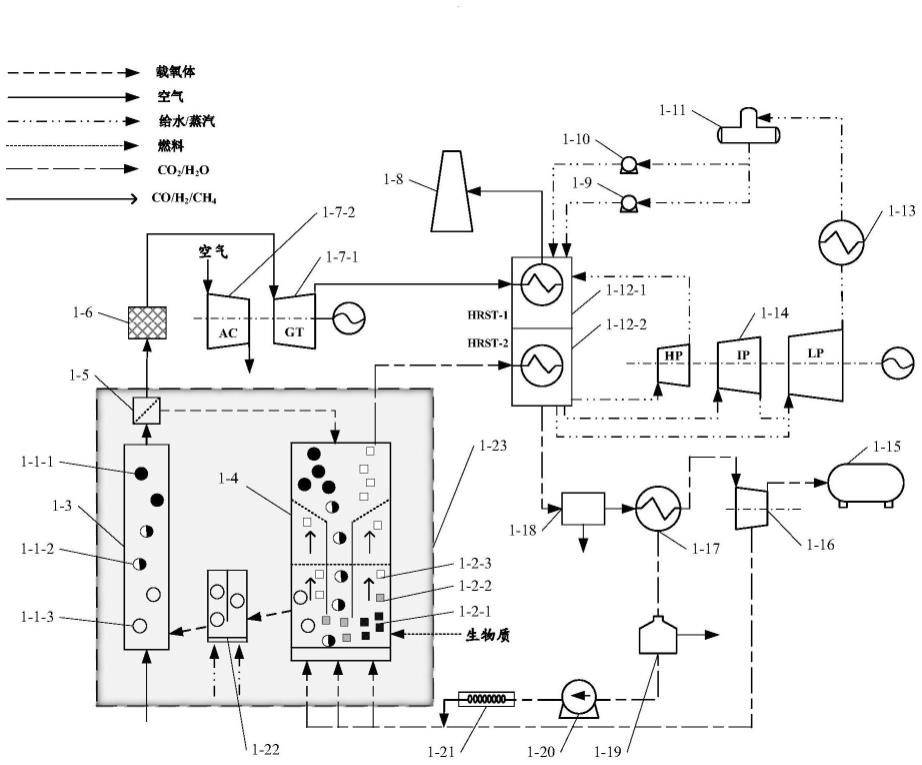
生物质加压化学链燃烧发电和负碳系统、燃料反应器
1.技术领域:本发明涉及生物质能源利用领域,具体涉及生物质加压化学链燃烧发电和负碳系统、燃料反应器。
背景技术:2.在全世界的能源消费体系当中,化石燃料燃烧所排放的co2是造成温室效应的主要原因。中国产业发展促进会生物质能产业分会发布的蓝皮书显示,目前我国主要生物质资源年产生量约为34.94亿吨,生物质资源能源化利用量约为4.61亿吨。随着近些年来全世界对温室效应的日益重视,生物质的能源利用在不实施co2捕集的情况下具有零碳特征,受到世界各国的普遍关注。目前,通过丰富的生物质资源实施燃烧发电,对于我国实现节能减排、“双碳目标”和可持续发展具有重要的现实意义。当前背景下,采用co2捕集技术与生物质燃烧发电相结合是实现“双碳”战略的一个重要技术途径。目前,生物质能源化利用技术方面进行了较为广泛的开发,但与co2捕捉技术结合实现低成本“负碳”排放和高效发电尚属于新领域,是当前能源技术和co2减排领域的一种迫切需求。
3.化学链燃烧是一种近乎可以实现零碳排放的新型燃料燃烧技术。它将传统燃料与空气燃烧方式分为两个步骤,即在燃料反应器内燃料与载氧体高温反应生成还原态载氧体和空气反应器内还原态的载氧体与空气的再生反应。燃料反应器通常为吸热反应,产物为二氧化碳和水蒸气,经过冷凝后理论上可获得纯co2,实现碳分离;空气反应器内反应为剧烈放热反应,产生的高温热烟气主要成分为氮气,可以用于发电或产生蒸汽。化学链燃烧主要依靠具有传氧功能的耐高温固体载氧体在两个反应器间循环释放氧和吸收氧来实现燃料的间接燃烧;它可以有效避免燃料和空气的直接接触,即避免了能耗极高的气-气分离过程,从而在理论能耗为零的情况下实现燃烧过程中co2分离。如果将上述具有燃烧过程中实施co2分离的高效化学链燃烧技术与生物质发电相结合,并在具体实施方案上实现突破,才能充分发挥出两者优势,实现“负碳排放”和高效发电目标。
4.以生物质作为燃料用于化学链燃烧,可以采用两种基本方式。
5.一种方式中,可以将生物质先气化,将合成气做燃料用于化学链燃烧,基本工艺流程较长,且仍然无法避免能耗较高的空气分离过程,导致总体效率低、而发电成本和co2捕集成本较高。
6.另一种方式中,可以将生物质作为固体燃料直接用于化学链燃烧,由化学链燃烧后高温烟气作为热源产生高温、高压蒸汽后再去推动汽轮机组发电;虽然系统得到了一定简化,但由于蒸汽参数的限制,发电效率一般在35%以下,无法兼顾高效发电和低成本co2捕集的总体目标,与现有燃煤电站燃烧后co2捕集技术相比并无明显优势。而且,在第二种方式下生物质燃料气化过程为速率限制步骤,导致化学链燃烧装置体积庞大,投资成本过高。
7.
技术实现要素:本发明要解决的技术问题:针对所述现状,本发明提出一种生物质加压化学链燃烧发电和捕集co2负碳系统,通过将化学链循环燃烧、增压流化床、燃气—蒸汽联合循环发
电相结合,采用结构优化的新型化学链燃烧反应装置,进而最大限度地提高燃烧效率、co2捕集效率和净发电效率,实现“负碳排放”。
