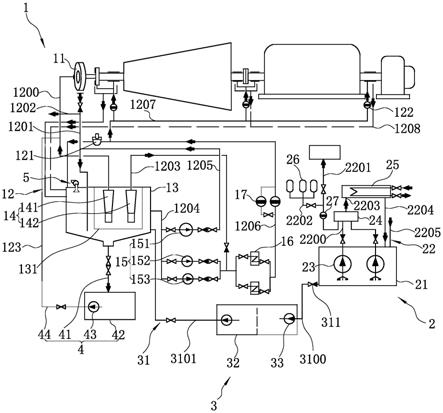
1.本发明涉及蒸汽轮机的技术领域,尤其是涉及一种蒸汽轮机轴承箱供油装置。
背景技术:2.目前,在发电过程中,尤其是火力发电的过程中,常用的是蒸汽轮机带动发电机发电,相关技术中,蒸汽轮机采用的是集中供油系统,集中供油系统主要由油箱、油泵、主油泵、抽油烟机、冷油器、双筒滤油器、仪表、阀门和供油管道组成,蒸汽轮机的轴承箱的润滑油和控制油均由不同的油泵从油箱中输送至轴承箱中。润滑油和控制油采用集中供油的方式,容易出现油压相互影响大和油质变差的情况,从而影响蒸汽轮机运行的可靠性和稳定性。
3.因此,亟需一种蒸汽轮机轴承箱供油装置,以改善上述问题。
技术实现要素:4.为了改善油质和减少润滑油、控制油之间的油压的相互影响,进而提高蒸汽轮机运行的可靠性和稳定性,本技术提供了一种蒸汽轮机轴承箱供油装置。
5.本技术提供的一种蒸汽轮机轴承箱供油装置采用如下的技术方案:一种蒸汽轮机轴承箱供油装置,包括:润滑供油机构,其包括安装在蒸汽轮机轴承上的主油泵、一端与主油泵连通的润滑输油管道、与润滑输油管道连通的主油箱、安装在主油箱内并与润滑输油管道连通的注油器、与注油器通过润滑输油管道连通的油泵组、与油泵组通过输油管道连通的第一冷油器和与第一冷油器通过润滑输油管道连通的第一滤油器组,所述第一滤油器组通过润滑输油管道与蒸汽轮机轴承上的主油泵连通;控制供油机构,其包括副油箱、一端与蒸汽轮机轴承箱的电流驱动器连通的控制输油管道、安装在副油箱内并与控制输油管道连通的控制油泵组、安装在控制输油管道上的溢流阀、与溢流阀通过控制输油管道连通的第二冷油器、与溢流阀通过控制输油管道连通的储能器和安装在控制输油管道上位于溢流阀至储能器之间的第二滤油器;过渡输油机构,其包括一端与副油箱连通的过渡输油管道、与过渡输油管道连通的过渡油箱和设在过渡油箱内的过渡油泵组,所述过渡油泵组通过过渡输油管道与主油箱连通;事故输油机构,与主油箱连通并用于为蒸汽轮机轴承继续供油不使润滑油迅速中断;以及排气机构,安装在主油箱上并用于抽出主油箱中的气体、油烟和水蒸汽。
6.通过采用上述技术方案,将蒸汽轮机轴承箱所需的润滑油和控制油分开,过渡输油机构能将控制供油机构中用过的控制油输送至润滑供油机构中作为润滑油使用,减少浪费,润滑供油机构提供润滑油,控制供油机构提供控制油,且主油箱的油不能流动到副油箱中,起到改善油质和减少润滑油、控制油之间的油压的相互影响的作用,进而提高蒸汽轮机
运行的可靠性和稳定性。
7.可选的,所述主油箱内的设有用于将注油器包围在内的过滤网框。
8.通过采用上述技术方案,过滤网框能将主油箱内的润滑油过滤后再经由注油器向润滑输油管道进行输油,使输送到主油泵的润滑油中的杂质更少。
9.可选的,所述润滑输油管道上位于第一滤油器组和主油箱之间的位置设有过压阀。
10.通过采用上述技术方案,当润滑油压力过高时,多余的流量能通过过压阀流回主油箱中,保护整个供油装置中各机构不因压力过高而损坏。
11.可选的,所述润滑输油管道上靠近蒸汽轮机轴承箱的进油端的位置均设有第二滤油器。
12.通过采用上述技术方案,第二滤油器能进一步将即将进入蒸汽轮机轴承箱中的润滑油进行过滤,减少润滑油中的杂质,进而使润滑油的油质更好。
13.可选的,所述油泵组包括一端通过润滑输油管道与注油器连通的高压油泵、与高压油泵的另一端通过润滑输油管道连通的交流润滑油泵和安装在润滑输油管道上并与交流润滑油泵并联的直流润滑油泵;所述交流润滑油泵、直流润滑油泵均通过润滑输油管道与注油器连通。
