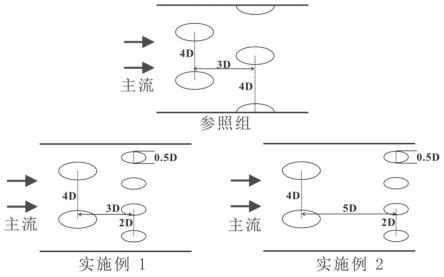
1.本发明属于燃气轮机高温涡轮叶片冷却技术领域,具体涉及一种组合式气膜孔及涡轮叶片。
背景技术:2.燃气轮机作为一种热动力装置,凭借体积小、功率大、高效、清洁、经济性好等优点,被广泛应用于舰船动力、陆上发电、工业驱动以及分布式供能等领域,特别是航空航天领域,在国民经济和国防安全中都起着重要的作用。提高涡轮前进口燃气温度是提升燃气轮机热效率和输出功率的最直接方法。目前,地面重型燃机和大推力航空发动机的透平进口温度已远超叶片合金材料的耐温极限。现代先进航空发动机的涡轮前进口燃气温度已高达2000k,远远超过了制造涡轮叶片高温材料的熔点。高温会降低航空发动机的使用寿命、稳定性和安全性,因此,发展高效的涡轮叶片冷却技术对提升燃气轮机性能极为重要。
3.常见的叶片冷却方式有气膜冷却、对流冷却等,其中气膜冷却技术为主要的外部冷却方式,其工作原理为叶片内部冷却通道中的冷气通过离散气膜孔流出而在主流作用下覆盖在叶片表面,形成一层贴附壁面的冷气膜,使叶片表面和高温主流相隔绝,从而达到降低叶片表面温度的目的。气膜冷却在有效降低涡轮叶片表面温度和热应力方面发挥着重要作用,对其进行持续而深入的研究是提高航空发动机性能的重要途径。
4.经过对现有技术文献的检索发现,国内外技术人员为提升气膜冷却效率提出了大量的结构或孔型,主要包括异形孔、在孔出口附近添加槽结构或突片、在孔上游或下游添加涡发生器。现有技术有采用展向扩张流向收缩的异形孔,以削弱气膜与主流的掺混作用并扩展气膜覆盖面积;还有通过在气膜孔出口上游布置楔形的涡发生器以削弱气膜与主流的掺混作用。
5.上述方法因其结构复杂,增加了加工难度,且削弱了叶片的力学和气动性能。目前气膜冷却中最常用的孔型仍然是圆柱孔,其具有结构简单、强度高、热应力小、加工方便等优点,但是,目前常见的圆柱孔排布方式存在着气膜冷却效率偏低、冷气覆盖面积小、不适于高吹风比等劣势。
技术实现要素:6.要解决的技术问题:
7.为了避免现有技术的不足之处,本发明提供一种组合式气膜孔及其在涡轮叶片的应用,该组合式气膜孔具有高气膜冷却效率和整体热性能;提升了涡轮叶片整体的气动和力学性能。
8.本发明的技术方案是:一种组合式气膜孔,包括双排气膜孔,第一排气膜孔包括多个直径为d、长度为l的第一圆柱孔,第二排气膜孔包括多个直径为0.5d、长度为l的第二圆柱孔;所述第一圆柱孔和第二圆柱孔的轴向与叶片表面之间的夹角为α;
9.所述第一排气膜孔和第二排气膜孔呈交错排列,即第一排气膜孔的第一圆柱孔中
点位于第二排气膜孔中相邻两个第二圆柱孔中点连线的中心线上。
10.本发明的进一步技术方案是:所述第一圆柱孔的直径d为0.2-1mm,长度l为0.2-10mm,倾斜角α为20
°‑
45
°
。
11.本发明的进一步技术方案是:所述第一排气膜孔中相邻第一圆柱孔的展向间距p为3-5d。
12.本发明的进一步技术方案是:所述第二排气膜孔中相邻圆柱孔的展向间距为第一排气膜中相邻圆柱孔展向间距的一半,即1.5-2.5d。
13.本发明的进一步技术方案是:所述第一排气膜孔与第二排气膜孔的流向距离s为3-5d。
14.一种涡轮叶片,所述叶片表面设置有一组或多组组合式气膜孔,所述组合式气膜孔中圆柱孔轴向与叶片表面之间的夹角α根据所处叶片位置和厚度调整。
15.本发明的进一步技术方案是:所述多组组合式气膜孔在叶片上按周期排布,相邻组之间的流向距离根据叶片热负荷调整。
16.本发明的进一步技术方案是:所述叶片的压力面或吸力面上成周期性排布有多组组合式气膜孔,用于叶片的气膜冷却,适用吹风比m为0.5-1.5。
17.有益效果
18.本发明的有益效果在于:
19.1、本发明基于圆柱形气膜孔提出,具有良好的力学性能和气动性能,其相对复杂的异形孔或辅助结构有较低的加工难度和更高的加工精度。
20.2、本发明通过第一排孔与第二排孔中相邻孔的组合,构成组合孔结构,每个组合孔结构中各孔射流产生的肾形涡对相互影响并构筑了反肾形涡结构,削弱了肾形涡对的强度和尺度,最终提升了冷气膜的贴附性和覆盖宽度,提升了整体气膜冷却效率。
21.3、本发明在提升或保持气膜冷却效率的同时大幅降低了冷气用量,且较小的气膜孔径使叶片整体强度提升,提升了叶片整体的气动和力学性能。具体提升效果可参考后文中具体实施例的工作效果。
22.本发明的设计要点是利用组合孔的概念,同时改变气膜孔孔径和气膜孔排布,现有研究中一般只考虑了气膜孔的排布。气膜孔设计参数的限定是为了让第一排和第二排孔产生的肾形涡对能有效的相互削弱,展向距离改变影响涡对的重叠率,流向距离影响涡对的强度和耗散程度;在使用简单圆柱形气膜孔获得更高的气膜冷却效率的同时,还要降低冷气用量。
