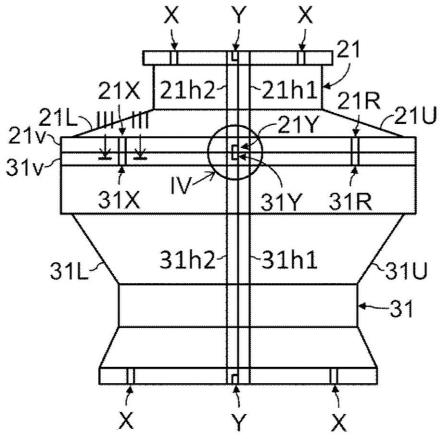
1.本发明涉及涡轮机机室、燃气轮机以及对位方法。
背景技术:2.例如,燃气轮机具备生成压缩空气的压缩机、将燃料混合于压缩空气并使其燃烧而生成燃烧气体的燃烧器、以及由燃烧气体驱动的涡轮机。构成该燃气轮机的外轮廓的涡轮机机室通常在轴向上被分割成多个部件(专利文献1)。
3.在先技术文献
4.专利文献
5.专利文献1:日本特开2013-181503号公报
6.在组装燃气轮机时,在内部组装转子而进行的最终组装之前,进行仅涡轮机机室的单件组装。在该单件组装的工序中,在使涡轮机机室铅垂地立起的状态下实施各部件的轴对准(中心对准)。在轴对准的作业中,有时使用在以杆(pole)为中心回转的臂安装有千分表的对准夹具。具体而言,以覆盖杆的方式放置部件,使臂绕杆回转并利用千分表测量杆与部件的内周面的距离,以内周面的整周距杆为等距离的方式在水平方向上调整部件的位置。通过每次对堆叠的全部部件进行这样的作业,从而以杆为基准使部件彼此的轴对齐。
7.但是,该作业需要时间,另外需要准备专用的对准夹具。
技术实现要素:8.本发明的目的在于提供一种不需要专用的对准夹具,且能够缩短单件组装的时间的涡轮机机室、燃气轮机以及对位方法。
9.为了实现上述目的,本发明提供一种涡轮机机室,其在轴向被分割为通过彼此的凸缘连结的所述第一壳体以及所述第二壳体,并且所述第一壳体以及所述第二壳体分别从轴向观察时被分割为上半壳体和下半壳体这两个部分,其中,所述涡轮机机室在周向上具有3个以上的设置于所述第一壳体的凸缘外周部的第一径向基准面与设置于所述第二壳体的凸缘外周部的第二径向基准面的组,各第一径向基准面位于距涡轮机中心轴等距离的位置,各第二径向基准面位于距所述涡轮机中心轴等距离的位置,所述涡轮机机室构成为,所述第一径向基准面与所述第二径向基准面的位置关系在各组中相等。
10.发明效果
11.根据本发明,不需要专用的对准夹具,且能够缩短单件组装的时间。
附图说明
12.图1是本发明的一实施方式的燃气轮机的一例的概要结构图。
13.图2是将构成本发明的一实施方式的燃气轮机的涡轮机机室的第一壳体及第二壳体抽出而表示的图。
14.图3是图2中的iii-iii线的剖视图。
15.图4是图2中的由箭头iv示出的部分的放大图。
16.图5是图3中的v-v线的剖视图。
17.附图标记说明:
18.21...燃烧器壳体(第二壳体);1c...第二侧倾基准面;21l...下半壳体;21r...第二径向基准面;21u...上半壳体;21v...凸缘;21x...狭缝;21y...切口;31...涡轮机壳体(第一壳体);31c...第一侧倾基准面;31l...下半壳体;31r...第一径向基准面;31u...上半壳体;31v...凸缘;31x...狭缝;31y...切口;41...贯通孔;43...定位销;44...衬套;dr...高低差(第一径向基准面与第二径向基准面的位置关系);r1...第一径向基准面与涡轮机中心轴的距离;r2...第二径向基准面与涡轮机中心轴的距离。
具体实施方式
19.以下,使用附图对本发明的实施方式进行说明。
[0020]-燃气轮机-[0021]