14.通过采用上述技术方案,高压油泵主要用于给整个蒸汽轮机系统提供润滑油和保安油,当蒸汽轮机盘车时需要使用交流润滑油泵,当蒸汽轮机因故障使润滑油油压低于极限值而交流润滑油泵无法投入工作时,直流润滑油泵用于为蒸汽轮机提供润滑油压,使蒸汽轮机能够安全的停下来,避免发生断油磨瓦事故。
15.可选的,所述第一冷油器的数量为两个且相互并联。
16.通过采用上述技术方案,第一冷油器能处于一备一用的状态,避免因维修影响蒸汽轮机的正常运转。
17.可选的,所述储能器的数量为多个并且相互并联。
18.通过采用上述技术方案,储能器的数量为多个,增加储能性能,进而使储整个润滑供油机构的卸压性能更好。
19.可选的,所述过渡油箱与副油箱之间的过渡输油管道上设有止逆阀。
20.通过采用上述技术方案,止逆阀的设置能防止过渡油箱中的回流至副油箱内,从而避免副油箱中排出的废油回流,为后期的排废和副油箱的换油操作增加工作量。
21.可选的,所述过渡输油机构还包括与过渡油箱连通的排油管道、与排油管道连通的沉淀箱、一端与沉淀箱连通的卸油管道和安装在排油管道上的排油泵;所述排油管道的另一端与主油箱连通。
22.通过采用上述技术方案,沉淀箱能将过渡油箱和主油箱中的排出的油进行沉淀除杂后,再由排油泵将油从排油管道输送回主油箱中,使润滑油的使用寿命更长且油质更好。
23.可选的,所述沉淀箱内设有过滤板,所述过滤板将沉淀箱内的区域分为沉淀区和储油区。
24.通过采用上述技术方案,过滤板能将从沉淀区经沉淀作用后的油过滤再流动到储油区中,然后从储油区被泵送至主油箱中。
25.综上所述,本技术包括以下至少一种有益技术效果:
1.蒸汽轮机轴承箱所需的润滑油和控制油被分开提供,过渡输油机构能将控制供油机构中用过的控制油输送至润滑供油机构中作为润滑油使用,减少浪费,润滑供油机构提供润滑油,控制供油机构提供控制油,且主油箱的油不能流动到副油箱中,起到改善油质和减少润滑油、控制油之间的油压的相互影响的作用,进而提高蒸汽轮机运行的可靠性和稳定性;2.过滤网框能将主油箱内的润滑油过滤后再经由注油器向润滑输油管道进行输油,使输送到主油泵的润滑油中的杂质更少;3.沉淀箱能将过渡油箱和主油箱中的排出的油进行沉淀除杂后,再由排油泵将油从排油管道输送回主油箱中,使润滑油的使用寿命更长且油质更好。
附图说明
26.图1是本技术实施例公开的一种蒸汽轮机轴承箱供油装置的整体供油示意图。
27.图2是本技术实施例公开的另一种蒸汽轮机轴承箱供油装置的整体供油示意图。
28.图3是本技术实施例中排气机构的结构示意图。
29.附图标记说明:1、润滑供油机构;11、主油泵;12、润滑输油管道;1200、第一润滑油管;1201、第二润滑油管;1202、第三润滑油管;1203、第四润滑油管;1204、第五润滑油管;1205、第六润滑油管;1206、第七润滑油管;1207、第八润滑油管;1208、第九润滑油管;121、过压阀;122、第二滤油器; 13、主油箱;131、过滤网框;14、注油器;141、低压注油器;142、高压注油器;15、油泵组;151、高压油泵;152、交流润滑油泵;153、直流润滑油泵;16、第一冷油器;17、第一滤油器组;2、控制供油机构;21、副油箱;22、控制输油管道;2200、第一控制油管;2201、第二控制油管;2202、第三控制油管;2203、第四控制油管;2204、第五控制油管;2205、第六控制油管;23、控制油泵组;24、溢流阀;25、第二冷油器;26、储能器;27、第二滤油器;3、过渡输油机构;31、过渡输油管道;3100、第一过渡油管;3101、第二过渡油管;311、止逆阀;32、过渡油箱;33、过渡油泵组;34、排油管道;3400、第一排油管;3401、第二排油管;35、沉淀箱;350、沉淀区;351、储油区;36、卸油管道;37、排油泵;38、过滤板;4、事故输油机构;41、事故输油管;42、事故油箱;43、事故输油泵;44、事故排油管;5、排气机构;51、排气管道;52、排气风机。
