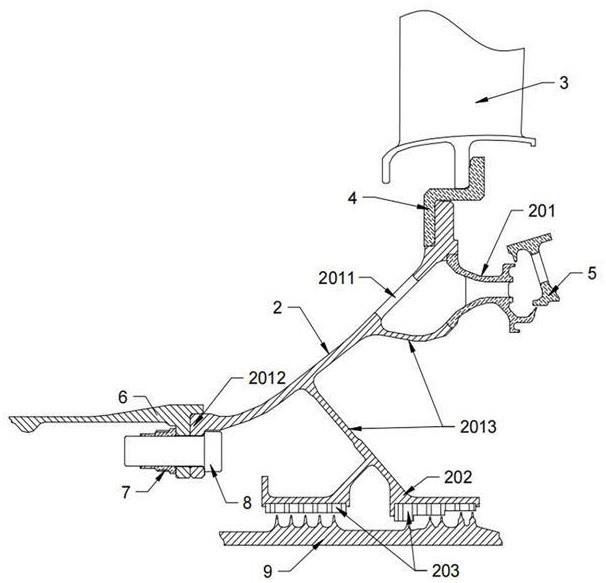
1.本发明涉及航空发动机静子部件承力结构领域,公开了一种鸟类骨架仿生式承力结构及其设计方法。
背景技术:2.承力结构是用于传递发动机内部载荷的刚性结构件,承力结构设计是发动机结构设计重要组成部分,很大程度上影响着发动机的推重比、可靠性、安全性等。其中静子的承力结构主要承受较高的温度载荷、内压并且要传递静子叶片的轴向力、扭矩及振动负荷。承力结构刚度不足会在工作时发生变形,影响转静子之间的间隙,严重时会使转静子发生碰磨。
3.现有承力结构设计方法较为单一,通常根据流道形状简化为线性结构,直接连接至其他零组件,其厚度为简单线性过渡,所以为了保证该承力结构拥有足够的刚/强度,通常壁厚设计较厚导致质量增加;并且由于结构简单,应力分布不均匀,通常伴随变形不协调的问题。同时,承力机匣上还会设有不同安装边用于连接其他功能件,进一步恶化承力机匣的重量属性,严重影响发动机推重比。因此,提高承力结构的刚/强度和降低承力结构的重量成为一组天然的矛盾,如何平衡两者关系成为承力结构设计的关键。
4.近年来,仿生设计为创造新型结构及功能材料提供了新的方法和途径,仿生结构具备接近生物体的优异特性。经研究,鸟类经过长期生物进化后,其骨架结构与功能已达到近乎完美的程度,结构当量刚度很高。鸟类负载后对空中飞行姿态和着陆影响较小,该特征满足承力结构在多种工况变形控制需求。并且鸟类为便于飞行,整个骨架重量很轻,该特征满足承力结构重量控制需求。同时,研究人员对鸟类后肢骨骼组合的长度比例及其机理初步分析,鸟类骨架尺寸对承力结构材料分布具有指导意义。如何针对承力结构的力学特征,通过仿生设计原理寻求一种固有抗变形、复杂载荷抗变形能力强,质量轻的承力结构,成为研究人员研究的新课题。
技术实现要素:5.本发明的目的在于提供一种鸟类骨架仿生式承力结构及其设计方法,采用鸟类仿生式承力结构,承力骨架、人字环组件和预旋喷嘴形成空间网格骨骼分布,承力骨架采用鸟类骨架仿生结构的变厚度承力骨架,使承力结构省去大量利用率极低材料,整体材料分布更加合理,在满足整体刚度/强度需求的同时,承力结构重量较传统连接极大降低。
6.为了实现上述技术效果,本发明采用的技术方案是:一种鸟类骨架仿生式承力结构,所述承力结构是以航空发动机中心线为回转轴的回转结构,其回转截面包括承力骨架、预旋喷嘴、人字环组件,所述承力骨架为承力脊椎骨架仿生,用于与燃烧室内机匣、叶片内支撑环固定连接;所述预旋喷嘴为鸟类头骨仿生,用于涡轮转子提供冷气,同时与转子挡板形成密封结构;所述人字环组件为后肢骨骼仿生,用于与转子轴形成封严副。
7.进一步地,预旋喷嘴靠近转子挡板的一端设置有篦齿,通过篦齿与转子挡板形成密封结构。
8.进一步地,人字环组件在与转子轴相邻的的位置设置有蜂窝密封组件。
9.为实现上述技术效果,本发明还提供了一种鸟类骨架仿生式承力结构的设计方法,包括如下步骤:s1、以航空发动机中心线为回转轴,分别将叶片安装截面半径、燃烧室机匣截面半径位置确定为承力骨架回转截面拟合线的起点和终点;s2、根据燃烧室火焰筒流道形状延伸曲线,确定承力骨架流道拟合点,将起点、拟合点、终点平滑连接形成承力骨架的拟合线;s3、基于承力骨架的拟合线,根据承力载荷初步分布承力骨架厚度,获得变厚度承力骨架;s4、根据转子结构确定预旋喷嘴位置和人字环组件位置,在变厚度承力骨架上确定预旋喷嘴和人字环组件的连接节点,由连接节点向对应的预旋喷嘴和人字环组件引出连接支架。
10.进一步地,步骤s4中由连接节点向封严副引出连接支架为鸟类后肢骨骼仿生的人字环组件。
11.进一步地,步骤s2中承力骨架流道拟合点的确定方法为:绘制b样条曲线连接起点和终点,所述b样条曲线与燃烧室机匣流道曲线一阶连续,在b样条曲线均匀确定n个拟合点;其中,,l