图1是本发明的一实施方式的燃气轮机的一例的概要结构图。该图所示的燃气轮机是驱动负载设备(未图示)的原动机,具备压缩机10、燃烧器20、涡轮机30、以及排气室35。压缩机10的壳体(压缩机壳体11)由腿部12支承,涡轮机30的壳体(涡轮机壳体31)由腿部32支承,排气室35由腿部38支承。负载设备代表性地是发电机,但有时也应用泵。需要说明的是,在将燃气轮机称为“燃气轮机发动机”的情况下,有时将涡轮机称为“燃气轮机”。
[0022]
压缩机10具有取入空气的空气取入口13、以及压缩机壳体11内的入口导向叶片(igv:inlet guide vane)14,并且在入口导向叶片14之后具备在涡轮机中心轴方向上交替地配置有静叶15和动叶16的级部。燃烧器20在压缩机10与涡轮机30之间在燃烧器壳体21的外周部呈环状地配置有多个。涡轮机30在涡轮机壳体31内具备沿涡轮机中心轴方向交替地配置的静叶33和动叶34。在该涡轮机壳体31的下游侧经由排气壳体36配设有排气室35。排气室35具有与涡轮机30连续的排气扩散器37。
[0023]
另外,转子5以贯通压缩机10、燃烧器20、涡轮机30及排气室35的中心的方式配置。转子5中的压缩机10侧的端部由轴承6旋转自如地支承,排气室35侧的端部由轴承7旋转自如地支承。转子5中的属于压缩机10的部分通过在外周部沿轴向重叠多个装配有多个动叶16的叶盘而构成。转子5中的属于涡轮机30的部分通过在外周部沿轴向重叠多个装配有多个动叶34的叶盘而构成。在图1的例子中,转子5中的排气室35侧的端部作为输出轴与负载设备(未图示)的驱动轴连结。
[0024]
在上述结构中,从空气取入口13取入至压缩机10的空气通过入口导向叶片14、静叶15的叶栅、动叶16的叶栅而被压缩,生成高温高压的压缩空气。在燃烧器20中,从燃料系统供给的燃料与从压缩机10供给的压缩空气混合并燃烧,生成高温的燃烧气体并向涡轮机30供给。燃料使用液体燃料或气体燃料。由燃烧器20生成的工作流体即高温高压的燃烧气体在涡轮机30中通过静叶33的叶栅和动叶34的叶栅,从而驱动转子5旋转。涡轮机30的输出的一部分用作压缩机10的动力,剩余部分用作负载设备4的动力。驱动涡轮机30后的燃烧气体经由排气室35作为废气排出。在本实施方式中,例示了单轴的燃气轮机,但发明的适用对象也包括双轴式燃气轮机。双轴式燃气轮机是包括旋转轴相互分离的高压涡轮机及低压涡轮机、且高压涡轮机与压缩机同轴地连结、低压涡轮机与涡轮机同轴地连结的结构。
[0025]-涡轮机机室-[0026]
在上述燃气轮机中,具备将转子5收容在内部的涡轮机机室。涡轮机机室在涡轮机中心轴方向上被分割成多个作为筒形部件的分割壳体、具体而言压缩机壳体11、燃烧器壳体21、涡轮机壳体31、排气壳体36等。压缩机壳体11和燃烧器壳体21在彼此的对置部具备铅垂的圆环状的凸缘(例如在图2中后述的凸缘21v、31v等),通过利用螺栓(未图示)将这些凸缘紧固而连结。燃烧器壳体21和涡轮机壳体31也同样。涡轮机壳体31和排气壳体36也同样。另外,涡轮机机室的轴向的分割数能够变更。
[0027]
而且,压缩机壳体11、燃烧器壳体21、涡轮机壳体31、排气壳体36这样的涡轮机机室的各部件分别从轴向观察时被分割为上半壳体和下半壳体这两个部分。各上半壳体和与其对应的下半壳体在彼此的对置部具备水平延伸的凸缘(例如在图2中后述的凸缘21h1、21h2、31h1、31h2等),通过利用多个螺栓(未图示)将这些凸缘紧固而连结。
[0028]-对准结构-[0029]