具体实施方式
30.以下结合附图1-3对本技术作进一步详细说明。
31.本技术实施例公开一种蒸汽轮机轴承箱供油装置,参照图1,该蒸汽轮机轴承箱供油装置包括与蒸汽轮机轴承箱连通并用于给蒸汽轮机轴承箱提供润滑油的供油的润滑供油机构1、与蒸汽轮机轴承箱的电流驱动器连通并用于提供控制油的控制供油机构2、用于将控制供油机构2中的待换油进行收集并输送至润滑供油机构1的过渡输油机构3、与润滑供油机构1连通并用于为蒸汽轮机轴承箱继续供油不使润滑油迅速中断的事故输油机构4和安装在润滑供油机构1上并用于抽出润滑供油机构1中的气体、油烟和水蒸汽的排气机构5。另外,润滑供油机构1、控制供油机构2、过渡输油机构3、事故输油机构4和排气机构5中的
所用的泵和阀门均由蒸汽轮机机组的控制柜电性连接,便于操作人员控制。
32.具体的,润滑供油机构1包括主油泵11、润滑输油管道12、主油箱13、注油器14、油泵组15、第一冷油器16和第一滤油器组17。其中,主油泵11可采用离心泵,主油泵11套设在蒸汽轮机的前轴承上并由蒸汽轮机主轴带动,蒸汽轮机的主轴高速转动时驱动主油泵11运转,把润滑油由前轴承箱的内部向外围扩散,然后产生高压油。一般情况下,主油泵11的出口油压为1.27兆帕。
33.参照图1,润滑输油管道12可采用不锈钢管制成,并作为整个润滑供油机构1中的润滑油供油管道,为了便于理解本技术实施例中的润滑输油管道12的布设路径,将润滑输油管道12的各段从第一润滑油管1200一直编号至第九润滑油管1208,并且第一润滑油管1200至第九润滑油管1208可根据具体供油情况设置阀门。
34.具体的,第一润滑油管1200的一端与主油泵11的进油端法兰连接,第一润滑油管1200的另一端则与注油器14的排油端螺纹连接,用于将主油箱13内的油注入到主油泵11中。第二润滑油管1201的一端与主油泵11的排油端法兰连接,第二润滑油管1201的另一端则与主油箱13内连通用于回油。而第二润滑油管1201在主油箱13和主油泵11之间的位置还通过转接头连接有第三润滑油管1202,第三润滑油管1202的排油端与蒸汽轮机组的保安系统或油动机连通,用于快速切断安全油,以保护蒸汽轮机。第四润滑油管1203与注油器14的排油端的一端连通,第四润滑油管1203的另一端通过三通转接头分别与油泵组15的进油端和第一冷油器16的进油端连通。润滑油在油泵组15的作用下,再通过第五润滑油管1204将油泵组15中的油输送回主油箱13中。
35.第六润滑油管1205的一端与油泵组15的排油端连通,第六润滑油管1205的另一端则与第二润滑油管1201连通。第七润滑油管1206的一端与第一冷油器16的排油端连通,第七润滑油管1206的另一端与第一滤油器组17的进油端连通。第八润滑油管1207的一端与第一滤油器组17的排油端连通,第八润滑油管1207的另一端则分别通过支管与蒸汽轮机轴承箱的各轴承进油端连通。第九润滑油管1208的一端与各轴承的排油端连通,第九润滑油管1208的另一端与主油箱13螺纹连接,最后回油经过第九润滑油管1208回至主油箱13中。
36.在本技术可能的实施方式中,润滑输油管道12上位于第一滤油器组17和主油箱之间的位置还安装有过压阀121,即在第八润滑油管1207上安装过压阀121即可。当润滑油压力过高时,多余的流量能通过过压阀121流回主油箱13中,保护整个供油装置中各机构不因压力过高而损坏。
37.进一步的,为使即将被输送至蒸汽轮机轴承箱的各轴承处的润滑油更纯净,减少润滑油中的杂质,在润滑输油管道12上靠近蒸汽轮机轴承箱的进油端的位置上均安装有第二滤油器122,用于过滤润滑油中的杂质。
