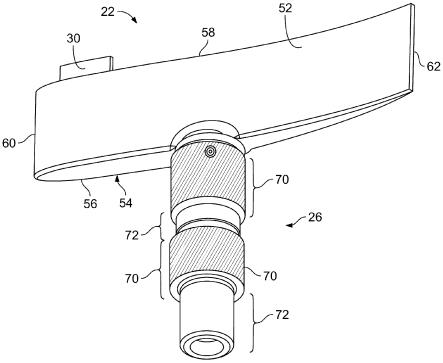
1.本公开总体上涉及涡轮增压器部件和用于制造涡轮增压器部件的方法。更特别地,本公开涉及双金属可变几何形状涡轮增压器叶片以及使用激光熔覆技术制造双金属涡轮增压器叶片的方法。
背景技术:2.用于汽油和柴油内燃机的涡轮增压器是本领域已知的装置,其用于通过使用离开发动机的排气的热量和体积流量来对被引导到发动机的燃烧室的进气流进行加压或增压。具体地,离开发动机的排气以使排气驱动的涡轮机在壳体内旋转的方式被引导到涡轮增压器的涡轮机壳体中。排气驱动的涡轮机安装到轴的一端上,该轴对径向空气压缩机是共用的,该径向空气压缩机安装在轴的相对端上并容纳在压缩机壳体中。因此,涡轮机的旋转动作还导致空气压缩机在涡轮增压器的与涡轮机壳体分开的压缩机壳体内旋转。空气压缩机的旋转动作使得进气进入压缩机壳体,并且在进气与燃料混合并在发动机燃烧室内燃烧之前被加压或增压期望的量。
3.在涡轮增压器中,通常期望控制流向涡轮机的排气的流量,以提高涡轮增压器的效率或操作范围。可变几何形状的涡轮增压器(vgt)已经被构造成满足这种需要。一种类型的这种vgt是具有可变排气喷嘴的vgt,称为可变喷嘴涡轮增压器(vnt)。已经采用了不同构造的可变喷嘴来控制排气流。在这种vgt中实现排气流控制所采用的一种方法涉及使用多个枢转叶片,这些叶片围绕涡轮机入口环形地定位。枢转叶片通常被控制以改变叶片之间的通道的喉部面积,从而起到控制进入涡轮机的排气流的作用。
4.枢转叶片可以被认为具有“功能”部分和“结构部分”。如本文所使用的,功能部分是指用于引起叶片的枢转动作的那些部分,并且通常包括叶片的柱形轴的一些或全部,该柱形轴不延伸到气流路径中,但是当轴在其壳体内旋转时由于摩擦效应而经受高温磨损。此外,如本文所使用的,结构部分是指直接在气流路径内且引导空气流的那些部分,且通常包括通常称为旗部(flag)的翼型形状的构件。在本文使用术语“功能”和“结构”不旨在在任何意义上限制任何叶片的操作特性;相反,它们仅在本文使用以便于描述和参考示例性叶片的某些部件/部分。
5.许多vgt涡轮增压器叶片使用不锈钢合金(说明性示例是hk 30不锈钢)或镍-铬超合金(说明性示例是inconel镍-铬超合金族)制成。这种不锈钢是完全奥氏体的,并且主要与铬和镍合金化,并且适合于高达约1020℃的温度,这种镍-铬超合金主要由大部分镍组成,与铬和铁合金化,并且适合于高达约1050℃的温度。由于它们围绕涡轮机入口的定位,枢转叶片经受非常热的排气,通常超过980℃和更高。然而,这些高温应用对高强度、耐腐蚀不锈钢材料(诸如上述hk 30示例)或镍-铬超合金材料(诸如上述inconel示例)造成潜在的磨损风险,尤其是在功能部分上。其他特种合金在本领域中是已知的,但这些材料通常比上述不锈钢合金或镍-铬超合金材料更昂贵,并且如果整个叶片(功能部分和结构部分两者)
由这些材料制造,则将造成显著的成本(以及制造)挑战。
6.因此,将期望提供用于涡轮增压器应用的可变喷嘴涡轮机叶片,其在高温操作期间能够在其功能部分处抵抗磨损。此外,将期望提供这种用于涡轮增压器应用的可变喷嘴涡轮机叶片,由于整个叶片使用特殊材料,因此该叶片不是非常昂贵。此外,结合附图和本发明主题的背景技术,从本发明主题的随后具体实施方式和所附权利要求中,本发明主题的其他期望特征和特性将变得显而易见。
技术实现要素:7.本文公开了双金属可变几何形状涡轮增压器叶片和使用激光熔覆技术制造双金属涡轮增压器叶片的方法。
8.在示例性实施例中,公开了一种双金属可变几何形状涡轮增压器(vgt)叶片,其包括结构性的翼型形状的旗部部分和连接到旗部部分的功能性的柱形轴部分。旗部部分和轴部分由第一金属合金形成,并且轴部分还包括由不同于第一金属合金的第二金属合金形成的表面区域。