图2是将构成涡轮机机室的第一壳体及第二壳体抽出而表示的图,图3是图2中的iii-iii线的剖视图,图4是由图2中的箭头iv示出的部分的放大图,图5是图3中的v-v线的剖视图。在燃气轮机的组装中,在将转子5(图1)组装于涡轮机机室而进行的最终组装前,进行涡轮机机室的单件组装。在图2-图5中,模拟在涡轮机机室的单件组装中进行的第一壳体与第二壳体的对位(对准)时的情形。具体而言,示出将涡轮机中心轴设为铅垂而在第一壳体上堆叠第二壳体的状态。
[0030]
在本技术说明书中,将在涡轮机轴向上相邻且通过彼此的凸缘连结的涡轮机机室的部件(分割壳体)适当记载为第一壳体及第二壳体。在图2中,作为第一壳体及第二壳体,例示了涡轮机壳体31及燃烧器壳体21。此外,排气壳体36及涡轮机壳体31、以及燃烧器壳体21及压缩机壳体11也相当于第一壳体及第二壳体。另外,第一壳体和第二壳体的对象也可以相反。
[0031]
在涡轮机机室中,在第一壳体(在此为涡轮机壳体31)与第二壳体(燃烧器壳体21)的对置部沿周向隔开间隔地具备3个以上(在本例中为4个)径向基准面的组。径向基准面的各组由设置于涡轮机壳体31的凸缘31v的外周部的第一径向基准面31r(图3、图5)和设置于燃烧器壳体21的凸缘21v的外周部的第二径向基准面21r(图5)构成。
[0032]
第一径向基准面31r分别位于全部距涡轮机中心轴等距离(距涡轮机中心轴的距离r1的位置)的位置。另外,各第一径向基准面31r由设置于涡轮机壳体31的凸缘31v的外周部的扁平的槽状的狭缝31x的内壁面中的、与涡轮机中心轴平行且朝向涡轮机壳体31的径向外侧的面构成。在本实施方式中,第一径向基准面31r采用平面,沿涡轮机中心轴方向观察时,第一径向基准面31r与在距涡轮机中心轴的距离r1的位置包含涡轮机中心轴的平面正交。即,沿涡轮机中心轴方向观察时,第一径向基准面31r分别形成以涡轮机中心轴为中心的同一圆的切线。但是,第一径向基准面31r只要与第二径向基准面21r为既定的位置关系,则不需要是平面,例如也可以是曲面。
[0033]
第二径向基准面21r分别位于全部距涡轮机中心轴等距离(距涡轮机中心轴的距离r2的位置)的位置。另外,各第二径向基准面21r由设置于燃烧器壳体21的凸缘21v的外周部的扁平的槽状的狭缝21x的内壁面中的、与涡轮机中心轴平行且朝向燃烧器壳体21的径向外侧的面构成。在本实施方式中,第二径向基准面21r采用平面,沿涡轮机中心轴方向观
察时,第二径向基准面21r与在距涡轮机中心轴的距离r2的位置包含涡轮机中心轴的平面正交。即,沿涡轮机中心轴方向观察时,第二径向基准面21r分别形成以涡轮机中心轴为中心的同一圆的切线。但是,第二径向基准面21r只要与第一径向基准面31r为既定的位置关系,则不需要是平面,例如也可以是曲面。
[0034]
第一径向基准面31r与第二径向基准面21r的位置关系构成为在第一和第二基准面的各组中相等。第一径向基准面31r和第二径向基准面21r也可以成为同一平面(也就是说r1=r2),但只要彼此的位置关系在各组中相等即可,不一定必须是同一平面。在图5中,例示了第二径向基准面21r相对于涡轮机中心轴比第一径向基准面31r远离距离dr,从而在径向基准面31r、21r之间存在高低差的情况。
[0035]
另外,如图4所示,在涡轮机机室中,在第一壳体(涡轮机壳体31)与第二壳体(燃烧器壳体21)的对置部具备至少1组(在本例中以180
