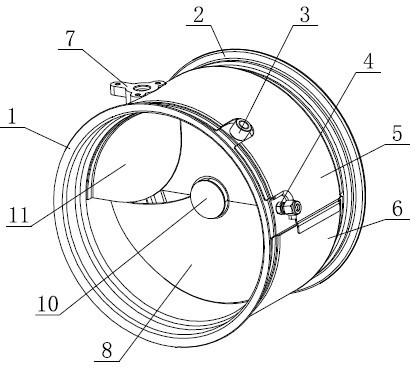
1.本实用新型涉及柴油发动机尾气后处理技术领域,尤其是一种柴油机尾气混合装置。
背景技术:2.目前,在柴油发动机尾气后处理系统中,通常采用选择性催化还原技术(scr)对发动机的尾气排放进行后处理;为了使尿素液滴能够在后处理系统中充分的与柴油机尾气混合均匀,需要在后处理系统中增加混合器,在混合器中喷入尿素水溶液,尿素水溶液经尾气加热被分解成氨气(nh3),在催化剂的作用下,氨气(nh3)把尾气中的氮氧化物(no
x
)还原成无害的氮气(n2)和水(h2o),最终从尾气管排出,从而达到降低排放物的目的。
3.现有的尾气后处理混合装置通常存在气体流速分布均匀性差、氨混合均匀性差的问题。气体流速分布均匀性差一方面会导致催化剂老化不均匀;另一方面,由于气体流速分布不均匀,在尾气后处理混合装置内部,处于气体流速较小区域的内壁面的温度较低,当尿素液滴接触到此部分内壁面后会带走一部分热量,使此部分的内壁面温度进一步降低,掉落在温度过低的内壁面上尿素液滴由于没有充分的吸热挥发,很容易形成尿素结晶,进而影响后处理系统性能,更甚者还会造成排放超标或后处理系统堵塞而造成车辆动力不足。氨混合均匀性差使氮氧化物的转化效率较差,并造成部分氨逃逸,从而影响催化剂的整体性能。
技术实现要素:4.本申请人针对上述现有尾气后处理混合装置存在气体流速分布均匀性差、容易形成尿素结晶,混合均匀性差的缺点,提供一种结构合理的柴油机尾气混合装置,气体流速分布均匀性高、结晶风险低,混合均匀性高。
5.本实用新型所采用的技术方案如下:
6.一种柴油机尾气混合装置,外壳内沿径向设置进气挡板、出气组件,进气挡板与出气组件之间沿轴向横置有中心管,外壳内部位于进气挡板、出气组件之间及中心管的外侧空腔为导流腔;进气挡板的外周轮廓尺寸与外壳内周轮廓尺寸相匹配,进气挡板的板面上凸起有第一凸起,形成第一开口、第二开口,第一凸起内侧形成混合腔;中心管的内部通道连通外壳的出气端部,中心管的圆周壁面上开设若干第二通孔,若干第二通孔及内部通道成为第一出气通道、导通导流腔与外壳的出气端部;出气组件的外周轮廓尺寸与外壳内周轮廓尺寸相匹配;出气组件上具有若干开孔部及第二凸起,第二凸起的外侧边缘朝外开出、形成第三开口;第二凸起位于开孔部的内侧,二者之间形成有出气腔,出气腔连通第三开口;开孔部上开设若干第一通孔,若干第一通孔成为第二出气通道、导通导流腔与出气腔;开孔部的外边缘与第二凸起的对应部位之间具有间隙、形成出气口,出气口作为第三出气通道、导通导流腔与出气腔。
7.本实用新型的尾气气流流经进气挡板时,对进气挡板的板面及第一凸起的第一弧
面进行了预热,使掉落在板面及第一弧面上尿素液滴充分吸热挥发,降低了尿素结晶的风险;尾气气流通过第一开口旋入混合腔内与尿素液滴相遇,气流在第一弧面的作用下加速旋流,旋入混合腔后形成环流,对喷射的尿素液滴起到有效的分散及预加热作用,同时也延长了气流对尿素液滴的加热路径,提高了尾气的热利用效率,使得尿素液滴充分吸热挥发,避免尿素液滴掉落到对应部件的内壁面上而形成尿素结晶,降低了尿素结晶的风险,保证了后处理系统的性能,避免造成排放超标或后处理系统堵塞,保证车辆动力要求。导流腔内的气流分别通过第一出气通道、第二出气通道、第三出气通道流出,进一步提高气流流速的均匀性,提高氨气的混合均匀性,使得尿素液滴充分吸热挥发,降低了尿素结晶的风险。
8.作为上述技术方案的进一步改进:
9.第一凸起为弧形凸起、具有第一弧面;第二凸起为弧形凸起、具有第二弧面。
10.出气组件上、靠近外侧边缘具有平面部分。
11.所述平面部分为环形平面,环形平面的面积为外壳横截面面积的25%~35%。
