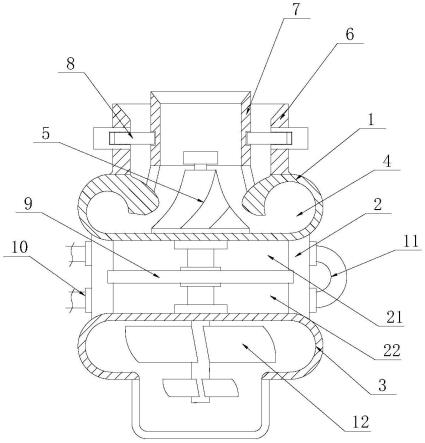
1.本实用新型属于涡轮增压技术领域,尤其是涉及一种涡轮增压节能耐磨无泄漏盘片泵。
背景技术:2.目前,公知的废气涡轮增压器是由滑动轴承或滚珠轴承支撑定位涡轮转子轴,涡轮转子轴总成处于750℃左右高温,转速可达30万r/min的高速旋转,高温导致零件微膨胀在高速旋转时产生摩擦,高温与摩擦加剧了涡轮的反应滞后,导致进气不足燃烧不充分;针对涡轮增压器高温进行结构改进,故提供一种涡轮增压节能耐磨无泄漏盘片泵。
技术实现要素:3.为解决现有技术的缺陷和不足问题;本实用新型的目的在于提供一种结构简单,设计合理、使用方便的涡轮增压节能耐磨无泄漏盘片泵,它利用隔离腔进行前后涡轮的热隔离,并配合冷媒循环进行降温;延长涡轮增压泵使用寿命;另采用双进气通道结构,提高废气利用率。
4.为实现上述目的,本实用新型采用的技术方案是:它包含进气涡轮壳体、隔离腔壳体、排气涡轮壳体、进气风道、锥形涡轮、次级进气通道、主进气通道、光阑式隔离窗、隔热阻隔片、冷媒进出口、u形循环通道、阶梯排气风扇;所述的进气涡轮壳体与排气涡轮壳体之间通过隔离腔壳体进行连接;所述的进气涡轮壳体的内部设置有进气风道,进气风道的中间连接有锥形涡轮,进气涡轮壳体外侧连接有次级进气通道,次级进气通道的内部通过连接支架连接有主进气通道,主进气通道与锥形涡轮保持对应;所述的次级进气通道中间设置有光阑式隔离窗,光阑式隔离窗隔离片卡接在次级进气通道、主进气通道之间;所述的隔离腔壳体的中间设置有隔热阻隔片,且隔离腔壳体的一侧连接有一对冷媒进出口,隔离腔壳体的另一侧连接有u形循环通道;排气涡轮壳体的内部设置有阶梯排气风扇。
5.作为优选,所述的光阑式隔离窗为双层光阑隔板结构,配合光阑式隔离窗外侧的驱动电机进行次级进气通道的开闭。
6.作为优选,所述的锥形涡轮与阶梯排气风扇之间通过连杆同轴连接,且连杆通过密封轴承活动穿插在隔热阻隔片中间。
7.作为优选,所述的隔热阻隔片将隔离腔壳体内部分割成低温隔离腔和高温隔离腔;冷却油通过冷媒进出口从低温隔离腔进入,并在u形循环通道导入高温隔离腔再导出;阻隔排气涡轮壳体的热传递。
8.作为优选,所述的光阑式隔离窗替换为数个翻板叶片,翻板叶片通过连接轴与次级进气通道外侧的驱动齿轮连接,且各驱动齿轮上端啮合有联动齿盘;所述的驱动齿轮与联动齿盘通过外托座进行固定包裹;对应的驱动齿轮与外托座外侧的伺服电机连接。
9.采用上述结构后,本实用新型有益效果为:
10.1、采用隔离腔将进气涡轮与排气涡轮进行隔离;减少排气涡轮对进气涡轮的热传
递;
11.2、利用隔离腔内部冷媒循环进行冷却作用,大大减低涡轮增压泵整体的温度,延长涡轮增压泵的寿命;
12.3、涡轮增压泵整体温度的降低,减少泵内部零件的膨胀,从而降低了泵内零件的磨损;
13.4、涡轮增压泵进气涡轮采用双通道结构,同转速下进气量能够根据需求自由调整节;充分利用高压废气的功能。
附图说明
14.为了更清楚地说明本实用新型实施例或现有技术中的技术方案,本实用新型由下述的具体实施及附图作以详细描述。
15.图1为本实用新型的结构示意图;
16.图2为本实用新型的俯视图;
17.图3为本实用新型的具体实施方式二的结构示意图;
18.附图标记说明:进气涡轮壳体1、隔离腔壳体2、排气涡轮壳体3、进气风道4、锥形涡轮5、次级进气通道6、主进气通道7、光阑式隔离窗8、隔热阻隔片9、冷媒进出口10、u形循环通道11、阶梯排气风扇12、驱动电机13、低温隔离腔21、高温隔离腔22、翻板叶片81、驱动齿轮82、伺服电机83、联动齿盘84、外托座85。
具体实施方式
19.为使本实用新型的目的、技术方案和优点更加清楚明了,下面通过附图中示出的具体实施例来描述本实用新型。但是应该理解,这些描述只是示例性的,而并非要限制本实用新型的范围。此外,在以下说明中,省略了对公知结构和技术的描述,以避免不必要地混淆本实用新型的概念。
20.在此,还需要说明的是,为了避免因不必要的细节而模糊了本实用新型,在附图中仅仅示出了与根据本实用新型的方案密切相关的结构和/或处理步骤,而省略了与本实用新型关系不大的其他细节。
21.具体实施方式一:
22.参看如图1、图2所示,本具体实施方式采用以下技术方案:它包含进气涡轮壳体1、隔离腔壳体2、排气涡轮壳体3、进气风道4、锥形涡轮5、次级进气通道6、主进气通道7、光阑式隔离窗8、隔热阻隔片9、冷媒进出口10、u形循环通道11、阶梯排气风扇12;所述的进气涡轮壳体1与排气涡轮壳体3之间通过隔离腔壳体2进行连接;所述的进气涡轮壳体1的内部设置有进气风道4,进气风道4的中间连接有锥形涡轮5,进气涡轮壳体1外侧连接有次级进气通道6,次级进气通道6的内部通过连接支架连接有主进气通道7,主进气通道7与锥形涡轮5保持对应;所述的次级进气通道6中间设置有光阑式隔离窗8,光阑式隔离窗8隔离片卡接在次级进气通道6、主进气通道7之间;所述的隔离腔壳体2的中间设置有隔热阻隔片9,且隔离腔壳体2的一侧连接有一对冷媒进出口10,隔离腔壳体2的另一侧连接有u形循环通道11;排气涡轮壳体3的内部设置有阶梯排气风扇12。
23.其中,所述的光阑式隔离窗8为双层光阑隔板结构,配合光阑式隔离窗8外侧的驱
动电机13进行次级进气通道6的开闭。光阑式隔离窗8内部的活动光阑隔板镶嵌卡接在主进气通道7外侧壁的嵌槽内部,实现次级进气通道6的密封闭合;且各活动光阑隔板边沿内嵌橡胶护边增加光阑式隔离窗8的密封性;
24.进一步,所述的锥形涡轮5与阶梯排气风扇12之间通过连杆同轴连接,且连杆通过密封轴承活动穿插在隔热阻隔片9之间;所述的隔热阻隔片9将隔离腔壳体2内部分割成低温隔离腔21和高温隔离腔22;冷却油通过冷媒进出口10从低温隔离腔21进入,并在u形循环通道11导入高温隔离腔22再导出;阻隔排气涡轮壳体3的热传递。隔热阻隔片9采用隔热材料,阻隔排气涡轮内部高温向进气涡轮扩散;另外,低温隔离腔21与高温隔离腔22之间通过通过冷媒进出口10与u形循环通道11的配合进行冷却循环,降低排气涡轮的温度。
25.本具体实施方式的工作原理:发动机产生的高温高压废气通过导管输送到排气涡轮壳体3的内部,并推动阶梯排气风扇12进行旋转,阶梯排气风扇12旋转的同时将废气向外疏导,阶梯排气风扇12通过连杆的配合带动锥形涡轮5进行旋转,锥形涡轮5高速旋转将外界口径向内抽吸并压缩输送到进气风道4内部;在此过程中,根据发动机进气量的需求可自由调节光阑式隔离窗8的开闭,进行发动机进气量的调整;另外,由于高温高压废气持续输送给排气涡轮壳体3,使得排气涡轮壳体3内部温度较高;温度沿着排气涡轮壳体3向隔离腔壳体2传递,隔离腔壳体2中间设置有隔热阻隔片9阻隔大量热量传递给进气涡轮壳体1;同时,冷媒从低温隔离腔21进入,并在u形循环通道11导入高温隔离腔22再导出;能够带走大量的热量以降低排气涡轮壳体3的高温。
26.具体实施方式二:
27.参看图3,本具体实施方式与具体是方式不同之处在于:将所述的光阑式隔离窗8替换为数个翻板叶片81,翻板叶片81通过连接轴与次级进气通道6外侧的驱动齿轮82连接,且各驱动齿轮82上端啮合有联动齿盘84;所述的驱动齿轮82与联动齿盘84通过外托座85进行固定包裹;对应的驱动齿轮82与外托座85外侧的伺服电机83连接;翻板叶片81的外边沿设置有密封橡胶包边,密封橡胶包边在旋转过程中能够收缩以贴合主进气通道7外曲面结构,且各翻板叶片81的翻转角度可进行调节,实现进气量的控制。
28.本实用新型采用隔离腔将进气涡轮与排气涡轮进行隔离;减少排气涡轮对进气涡轮的热传递;利用隔离腔内部冷媒循环进行冷却作用,大大减低涡轮增压泵整体的温度,延长涡轮增压泵的寿命;涡轮增压泵整体温度的降低,减少泵内部零件的膨胀,从而降低了泵内零件的磨损;涡轮增压泵进气涡轮采用双通道结构,同转速下进气量能够根据需求自由调整节。
29.对于本领域技术人员而言,显然本实用新型不限于上述示范性实施例的细节,而且在不背离本实用新型的精神或基本特征的情况下,能够以其他的具体形式实现本实用新型。因此,无论从哪一点来看,均应将实施例看作是示范性的,而且是非限制性的,本实用新型的范围由所附权利要求而不是上述说明限定,因此旨在将落在权利要求的等同要件的含义和范围内的所有变化囊括在本实用新型内。
30.此外,应当理解,虽然本说明书按照实施方式加以描述,但并非每个实施方式仅包含一个独立的技术方案,说明书的这种叙述方式仅仅是为清楚起见,本领域技术人员应当将说明书作为一个整体,各实施例中的技术方案也可以经适当组合,形成本领域技术人员可以理解的其他实施方式。