°
间距为2组)槽状的切口31y、21y。
[0036]
切口31y在涡轮机壳体31的上半壳体31u以及下半壳体31l中的一侧(在图4中为下半壳体31l)以与另一侧(上半壳体31u)对置的方式设置。即,切口31y设置于涡轮机壳体31的凸缘31v、31h2的端面交叉的角部分。上半壳体31u的与下半壳体31l对置的对置面(即上半壳体31u的凸缘31h1的端面)以一部分露出的方式面向该切口31y。面向该切口31y的凸缘31h1的端面构成用于进行涡轮机壳体31与燃烧器壳体21的周向的对位的第一侧倾基准面31c。因此,第一侧倾基准面31c相当于涡轮机壳体31的上半壳体31u的凸缘31h1的端面部中的凸缘31v的剖面。
[0037]
切口21y在燃烧器壳体21的上半壳体21u以及下半壳体21l中的一侧(在本例中设为下半壳体21l)以与另一侧(上半壳体21u)对置的方式设置。即,切口21y设置于燃烧器壳体21的凸缘21v、21h2的端面交叉的角部分。切口21y、31y的周向位置相对应,且彼此在涡轮机中心轴方向上对置。另外,上半壳体21u的与下半壳体21l对置的对置面(即上半壳体21u的凸缘21h1的端面)以一部分露出的方式面向切口21y。面向该切口21y的凸缘21h1的端面构成用于进行涡轮机壳体31与燃烧器壳体21的周向的对位的第二侧倾基准面21c。因此,第二侧倾基准面21c相当于燃烧器壳体21的上半壳体21u的凸缘21h1的端面中的凸缘21v的剖面。
[0038]
第一侧倾基准面31c以及第二侧倾基准面21c均为与下半壳体31l、21l对置的上半壳体31u、21u的端面,因此在涡轮机机室组装完成的状态下周向位置高精度地一致。切口31y、21y的周向的宽度尺寸可以一致,但不一定需要一致。
[0039]
另外,如图5所示,在第二壳体(燃烧器壳体21)的凸缘21v设置有与涡轮机中心轴平行的贯通孔41。另外,在第一壳体(涡轮机壳体31)的凸缘31v的端面设置有位置与贯通孔41对应的定位孔42。定位孔42是用于插入定位销43的销孔。定位销43的外径与定位孔42的内径的尺寸公差设定得极小,在定位销43的外周面与定位孔42的内周面之间实质上不存在间隙。定位销43的一部分通过贯通孔41插入涡轮机壳体31的凸缘31v的定位孔42,从定位孔42突出的剩余部分位于贯通孔41的内部。另外,衬套44位于贯通孔41的内部。
[0040]
衬套44是圆筒状的构件,作为覆盖并嵌入定位销43以填埋定位销43与贯通孔41间的间隙的间隔件发挥功能。定位销43的外径与衬套44的内径的尺寸公差设定得极小,在定位销43的外周面与衬套44的内周面之间实质上不存在间隙。与此相对,虽然在图5的示意图中未表示,但贯通孔41的内径设定为比衬套44的外径稍大,在贯通孔41的内周面与衬套44
的外周面之间存在规定的间隙。衬套44在嵌入定位销43的状态下通过焊接(焊接部45)固定于燃烧器壳体21的凸缘21v(例如贯通孔41的内壁)。由此,定位销43被定位孔42限制,衬套44被定位销43限制,贯通孔41被衬套44限制,凸缘31v、21v相互被限制。
[0041]
需要说明的是,在图2-图5中,以涡轮机壳体31与燃烧器壳体21的对置部的结构为例进行了说明,但关于径向基准面、侧倾基准面、定位销等的结构,在其他的第一壳体与第二壳体的对置部中也同样地具备。作为参考,在图2中,图示了径向基准面x、侧倾基准面y。