38.主油箱13可采用铝合金材料制成,主油箱13的底部呈锥形缩口结构,便于沉淀润滑油中的滤渣。主油箱13上通过螺纹连接的方式与润滑输油管道12连通,用于储存润滑油。
39.在本技术一些可能的实施方式中,为减少杂质从主油箱13进入注油器14内,在主油箱13内的顶板上可采用螺栓连接的方式固定安装有过滤网框131,过滤网框131可以是顶端开口的矩形金属过滤网框体,过滤网框131结合主油箱13的顶板将注油器14包围在内,这样能减少杂质进入注油器14中。
40.注油器14的数量为两个,分别是低压注油器141和高压注油器142,其中,低压注油
器141的排油端与第一润滑油管1200连通,且低压注油器141的排油端压力一般为0.1兆帕并用于给主油泵11供油,高压注油器142的排油端与第四润滑油管1203连通,且高压注油器142的排油端压力一般为0.22兆帕并用于,在高压注油器142的作用下,润滑油依次经过第一冷油器16和第一滤油器组17后供油给各轴承润滑冷却用。
41.油泵组15油泵组15包括一端通过润滑输油管道12与注油器14连通的高压油泵151、与高压油泵151的另一端通过润滑输油管道12连通的交流润滑油泵152和安装在润滑输油管道12上并与交流润滑油泵152并联的直流润滑油泵153。具体的,高压油泵151的两端分别与第五润滑油管1204和第六润滑油管1205连通,高压油泵151可采用高压交流油泵,且高压油泵151主要用于给整个蒸汽轮机系统提供润滑油和保安油,当蒸汽轮机正常运行时,润滑油和保安油均由主油泵11提供,高压油泵151作为紧急备用泵,当蒸汽轮机转速正常时带动主油泵11开始工作时,需要将高压油泵151停用,避免主油泵11的排油端的压力高于高压油泵151的排油端的压力,进而使高压油泵151损坏。交流润滑油泵152可以是低压交流泵,交流润滑油泵152的两端分别可采用法兰连接的方式与第四润滑油管1203和第五润滑油管1204连通。直流润滑油泵153的两端也可采用法兰连接的方式与第四润滑油管1203和第五润滑油管1204连通,即直流润滑油泵153与交流润滑油泵152并联。
42.当蒸汽轮机盘车时使用交流润滑油泵152,同时,交流润滑油泵152还可以作为紧急备用泵。当蒸汽轮机因故障使润滑油油压低于极限值而交流润滑油泵152无法投入工作时,直流润滑油泵153用于为蒸汽轮机提供润滑油压,使蒸汽轮机能够安全的停下来,避免发生断油磨瓦事故。
43.第一冷油器16可采用水冷式冷油器,第一冷油器16的两端分别与第四润滑油管1203和第七润滑油管1206连通。在本技术可能的实施方式中,第一冷油器16的数量为两个,并且呈相互并联的关系,作为一备一用。润滑油经过第一冷油器16后一般能将排油温度控制在40摄氏度左右,能将在润滑油循环使用过程中持续不断的将轴承箱转动摩擦部分的发热量带走。
44.第一滤油器组17由两个滤油器并联组成,一备一用,当滤油器压差高时可立即切换油滤,第一滤油器组17与可采用法兰连接的方式安装在第七润滑油管1206上。第一滤油器组17的作用是在线过滤润滑油中的杂质,提高用油的安全性。
45.润滑油在润滑供油机构1中的流动如下,主油箱13内的低压注油器141给主油泵11提供润滑油,然后主油泵11产生高压油并输送至蒸汽轮机并作为主汽门高压用油和机械超速用油。然后润滑油从第三润滑油管1202流回主油箱13中,润滑油中的一些杂质沉淀在主油箱13的底部,还有一些杂质经过过滤网框131的过滤,被过滤后的润滑油再由高压注油器142输送至第四润滑油管1203后再依次第一冷油器16和第七润滑油管1206上的第一滤油器组17后从第八润滑油管1207输送至汽轮机和发电机,作为轴承的润滑用油。当蒸汽轮机刚启动时,由于转速较低,需要高压油泵151将润滑油从第六润滑油管1205输送至主油泵11。当蒸汽轮机盘车时,由交流润滑油泵152作为紧急备用。当整个蒸汽轮机故障时,因为润滑油油压较低而交流润滑油泵152并未联动启动,此时启动直流润滑油泵153,为蒸汽轮机提高润滑油压,使蒸汽轮机能够安全的停机。