8.技术方案:包含生物质加压化学链燃烧系统、燃气轮机发电系统、余热发电系统和co2压缩脱水纯化工艺系统;通过所述生物质加压化学链燃烧系统,实施生物质燃料的燃烧和co2原位分离,产生高温高压烟气驱动所述燃气轮机发电系统;通过所述燃气轮机发电系统和余热发电系统耦合匹配,实施燃气蒸汽联合循环发电;通过所述co2压缩脱水纯化工艺系统将所述生物质加压化学链燃烧系统分离出的co2压缩至达到管道输送要求的超临界状态,输送至生物质加压化学链燃烧系统中,作为流化介质和气化介质。
9.进一步,所述生物质加压化学链燃烧系统采用高压运行方式;所述生物质加压化学链燃烧系统采用铁基载氧体和生物质颗粒分别作为循环传氧物料和燃料。
10.进一步的,所述生物质加压化学链燃烧系统包括空气反应器和燃料反应器;所述燃料反应器通过返料阀向空气反应器输送传氧物料;所述空气反应器和燃料反应器设置在所述耐压壳体内。
11.进一步的,空气经过空压机升压成为高压空气送入空气反应器;在所述空气反应器内,高压空气与还原态载氧体发生剧烈放热反应,形成高压高温烟气和氧化态载氧体;所述高压高温烟气经过旋风分离器颗粒分离和高温陶瓷过滤器除尘后,形成净化的高压高温烟气,进入燃气轮机膨胀做功,而后由燃气轮机末端进入余热锅炉烟气侧放热,温度降低至5
°
c以下形成低温低压烟气,由烟囱排入大气。
12.进一步的,所述氧化态载氧体经过旋风分离器送入燃料反应器;在所述燃料反应器内,生物质颗粒与所述氧化态载氧体之间发生充分燃烧反应,转化为co2/水蒸气混合气;所述co2/水蒸气混合气携带飞灰与剩余气化介质送入余热锅炉co2侧放热至120
°
c,降温后的co2/水蒸气混合气进入co2压缩脱水纯化工艺,被压缩净化为可供管道输送的超临界二氧化碳。
13.进一步的,所述余热发电系统设置包括余热锅炉烟气侧和余热锅炉co2侧;所述余热锅炉烟气侧吸收燃气轮机排气的热量;所述余热锅炉co2侧吸收燃料反应器出口co2/水蒸气混合气的热量,确保在整体工艺中两股气流之间彼此不掺混。
14.进一步的,所述生物质加压化学链燃烧反应系统,设计运行压力在1.2~2.0mpa,空气反应器设计操作温度为900~950
°
c,燃料反应器设计操作平均温度在600~750
°
c;所述的高温陶瓷过滤器的烟气入口温度控制在900
°
c以下;所述的燃气轮机的额定排汽温度为550
°
c;所述的余热锅炉烟气侧和余热锅炉co2侧的额定排烟温度为110~120
°
c。
15.进一步的,采用由炼铝废弃物或天然钛铁矿制备的铁基载氧体作为生物质加压化学链燃烧反应系统的循环物料传递晶格氧,通过挤出造粒或破碎制备成颗粒状,粒度范围0.2~0.5mm,通过高温煅烧使其具备反应活性和高机械强度;采用生物质燃料为制备成型的颗粒燃料。
16.本发明还公开了一种用于生物质加压化学链燃烧发电和捕集co2负碳系统的生物质加压化学链燃烧反应系统的燃料反应器,包括燃料反应器设置多孔板将所述燃料反应器分为上部反应区和下部反应区两个区域;所述下部反应区实施生物质颗粒快速热解、气化及反应中间产物气体与部分氧化态载氧体的还原反应,并采用鼓泡流态化,强化气固之间的混合与传热,防止生物质颗粒或焦炭与铁基载氧体间的分离倾向,提高生物质焦炭转化速率和燃尽率,实现铁基载氧体的深度还原;所述上部反应区,实现由所述下部反应区而来混合气与氧化态载氧体的燃烧反应,将混合气中的co/h2/ch4等可燃成分全部转化为co2和水蒸气。