9.在另一示例性实施例中,公开了一种用于制造双金属可变几何形状涡轮增压器(vgt)叶片的方法,包括提供或获得未处理的vgt叶片的步骤。未处理的vgt叶片包括结构性的翼型形状的旗部部分和连接到旗部部分的功能性的柱形轴部分。旗部部分和轴部分由第一金属合金形成。该方法还包括使用不同于第一金属合金的第二金属合金使轴部分经受激光熔覆工艺,从而在轴部分上形成第二金属的表面区域的步骤。
10.提供本发明内容以便以简化的形式介绍以下在具体实施方式中进一步描述的构思的选择。本发明内容不旨在标识所要求保护的主题的关键特征或必要特征,也不旨在用于帮助确定所要求保护的主题的范围。
附图说明
11.本发明的主题将在下文中结合以下附图进行描述,其中相同的附图标记表示相同的元件,并且其中:图1是根据本公开的一些实施例的采用可移动叶片的可变几何形状涡轮增压器的涡轮机壳体的分解等距视图;图2是根据本公开的一些实施例的图1的涡轮增压器的同步环(unison ring)的俯视图,示出了处于不同叶片操作位置的叶片;图3是根据本公开的一些实施例的图2中所示的叶片的详细视图;图4示出了适于根据本公开的一些实施例使用的激光熔覆装置;以及图5是示出根据本公开的一些实施例的用于制造vgt叶片的方法的流程图。
具体实施方式
12.以下具体实施方式本质上仅是示例性的,而不旨在限制本发明或本发明的应用和使用。如本文所使用的,词语“示例性”意味着“用作示例、实例或说明”。因此,本文中描述为“示例性”的任何实施例不必被解释为比其他实施例优选或有利。本文所描述的所有实施例是示例性实施例,提供这些示例性实施例是为了使本领域技术人员能够制造或使用本发
明,而不是限制由权利要求限定的本发明的范围。此外,不旨在受前述技术领域、背景技术、发明内容或以下具体实施方式中所呈现的任何明示或暗示理论的约束。
13.除非具体说明或从上下文显而易见,如本文所使用的,术语“约”应理解为在本领域的正常公差范围内,例如在平均值的2个标准偏差内。“约”可以理解为在所述值的10%、5%、1%、0.5%、0.1%、0.05%或0.01%内。“约”可以替代地理解为暗示所述的精确值。除非上下文另有清楚说明,本文提供的所有数值均用术语“约”修饰。
14.本公开总体上涉及双金属可变几何形状涡轮增压器叶片以及使用激光熔覆技术制造双金属涡轮增压器叶片的方法。在本文特别描述的是使用激光熔覆工艺来对叶片的功能部分,即叶片轴的表面区域进行局部处理。这可以通过应用合适的旋转高速、全自动激光熔覆工艺来实现,该熔覆工艺具有比用于形成叶片的典型合金更耐磨的包覆材料。包覆材料表现出与典型的(较不昂贵)基底叶片合金(诸如上述不锈钢合金或镍基超合金等)的足够的粘附性,叶片的其余部分由所述基底叶片合金制成。为了实现叶片轴的限定功能区域的高质量、无孔和无裂纹处理,包覆材料层的最小所需厚度可以是在轴的限定区域的表面上沉积时从大约20μm到大约500μm,例如沉积时诸如从大约20μm到大约200μm。作为优于现有技术的益处,这种经由激光熔覆的表面处理保护关键的叶片轴区域免受摩擦磨损,并且不改变叶片几何形状。因此,本公开提供了一种限于叶片轴的关键表面区域的处理,以提高高温下的耐磨性并避免叶片轴的这些受应力区域上的缺陷,与使用用于整个叶片的特殊材料相比,成本降低。
15.图1示出了包括涡轮机壳体12的vgt10的一部分,该涡轮机壳体具有用于接收排气流的标准入口14和用于将排气引导到发动机的排气系统的出口16。蜗壳连接到排气入口,并且一体的外喷嘴壁邻近蜗壳结合在涡轮机壳体铸件中。涡轮机叶轮17和轴组件18被承载在涡轮机壳体12内。供应涡轮增压器的排气或其他高能气体通过入口14进入涡轮机壳体12,并通过涡轮机壳体12中的蜗壳分配,以通过周向喷嘴入口20基本上径向地输送到涡轮机叶轮。