12.本实用新型的出气组件的平面部分使第三开口及第二弧面更靠近中心管,可以迫使靠近外壳内壁面的高速气流向第三开口流动,改善气流流出后的流速分布,使流出后的气流流速分布更均匀。
13.出气组件的中央具有套筒,套筒套设在中心管的出气端部外周。
14.出气组件由若干块出气挡板瓣合组成圆形;出气挡板的板面部一边外侧朝外延伸形成开孔部,板面部凸起有第二凸起,第二凸起位于与开孔部相对的另一侧部,板面部的内侧翻起有内凹弧形翻边,板面部上、靠近外侧边缘具有平面部;各出气挡板瓣合后,按顺时针顺序数起,前一块出气挡板的第二凸起位于相邻后一块出气挡板的开孔部的内侧,各出气挡板的翻边围成圆形套筒,各出气挡板的平面部组合形成一圈环形平面。
15.中心管的前端部穿过进气挡板;中心管采用一端封闭、一端开口的管件,或在中心管的前端面封盖盖板实现对前端部的封闭。
16.中心管的前端面固定在进气挡板的内侧壁面上,实现对中心管前端面的封闭。
17.外壳上、正对进气挡板的第一开口设置有喷嘴座,喷嘴座内设置尿素喷嘴;外壳的内壁面上、位于喷嘴座的进气一侧外侧设置有阻气板;阻气板位于第一开口的斜上方。
18.本实用新型的阻气板设置在喷嘴座位于进气一侧的外侧,避免尾气气流直吹尿素喷射线、而将尿素液滴吹落到进气挡板的壁面上而形成尿素结晶,同时,尾气气流在阻气板的引导下,与进气挡板一起作用,改变气流的方向和流速,全部汇入进气挡板的第一开口。
19.外壳的外周设置有半圆筒形的第一保温组件与第二保温组件,第一保温组件与第二保温组件瓣合成圆筒形、套设在外壳的筒体外周;外壳的出气端部设置有出气连接件,进气端部的壁面上设置压差传感器座、温度传感器座。
20.本实用新型的保温组件对外壳的壁面起保温作用,保证外壳的壁面始终保持在较高的温度,使落到壁面上的尿素液滴迅速挥发热解,避免壁面上存在低温区域,降低尿素结晶的风险,保证后处理系统的性能。
21.本实用新型的有益效果如下:
22.本实用新型的尾气气流流经进气挡板时,对进气挡板的板面及第一凸起的第一弧面进行了预热,使掉落在板面及第一弧面上尿素液滴充分吸热挥发,降低了尿素结晶的风险;尾气气流通过第一开口旋入混合腔内与尿素液滴相遇,气流在第一弧面的作用下加速
旋流,旋入混合腔后形成环流,对喷射的尿素液滴起到有效的分散及预加热作用,同时也延长了气流对尿素液滴的加热路径,提高了尾气的热利用效率,使得尿素液滴充分吸热挥发,避免尿素液滴掉落到对应部件的内壁面上而形成尿素结晶,降低了尿素结晶的风险,保证了后处理系统的性能,避免造成排放超标或后处理系统堵塞,保证车辆动力要求。导流腔内的气流分别通过第一出气通道、第二出气通道、第三出气通道流出,进一步提高气流流速的均匀性,提高氨气的混合均匀性,使得尿素液滴充分吸热挥发,降低了尿素结晶的风险。
23.本实用新型的出气组件的平面部分使第三开口及第二弧面更靠近中心管,可以迫使靠近外壳内壁面的高速气流向第三开口流动,改善气流流出后的流速分布,使流出后的气流流速分布更均匀。
24.本实用新型的阻气板设置在喷嘴座位于进气一侧的外侧,避免尾气气流直吹尿素喷射线、而将尿素液滴吹落到进气挡板的壁面上而形成尿素结晶,同时,尾气气流在阻气板的引导下,与进气挡板一起作用,改变气流的方向和流速,全部汇入进气挡板的第一开口。
25.本实用新型的保温组件对外壳的壁面起保温作用,保证外壳的壁面始终保持在较高的温度,使落到壁面上的尿素液滴迅速挥发热解,避免壁面上存在低温区域,降低尿素结晶的风险,保证后处理系统的性能。
附图说明
26.图1为本实用新型的立体图。
27.图2为图1的爆炸图。
28.图3为图1拆除外壳、保温部件及出气连接件后的结构示意图,图中箭头表示气流的走向。
29.图4为进气挡板的立体图。
30.图5为出气组件的立体图。
31.图6为出气挡板的立体图。
32.图中:1、外壳;2、出气连接件;3、压差传感器座;4、温度传感器座;5、第一保温组件;6、第二保温组件;7、喷嘴座;71、尿素喷射线;
