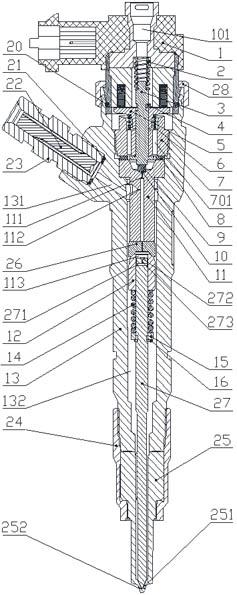
1.本实用新型涉及涉及一种电控高压燃油喷射装置,尤其涉及一种主要用于高压共轨供油系统的具有动态泄流控制的电控共轨喷油器。
背景技术:2.电控高压共轨供油系统是先进的柴油机供油系统。电控高压共轨供油系统有三个最主要的特点,首先该系统不仅能够对高压油泵实现控制,也能够对喷油器实现控制,可以根据燃烧效率、污染物排放和舒适性等的要求在一个工作循环中实现多次喷射;其次电控高压共轨供油系统有一个共同的储油容积,即所谓共同的高压油轨 ,简称“共轨”,高压油泵将燃油压缩后送入这个共同的高压油轨的容积中,再由这个共同的高压油轨将高压燃油输送至各个相应汽缸的电控燃油喷射装置,使各个汽缸的电控燃油喷射装置在相同的喷射压力下进行喷射,从而保证了各缸燃油喷射量和喷射压力的精准性和一致性;第三由于基于高压油泵进油量控制的技术,使得系统的喷射压力能够与发动机转速解耦,因此能够做到系统的喷射压力与发动机转速无关,使不论发动机工作在何种工况,电控高压共轨供油系统都可以提供最佳的喷射压力而不再受发动机转速的影响。电控高压共轨供油系统的这些特点是以往在柴油机上所采用的任何供油系统所不具备的,因此电控高压共轨供油系统成为目前柴油机供油系统的首选。电控高压共轨供油系统主要由电控高压油泵、高压油轨(即所谓“共轨”)、电控高压燃油喷射装置、控制器(即电控单元ecu)、传感器和控制软件等组成,在ecu中存储根据发动机工况的需要编写的控制软件,发动机工作时将驾驶员的意愿以及传感器检测到的发动机的实时工况参数如:转速、负荷、温度、压力等信息输入ecu,再根据ecu的运算结果发送指令到电控高压油泵、电控高压燃油喷射装置,用以控制电控高压油泵输出的油量、压力、以及电控高压燃油喷射装置开始喷射的时刻、喷射的持续时间、一个循环中喷射的次数等。
3.电控高压燃油喷射装置是电控高压共轨供油系统的执行器,包括喷油器本体、置于喷油器本体一端的前置控制部件、置于喷油器本体另一端的燃油喷射部件、设置在喷油器本体内连接前置控制部件和燃油喷射部件的液力放大部件、以及设置在喷油器本体上的进油组件,所述的前置控制部件包括电磁铁和控制阀组件,所述液力放大部件包括活塞套和活塞,所述燃油喷射部件包括针阀和针阀体,喷油器本体上还设置有为电控燃油喷射装置提供高低压燃油的流道、燃油的过滤、密封以及固联等功能的、以及进油组件等零部件。
4.图3和图4示出了现有技术的一种电控高压燃油喷射装置,包括喷油器本体13,所述的喷油器本体13制有多级直径的中心容腔,所述容腔上部台阶平面上依次叠装阀座11、阀杆行程调节垫8,由紧定螺套7固联在喷油器本体13上,阀座11的上部制有锥孔,在锥孔下端一个出油计量孔111与之链接,出油计量孔111下端贯穿至阀座11的底面,阀座11的上部的锥孔与密封球10配合组成线密封结构,密封球10上面依次叠装密封球座9、阀杆3,紧固螺套28将电磁铁1与喷油器本体13固联在一起,电磁铁弹簧2支撑在阀杆3的肩部与电磁铁1容腔台阶平面之间,阀杆3的上部制有环形凹槽,开口垫圈4卡装在所述环形凹槽中,衔铁5同
心套装在阀杆3上,阻尼弹簧6支撑在衔铁5与紧定螺套7之间使衔铁5的上端面抵靠在开口垫圈4的底平面上;油嘴紧固螺套24将针阀体25固联在喷油器本体13的下端平面上。针阀体25同心制出中孔,在所述中孔下端制有锥孔与之相连,在所述锥孔的下端制有一个囊形中心孔的压力室251,放射状分布的喷油孔252一端与所述压力室251相通,另一端通向针阀体25外部;活塞17插装在活塞套12的中孔内,针阀19插装在针阀体25的中孔内,接杆套管18将活塞17与针阀19固联在一起,针阀19下端的锥体与针阀体25下端的锥孔形成一个可开关的密封带, 在针阀17的直径制出的用以将高压盛油腔132内的高压燃油输送到密封带处的直槽,当针阀19开启后高压燃油能够穿过针阀19与针阀体25的密封带,流入压力室251并经喷油孔252喷出。
