气体塞1进行间隔;出气口9依次阵列于颗粒捕捉器后侧,出气口9之间采用后气体塞3进行间隔。最端部的前气体塞1与后气体塞3之间采用侧气体塞2相连接。相邻的入口面4之间采用防止尾气泄露的内后气体塞7相连,该内后气体塞7与后气体塞3位于同侧。相邻的出口面5之间采用防止尾气泄露的内前气体塞6相连,该内前气体塞6与前气体塞1位于同侧。前气体塞1、内前气体塞6与出气口9在水平方向上对应布置,进气口8、内后气体塞7和后气体塞3在水平方向上对应布置。
33.该柴油机尾气处理用分面涂覆式sdpf系统的制备方法,该方法包括以下步骤:
34.(1)制备dpf被动再生催化剂涂覆浆液:将dpf被动再生催化剂与去离子水搅拌均匀,研磨至浆液的颗粒度d90为2
‑
20μm,再加入去离子水搅拌均匀,获得浆液;其中,研磨采用行星式球磨机,其转速为250
‑
380r/min,运行时间为3
‑
6h;
35.(2)涂覆dpf被动再生催化剂:将入口面4竖直放置于定量涂覆专机的涂覆腔处,再将dpf被动再生催化剂涂覆浆液加入到定量涂覆专机的浆料盘中,进行涂覆,后经烘干和焙烧,得到涂有dpf被动再生催化剂的入口面4;其中,烘干温度为100
‑
150℃,烘干时间为3
‑
6h;焙烧温度为450
‑
550℃,焙烧时间为1
‑
2h
36.(3)制备scr催化剂涂覆浆液:将scr催化剂与去离子水搅拌均匀,研磨至浆液的颗粒度d90为2
‑
18μm,再加入去离子水搅拌均匀,获得浆液;其中,研磨采用行星式球磨机,其转速为260
‑
390r/min,运行时间为4
‑
7h;
37.(4)涂覆scr催化剂:将出口面5竖直放置于定量涂覆专机的涂覆腔处,再将scr催化剂涂覆浆液加入到定量涂覆专机的浆料盘中,进行涂覆,后经烘干和焙烧,得到涂有scr催化剂的出口面5,其中,烘干温度为110
‑
160℃,烘干时间为3
‑
6h;焙烧温度为450
‑
550℃,焙烧时间为1
‑
2h。
38.本实施例中,以贵金属催化剂涂覆量7g/l,scr催化剂60g/l为例,其中,dpf被动再生催化剂为贵金属pt,scr催化剂为分子筛或钒基催化剂,传统sdpf的dpf平衡温度(即dpf碳烟颗粒的捕集速率与再生速率平衡的温度)为300℃,而采用本发明的平衡点温度为275℃,可将dpf主动再生效率从72%提高到80%。
39.以上所述,仅是本发明的较佳实施例而已,并非是对本发明作其它形式的限制,任何熟悉本专业的技术人员可能利用上述揭示的技术内容加以变更或改型为等同变化的等效实施例。但是凡是未脱离本发明技术方案内容,依据本发明的技术实质对以上实施例所作的任何简单修改、等同变化与改型,仍属于本发明技术方案的保护范围。