17.进一步的,在燃料反应器内设置下降管;所述下降管两端分别连接多孔板和下部反应区,所述下降管下端部分埋入鼓泡流化床层内;在压力自平衡条件下,下降管将所述上部反应区的部分氧化态载氧体连续地送入所述下部反应区的鼓泡流化床层内部,以实现部分氧化态载氧体的快速扩散和与其他物料间的充分混合与热交。
18.本发明与现有技术相比的有益效果:1.本发明中生物质加压化学链燃烧发电和负碳系统将先进的化学链循环燃烧、增压流化床、燃气-蒸汽联合循环发电相结合,能够最大限度地提高燃烧热效率、co2捕集效率和净发电效率,并采用资源量丰富的生物质为燃料,从而降低发电成本,实现“负碳排放”。
19.2.采用了加压循环流化床实现化学链燃烧,并在燃料反应器下部采用鼓泡流化床形式,可有效调整气体、生物质和载氧体之间的混合流动,实现生物质颗粒热解、气化反应及载氧体还原反应之间的热-质耦合,提高固体燃料转化速率和燃尽率,可实现高效燃烧,减小设备体积和投资成本。
20.3.在燃料反应器上部设置反应区,采用氧化态载氧体将可燃气体成分充分燃烧,降低了热损失,提高了反应器出口co2捕集浓度。
21.4.本发明采用廉价的铁基载氧体实施生物质化学链燃烧,该类载氧体具备高反应活性和催化气化功能、抗灰和抗烧结能力,具有较高的机械强度和热稳定性,价格低廉,降低运行和co2捕集成本。
附图说明
22.图1为本发明中生物质加压化学链燃烧发电和负碳系统图;图2为本发明中生物质加压化学链燃烧反应装置图。
23.附图标记说明:1-1-1氧化态载氧体;1-1-2部分氧化载氧体;1-1-3还原态载氧体;1-2-1生物质颗粒;1-2-2生物质焦炭;1-2-3飞灰;1-3空气反应器;1-4燃料反应器;1-5旋风分离器;1-6高温陶瓷过滤器;1-7-1燃气轮机;1-7-2空气压缩机;1-8烟囱;1-9高压给水泵;1-10低压给水泵;1-11除氧器;1-12-1余热锅炉烟气侧;余热锅炉co2侧1-12-2;1-13冷凝器;1-14汽轮机;1-15液态co2储存罐;1-16co2压缩机;1-17co2除水冷凝器;1-18颗粒分离装置;1-19储液箱;1-20水泵;1-21蒸发器;1-22返料阀;1-23耐压壳体;2-1多孔板;2-2下降管;2-3一级料罐;2-4二级料罐;2-5螺旋给料器。
具体实施方式
24.为使本发明的目的,技术方案和优点更加清楚,下面将结合本发明实例中的附图,对本发明中的技术方案进行更加清楚,完整地描述。
25.如图1所示,本发明提出的生物质加压化学链燃烧发电和捕集co2负碳系统,通过生物质加压化学链燃烧反应装置、燃气轮机发电系统、余热发电系统和co2压缩-脱水-纯化工艺之间的顺序匹配和系统耦合,完成生物质燃料的高效燃烧、co2低成本原位分离及高效发电。
26.本发明具体包括:空气反应器1-3;燃料反应器1-4;旋风分离器1-5;高温陶瓷过滤器1-6;燃气轮机1-7-1;空压机1-7-2;烟囱1-8;高压给水泵1-9;低压给水泵1-10;除氧器1-11;余热锅炉烟气侧1-12-1;余热锅炉co2侧1-12-2;冷凝器1-13;汽轮机1-14;液态co2储存罐1-15;co2压缩机1-16;co2冷凝器1-17;颗粒分离装置1-18;储水箱1-19;水泵1-20;蒸发器1-21;返料阀1-22;耐压壳体1-23。