5.现有技术的电控高压燃油喷射装置的不足在于:在喷射过程中高压燃油的泄流量过大,导致系统的效率降低。喷射开始时在电磁铁1向上抬起阀杆3,密封球10被控制室113内的高压燃油冲起离开阀座11的锥孔,同时控制室113内的高压燃油经由活塞17的顶面与阀座11底面之间的间隙、出油计量孔111、密封球10与阀座11的锥孔之间的间隙流向低压区,使控制室113内压力降低,由于控制室113内压力降低后燃油对活塞17的液压力减小,活塞17和针阀19开始抬起,在针阀19抬起初期由于活塞17的顶面与阀座11底面之间的间隙很大,所以活塞17的顶面与阀座11底面之间的间隙的流阻可以忽略不计,此时对于控制室113的出口而言,影响流出流量大小的主要是出油计量孔111的流通面积以及密封球10与阀座11的锥孔之间的开度两个因素,因此控制室113内的压力下降的速度很快。假如阀座11的下端只是一个圆孔的话,一旦活塞17和针阀19运动到达上死点就会使活塞17的顶平面抵靠在阀座11的下端平面上,将阀座11的下端孔口堵死,通向出油计量孔111的流动即被截断,但此时高压盛油腔132内的燃油仍然通过进油计量孔112流入控制室113内,其结果导致控制室113内燃油压力升高,并驱动活塞17和针阀19下行,使活塞17的顶平面离开阀座11的下端平面,致使通向出油计量孔111的流动再次恢复,又一次导致控制室113内燃油压力降低,再一次使活塞17的顶平面抵靠在阀座11的下端平面上,活塞17和针阀19如此反复振荡不已,结果影响喷射的稳定性。消除喷射振荡的方法就是使活塞17运动到上死点时不再遮盖通往出油计量孔111的出口。图4所示的是现有技术的电控高压燃油喷射装置的阀座11剖面图,由图4可知现有技术的电控高压燃油喷射装置采取的办法是在阀座11的下端平面通往出油计量孔111的出口处制出一个截面积很大的横槽115,使当活塞17和针阀19运动到上死点时控制室113内的燃油能够通过横槽115流向出油计量孔111以保证活塞17和针阀19运动到上死点后的喷射期间不再发生振荡。
6.问题在于所述横槽115的尺寸无法精确控制,因此必须将横槽115的截面做的足够大,过大的横槽115得截面虽能保证确保活塞17和针阀19运动到上死点后的喷射期间不再发生振荡,带来的结果却是流量过大,这些多余的泄流量都是从高压腔流入低压腔的,因而使得电控高压燃油喷射装置的回油量大大增加,以至于影响喷射装置的效率。
技术实现要素:7.本实用新型的目的是针对现有技术的电控高压燃油喷射装置存在的动态泄流量过大的不足之处,提供一种减少动态泄流量的、效率更高的电控高压燃油喷射装置。
8.为此,本实用新型提供了具有动态泄流控制的电控共轨喷油器。本实用新型的具
有动态泄流控制的电控共轨喷油器,包括液力放大部件,所述液力放大部件包括活塞套12和插装在活塞套12的中孔内的活塞17,其特征在于:所述活塞17的顶端两侧对称削扁后制出横孔271,所述活塞17的顶端向下同心制出一个轴向的竖孔272,在竖孔272的下面制出阻尼计量孔273与横孔271相通。
9.在另一个实施例中,所述的活塞套12内插装活塞和针阀一体制造的活塞针阀27,所述的活塞针阀27的顶端两侧对称削扁后制出横孔271,所述的活塞针阀27的顶端向下同心制出一个轴向的竖孔272,在竖孔272的下面制出阻尼计量孔273与横孔271相通,活塞针阀27靠近下端的针阀部分插装在在针阀体25的中心孔中。