23.根据实施例可知,本发明提出的利用组合孔的新型气膜孔排布方式可以有效抑制圆柱形孔在高吹风比下易吹离的有害特性,在降低冷气用量的同时提升整体冷却性能。
附图说明
24.图1是本发明所适用的冷却模型及布置位置示意图;
25.图2是本发明实施例1、实施例2和参照组的气膜孔分布示意图;
26.图3是通过数值模拟得到的本发明实施例1、实施例2和参照组的平均气膜冷却效率及冷气质量流量的对比图;
27.图4是通过数值模拟得到的本发明实施例1、实施例2和参照组的气膜冷却效率分
布云图;
28.附图标记说明:d.气膜孔直径,η.气膜冷却效率,mfr.冷气质量流量,m.吹风比,x.流向,y.展向。
具体实施方式
29.下面通过参考附图描述的实施例是示例性的,旨在用于解释本发明,而不能理解为对本发明的限制。
30.在本发明的描述中,需要理解的是,术语“中心”、“纵向”、“横向”、“长度”、“宽度”、“厚度”、“上”、“下”、“前”、“后”、“左”、“右”、“竖直”、“水平”、“顶”、“底”、“内”、“外”、“顺时针”、“逆时针”等指示的方位或位置关系为基于附图所示的方位或位置关系,仅是为了便于描述本发明和简化描述,而不是指示或暗示所指的装置或元件必须具有特定的方位、以特定的方位构造和操作,因此不能理解为对本发明的限制。
31.本发明提供了一种可用于燃气轮机叶片冷却的新型气膜孔排布方式,该排布方式以双排气膜孔为一个基础单元,可在叶片压力面和吸力面上布置一组或多组该基础单元。双排孔中的第一排孔中的圆柱孔直径为d,长度为l,倾斜角为α。双排孔中的第二排孔中的圆柱孔直径为0.5d,长度与倾斜角不变。两排孔中第一排孔的展向间距p为3-5d,第二排孔的展向间距为第一排孔展向间距的一半,即1.5-2.5d。双排孔之间的流向距离s为3-5d。第一排孔与第二排孔呈交错排列,即第一排孔中每个孔的孔中心与下游第二排孔中两相邻孔的孔中心连线中点具有相同的展向位置。
32.图1为本发明所适用的冷却模型及布置位置示意图,该气膜冷却方式适用于燃气轮机或航空发动机静叶及动叶。冷却气由内部冷却方式提供,图中冷气腔仅为示意,之后冷气由气膜孔射入主流,在叶片表面形成一层贴附于壁面的冷气膜,隔绝和降低高温燃气对叶片表面的烧蚀和加热。本发明可布置于叶片压力面和吸力面。
33.图2为本发明实施例1和2及参照组的结构示意图。参照组为航空发动机叶片上常用的双排错排气膜孔,气膜孔直径为d,倾斜角为α,气膜孔的展向间距为4d,孔排间的流向间距为3d。实施例1中第一排孔的几何参数与参照组一致,气膜孔直径为d,倾斜角为α,气膜孔的展向间距为4d。第二排孔直径为0.5d,倾斜角为α,气膜孔的展向间距为2d。两排孔之间的流向间距为3d。第一排孔与第二排孔呈交错排列,即第一排孔中每个孔的孔中心与下游第二排孔中两相邻孔的孔中心连线中点具有相同的展向位置。这三个孔构成一个组合孔结构。实施例2中两排气膜孔的几何参数与实施例1中的两排气膜孔一致,但两排孔的流向间距改为5d。
34.图3为通过数值模拟得到的本发明实施例1和2与对应的参照组在吹风比为0.5和1.0时的平均气膜冷却效率和冷气质量流量对比图。可见,由于本发明中第二排孔的孔径仅为参照组的一半,在相同冷却面积上的冷气质量流量降低,同等吹风比下整体冷气用量降低了25%。与此同时,在吹风比为0.5时,实施例1和2的表面气膜冷却效率与参照组几乎一样,且实施例1相较参照组有少量提升;在吹风比为1.0时,实施例1和2的表面气膜冷却效率均高于参照组,实施例1和2的气膜冷却效率相较参照组分别提升24.2%和12.7%。
35.图4为通过数值模拟得到的本发明实施例1和2与对应的参照组在吹风比为0.5和1.0时的气膜冷却效率云图。可知,在吹风比为0.5和1.0时,传统气膜孔排布方式中相邻气
膜孔射出的冷气各自工作,仅能覆盖孔下游区域,气膜覆盖宽度较窄,且随吹风比增大气膜吹离现象加剧,导致气膜冷却效率下降。而本发明实施例1和2中,第一排气膜孔与下游相邻第二排气膜孔组成组合孔冷却结构,如图中白色线框所示。组合孔中上游射流形成的肾形涡对与下游射流形成的肾形涡对相互影响并最终削弱,提升了气膜的贴附性并扩宽了气膜覆盖面积,与参照组相比取得了更好的整体气膜冷却效率。
36.上述结果表明,本发明提出的利用组合孔的新型气膜孔排布方式可以有效抑制圆柱形孔在高吹风比下易吹离的有害特性,在降低冷气用量的同时提升整体冷却性能。
37.尽管上面已经示出和描述了本发明的实施例,可以理解的是,上述实施例是示例性的,不能理解为对本发明的限制,本领域的普通技术人员在不脱离本发明的原理和宗旨的情况下在本发明的范围内可以对上述实施例进行变化、修改、替换和变型。