16.多个叶片22被安装到喷嘴壁24,该喷嘴壁是使用从这些叶片垂直地向外突出的轴26而被加工到涡轮机壳体12中的。用于这种vgt中的叶片22通常是细长的并且处于翼型件构造中。轴26旋转地接合在喷嘴壁中的相应开口28内。叶片22各自包括致动凸出部30,所述致动凸出部从与轴相对的一侧突出,并且由同步环34中的相应槽32接合,该同步环用作第二喷嘴壁。
17.致动器组件(未示出)与同步环34连接,并且构造成根据需要使该环在一个方向或另一个方向上旋转,以使叶片径向向外或向内移动,从而分别增加或减少流向涡轮机的排气流的量。当同步环旋转时,使得叶片凸出部30在它们相应的槽32内从一个槽端移动到相对的槽端。由于槽沿着同步环径向定向,叶片凸出部30在相应槽32内的移动使得叶片经由叶片轴在它们相应开口内的旋转而枢转并根据同步环旋转方向径向向外或向内移动。
18.图2示出了当由同步环致动时,如上文在图1中描述和示出的vgt 10中使用的叶片22的一般移动模式。每个叶片凸出部30设置在同步环34的相应槽32内。在闭合位置“a”中,叶片凸出部30邻近槽32的第一端44定位。该位置被称为闭合位置,因为叶片没有径向向外张开,从而用于限制到涡轮机的排气流。在中间位置“b”处,同步环34已经旋转了足够的量,使得叶片凸出部30在槽32内远离第一槽端44朝向槽的中间位置移动。
19.叶片凸出部30的移动由叶片相对于喷嘴壁的枢转动作提供,从而允许叶片22径向向外旋转给定的程度。在位置“b”处,与闭合位置“a”相比,叶片22的中间径向突出部用于增加流向涡轮机的排气流。在位置“c”处,同步环34现在已经旋转到最大位置,导致叶片凸出部30在槽32内移动到第二端46。同样,通过叶片22和喷嘴壁24之间的枢转布置,允许叶片22径向向外旋转到最大位置,有助于这种进一步的叶片移动。在位置“c”处,当与中间位置“a”相比,叶片22的最大径向突出部用于增加流向涡轮机的排气流。
20.图3是示例性叶片22的放大图,该叶片包括内径向表面52、相对的外径向表面54以及轴向表面56和58。这些叶片表面相对于叶片在涡轮机壳体12内的放置而限定。表面52、54、56和58限定了翼型件构造(旗部(flag)),该翼型件构造可被认为是叶片22的结构部分。叶片22包括在内径向表面52和外径向表面54的相对的共用端处的前缘或鼻部60和后缘62。如本文所使用的,术语前缘用于指叶片22的圆形鼻部部分,并且不旨在为急剧或突然成角度的表面特征。叶片22包括远离轴向表面58向外突出并且邻近前缘60定位的凸出部30,该凸出部30构造成以上述方式与同步环槽32协作以便于叶片致动。轴26包括扩大的直径区段70,其被定尺寸和构造成在开口28内提供牢固的压配合附接。与扩大的直径区段70相邻的是凹入的直径区段72。当然,在替代实施例中,轴26可以具有恒定或基本恒定的直径。在任一实施例中,轴26可具有约10mm或更小的最大直径。轴26可被认为是叶片22的功能部分。
21.叶片22可以使用展现良好强度、可加工性以及高温抗氧化性和耐磨性的金属材料制造。在一些实施例中,叶片22可以使用不锈钢材料制造。不锈钢是铁基合金,其包括至少11%的铬,以及一种或多种其他合金元素,诸如例如碳、氮、铝、硅、硫、钛、镍、铜、硒、铌和钼。不锈钢可以是奥氏体、铁素体或马氏体。在一些实施例中,奥氏体不锈钢可用于制造叶片22,这是由于它们的高温性能和易于加工。如上所述,也可以适当地采用其他合金,诸如例如镍基超合金。叶片22可以使用铸造、金属注射成型、增材制造或其他已知的工艺来制造。