33.8、进气挡板;81、板面;82、中心孔;83、第一凸起;84、第一弧面;85、第一开口;86、第二开口;87、混合腔;
34.9、出气组件;91、出气挡板;911、板面部;912、开孔部;913、第二凸起;914、第二弧面;915、翻边;916、第一通孔;917、平面部;92、出气口;93、第三开口;94、出气腔;
35.10、中心管;101、盖板;102、第二通孔;
36.11、阻气板;
37.20、导流腔。
具体实施方式
38.下面结合附图,说明本实用新型的具体实施方式。
39.如图1、图2、图3所示,本实用新型的圆筒形外壳1的出气端部设置有出气连接件2,进气端部的壁面上设置压差传感器座3、温度传感器座4及喷嘴座7,喷嘴座7内设置尿素喷嘴(图中未示出);外壳1的外周设置有第一保温组件5与第二保温组件6,第一保温组件5、第
二保温组件6为半圆筒形,二者瓣合成圆筒形、套设在外壳1的筒体外周,对外壳1的壁面起保温作用,保证外壳1的壁面始终保持在较高的温度,使落到壁面上的尿素液滴迅速挥发热解,避免壁面上存在低温区域,降低尿素结晶的风险,保证后处理系统的性能。外壳1的前端内壁面上沿径向竖直设置有圆形的进气挡板8,进气挡板8的外周轮廓尺寸与外壳1内周轮廓尺寸相匹配;进气挡板8的后方、沿径向竖直设置有出气组件9;进气挡板8与出气组件9之间沿轴向横置有中心管10,中心管10位于外壳1的中央,其前后端部分别穿过进气挡板8、出气组件9,外壳1内部位于进气挡板8、出气组件9之间及中心管10的外侧空腔为导流腔20。如图2、图3所示,中心管10穿出进气挡板8的端部封盖有盖板101,在中心管10内形成一端封闭、一端开口的内部通道,避免尾气不经混合直接从中心管10的内部通道流出,在其他实施例中,也可将中心管10加工成一端封闭、一端开口的管件;中心管10的圆周壁面上开设有若干贯通的第二通孔102,第二通孔102连通中心管10的内部通道,中心管10的若干第二通孔102及内部通道成为第一出气通道,导通导流腔20与外壳1的出气端部,导流腔20内的一部分通过第一出气通道流出。
40.如图4所示,进气挡板8的板面81中央开设中心孔82,如图3所示,中心管10的前端部从中心孔82穿出。板面81的下部、位于中心孔82的一侧、朝向进气方向向外侧凸起有弧形的第一凸起83,第一凸起83具有第一弧面84;第一凸起83直接从板面81上朝外凸起、其上边沿从板面81上开裂,在进气挡板8上形成轴向的第一开口85及径向的第二开口86,在第一凸起83内侧形成混合腔87;如图3所示,进气挡板8的第一开口85正对喷嘴座7,位于喷嘴座7的正下方,喷嘴座7内的尿素喷嘴喷射的尿素喷射线71正对第一开口85往混合腔87内喷入。尾气气流流经进气挡板8时,一部分气流撞击至板面81发生转向形成旋流、沿进气挡板8的边缘绕进第一开口85,另一部分气流撞击第一凸起83的第一弧面84、沿着第一弧面84导流至板面81、与另一部分气流混合旋进第一开口85,两部分在绕进第一开口85前,分别对进气挡板8的板面81及第一凸起83的第一弧面84进行了预热,使掉落在板面81及第一弧面84上尿素液滴充分吸热挥发,降低了尿素结晶的风险;尾气气流通过第一开口85旋入混合腔87内与尿素液滴相遇,气流在第一弧面84的作用下加速旋流,旋入混合腔87后形成环流,对喷射的尿素液滴起到有效的分散及预加热作用,同时也延长了气流对尿素液滴的加热路径,提高了尾气的热利用效率,使得尿素液滴充分吸热挥发,避免尿素液滴掉落到对应部件的内壁面上而形成尿素结晶,降低了尿素结晶的风险,保证了后处理系统的性能,避免造成排放超标或后处理系统堵塞,保证车辆动力要求。如图1、图2、图3所示,外壳1的前端内壁面上、位于进气挡板8的前方固定设置有阻气板11,阻气板11位于第一开口85的斜上方、遮挡在在喷嘴座7的尿素喷嘴的外侧,即阻气板11设置在喷嘴座7位于进气一侧的外侧,避免尾气气流直吹尿素喷射线71、而将尿素液滴吹落到进气挡板8的壁面上而形成尿素结晶,同时,尾气气流在阻气板11的引导下,与进气挡板8一起作用,改变气流的方向和流速,全部汇入进气挡板8的第一开口85。