[0042]-涡轮机机室的对位方法-[0043]
使用图2-图5对在涡轮机机室的单件组装的过程中进行的、在轴向上相邻的第一壳体与第二壳体的轴对准及角度对准的工序进行说明。在进行该工序时,涡轮机壳体31的上半壳体31u及下半壳体31l预先相互连结而成为筒状。燃烧器壳体21的上半壳体21u及下半壳体21l也同样。在这些涡轮机壳体31和燃烧器壳体21预先设置有之前说明的第一径向基准面31r、第二径向基准面21r、第一侧倾基准面31c、第二侧倾基准面21c。
[0044]
例如,涡轮机壳体31在形成为筒状的状态下通过例如加工中心对内径进行机械加工(旋削),但此时,一并(在1次准备作业中)通过例如铣削加工等预先形成第一径向基准面31r(狭缝31x)。通过以与内径加工相同的方法形成各第一径向基准面31r,能够将全部的第一径向基准面31r高精度地形成为距涡轮机中心轴等距离。关于与第一侧倾基准面31c相关的切口31y、定位孔42,可以在涡轮机壳体31的内径加工时一并形成,但由于不要求位置精度,因此也可以通过其他工序进行机械加工。
[0045]
同样地,在对燃烧器壳体21的内径进行机械加工(旋削)时,一并(在1次准备作业中)通过例如铣削加工等形成第二径向基准面21r(狭缝21x)。通过以与内径加工相同的方法形成第二径向基准面21r,能够将全部的第二径向基准面21r高精度地形成为距涡轮机中心轴等距离。关于与第二侧倾基准面21c相关的切口21y、贯通孔41,可以在燃烧器壳体21的内径加工时一并形成,但由于不要求位置精度,因此可以通过其他工序进行机械加工。
[0046]
在涡轮机机室的单件组装时,进行上述那样分别制作出的涡轮机壳体31与燃烧器壳体21的对位(轴对准及角度对准)。例如在水平的盘面上,以在使涡轮机中心轴朝向上下的姿态下彼此的凸缘31v、21v相对的方式,在涡轮机壳体31上使用例如起重机放置燃烧器壳体21。在将燃烧器壳体21堆叠于涡轮机壳体31时,使狭缝31x、21x、切口31y、21y的周向位置大致对准。
[0047]
接着,实施燃烧器壳体21相对于涡轮机壳体31的轴对准及角度对准的工序。这些轴对准及角度对准的工序连续或并行地实施,在轴对准时也一并进行角度对准的作业。在连续进行轴对准及角度对准的工序的情况下,可以先进行任一工序。根据需要,也可以交替地重复几次轴对准和角度对准的作业。
[0048]
首先,对燃烧器壳体21相对于涡轮机壳体31的角度对准的工序进行说明。在角度对准的工序中,在利用起重机等将燃烧器壳体21向上抬起的同时,例如利用人手使燃烧器壳体21绕中心轴旋转(侧倾)以使涡轮机壳体31与燃烧器壳体21的周向的位置对准。通过像这样对燃烧器壳体21的角度进行微调整,使第一侧倾基准面31c与第二侧倾基准面21c的周向位置一致。作为此时的一个方法,例如在切口31y、21y的内部使抵接金属件m(图4)与侧倾基准面31c或21c(在图4的例子中为侧倾基准面31c)抵接。然后,利用标尺、间隙规等测定抵接金属件m与侧倾基准面21c或31c(在图4的例子中为侧倾基准面21c)的间隙g,以使间隙g
成为0的方式使燃烧器壳体21移动。由此,能够使燃烧器壳体21相对于涡轮机壳体31的角度对准。
[0049]