弦长
为起点和终点之间的直线距离。
12.进一步地,步骤s2中b样条曲线的曲率与火焰筒流道曲率在相差
±
15%以内。
13.进一步地,步骤s2中采用直线将起点、拟合点、终点依次连接,各连接处采用r5~r10平滑连接。
14.进一步地,步骤s3中分别在起点或终点位置设置与燃烧室机匣、叶片内支撑环相匹配的安装组件。
15.进一步地,步骤s3中变厚度承力骨架的厚度t分布为:流道段厚度最小值t
min
≥2.5mm;连接节点位置:t=1.5t
min
。
16.与现有技术相比,本发明所具备的有益效果是:1、本发明采用鸟类仿生式承力结构,承力骨架、人字环组件和预旋喷嘴形成空间网格骨骼分布,承力骨架采用鸟类骨架仿生结构的变厚度承力骨架,使承力结构省去大量利用率极低材料,整体材料分布更加合理,在满足整体刚度/强度需求的同时,承力结构重量较传统连接极大降低。
17.2、承力骨架与预旋喷嘴、封严副的连接节点位置位于鸟类骨骼承力点,模拟鸟类骨架传力方式,承力结构全工况整体框架抗变形能力强,转、静子间隙保持能力更强。
18.3、通过结构设计,预旋喷嘴和人字环组件在满足空气流路封严要求的同时,提高承力框架整体刚度和抗变形能力,叶片通过承力骨架传力至燃烧室机匣,传力可靠。
附图说明
19.图1为实施例1或2中的鸟类骨架仿生结构示意图;图2为实施例1或2中鸟类骨架仿生式承力结构及其安装结构示意图;图3是实施例2中变厚度承力骨架结构示意图;图4为实施例2中预旋喷嘴的结构示意图;图5为实施例2中人字环组件结构示意图;其中,1、鸟类骨架仿生;101、承力脊椎骨架仿生;102、头骨仿生;103、后肢骨骼仿生;2、承力骨架;201、预旋喷嘴;202、人字环组件;203、蜂窝密封组件;2011、进气口;2012、起点;2013、连接支架;3、涡轮静子叶片;4、叶片内支撑环;5、转子挡板;6、燃烧室机匣;7、螺母;8、d头螺栓;9、转子轴。
具体实施方式
20.下面结合实施例及附图对本发明作进一步的详细描述。但不应将此理解为本发明上述主题的范围仅限于以下的实施例,凡基于本发明内容所实现的技术均属于本发明的范围。
21.实施例1参见图1和图2,一种鸟类骨架仿生式承力结构,承力结构是以航空发动机中心线为回转轴的回转结构,其回转截面包括承力骨架2、预旋喷嘴201、人字环组件202,承力骨架2为承力脊椎骨架仿生101,用于与燃烧室机匣6、叶片内支撑环4固定连接;预旋喷嘴201为鸟类头骨仿生102,用于与转子挡板5形成密封结构;人字环组件202为后肢骨骼仿生103,用于与转子轴9形成封严副。
22.在本实施例中,承力结构回转截面采用鸟类仿生式,采用曲线拟合形成,根据承力载荷分布设计为变厚度承力骨,由“厚骨节”承力,“骨体”进行支撑,使得承力结构整体性良好,力学分布合理,其当量刚度/强度明显提高。
23.此外,承力骨架2、人字环组件202和预旋喷嘴201形成空间网格骨骼分布,使承力结构省去大量利用率极低材料,整体材料分布更加合理,在满足整体刚度/强度需求的同时,承力结构重量较传统连接极大降低。
24.预旋喷嘴201为鸟类头骨仿生102,人字环组件202为后肢骨骼仿生103,形成模拟鸟类骨架传力方式;预旋喷嘴201位于承力骨架2上侧靠近叶片一端,与承力骨架2、及连接预旋喷嘴201的连接支架2013形成仿头骨型空腔,近似为橄榄形的整环,整体刚性良好。为减少气体流阻,内部光滑过渡。人字环组件202由其在承力骨架2上的连接节点向右下延伸,呈三角分布,稳定性好,支撑刚度强。本实施例中的预旋喷嘴201、封严副位置位于鸟类骨骼承力点,使得承力结构全工况整体框架抗变形能力强,转、静子间隙保持能力更强。
