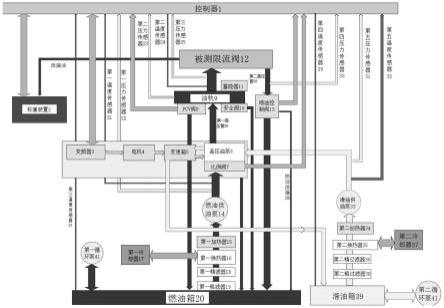
1.本发明涉及大功率船用低速柴油机共轨系统,具体涉及一种低速机共轨限流阀测试系统。
背景技术:2.随着航运业的发展,大型远洋船舶主要选用大功率二冲程低速柴油机作为船舶的主推动力。随着技术的发展,具有低排放、低油耗、运行维护方便和可靠性高等优点的智能型低速柴油机已取代原有传统低速柴油机成为市场主流产品。智能型低速柴油机的电控系统主要以电液增压电控技术与高压共轨电控技术为主要代表,其中高压共轨电控技术相较而言技术性能略高于电液增压电控技术,高压共轨电控技术的主要特点是采用了高压燃油共轨与伺服油共轨技术。
3.电控共轨燃油系统主要包括高压油泵、共轨管、电控喷油器、高压油管、循环阀、压力控制阀、安全阀、限流阀、电磁阀以及各种传感器等部件。高压油泵将低压燃油加压并送入高压油轨,高压油轨中的压力由安装于油轨上的压力传感器测量,并根据运行工况的需要由压力控制阀进行调节,高压油轨内的燃油经过限流阀、高压油管进入电控喷油器,并由电控喷油器喷入气缸。
4.限流阀安装于高压油轨上,通过高压油管连接电控喷油器。限流阀属于一种保护装置,当电控喷油器出现故障无法关闭或者高压油管出现破裂,导致瞬时流量过大时,限流阀将关闭并切断出油,当故障消除后,限流阀又可以迅速自动打开并恢复。
5.限流阀起到保护高压共轨系统避免出现电控喷油器或者高压油管故障使燃油大量泄漏而导致安全事故发生的作用。
6.对于人员与设备安全必须极度重视的情况下,在低速机高压共轨电控系统中,限流阀属于一种非常有效且必须存在的保护措施与装置,限流阀能否正常发挥其应有的作用,对柴油机极其重要,目前尚没有专门的测试系统对限流阀的性能进行测试。
技术实现要素:7.本发明的目的提供一种低速机共轨限流阀测试系统,能够检测低速机共轨限流阀的性能,判断共轨限流阀是否符合设计要求。
8.本发明的技术方案为:本发明提供了一种低速机共轨限流阀测试系统,包括:控制器1、燃油油路和对泄漏燃油进行称重的称重装置2;燃油油路包括:燃油箱20、燃油供油泵14、油轨9、高压油泵6、油轨9、被测限流阀12、喷油控制阀13、比例阀7、pcv阀8、安全阀10、蓄能器11以及对高压油泵6进行驱动的驱动系统;燃油箱20中燃油经过第一粗过滤器19和第一精过滤器18过滤后,再经过第一换热器16、第一加热器15和第一冷却器17处理后,使燃油以第一预定温度进入燃油供油泵14,燃
油供油泵14将第一预定温度的燃油供至高压油泵6,驱动系统在控制器1的控制下驱动高压油泵6以预设转速运行,再通过第一高压管26为油轨9注入高压燃油,油轨9中的高压燃油通过被测限流阀12和与被测限流阀12连接的第二高压管28进入喷油控制阀13,喷油控制阀13喷射出的燃油回流至燃油箱20中;被测限流阀12的泄漏燃油通过泄漏油管连接至称重装置2,称重装置2与控制器1连接;比例阀7步骤在燃油供油泵14和高压油泵6之间,比例阀7与控制器1连接;油轨9通过pcv阀8和安全阀10分别连接至燃油箱20,pcv阀8与控制器1连接;油轨9和蓄能器11连接;控制器1通过布置在被测限流阀12之前的第三压力传感器25和布置在被测限流阀12之后的第四压力传感器30所检测到的压力数据,测试被测限流阀12的压力变化是否满足预设压力变化要求;控制器1通过控制喷油控制阀13不喷油,使被测限流阀12模拟在柴油机上的静态不工作状态,控制器1通过称重装置2对被测限流阀处于静态不