接着,对轴对准的工序进行说明。轴对准的工序也与角度对准的工序同样地,在利用起重机将燃烧器壳体21向上抬起的同时,例如利用人手使燃烧器壳体21沿水平方向移动(位移)以使燃烧器壳体21的中心与涡轮机壳体31的中心对准。通过像这样对燃烧器壳体21的水平方向的位置进行微调整,使第一径向基准面31r与第二径向基准面21r的位置关系在周向的全部部位相等。具体而言,作为第一径向基准面31r与第二径向基准面21r的位置关系,利用千分表等测定器具测定两者的高低差尺寸,使高低差在周向的全部部位相等。即,第一径向基准面31r与第二径向基准面21r的高低差全部成为相对于距离dr(图5)预先设定的容许值内的值。
[0050]
此时,例如若使狭缝31x或21x的宽度尺寸与保持千分表的磁铁台的宽度一致,则通过将磁铁台设置于狭缝31x或21x,也容易进行利用千分表测定的点的定位。若像这样在周向的各部位设置千分表,一边观察各千分表的测定值一边调整燃烧器壳体21的位置,则轴对准作业的效率良好。
[0051]-效果-[0052]
(1)如上所述,当使在轴向上相邻的第一壳体及第二壳体的轴对准时,在周向上设置有3组以上的第一径向基准面31r与第二径向基准面21r的组。第一径向基准面31r全部处于距涡轮机中心轴等距离的位置,第二径向基准面21r也全部处于距涡轮机中心轴等距离的位置。因此,只要调整为在3个以上的部位处第一径向基准面31r与第二径向基准面21r的位置关系相等,则能够在几何学上使第一壳体与第二壳体的中心一致。这样,根据本实施方式,在第一壳体及第二壳体的轴对准的作业中不需要专用的对准夹具。另外,由于作业容易,因此能够缩短第一壳体及第二壳体的轴对准的作业时间,能够缩短涡轮机机室的单件组装的时间。
[0053]
(2)作为第一径向基准面31r和第二径向基准面21r,理论上也考虑选择未加工的凸缘的特定部位。但是,在该情况下,除了凸缘为高精度的正圆之外,在对第一壳体及第二壳体的内径进行加工时,还要求以凸缘的外径为基准极其严格的定心精度。
[0054]
因此,在本实施方式中,在第一壳体及第二壳体的凸缘外周部设置有狭缝31x、21x,将狭缝31x、21x的内壁面设为第一径向基准面31r及第二径向基准面21r。狭缝31x、21x例如在第一壳体及第二壳体的内径加工时,能够使用加工中心等以与内径加工相同的方法一并进行机械加工。由此,能够使各第一径向基准面31r与涡轮机中心轴的距离高精度地一致。同样地,也能够使各第二径向基准面21r与涡轮机中心轴的距离高精度地一致。
[0055]
狭缝31x、21x要求第一径向基准面31r与第二径向基准面21r的距涡轮机中心轴的距离的精度,另一方面,即使位置沿着第一径向基准面31r与第二径向基准面21r稍微偏移,也不会影响功能。
[0056]
但是,只要能够得到上述的本质效果(1),则不一定需要为了形成第一径向基准面31r及第二径向基准面21r而设置狭缝31x、21x。例如,在第一壳体及第二壳体的凸缘31v、21v的外周面,在形成第一径向基准面31r及第二径向基准面21r的预定的部位预先形成突出部。而且,也可以考虑通过机械加工将该突出部的端面削落而形成第一径向基准面31r及第二径向基准面21r的方式。在该情况下,第一径向基准面31r及第二径向基准面21r位于比
凸缘31v、21v的外周面远离涡轮机中心轴的位置。
[0057]