46.参照图1,控制供油机构2包括副油箱21、一端与蒸汽轮机轴承箱的控制端连通的控制输油管道22、安装在副油箱21内并与控制输油管道22连通的控制油泵组23、安装在控
制输油管道22上的溢流阀24、与溢流阀24通过控制输油管道22连通的第二冷油器25、与溢流阀24通过控制输油管道22连通的储能器26和安装在控制输油管道22上位于溢流阀24至储能器26之间的第二滤油器27。
47.具体的,副油箱21可采用铝合金冲压成型的矩形箱体,用于储存控制用油,控制输油管道22同样由多段控制油管组成,为了方便理解控制用油的流动路径,将控制输油管道22按第一控制油管2200依次编号至第六控制油管2205。其中,第一控制油管2200的数量为两根,两根第一控制油管2200的进油端与置于副油箱21中对应的控制油泵组23的排油端连通,第一控制油管2200的另一端则与溢流阀24的进油端连通。第二控制油管2201的一端与溢流阀24的排油端连通,用于将溢流阀24排出的油输送至蒸汽轮机轴承箱的控制端的进油端。
48.第三控制油管2202的一端与第二控制油管2201连通,第三控制油管2202的另一端与储能器26连通,在第三控制油管2202上安装有阀门。第四控制油管2203的两端分别与溢流阀24和第二冷油器25连通。第五控制油管2204的两端分别与第二冷油器25的排油端和副油箱21的进油端连通,用于将冷却后的油输送至副油箱21中。第六控制油管2205的两端分别与蒸汽轮机控制端和副油箱21的进油端连通,用于控制油的回油。
49.控制油泵组23由两个eh油泵组成,两个eh油泵安装在副油箱21内,且供油端与用于给第一控制油管2200供油,两个eh油泵一备一用,避免控制油泵组23维护时影响蒸汽轮机的正常运转。
50.溢流阀24用于给整个控制供油机构2进行卸荷,当系统压力增大时,会使控制油的流量减小,此时溢流阀24开启,使多余的控制油溢回副油箱21内,保证溢流阀24的进口压力。
51.第二冷油器25可采用水冷式冷油器,第二冷油器25中安装的冷却水管上螺纹连接有控制阀,控制油从第四控制油管2203进入第二冷油器25中,热量被冷却水管中流动的水带走,冷却后的控制油再从第五控制油管2204流回副油箱21中。
52.储能器26作为辅助压力油源,用于吸收和储存控制供油机构2中的,从而减小管路中的油压波动,减少设备运行切换对控制供油机构2的冲击,进而避免蒸汽轮机机组跳闸等事故的发生。在本技术实施例中,储能器26的数量设置为三个,三个储能器26的进油端分别与安装在第三控制油管2202上的四通转接头的排油端。第二滤油器27可采用螺纹连接的方式安装在第二控制油管2201上了,用于过滤掉即将被输送至蒸汽轮机控制端的控制油。
53.参照图,控制油在控制供油机构2中的主要的两种流通路径如下:首先,在控制油泵组23的泵送作用下从第一控制油管2200进入溢流阀24中,然后再经过第二滤油器27的过滤后从第二控制油管2201进入汽轮机轴承机的控制端,最后从第六控制油管2205流回副油箱21中。而副油箱21内的一部分油在从溢流阀24分流,分流后的控制油从溢流阀24排出经过第四控制油管2203进入第二冷油器25中,经过第二冷油器25的冷却作用后,从第五控制油管2204回流至副油箱21中。