27.空气反应器1-3和燃料反应器1-4构成生物质加压化学链燃烧装置主体部分,分别实现还原载氧体1-1-3的氧化再生和生物质颗粒燃料1-2-1与氧化态载氧体1-1-1间的燃烧反应;分别产生高温、高压烟气和co2/水蒸气混合气,前者驱动燃气轮机1-7-1做功,后者为余热锅炉co2侧1-12-2提供热能,以此实现生物质燃烧过程和co2分离;两个反应器置于耐压壳体内实施高压力下反应过程。
28.燃气轮机1-7-1与空压机1-7-2同轴,前者将高温、高压烟气在其中膨胀做功,为空压机1-7-2压缩空气提供动力,多余机械能用于发电;与传统燃气轮机系统不同,燃气轮机1-7-1不设置顶燃烧室。
29.设置旋风分离器1-5和高温陶瓷过滤器1-6,分别除去大颗粒和细飞灰;在进入燃气轮机1-7-1做功前,高温烟气含尘量应《0.5μg/nm3。
30.在燃气轮机1-7-1下游设置余热发电系统,形成高效的燃气-蒸汽联合循环发电方式;余热锅炉设置为余热锅炉烟气侧1-12-1和余热锅炉co2侧1-12-2,分别吸收燃气轮机1-7-1的排气热量和燃料反应器1-4出口co2/水蒸气混合气的热量,两股气流之间彼此不掺混;余热锅炉的蒸汽动力侧采用一体化设置,采用双压或三压参数提高循环效率。
31.co2压缩机1-16可将co2气体直接压缩至工业级低温液体co2后送至液态co2储存罐1-15存储,再进一步提升压力后进行管道输送。co2气体在进入co2压缩机1-16前,需要经过颗粒分离装置1-18和co2冷凝器1-17除去固体颗粒和大部分水分。当需要除去so2杂质气体时,co2气体可采用两段压缩,即co2压缩机1-16将co2气体初步压缩至2.0~2.5mpa温度40℃左右,进一步通过脱硫装置和脱水模块后,再将高压co2气体压缩至临界状态。燃料反应器1-4出口气体中含有较高浓度的no
x
,co2压缩流程还需要设置no
x
去除工艺和设备。
32.生物质加压化学链燃烧发电和捕集co2负碳系统使用廉价铁基载氧体以降低运行成本,如采用炼铝废弃物或天然钛铁矿制备载氧体,通过挤出造粒或破碎制备成颗粒状,粒度范围0.2~0.5mm,通过煅烧工艺使其具备较高反应活性和机械强度;所使用的生物质燃料同样需要预先制备为成型颗粒燃料,以方便高压加料。
33.以300mwe装机容量为例,的生物质加压化学链燃烧反应装置,其设计运行压力在1.2~2.0mpa,空气反应器1-3操作温度为900~950
°
c,燃料反应器1-4操作平均温度在600~750
°
c;运行中防止反应温度过高,以防载氧体颗粒与飞灰烧结与团聚。高温陶瓷过滤器1-6
入口温度控制在900
°
c以下,防止温度过高导致的材料寿命减损和表面高温灰分粘结。燃气轮机1-7-1的额定排汽温度为550
°
c;余热锅炉烟气侧1-12-1和余热锅炉co2侧1-12-2的额定排烟温度均为110~120
°
c。
34.生物质加压化学链燃烧发电和负碳系统运行方式如下:空气经过空压机1-7-2压缩提升》1.2mpa后送入空气反应器1-3,与燃料反应器1-4返回的还原态载氧体1-1-3发生剧烈放热反应,形成高压高温烟气,经过旋风分离器1-5和高温陶瓷过滤器1-6实施颗粒分离和除尘后,进入燃气轮机1-7-1膨胀做功,压力降低至略高于大气压力,温度降低至550
°