工作状态时所检测到的燃油泄漏量,测试是否满足第一预设泄漏要求;控制器1通过控制喷油控制阀13进行正常喷油,使被测限流阀12模拟在柴油机上的动态工作状态,控制器1通过称重装置2对被测限流阀处于动态工作状态时所检测到的燃油泄漏量,测试是否满足第二预设泄漏要求;控制器1通过控制喷油控制阀13进入故障模式,实现对被测限流阀12出现瞬时大量泄油是否具有自行关闭的能力进行测试,以及通过控制喷油控制阀13由故障模式转为关闭状态,实现对被测限流阀12在导致其自行关闭的故障解决后是否具有自行复位的能力进行测试。
9.优选地,所述低速机共轨限流阀测试系统还包括: 滑油油路;滑油油路包括:滑油箱39和滑油供油泵33;滑油箱39中滑油通过第二粗过滤器38和第二精过滤器36过滤后,再经过第二换热器35、第二加热器36和第二冷却器37处理后,使滑油以第二预设温度进入滑油供油泵33,滑油供油泵33将第二预定温度的滑油泵入高压油泵6,完成对高压油泵6润滑后的滑油再进入驱动系统为其润滑,后回流至滑油箱29。
10.优选地,控制器1通过燃油箱20中布置的第三温度传感器27、燃油供油泵14之后布置的第一温度传感器21和被测限流阀12之前布置的第二温度传感器24收集的温度数据,来控制第一加热器15、第一换热器16和第一冷却器17的工作状态;控制器1通过滑油箱29中布置的第四温度传感器29和滑油供油泵33之后布置的第五温度传感器32收集的温度数据,来控制第二加热器34、第二换热器35和第二冷却器37的工作状态;控制器1通过在滑油供油泵33后布置的第五压力传感器31收集滑油供油泵33泵出的滑油压力数据;控制器1通过在燃油供油泵14后布置的第一压力传感器22收集燃油喷射泵14泵出的燃油压力数据;控制器1通过在油轨9中布置的第二压力传感器23收集油轨9中的高压燃油压力数
据,来对比例阀7和pcv阀8进行开闭控制,以调节油轨9中的高压燃油压力。
11.优选地,驱动系统包括:变频器3、电机4、变速箱5;变频器3与控制器1连接;控制器1控制变频器3带动电机4运行,电机4输出的动力通过变速箱5带动高压油泵6以预设转速运行;完成对高压油泵6润滑的滑油通过油管进入变速箱5为其润滑,后再通过油管回流至滑油箱29。
12.优选地,通过第一循环泵40实现燃油箱20中的燃油处于循环状态;通过第二循环泵41实现滑油箱39中的滑油处于循环状态。
13.优选地,在第二压力传感器23采集到的油轨9中的高压燃油压力超过预设的最大燃油压力时,控制器1控制变频器3使电机4停止运行。
14.优选地,在第四温度传感器29和第五温度传感器32采集的温度均高于各自对应的最大预设滑油温度时,控制器1控制变频器3使电机4停止运行;在第三温度传感器27和第一温度传感器21采集的温度均高于各自对应的最大预设燃油温度时,控制器1控制变频器3使电机4停止运行。
15.优选地,控制器1控制喷油控制器13不喷油时,被测限流阀12不动作,控制器1通过控制比例阀7和pcv阀8的开度,实现油轨9中的压力稳定在第一预设轨压要求范围内,比例阀7和pcv阀8的回油均通过油管回流至燃油箱20中;控制器1控制喷油控制器13正常喷油时,喷油控制阀13每喷一次油,被测限流阀12动作一次,控制器1通过控制比例阀7和pcv阀8的开度,实现油轨9中的压力稳定在第二预设轨压要求范围内,比例阀7和pcv阀8的回油均通过油管回流至燃油箱20中。