54.参照图1,过渡输油机构3能用于将控制供油机构2中用过的控制油输送至润滑供油机构1中,避免浪费控制油。过渡输油机构3包括一端与副油箱21连通的过渡输油管道31、与过渡输油管道31连通的过渡油箱32和设在过渡油箱32内的过渡油泵组33。
55.具体的,过渡输油管道31由第一过渡油管3100和第二过渡油管3101组成,其中,第
一过渡油管3100的两端分别与副油箱21和过渡油箱32连通,第二过渡油管3101的两端分别与过渡油箱32和主油箱13连通。过渡油箱32可采用铝合金制成的矩形箱体,用于临时储存从副油箱21排出的控制油。过渡油泵组33由两个安装在过渡油箱32内的过渡油泵组成,其中一个过渡油泵的进油端与第一过渡油管3100的排油端连通,用于抽取副油箱21中的控制油。另一个过渡油泵的排油端与第二过渡油管3101的进油端连通,用于将过渡油箱32内的控制油泵送至主油箱13中。
56.参照图1和图2,在本技术可能的实施方式中,过渡油箱32与副油箱21之间的过渡输油管道31上设置有止逆阀,即第一过渡油管3100上可采用螺纹连接的方式安装有止逆阀,这样能避免过渡油箱32中的回流至副油箱21内。
57.进一步的,为使主油箱13内的润滑油油质更好,杂质更少,在本身其他可能的实施方式中,过渡输油机构3还包括与过渡油箱32连通的排油管道34、与排油管道34连通的沉淀箱35、一端与沉淀箱35连通的卸油管道36和安装在排油管道34上的排油泵37。
58.具体的,排油管道34油第一排油管3400和第二排油管3401组成,第一排油管3400为两段并联的管道,第一排油管3400的两端分别与过渡油箱32和沉淀箱35连通,用于将过渡油箱32中收集的油输送至沉淀箱35内。第二排油管3401的两端分别与沉淀箱35和主油箱13连通,用于将经过沉淀过滤后的油输送至主油箱13中作为润滑油。沉淀箱35可采用铝合金制成的矩形箱体,用于油的静止沉淀。卸油管道36用于将沉淀箱35内的劣质油或费油排出,当然,卸油管道36上应安装阀门。排油泵37的安装在排油管道34的第二排油管3401上。
59.进一步的,为使沉淀箱35除去油中的杂质的效果更好,在沉淀箱35内还插设有过滤板38,过滤板38将沉淀箱35内的区域分为沉淀区350和储油区351,沉淀区350用于静止沉淀除杂,储油区351用于给排油泵37供油,过滤板38可采用无纺布和过滤网制成的板体,可采用螺栓连接的方式或焊接的方式安装在沉淀箱35内,用于过滤油中的杂质。
60.参照图1,事故输油机构4可以由事故输油管41、事故油箱42、事故输油泵43和事故排油管44组成,其中,事故输油管41上安装有多个阀门,事故输油管41的两端分别与事故油箱42和主油箱13连通,事故油箱42可采用铝合金制成的矩形箱体,用于临时储存润滑油,事故输油泵43安装在事故油箱42内,事故排油管44的两端分别与事故输油泵43和第一润滑油管1200连通。当主油泵11停止运行时,而蒸汽轮机还处于运转的事故状态下,事故输油机构4能将润滑油输送至主油泵11中,不致使润滑油的供油迅速中断,同时还能给操作人员充足的时间反应,避免发生蒸汽轮机损坏的事故。
61.参照图2和图3,排气机构5安装在主油箱13上并用于抽出主油箱13中的气体、油、烟和水蒸汽。排气机构5包括排气管道51和排气风机52,其中排气管道51的一端穿设在主油箱13的顶板上,为使排气效果更好,在排气管道51的进气口呈上窄下宽的喇叭状。排气管道51的排气端与排气风机52法兰连接,排气风机52可采用离心风机。
62.以上均为本技术的较佳实施例,并非依此限制本技术的保护范围,故:凡依本技术的结构、形状、原理所做的等效变化,均应涵盖于本技术的保护范围之内。