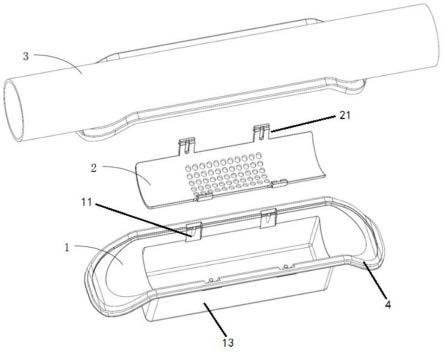
1.本发明涉及消声器技术领域,具体涉及一种宽频消声器结构。
背景技术:2.目前,许多车辆进气系统或燃料电池进、排气系统需要集成宽频消声器以消除或降低车辆进气时所产生的嘶嘶声、喘振声、涡轮增压器泄气声、燃料电池压气机等中高频噪声。
3.现有设计的宽频消声器一般由管路上片、管路下片和消声器盖三部分组成。其中管路上片和下片之间需要通过焊接工艺形成完整的通气管路,通气管路再和消声器盖通过焊接工艺形成集成宽频消声器的通气管路。
4.现有技术中,宽频消声器的结构包括谐振腔盖、集成多孔板的管路上片和管路下片,需要将谐振腔盖和管路上片焊接,再将集成多孔板的管路上片和管路下片焊接,需两道焊接工序才能形成宽频消声器总成。
5.此类方案的问题在于:
6.一:需要经过两道焊接工艺,才成形成完整的,集成宽频消声器的通气管路,制造成本较高。
7.二:子零件形状需要有两道焊接的焊接筋,重量较重。
技术实现要素:8.本发明的目的就是为了克服上述现有技术存在的缺陷而提供一种宽频消声器结构,可降低重量,降低焊接成本。
9.本发明的目的可以通过以下技术方案来实现:一种宽频消声器结构,包括管路上片、消声器多孔板和管路下片,所述的管路上片上设有凹槽,消声器多孔板上设有与凹槽相匹配的卡扣。
10.进一步地,所述的管路上片上集成有谐振腔,消声器多孔板通过卡扣连接到管路上片上,且内嵌于谐振腔的开口处。消声器多孔板不突出于管路内壁。
11.由于注塑工艺的限制,现有技术多将消声器多孔板和管路上片一体成型,另一侧开口,需要用谐振腔盖密封来形成谐振腔,因此需要将谐振腔盖和带有消声器多孔板的管路上片焊接,再将管路上片和管路下片焊接,需两道焊接工序才能形成宽频消声器总成。
12.本发明中的消声器多孔板为单独零件,而将谐振腔与管路上片一体成型,避免了现有技术中谐振腔盖和集成多孔板的管路上片的焊接过程,简化安装步骤,且减少了焊接筋的使用,减轻重量,开口侧通过凹槽结构连接消声器多孔板,消声器多孔板质量轻,结构简单,且无需焊接即可连接管路上片,安装方便。
13.所述的凹槽内设有定位销,所述的卡扣上设有与定位销相匹配的定位孔。组装时,消声器多孔板的定位孔对准管路上片的定位销,将消声器多孔板安装到管路上片中去,在此过程中,定位销和定位孔的形状会起到引导和定位作用,使得卡扣可以安装到凹槽中去,
安装完成后,管路上片和消声器多孔板形成一个整体。
14.进一步地,所述的凹槽有偶数个,对称设置在管路上片的侧壁上,卡扣数目与凹槽相同,对称设置在消声器多孔板的边缘,定位销和定位孔在宽频消声器结构两侧对称设置,每对定位孔外侧壁面之间的距离略小于每对定位销外侧面壁面之间的距离。定位孔和定位销设计为略微干涉,定位孔外侧壁面与定位销外侧壁面的干涉量为0.1~0.5mm,从而实现消声器多孔板紧固地与管路上片卡接在一起,防止在焊接过程中脱落。
15.所述的定位销竖向设置在凹槽上,呈圆台结构,所述的定位孔呈椭圆形长孔结构,竖向设置在卡扣上。此结构方便定位销从定位孔中穿过,提高引导和定位效率,同时增强凹槽和卡扣的连接强度。
16.所述的管路上片和管路下片上均设有焊接筋,管路上片和管路下片通过焊接筋连接。焊接筋通过焊接工艺熔融在一起,完成零件装配。焊接工艺可选用振动摩擦焊、热板焊、红外焊、红外振动摩擦焊、热气焊、激光焊等。焊接筋形状需要匹配所选用的焊接工艺。
17.进一步地,所述的卡扣外侧设有凸块,凹槽上设有与凸块对应的横槽。凸块和横槽的设置可进一步提高凹槽和卡扣连接位置的准确性和连接强度。
18.更进一步地,所述的凸块为长方体或正方体结构,长度为10~20mm,宽度为2~3mm,厚度为2~3mm,所述的横槽的长度、宽度和厚度分别与凸块相同。
19.或者,所述的凸块和横槽为相匹配的弧面结构。
20.所述的横槽设于管路上片的焊接筋上,所述的凸块通过横槽与焊接筋相连。凸块在横槽的长度范围内充当一部分焊接筋的作用,一旦消声器多孔板和管路上片预安装成一个整体后,消声器多孔板的这部分凸块和管路上片的焊接筋一起参与和管路下片的焊接,使得在焊接之后,三个零件形成牢固的总成。
21.本发明通过上述方法将定位孔和定位销设计为略微干涉,加强了凹槽和卡扣的连接强度,使得消声器多孔板在预安装到管路上片后可以卡在管路上片中不会掉落,使得后续的焊接工序可行。
22.宽频消声器组装完成后,集成谐振腔的管路上片和消声器多孔板之间形成了密闭的赫姆霍兹谐振腔,同时管路上片、消声器多孔板和管路下片之间形成了通气管路,消声器多孔板上集成有用于消音的圆孔或方孔或其他形状的用于消音的孔洞,便形成了一个典型的宽频消声器。