16.优选地,控制器1通过控制喷油控制阀13延长喷油持续期而进入故障模式,使被测限流阀12的容积腔中燃油全部喷出;在被测限流阀12的容积腔的体积小于喷油控制阀13的单次喷射量时,测试是否被测限流阀12自行关闭;若确定被测限流阀12自行关闭,控制器1控制喷油控制阀13关闭,被测限流阀12的容积腔中的高压燃油通过节流孔缓慢进入被测限流阀12和喷油控制阀13之间的第二高压管28中,使第二高压管28中的燃油压力逐渐升高;在第二高压管28中的燃油压力逐渐升高至使被测限流阀12的燃油活塞后的作用力大于油轨9中的燃油压力对被测限流阀12的燃油活塞的作用力时,测试被测限流阀12是否自行复位。
17.本发明的有益效果为:本发明所述低速机共轨限流阀测试系统,能够通过控制器的控制,模拟被测限流阀在柴油机上的运行状态,检测被测限流阀在各种不同共轨压力、不同喷射频率等工况下工作是否正常,检测被测限流阀阀前与阀后的压力变化,检测被测限流阀在紧急状态下能否发挥切断共轨中燃油输出的作用,测试被测限流阀在系统故障解除后自行复位恢复的功能是否正常,以及检测被测限流阀在各种状态下的内部泄漏情况,以此判断被测限流阀是否属于合格产品,并自动生成报告。
18.本发明所述低速机共轨限流阀测试系统,通过对限流阀的性能测试,极大程度上保证限流阀的合格性,对于柴油机在使用中的设备与人员的安全性提供了有力的保障。
附图说明
19.图1为本发明测试系统的原理结构图;其中,1-控制器、2-称重装置、3-变频器、4-电机、5-变速箱、6-高压油泵、7-比例阀、8-pcv阀、9-油轨、10-安全阀、11-蓄能器、12-被测限流阀、13-喷油控制阀、14-燃油供油泵、15-第一加热器、16-第一换热器、17-第一冷却器、18-第一精滤器、19-第一粗滤器、20-燃油箱、21-第一温度传感器、22-第一压力传感器、23-第二压力传感器、24-第二温度传感器、25-第三压力传感器、26-第一高压管、27-第三温度传感器、28-第二高压管、29-第四温度传感器、30-第四压力传感器、31-第五压力传感器、32-第五温度传感器、33-滑油供油泵、34-第二加热器、35-第二换热器、37-第二冷却器、36-第二精滤器、38-第二粗滤器、39-滑油箱、40-第一循环泵、41-第二循环泵。
具体实施方式
20.下面结合附图对本发明作详细说明。
21.参见图1所示,本实施例提供了一种低速机共轨限流阀测试系统,该系统包括:第一循环泵40,第二循环泵41,燃油供油泵14,高压油泵6,油轨9、喷油控制阀,称重装置2,燃油箱20,滑油箱39,第一高压管26,第二高压管28,pcv阀8,安全阀10、变速箱5、电机4、变频器3、控制器1、第一粗滤器19、第二粗滤器38、第一换热器16、第二换热器35、第一加热器15、第二加热器35、第一冷却器17、第二冷却器37、第一至第五温度传感器21、24、27、29、32、第一至第五压力传感器22、23、25、30、31、被测限流阀12以及各部件之间的连接管线等。
22.所述燃油箱20通过第二循环泵41保证油箱中燃油处于循环状态。燃油箱20中燃油经过第一粗滤器19粗滤与第一精滤器18精滤后,并经过第一加热器15、第一换热器16、第一冷却器17的处理使燃油以合适的温度进入燃油供油泵14,换热介质为水或者其他液体,并通过燃油供油泵14将燃油以低压通过油管供至高压油泵6。控制器1根据控制变频器3带动电机4运行,通过变速箱5带动高压油泵6以要求的转速运行,通过第一高压管26为油轨9中注入高压燃油。油轨9中高压燃油通过被测限流阀12与第二高压管28进入喷油控制阀13,被测限流阀12泄漏油管与2称重装置2连接。