25.实施例2参见图1-图5,本实施例以某一型号的航空发动机静子的承力结构设计流程为例,对本发明的结构和设计方法进行详细说明,具体结构和设计步骤如下:1)结构简介如图1所示为本实施例中设计的仿生式结构,鸟类骨架仿生1由承力脊椎骨架仿生101,头骨仿生102,后肢骨骼仿生103组成,各组成部分可根据涡轮静子部件功能需求衍化
为功能性零件。
26.如图2所示,以图1中鸟类骨架仿生1承力框架结构为基础,根据对应的涡轮静子部件功能需求衍化:承力脊椎骨架仿生101衍化为承力骨架2,头骨仿生102衍化为预旋喷嘴201,预旋喷嘴201与承力骨架2形成仿头骨型空腔,位于整个承力结构右端;后肢骨骼仿生103衍化为用于与转子轴9形成封严副的人字环组件202,各零件通过焊接方式连接。人字环组件202与变厚度承力骨架2垂直向右下延伸,各零件呈三角分布。
27.2)设计流程:s1、以航空发动机中心线为回转轴,分别将叶片安装截面半径、燃烧室机匣6截面半径位置确定为承力骨架2回转截面拟合线的起点2012和终点;s2、根据燃烧室火焰筒流道形状延伸曲线,确定承力骨架2流道拟合点,将起点2012、拟合点、终点平滑连接形成承力骨架2的拟合线;本实施例中采用直线将起点2012、拟合点、终点依次连接,各连接处采用r5~r10平滑连接。
28.承力骨架2流道拟合点的确定方法为:绘制b样条曲线(b-spline curve)连接起点2012和终点,使b样条曲线与燃烧室机匣6流道曲线一阶连续,在b样条曲线均匀确定n个拟合点;其中,,l
弦长
为起点和终点之间的直线距离。b样条曲线的曲率与火焰筒流道曲率在相差
±
15%以内。
29.s3、基于承力骨架2的拟合线,根据承力载荷初步分布承力骨架2厚度,获得变厚度承力骨架2;本实施例中变厚度承力骨架2的厚度t分布为:流道段厚度最小值t
min
≥2.5mm;与连接支架2013对应的连接节点位置厚度t=1.5t
min
。
30.为实现承力骨架2与燃烧室机匣6、叶片内支撑环4的固定连接,本实施例中在起点2012位置设置与燃烧室机匣6相匹配的安装组件,在终点位置设置与叶片内支撑环4相匹配的安装组件。
31.s4、根据转子结构确定预旋喷嘴201位置和封严副位置,在变厚度承力骨架2上确定预旋喷嘴201和封严副的连接节点,由连接节点向对应的预旋喷嘴201和封严副引出连接支架2013。
32.如图3所示,承力骨架2轮廓线由多段直线拟合形成,起点2012厚度较厚,两个连接支架2013与承力骨架2平缓光滑过渡;承力骨架2上在预旋喷嘴201对应的位置开孔,为预旋喷嘴201的进气口2011。
33.如图4所示,预旋喷嘴201右端形成篦齿用于与转子挡板5形成动密封结构。
34.如图5所示,人字环组件202中焊接蜂窝密封组件203或台阶蜂窝密封组件203,用于与转子轴9形成封严副。
35.3)工作原理如图2所示,仿生承力结构上端安装组件通过叶片内支撑环4与涡轮静子叶片3连接(连接方式可为销钉/螺栓),左端安装组件通过d头螺栓8、螺母7与燃烧室机匣6连接。由仿生承力结构上端承载叶片产生的气动载荷,该载荷沿变厚度承力骨架2传递至燃烧室机匣6。
36.下端由转子轴9与蜂窝密封组件203、台阶蜂窝密封组件203形成篦齿封严副,右端由篦齿与转子挡板5形成密封结构。
37.预旋喷嘴201和人字环组件202在满足空气流路封严要求的同时,提高承力框架整体刚度和抗变形能力,叶片通过承力骨架2传力至燃烧室机匣6,传力可靠。同时,承力结构的仿生形式,使预旋喷嘴201以及人字环组件202对应的封严副热变形极小,转、静子冷态间隙仅需0.6mm便可满足发动机全工况使用要求,提高发动机性能。
38.该承力结构总重量约14kg,远小于其他发动机类似结构组件重量。
39.以上仅为本发明的较佳实施例而已,并不用以限制本发明,凡在本发明的精神和原则之内所作的任何修改、等同替换和改进等,均应包含在本发明的保护范围之内。