23.与现有技术相比,本发明具有以下优点:
24.1.制造成本低:现有设计结构需要两次焊接,而本发明只需要一次焊接就可以形成宽频消声器总成,节省了一次焊接的所需要的制造成本;
25.2.重量轻:现有设计结构需要集成两次焊接的焊接筋,而本发明只需要集成一次焊接的焊接筋,重量更轻,对于达成零部件减重目标和降低原材料成本都能有所贡献,对现有设计的宽频消声器重量可减轻6~8%;
26.3.安装方便:本发明可中的消声器多孔板通过卡扣结构与管路上片上的凹槽相连,且通过定位销和定位孔的引导和定位作用,安装方便快速,定位准确;
27.4.连接强度高:本发明通过定位孔和定位销的略微干涉设计,使消声器多孔板和管路上片连接稳定,不易掉落,使得后续焊接工序可行,凸块通过横槽与焊接筋相连,使凸块兼具焊接筋功能,可通过焊接作用与管路上片和管路下片牢固连接。
附图说明
28.图1为本发明宽频消声器结构的立体图;
29.图2为本发明宽频消声器结构的爆炸图;
30.图3为管路上片结构示意图;
31.图4为管路上片正视图;
32.图5为消声器多孔板结构示意图;
33.图6为消声器多孔板正视图;
34.图7为管路下片结构示意图一;
35.图8为管路下片结构示意图二;
36.图9为管路上片和管路下片安装示意图;
37.图10为管路上片和管路下片安装正视图;
38.图11为对比例1的宽频消声器的爆炸图;
39.图中:1-管路上片,10-定位销,11-凹槽,12-横槽,13-谐振腔,2-消声器多孔板,20-定位孔,21-卡扣,22-凸块,3-管路下片,31-管状结构,32-外侧挡料筋,33-内侧挡料筋,4-焊接筋,5-谐振腔盖。
具体实施方式
40.下面结合附图和具体实施例对本发明进行详细说明。以下实施例在以本发明技术方案为前提下进行实施,给出了详细的实施方式和具体的操作过程,但本发明的保护范围不限于下述的实施例。
41.实施例1
42.一种宽频消声器结构,如图1~2所示,包括管路上片1、管路下片3和位于两者之间的消声器多孔板2。
43.如图3~4所示,管路上片1侧壁上对称设置有4个凹槽11,凹槽11内设有定位销10,且凹槽11顶部设有横槽12,管路上片1上设有一圈焊接筋4,横槽12位于加强筋4上,管路上片1集成有谐振腔13。
44.如图5~6所示,消声器多孔板2上设有多个消音圆孔,边缘对称设置4个与凹槽11相匹配的卡扣21,卡扣21上设有与定位销10相匹配的定位孔20,起到引导和定位作用,使得卡扣21可以安装到凹槽11中去,位于宽频消声器结构两侧的每对定位孔20外侧壁面之间的距离略小于每对定位销10外侧面壁面之间的距离。卡扣21外侧设有凸块22,与横槽12相对应,如图9~10所示,安装完成后,管路上片1和消声器多孔板2形成一个整体,消声器多孔板2内嵌于谐振腔13的开口处,定位销10与定位孔20形成略微干涉,使消声器多孔板2和管路上片1连接稳定,不易掉落,且凸块22安装后与焊接筋4相连,兼具焊接筋的功能,可通过焊接作用与管路上片1和管路下片3牢固连接。
45.如图7~8所示,管路下片3包括管状结构31、一圈外侧挡料筋32、一圈内侧挡料筋33和一圈焊接筋4。
46.在消声器多孔板2通过卡扣21连接至管路上片1内后,管路上片1和管路下片3通过对焊接筋4的焊接作用进行连接,完成组装,管路上片1和消声器多孔板2之间形成了密闭的赫姆霍兹谐振腔,同时管路上片1、消声器多孔板2和管路下片3之间形成了通气管路,消声
器多孔板2上集成有用于消音的圆孔,形成了宽频消声器结构。本宽频消声器管道内径ф55,管道长度412mm,谐振腔容积详0.35l,结构重量为416g。
47.对比例1
48.现有技术的宽频消声器的结构如图11所示,包括谐振腔盖5、集成多孔板的管路上片1和管路下片3,谐振腔盖5、集成多孔板的管路上片1和管路下片3上均设有焊接筋4,需要将谐振腔盖5和集成多孔板的管路上片1焊接,再将集成多孔板的管路上片1和管路下片3焊接,需两道焊接工序才能形成宽频消声器总成。该宽频消声器管道内径、管道长度和谐振腔容积均与新型宽频消声器一致,重量为447g。
49.实施例1与对比例1相比,减重7%,可知,本发明的宽频消声器结构可对现有技术中的宽频消声器进行减重,对于达成零部件减重目标和降低原材料成本都能有所贡献。
50.上述的对实施例的描述是为便于该技术领域的普通技术人员能理解和使用发明。熟悉本领域技术的人员显然可以容易地对这些实施例做出各种修改,并把在此说明的一般原理应用到其他实施例中而不必经过创造性的劳动。因此,本发明不限于上述实施例,本领域技术人员根据本发明的揭示,不脱离本发明范畴所做出的改进和修改都应该在本发明的保护范围之内。