23.滑油箱39中滑油通过第一循环泵40保持循环,滑油通过第二粗滤器38粗滤与第二精滤器36精滤,并经过第二加热器34、第二换热器35、第二冷却器37的作用,以适宜的温度进入高压油泵6并对其进行润滑作用,完成润滑高压油泵6的滑油进入变速箱5,亦可对变速箱5进行润滑,然后滑油通过油管回流进入滑油箱39。
24.控制器1通过燃油箱20的第三温度传感器27、燃油供油泵14后第一温度传感器21、被测限流阀12之前的第二温度传感器24收集温度数据,经过计算后来控制第一加热器15、第一换热器16与第一冷却器17的工作,以使燃油供油泵14后、燃油箱20与待测被测限流阀12前的温度符合要求,当燃油箱20的第三温度传感器27或者燃油供油泵14后第一温度传感器21反馈的温度超出限值,控制器1即控制变频器3使电机4停止运行,防止高压油泵6咬卡。
25.控制器1通过滑油箱39的第四温度传感器29与滑油供油泵33后第五温度传感器32收集温度数据,经过计算后来控制第二加热器34、第二换热器35与第二冷却器37的工作,以使滑油供油泵33后与滑油箱39的温度符合要求,当滑油供油泵33后与滑油箱39的温度超出限值,控制器1即控制变频器3使电机4停止运行,防止高压油泵6咬卡。
26.控制器1通过布置在被测限流阀12之前的第三压力传感器25和布置在被测限流阀12之后的第四压力传感器30所检测到的压力数据,测试被测限流阀12的压力变化是否满足预设压力变化要求。
27.控制器1通过在滑油供油泵33后布置的第五压力传感器31收集滑油供油泵33泵出的滑油压力数据;控制器1通过在燃油供油泵14后布置的第一压力传感器22收集燃油喷射泵14泵出的燃油压力数据;控制器1通过在油轨9中布置的第二压力传感器23收集油轨9中的高压燃油压力数据,来对比例阀7和pcv阀8进行开闭控制,以调节油轨9中的高压燃油压力。
28.安全阀10安装于油轨9上,当油轨9轨压超过一定范围时(比例阀7与pcv阀8控制失效,无法控制轨压),安全阀10打开,通过油管将油泄入燃油箱20,使油轨9中的压力避免过高。当比例阀7与pcv阀8控制失效,且安全阀10也失效,轨压超过设定上限值时,控制器1将控制变频器3控制电机4停止运行。最后还可以通过紧急停机按钮使测试系统断电而停止运行。
29.油轨9中高压燃油通过被测限流阀12与第二高压管28进入喷油控制阀13。
30.当控制器1控制喷油控制阀13不喷油时,被测限流阀12不动作,控制器1通过程序计算控制比例阀7与pcv阀8的开度,实现油轨9中的压力稳定在第一预设轨压要求范围内,同时比例阀7与pcv阀8的回油均通过油管进入燃油箱20,此时可以测量被测限流阀12静态时的燃油通过间隙的泄漏量,通过2称重装置2检测泄漏量。
31.当控制器1控制喷油控制阀13正常工作时,其每喷一次油,被测限流阀12即动作一次,控制器1通过程序计算控制比例阀7与pcv阀8的开度,以及利用蓄能器11的作用,实现油轨 9中的压力稳定在第二预设轨压要求范围内,同时比例阀7与pcv阀8的回油均通过油管进入燃油箱20,此时可以测量被测限流阀12动态时的燃油通过间隙的泄漏量,通过2称重装置2检测泄漏量。