41.如图5、图6所示,出气组件9为由若干块出气挡板91瓣合组成的圆形,本实施例中,四块出气挡板91瓣合组成圆形的出气组件9,组合后的出气组件9的外周轮廓尺寸与外壳1内周轮廓尺寸相匹配。如图6所示,出气挡板91包括板面部911及开孔部912,开孔部912从板面部911的一边外侧沿径向朝外延伸形成,开孔部912上开设若干第一通孔916;板面部911与开孔部912相对的另一侧部、朝向出气方向向外凸起有弧形的第二凸起913,第二凸起913
具有第二弧面914;板面部911的内侧翻起有内凹弧形翻边915,弧形的内表面轮廓尺寸与中心管10的外表面轮廓尺寸相匹配;板面部911上、靠近外侧边缘具有平面部917。如图3、图5所示,各出气挡板91瓣合成出气组件9后,各出气挡板91的第二凸起913的外侧边缘朝外开出、形成第三开口93;按顺时针顺序数起,前一块出气挡板91的第二凸起913位于相邻后一块出气挡板91的开孔部912的内侧,第二凸起913与开孔部912之间形成出气腔94,出气腔94连通第三开口93;开孔部912的若干第一通孔916成为第二出气通道、导通导流腔20与出气腔94;开孔部912的外边缘与第二凸起913的第二弧面914对应部位之间具有间隙、形成出气口92,出气口92作为第三出气通道、导通导流腔20与出气腔94;导流腔20内的一部分气流分别通过第二出气通道、第三出气通道流至若干出气腔94,从若干第三开口93流出;出气组件9的内外侧面形成凹凸起伏的波浪形状,导流腔20内旋流的气流在撞击到出气组件9的凹凸不平的内侧面上,进一步加速旋流,提高氨气的混合均匀性,使得尿素液滴充分吸热挥发,降低了尿素结晶的风险,各出气挡板91的第二弧面914对气流起导流作用,引导气流流向各开孔部912及出气口92。如图3、图5所示,各出气挡板91瓣合成出气组件9后,各出气挡板91的翻边915围成圆形套筒、套设在中心管10的出气端部外周,各出气挡板91的平面部917组合形成一圈环形平面,该环形平面的面积为外壳1横截面面积的25%~35%,该圆环平面使第三开口93及第二弧面914更靠近中心管10,可以迫使靠近外壳1内壁面的高速气流向第三开口93流动,改善气流流出后的流速分布,使流出后的气流流速分布更均匀。
42.实际使用时,如图3所示,喷嘴座7内的尿素喷嘴往混合腔87内喷射尿素喷射线71;尾气从第一开口85进入混合腔87与喷射尿素喷射线71混合,将尿素液滴雾化蒸发并进行热解、形成混合气流从第二开口86进入导流腔20,再分别通过第一出气通道、第二出气通道、第三出气通道排出。
43.本实用新型的气流旋转进入混合腔87,降低了尿素结晶的风险;导流腔20内的气流具有三个出气通道,导流腔20内旋转的气流,碰到出气组件9后,一部分气流沿着第二弧面914流至出气腔94、从第三开口93流出,一部分气流从出气挡板91的开孔部912的若干第一通孔916流出,剩余的少量气流在导流腔20内压力的作用下、从中心管10的若干第二通孔102及其内部通道流出;气流流速分布均匀性高,结晶风险低,尾气与氨气的混合更均匀。
44.以上描述是对本实用新型的解释,不是对本实用新型的限定,在不违背本实用新型精神的情况下,本实用新型可以作任何形式的修改。比如,在其他实施例中,进气挡板8上也可以不开设中心孔82,中心管10的前端部不穿过进气挡板8、其前端面直接焊接固定在进气挡板8的内侧壁面上,实现对其前端面的封闭。