10.进一步,所述的阻尼计量孔273的最终直径是先在竖孔272与横孔271之间制出初孔,在装配成成品电控高压燃油喷射装置后通过通入磨削油液将初孔的直径大小扩至泄流量检测合格的尺寸。
11.本实用新型的具有动态泄流控制的电控共轨喷油器具有如下积极效果:
12.通过利用阻尼计量孔273控制活塞17到达上死点后控制室113向低压区的泄流量达从而达到减少动态泄流量的目的。由于活塞17顶端抵住阀座11的下平面后,或者另一个实施例的活塞针阀27顶端抵住活塞套座26的下平面后,通过利用阻尼计量孔273对从控制室流向低压区的流量的控制,使能在活塞17或活塞针阀27到达上死点后既能避免活塞的往复振荡又能使控制室113向低压区的泄流量大大减少,从而能够提高喷射装置的效率。
附图说明
13.图1是本实用新型的具有动态泄流控制的电控共轨喷油器的结构示意图。
14.图2是本实用新型的具有动态泄流控制的电控共轨喷油器的阻尼计量孔的剖视示意图。
15.图3是现有技术的电控高压燃油喷射装置的剖视示意图。
16.图4是现有技术的电控高压燃油喷射装置的横槽115的剖视图。
17.图中:1电磁铁,2电磁铁弹簧,3阀杆,4开口垫圈, 5衔铁,6阻尼弹簧,7紧定螺套,8阀杆行程调节垫,9密封球座,10密封球,11阀座,12活塞套,13喷油器本体,14针阀弹簧,15调整垫,16开口挡圈,17活塞,18接杆套管,19针阀,20电磁铁密封圈,21进油螺栓密封垫,22进油滤芯,23进油螺栓, 24油嘴紧固螺套,25针阀体,26活塞套座,27活塞针阀,28紧固螺套,101低压出油孔,111出油计量孔,112进油计量孔,113控制室,115横槽,131高压进油孔,132高压盛油腔,251压力室,252喷油孔,271横孔,272竖孔,273阻尼计量孔,701低压通油孔。
具体实施方式
18.为进一步说明本实用新型的原理和结构,现结合附图对本实用新型的实施例进行详细说明。
19.本实用新型的具有动态泄流控制的电控共轨喷油器,包括液力放大部件,所述液力放大部件包括活塞套12和插装在活塞套12的中孔内的活塞17,其特征在于:所述活塞17的顶端两侧对称削扁后制出横孔271,所述活塞17的顶端向下同心制出一个轴向的竖孔272,在竖孔272的下面制出阻尼计量孔273与横孔271相通。
20.图1和图2示出了本实用新型的具有动态泄流控制的电控共轨喷油器的另一个实施例,所述的活塞套12内插装活塞和针阀一体制造的活塞针阀27,所述的活塞针阀27的顶端两侧对称削扁后制出横孔271,所述的活塞针阀27的顶端向下同心制出一个轴向的竖孔272,在竖孔272的下面制出阻尼计量孔273与横孔271相通,活塞针阀27靠近下端的针阀部分插装在在针阀体25的中心孔中。
21.进一步,所述的阻尼计量孔273的最终直径是先在竖孔272与横孔271之间制出初孔,在装配成成品电控高压燃油喷射装置后通过通入磨削油液将初孔的直径大小扩至泄流量检测合格的尺寸。
22.进一步,阀座11是具有上大下小的两级同心圆柱体,阀座11安装在喷油器本体13的中心容腔平面之上,阀座11的上平面依次叠装阀杆行程调节垫8,紧定螺套7,所述该紧固螺套将阀座11、阀杆行程调节垫8固联在喷油器本体13中心容腔的台阶平面上,阀座11同心制有中心孔,阀座11小直径圆柱的左侧中上部制有一个横向锥孔,在所述锥孔底部制有一个横向的进油计量孔112与阀座11中心孔相通,阀座11中心孔的上部制有一个出油计量孔111,出油计量孔111上端与锥形孔相连,所述该锥形孔上依次同心安装密封球10、密封球座9、阀杆3,电磁铁弹簧2支撑在阀杆3的上肩部与电磁铁1的中孔容腔平面之间,紧固螺套28同心将电磁铁1固联在喷油器本体13上部,电磁铁密封圈20安装在电磁铁1与喷油器本体13之间起密封低压燃油防止渗漏的作用,在阀杆3的中上部制有同心环形凹槽,开口垫圈4安装在所述阀杆3的凹槽中,衔铁5同心套装在阀杆上,阻尼弹簧6同心支撑在紧定螺套7与衔铁5之间以便保证所述衔铁5在静态时其上平面始终抵靠在开口垫圈4的下平面上。