c左右,而后进入余热锅炉烟气侧1-12-1放热,温度再次降低至115
°
c以下,无需脱硫、脱硝净化过程直接由烟囱1-8排入大气。
35.在燃料反应器1-4,生物质颗粒1-2-1与氧化态载氧体1-1-1发生充分燃烧反应,最终转化为co2/水蒸气混合气,该混合气携带飞灰1-2-3与剩余气化介质送入余热锅炉co2侧1-12-2放热至120
°
c,而后进入下游的co2压缩、脱水和纯化工艺;其中一部分co2和水分用作燃料反应器1-4的流化介质和气化介质。
36.正常运行状态下,载氧体颗粒在空气反应器1-3与燃料反应器1-4之间连续循环;在两者之间设置旋风分离器1-5和返料阀1-22,以实现载氧体的物料循环和装置连续运行,确保两个反应器中的气体不掺混。
37.在如上的运行参数下,将本发明提出的生物质加压化学链燃烧发电和捕集co2负碳系统的容量设定在300mw发电量,脱水后co2捕集浓度设定在95%,压缩至15.0mpa液态;设定关键设备参数,燃料反应器1-4的燃料转化率98%;空压机1-7-2等熵效率85%、燃气轮机1-7-1的等熵效率和机械效率分别为95%和99%、余热锅炉烟气侧1-12-1和余热锅炉co2侧1-12-2保温效率98%、采用三压参数且汽轮机1-14高中低压缸的等熵效率分别为88%、92.5%和92%。此时,该工艺系统对应的理论计算发电效率可达42%左右,远高于相同容量常规火力发电机组采用燃烧后捕集co2方式的发电效率30%左右。
38.如图2所示,本发明提出的生物质加压化学链燃烧反应装置中,通过铁基载氧体颗粒在两个反应器中循环传递晶格氧,实现生物质燃料燃烧和co2就地分离,并通过耐压壳体承压实现加压化学链燃烧方式,该装置主要构成为:空气反应器1-3、燃料反应器1-4、旋风分离器1-5、耐压壳体1-23、返料阀1-22、多孔板2-1、下降管2-2、一级料罐2-3、二级料罐2-4、螺旋给料器2-5和辅助管路。
39.空气反应器1-3和燃料反应器1-4相互串联;空气反应器1-3和燃料反应器1-4及其附件置于金属耐压壳体1-23中,金属耐压壳体1-23承受高压,以此实现空气反应器1-3和燃料反应器1-4内的反应在相同的背景压力下进行。
40.空气反应器1-3是还原态载氧体1-1-3实现空气氧化再生的场所,采用快速流态化,并可以将氧化态载氧体1-1-1输送至空气反应器1-3上部,以此为载氧体在燃烧装置内循环流动提供动力。
41.空气反应器1-3内为剧烈放热反应,产生的热量一部分由烟气吸收形成高温烟气经过净化后去燃气轮机做功;其余部分热量以氧化态载氧体1-1-1显热的形式带入燃料反应器1-4,为反应提供所需热量和晶格氧;燃料反应器1-4是生物质颗粒1-2-1热解、气化中间产物与铁基载氧体反应生成co2和水蒸气的场所。在燃料反应器1-4内设置多孔板2-1,将反应分为两个区域进行:在燃
料反应器1-4下部为生物质颗粒1-2-1快速热解、气化反应及中间产物气体与部分氧化态载氧体1-1-2之间的还原反应,采用鼓泡流态化,强化气体-固体间的传热传质,调整气体、生物质和载氧体之间的混合流动,防止生物质颗粒或焦炭1-2-1,1-2-2与载氧体间的分离倾向,提高生物质焦炭的转化速率和燃尽率,并实现载氧体的深度还原;在燃料反应器1-4上部,混合气穿过多孔板2-1后与氧化态载氧体1-1-1床层进行反应,实现充分燃烧,并完全转化为co2/水蒸气混合气。