22.返回参考图3,如图所示,功能轴26的区段的表面,即扩大直径区段70,由与叶片22的其余部分(即,凹入直径区段72和翼型件(旗部)52、54、56、58的结构表面)不同的材料构成。这可以通过应用合适的旋转地高速的全自动激光熔覆工艺来实现,该熔覆工艺使用比用于形成叶片22的典型合金更耐磨的包覆材料。在轴26具有恒定或基本恒定的直径的实施例中,不同的材料可以存在于整个轴26的表面处。包覆材料表现出与典型的(较不昂贵)基底叶片合金的足够的粘附性,该基底叶片合金诸如为如上所述的不锈钢合金或镍基超合金等,叶片22的其余部分由该基底叶片合金制成。例如,在不锈钢合金(其说明性示例为hk 30)用作基底合金的情况下,更高温的镍基超合金或增强镍基超合金(其说明性示例分别为inconel 601或inconel 713)可用作包覆材料。在另一示例中,在镍基超合金(其说明性示例为inconel 601)用作基底合金的情况下,可以使用进一步更高温度的增强镍基超合金(其说明性示例为inconel 713或718(适于在高达约1050℃的温度下使用))作为包覆材料。当然,合金的其他组合也是合适的。通常,可以选择基底合金和包覆合金,使得包覆合金具有比基底合金的温度规格高约10℃至约100℃的温度规格,诸如高从约20℃至约70℃。如本文所使用的,术语“温度规格”用于表示所参考的材料在较高温度下具有至少一种改善的机械功能性能,其非限制性示例包括:热机械性能、耐磨性、硬度、摩擦系数、抗氧化性。为了实现叶片轴26的限定功能区域、即区段70的高质量、无孔且无裂纹的处理,包覆材料层的最小所需厚度可以是沉积在轴26的限定区域70的表面上的从约20μm至约500μm(诸如从约20μm
至约200μm,例如从约20μm至约100μm,诸如从约20μm至约50μm)。
23.激光熔覆是一种沉积材料的方法,通过该方法,粉末状或丝状原料材料通过使用激光被熔化和固结,以便涂覆部分衬底。用于激光熔覆的粉末通过同轴或横向喷嘴注入系统中。金属粉末流和激光的相互作用导致发生熔化,并且被称为熔池。将其沉积在衬底上;移动衬底允许熔池凝固,从而产生固体金属的轨道。衬底的运动由cad系统引导,该cad系统将固体物体插入一组轨道中,从而在轨迹的末端产生期望的部件。
24.现在参考图4,其示出了根据本公开的实施例使用的合适的激光熔覆装置400。装置400在附图标记401a处开始,其包括提供或获得仅由基底合金制成的未处理叶片(22a),所述基底合金是例如不锈钢合金或镍基超合金,如上所述)。如附图标记401b处所示,叶片22a(“衬底”)被放置在激光熔覆设备中。在附图标记402处,激光束被激活并被引导到衬底。此后,在附图标记403处,激活的激光束使得在衬底上形成熔池。当激光束被激活时,衬底围绕穿过叶片轴的中心的轴线以高速旋转,如附图标记404处所示。激光束的形状由聚焦镜(或透镜)的光学器件控制,并且可以通过改变聚焦装置与衬底的表面之间的工作距离来调整光束面积。例如,激光束可以垂直于或横向于衬底表面(即,叶片轴的限定区域(70))。可以在本领域普通技术人员的技术水平内调整的激光操作的合适参数可以包括光斑尺寸、强度、波长、激光功率、扫描速度、供给速率和粉末预热。这些参数影响热影响区(haz)和结合区(附图标记405)的范围,其影响包覆层的最终质量(附图标记406)。