32.当控制器1控制喷油控制阀13延长喷油持续期,使被测限流阀12的容积腔中燃油全部喷出,容积腔的体积小于喷油控制阀13的单次喷射量,此时被测限流阀12即处于关闭状态。此时通过控制器1控制喷油控制阀13关闭,燃油将通过被测限流阀12的极小的节流孔缓慢进入被测限流阀12与喷油控制阀13之间的第二高压管28,并使第二高压管28中的压力逐渐升高,当压力升高到一定程度后被测限流阀12燃油活塞后的作用力大于油轨9中油压对燃油活塞的作用力,被测限流阀12中的燃油活塞将被推开并复位。
33.通过控制器1控制喷油控制阀13的工作,模拟实现被测限流阀12在柴油机上的工作状态,以及在被测限流阀12后出现故障瞬时大量泄油,影响柴油机使用安全的情况下被测限流阀12自行切断供油,并在瞬时大量泄漏解决后其自行恢复打开的能力。通过本测试系统的测试,可以验证被测限流阀12是否符合设计要求,同时被测限流阀12测试完成后可自动生成测试报告。
34.本发明的工作原理为:燃油箱20中的燃油经过第一加热器15、第一换热器16、第一冷却器17、第一精滤器18、第一粗滤器19进入燃油供油泵14以较低压力进入比例阀7与高压油泵6,控制器1根据控制变频器3带动电机4运行,通过变速箱5带动高压油泵6运行,通过第一高压管26为油轨9中注入高压燃油,油轨9中高压燃油通过被测限流阀12与第二高压管28进入喷油控制阀13。滑
油箱39中滑油通过第二粗滤器38、第二精滤器36、第二加热器34、第二换热器35、第二冷却器37的进入高压油泵6对其进行润滑,滑油回油进入变速箱5对变速箱5进行润滑,然后滑油通过油管回流进入滑油箱39。
35.当系统中轨压(900bar)、温度(限流阀前温度40-45℃)达到试验要求后,控制器1控制喷油控制阀13正常运行,当喷油控制阀13的喷油持续器延长到一定程度后单次喷油量超过被测限流阀12最大容积,被测限流阀12关闭,此时切断喷油控制阀13停止喷油,燃油将通过被测限流阀12的极小的节流孔缓慢进入被测限流阀12与喷油控制阀13之间的第二高压管28,并使第二高压管28中的压力逐渐升高,当压力升高到一定程度后被测限流阀12燃油活塞后的作用力大于油轨9中油压对燃油活塞的作用力,被测限流阀12中的燃油活塞将被推开并复位。
36.本发明的工作流程为:步骤一:装配与检查,安装待测被测限流阀12,检查各部件的连接。
37.步骤二:启动试验台,运行测试软件,启动“燃油供油”与“滑油供油”,输入被测限流阀12、测试员、日期等信息。
38.步骤三:点击测试软件中“试验启动”选项,将高压油泵6转速调整至设定转速,并等待系统温度达到要求,同时观察测试软件界面是否有报警项目。
39.步骤四:逐步进行“试验一”、“试验二”、“试验三”等,模拟不同轨压与喷射频率下系统中的压力变化情况,按照要求,每种状态下运行一定时间,软件自动记录数据,同时可由2称重装置2记录限流阀的泄漏情况。
40.步骤五:点击“复位试验”,被测限流阀12切断燃油输出并在一段时间后复位打开,记录时间与系统压力变化情况。
41.步骤六:点击“试验归零”,调整高压油泵转速至0,点击关闭“燃油供油”与“滑油供油”,点击“报告生成”,生成报告。
42.步骤七:关闭试验台或者更换限流阀后重复前述步骤。
43.本发明测试系统用电、液位、温度、压力,防爆门等均设有监控并反馈到控制器1中,可在试验台自带工控机上操作也可连接电脑远程操作。
44.本发明测试系统内高压通过强度校核等,可承受150mpa以上测试压力,零部件防爆等级满足要求。
45.本发明测试系统设置有多重安全措施,超压会自动泄压乃至停机,不存在超压危险。