23.进一步,在阀座11的下平面与活塞套12之间设置活塞套座26,所述的活塞套座26是圆柱形状,底部制出锥孔,在所述锥孔上面制出台阶孔,在所述台阶孔的上面制出小圆孔,活塞套座26的上平面与阀座11的下平面抵靠在一起;活塞套12上端制出球缺形状的球面与所述活塞套座26底部的锥孔相配合形成铰接的线密封结构。活塞套12的中孔套装在活塞针阀27上端部分的活塞直径外面,针阀体25由油嘴紧固螺套24同心固联在喷油器本体的下平面上,
24.进一步,在活塞针阀27中部制有一个同心环形凹槽,开口挡圈16安装在凹槽内,开口挡圈16的上平面同心装有调整垫15,针阀弹簧14支撑在调整垫15的上平面与活塞套12的下平面之间,在活塞针阀27的下部针阀部分的下端制出一个圆锥体,所述圆锥体与针阀体25下部中心容腔的锥孔配合,形成一个可开关的密封带,针阀体25锥孔的下部制有一个称为压力室251的囊形中心孔,放射状分布的喷油孔252一端与所述压力室251相通,另一端通向针阀体25外部, 活塞针阀27与针阀体25配合部分的圆柱体制出轴向凹陷的直槽,既可以对针阀的上下运动起导向作用,又能在喷射时为高压盛油腔132的高压燃油流入压力室提供流道。
25.静态时,控制室113内燃油压力与高压盛油腔132内的燃油压力相等,而控制室113内的燃油对活塞针阀27的向下作用面积大于高压盛油腔132燃油对活塞针阀27的向上的作用面积,再加上针阀弹簧14向下的弹簧力也压在活塞针阀27上,活塞针阀27所受的向下的液压力和弹簧力的合力克服高压盛油腔132燃油对针阀19向上的作用力,使活塞针阀27下端的圆锥体贴合在针阀体25锥孔上形成一道密封带,进而使高压盛油腔132与压力室251隔离开,因此喷射装置不能喷射燃油。
26.喷射时,首先给电磁铁1通电,衔铁5产生一个向上的电磁力,所述该电磁力克服电磁铁弹簧2的弹簧力并带动阀杆3向上运动,与此同时,控制室113内燃油压力直接冲向密封球10,并带动密封球座9一起离开阀座11的密封锥面,控制室内的燃油开始经由出油计量孔111、低压通油孔701、低压出油孔101流低压回油箱,使得控制室113内的燃油压力持续下降,导致活塞针阀27向下的作用力持续减小,另一方面,高压盛油腔132内燃油对活塞针阀27向上的作用力没有变化,当活塞针阀27和针阀弹簧14的弹簧力向下的合力小于高压盛油腔132内燃油对活塞针阀27向上的作用力时,活塞针阀27向上抬起,使高压盛油腔132与压力室251相通,来自高压盛油腔132的高压燃油进入压力室251并经由与压力室251相连通的喷油孔252向外喷射。
27.电磁铁1断电后,电磁力消失,在电磁铁弹簧2的作用下使阀杆3向下运动驱动密封球座9、密封球10落座,将阀座11的锥孔密封,出油计量孔111向外流的路径被切断,但此时高压燃油仍然通过进油计量孔112流入控制室113,使得控制室113内的压力迅速升高,推动活塞17并带动针阀向下运动直至针阀关闭,喷油结束。
28.以上所述,仅为本实用新型较佳实施例而已,故不能以此限定本实用新型实施的范围,即依本实用新型申请专利范围及说明书内容所作的等效变化与修饰,皆应仍属本实用新型专利涵盖的范围内。