25.继续参考图4,如附图标记407处所示,与熔体结合的预热粉末形式的包覆材料由载气(附图标记408)通过粉末供给系统(附图标记409)供应。激光熔覆设备包括确保叶片22a和激光束的相对移动的机器人系统。例如,衬底可以被夹持到专用夹具,该专用夹具覆盖叶片旗部,并且相对于静止的激光粉末输送系统(附图标记410)(以高速)旋转以及线性地移动。因此,激光熔覆工艺包括使vgt叶片高速旋转(这种速度是本领域的激光熔覆机器已知且使用的),并且在使vgt叶片以高速旋转之前在旗部部分上方提供高速旋转夹持夹具(即,在围绕穿过轴的轴线高速旋转期间夹持到旗部部分且使旗部部分稳定的夹具),以便保护旗部部分且防止对旗部部分的任何损坏(为了图示清楚而未单独示出)。诸如氦、氩、氮等的保护气体(附图标记411)与载气一起被输送到包覆区域,以保护熔池免受大气影响,否则大气可能导致氧化。
26.结果,如附图标记412处所示,叶片轴区段70具有如上所述的包覆层,该包覆层在高温下具有更高的硬度和耐磨性。更具体地,提供了一种可变几何形状涡轮增压器叶片(22b),其包括结构性的翼型件形状的旗部部分和连接到旗部部分的功能性的柱形形状的轴部分。旗部部分和轴部分由第一金属合金形成,并且轴部分还包括由不同于第一金属合金的第二金属合金形成的表面区域。
27.图5是示出根据本公开的用于制造vgt叶片的方法500的流程图。方法500包括涉及提供或获得未处理的vgt叶片的各个步骤。未处理的vgt叶片包括结构性的翼型形状的旗部部分和连接到旗部部分的功能性的柱形形状的轴部分。旗部部分和轴部分由第一金属合金形成。方法500还包括与使用不同于第一金属合金的第二金属合金使轴部分经受激光熔覆工艺相关的各种步骤,从而在轴部分上形成第二金属的表面区域。
28.更具体地,方法500可以开始于步骤502,其中vgt叶片最初例如使用铸造或金属注射成型(mim)技术制造。然后,在步骤504处,在步骤502中不包括设计的某些特征的情况下,
进行预加工的可选步骤,其不需要在所有实施例中执行,或者更接近地实现期望的公差。此后,在步骤506处,使用例如合适的溶剂或其他常规清洁方法预清洁vgt叶片。然后,在步骤508处,如上所述,执行激光熔覆工艺。在激光熔覆工艺之后,可以完成在所有实施例中都需要执行的可选的后加工步骤510。如果采用的话,步骤508可以使用常规的加工技术来执行,或者优选地,可以使用激光再熔化来执行。激光再熔化可以用一个工艺步骤并且使用与步骤508中相同的激光来完成。之后,可在步骤512处以上文关于步骤506描述的方式执行后清洁工艺。方法500以最终检查步骤514和包装及装运步骤516结束。
29.因此,本公开已经提供了双金属可变几何形状涡轮增压器叶片以及用于使用激光熔覆技术制造双金属涡轮增压器叶片的方法。该方法提供了使用激光熔覆工艺来对叶片的功能部分,即叶片轴的表面区域进行局部处理。这已经通过应用合适的旋转高速、全自动激光熔覆工艺来实现,该熔覆工艺具有比用于形成叶片的典型(较不昂贵)合金更耐磨的包覆材料。包覆材料表现出与典型的基底叶片合金的足够的粘附性,并且它们实现叶片轴的限定的功能区域的高质量、无孔和无裂纹的处理。作为优于现有技术的益处,这种经由激光熔覆的表面处理保护关键的叶片轴区域免受摩擦磨损,并且不改变叶片几何形状。因此,本公开已经提供了一种限于叶片轴的关键表面区域的处理,以提高高温下的耐磨性并避免叶片轴的这些受应力区域上的缺陷,与使用特殊材料用于整个叶片相比,成本降低。
30.虽然在本发明主题的前述具体实施方式中已经呈现了至少一个示例性实施例,但是应当了解,存在大量的变型。还应当了解,一个或多个示例性实施例仅是示例,并且不旨在以任何方式限制本发明主题的范围、适用性或构造。相反,前面的具体实施方式将为本领域技术人员提供用于实现本发明主题的示例性实施例的方便的路线图。应当理解,在不背离所附权利要求中阐述的本发明主题的范围的情况下,可以对示例性实施例中描述的元件的功能和布置进行各种改变。