(3)如上所述,当使在轴向上相邻的第一壳体及第二壳体的周向位置对准时,设置彼此的周向位置一致的第一侧倾基准面31c和第二侧倾基准面21c。因此,在涡轮机机室的单件组装时,通过使第一侧倾基准面31c与第二侧倾基准面21c的位置对准,从而使第一壳体与第二壳体的相对的周向位置对准。因此,根据本实施方式,在第一壳体与第二壳体的周向的对位时不需要专用的对准夹具。另外,由于作业容易,因此能够缩短第一壳体及第二壳体的周向的对位的作业时间,能够缩短涡轮机机室的单件组装的时间。
[0058]
(4)在本实施方式中,在第一壳体以及第二壳体的下半壳体31l、21l设置有与上半壳体31u、21u对置的切口31y、21y。而且,将面向这些切口31y、21y的上半壳体31u的凸缘31h1、21h1的端面设为第一侧倾基准面31c以及第二侧倾基准面21c。通过将该端面设为侧倾基准面,能够容易地确保基准位置的精度。
[0059]
另外,通过设置切口31y、21y,如前所述,能够使如图4的抵接金属件m那样具有平坦面的金属件、标尺等与侧倾基准面抵接。由此,容易测定第一侧倾基准面31c与第二侧倾基准面21c的高低差、即第一壳体与第二壳体的周向位置的偏移量。这一点也有助于第一壳体与第二壳体的角度对准的作业的容易化。
[0060]
但是,上半壳体31u、21u与下半壳体31l、21l的边界即使没有切口31y、21y也能够目视确认。因此,在以上半壳体31u、21u与下半壳体31l、21l的对置面为基准而采用的基础上,不一定需要切口31y、21y。
[0061]
另外,只要能够确保第一侧倾基准面31c与第二侧倾基准面21c的位置精度,则不一定需要将上半壳体与下半壳体的对置端面设为侧倾基准面。例如若使狭缝31x、21x的内壁面中的朝向周向的面(例如图3、图5的面n1、n2)的周向的加工位置高精度地对准,则也能够将这些面用作侧倾基准面。
[0062]
(5)另外,为了固定第一壳体与第二壳体的相对位置,在第一壳体设置定位孔42并立起定位销43,另一方面,在第二壳体设置相对于定位销43大小富余的贯通孔41。因此,在第一壳体与第二壳体的轴对准和角度对准完成后,即使贯通孔41与定位孔42的中心稍微偏离,也能够经由贯通孔41将定位销43容易地打入定位孔42。另外,在定位销43与贯通孔41之间存在间隙,在打入定位销43的时间点,定位销43与第二壳体不处于固定关系,但对定位销43嵌入衬套44并将贯通孔41与衬套44焊接。由此,定位销43被衬套44及焊接部45固定,能够将第一壳体与第二壳体在对准完成的状态下相互固定。
[0063]
通常,有时在进行了对准作业之后对第一壳体与第二壳体的彼此的凸缘进行共孔加工,将定位销打入该凸缘而将对准后的第一壳体与第二壳体固定。在该情况下,需要在对准后将第一壳体和第二壳体以堆叠的状态移载到机床,共孔加工也需要工时。
[0064]
与此相对,在本实施方式中,如上所述,贯通孔41的内径设定为相对于定位销43的外径具有富余的大小。因此,即使贯通孔41与定位孔42的中心稍微偏离,也能够通过向定位孔42打入定位销43,并在定位销43上覆盖衬套44且进行焊接,从而将第一壳体与第二壳体固定。这样,贯通孔41和定位孔42不要求严格的位置精度,因此能够在第一壳体与第二壳体的对准前预先开设。因此,在对准作业结束后,能够当场固定第一壳体与第二壳体,也不需要为了共孔加工而将第一壳体和第二壳体移载到机床。这一点也有助于涡轮机机室的单件组装的工序的缩短。