42.在燃料反应器1-4内设置下降管2-2,下降管两端分别连接多孔板2-1和燃料反应器1-4下部反应区,下降管2-2下端部分埋入燃料反应器下部反应区流化床层,在压力自平衡条件下下降管将燃料反应器上部的部分氧化态载氧体1-1-2连续送入燃料反应器1-4下部的床层内部,实现部分氧化态载氧体快速扩散和与其他物料间的充分混合。
43.设置返料阀2-2,采用高温蒸汽作流化介质,将燃料反应器2-4下部床层内还原态载氧体2-1-3连续送入空气反应器2-3床层底部。
44.新鲜载氧体由返料阀1-22加入,以补充载氧体在化学链燃烧反应装置内的损耗;生物质燃料制备成为颗粒状1-2-1,从燃料反应器1-4下部床层加入。
45.生物质加压化学链燃烧反应装置在1.2~2.0mpa压力下运行,空气反应器1-3操作温度为900~950
°
c,燃料反应器1-4操作平均温度在600~750
°
c。
46.本发明中,生物质加压化学链燃烧发电和捕集co2系统运行方式如下:由空气反应器1-3来的高温氧化态载氧体1-1-1,经过高温旋风分离器1-5后由燃料反应器1-4顶部加入到燃料反应器1-4上部反应区。在燃料反应器1-4上部反应区内,氧化态载氧体1-1-1与穿过多孔板2-1而来的可燃成分反应,生成为部分氧化态载氧体1-1-2,而后经由下降管2-2连续送入燃料反应器1-4下部反应区内。在燃料反应器1-4下部反应区内,部分氧化态载氧1-1-2颗粒在鼓泡床层内快速与生物质颗粒1-2-1、生物质焦炭1-2-2和气化介质间之间进行充分混合与热交换,并与生物质热解、气化中间产物进行还原反应后生成还原态载氧体1-1-3,通过返料阀1-22输送至空气反应器1-3后与高压空气进行再生反应。经过再生后获得高温氧化态载氧体1-1-1,再由空气反应器1-3上部再次输送至燃料反应器1-4内开始下一个循环反应过程。
47.存放于一级料罐2-3中的生物质颗粒1-2-1,经由二级料罐2-4和螺旋给料器2-5实现精确料量输送至燃料反应器1-4下部的鼓泡床反应区。在鼓泡床反应区内,生物质颗粒1-2-1与床料快速混合,并热解出生物质焦炭1-2-2和热解气,生物质焦炭1-2-2在气化介质作用下完全气化为合成气成分。混合的热解气和合成气大部分与部分氧化态载氧体1-1-2反应后,生成的气体以co2和水蒸气占主导地位,并含有一定量的可燃成分;该气体与剩余的气化介质继续上升并穿过多孔板2-1,其中可燃部分与氧化态载氧体1-1-1充分反应后生成co2和水蒸气,其温度可达》600
°
c,携带飞灰1-2-3到下游进行余热回收。
48.高压空气从空气反应器1-3下部送入,在空气反应器内氧气成分与还原态载氧体1-1-3发生剧烈放热反应;空气吸收反应热,同时将新生的氧化态载氧体1-1-1颗粒输送至空气反应器1-3顶部,经过高温旋风分离器1-5分离后,其参数可达到900
°
c/1.0~2.0mpa,然后进一步净化后送入燃气轮做功。
49.上述具体实施方式,仅为说明本发明的技术构思和结构特征,目的在于让熟悉此项技术的相关人士能够据以实施,但以上内容并不限制本发明的保护范围,凡是依据本发
明的精神实质所作的任何等效变化或修饰,均应落入本发明的保护范围之内。