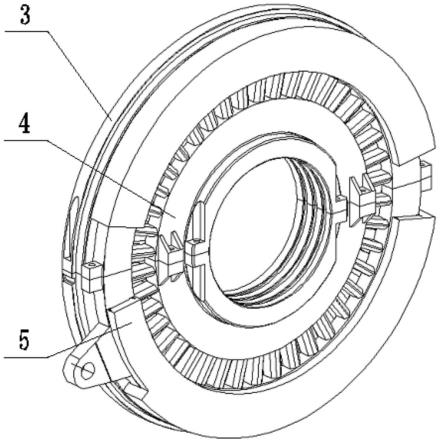
1.本实用新型属于汽轮机旋转隔板,尤其涉及一种适用于超临界工业抽汽用的旋转隔板。
背景技术:2.随着我国经济发展,热电联产和集中供热的市场需求越来越大,相应的大型的、具备可调整抽汽功能的汽轮机深受用户欢迎。用旋转隔板控制抽汽的大功率汽轮机,其抽汽能力可满足热用户需求,很好的实现汽机热电联产的市场需求。
3.传统的旋转隔板受deva合金使用条件限制,作为隔板体摩擦副(deva合金)结合面必须使用不锈钢,同时还需具有足够高的光洁度和硬度。传统隔板转动环采用不锈钢加工,而不锈钢要达到足够高硬度,必需进行淬火等处理。淬火后,机械加工及焊接等残余应力较难去除,这就存在工作变形的隐患。以往在旋转隔板应用中经常出现老机组的旋转隔板运行卡涩、转动环变形及转动环柄焊接断裂等问题。
技术实现要素:4.本实用新型需要解决的技术问题是:现有的隔板体在生产过程中因焊接、机械加工及热处理等存在残余应力,转动环由于前后压力不均匀以及隔板体残余应力的问题容易引起转动环的变形,最终产生的转动环旋转卡涩的问题;进而提供一种适用于超临界工业抽汽用的旋转隔板。
5.本实用新型为解决上述技术问题采用的技术方案是:一种适用于超临界工业抽汽用的旋转隔板,它包括汽封圈、汽封体、隔板体、转动环和罩环;所述的汽封圈、汽封体、隔板体、转动环和罩环均为环形结构,所述的汽封圈安装在隔板体的内环面上,所述的汽封体同轴安装在隔板体的出汽侧,转动环同轴安装在隔板体的进汽侧,并对隔板体产生正压力,同时转动环与隔板体之间形成转动摩擦副;所述的罩环罩在转动环上并同轴安装在隔板体上,所述的罩环、转动环和隔板体之间形成两个上下对称的压力平衡室,所述的两个压力平衡室保证了转动环对隔板体所产生的正压力的恒定。
6.进一步的,所述的隔板体包括隔板外环、隔板内环和多片隔板静叶片,所述的隔板外环同轴套在隔板内环外,并与隔板内环之间形成环形汽道ⅰ,所述的多片隔板静叶片均匀分布到环形汽道ⅰ内,并将环形汽道分隔成多个汽道口ⅰ;所述转动环包括转动环外环、转动环内环和多片转动环静叶片,所述的转动环外环同轴套在转动环内环外,并与转动环内环之间形成环形汽道ⅱ,所述的多片转动环静叶片均匀间隔的分布到环形汽道ⅱ内,并将环形汽道ⅱ分隔成多个汽道口ⅱ;所述转动环静叶片的数量与隔板体上汽道口ⅰ的数量相同,且每片转动环静叶片的截面积等于每道汽道口ⅰ的通流面积。
7.进一步的,所述的罩环包括上半罩环和下半罩环,所述的上半罩环和下半罩环上下相对设置,所述下半罩环的一侧开有一个导向豁口;所述转动环的外环面上设置有一个转动柄,所述的转动柄插在下半罩环上的导向豁口内,并可沿着导向豁口的弧形延伸度方
向移动。
8.进一步的,所述隔板体的进汽侧端面上同轴设置有两条环形的摩擦带,所述的两条摩擦带分别为摩擦带ⅰ和摩擦带ⅱ,所述转动环的出汽侧端面上设置两条同轴的环形的摩擦带,转动环上的两条摩擦带分别为摩擦带ⅲ和摩擦带ⅳ,所述隔板体上的摩擦带ⅰ与转动环上的摩擦带ⅲ形成转动摩擦副ⅰ,隔板体上的摩擦带ⅱ与转动环上的摩擦带ⅳ形成转动摩擦副ⅱ;所述的转动摩擦副ⅰ与转动摩擦副ⅱ共同形成转动环与隔板体之间的转动摩擦副。
9.进一步的,所述的摩擦带ⅰ处于隔板外环上并靠近环形汽道ⅰ处设置,所述的摩擦带ⅱ处于隔板内环上并靠近环形汽道ⅰ处设置;
10.所述的摩擦带ⅲ处于转动环外环上并靠近环形汽道ⅱ处设置,所述的摩擦带ⅳ处于转动环内环上并靠近环形汽道ⅱ处设置。
11.进一步的,所述的摩擦带ⅰ和摩擦带ⅱ为与隔板体一体制成的两条环形凸起ⅰ,所述的两条环形凸起ⅰ上分别堆焊司太立合金;
12.所述的摩擦带ⅲ和摩擦带ⅳ为与转动环一体制成的两条环形凸起ⅱ,所述的两条环形凸起ⅱ上喷涂有cr3c
2-nicr金属陶瓷涂层。
13.进一步的,所述的上半罩环、转动环的上半部分与隔板体的上半部分形成一个压力平衡室,下半罩环、转动环的下半部分与隔板体的下半部分形成一个压力平衡室,所述的两个压力平衡室结构形式相同,故以其中一个压力平衡室进行说明;
14.所述的上半罩环与转动环外环的进汽侧形成密封腔ⅰ,所述转动环外环的出汽侧与隔板外环的进汽侧形成密封腔ⅱ;所述的上半罩环上沿其弧形延伸方向均匀开有若干个平衡通道ⅰ,所述的隔板外环上沿其弧形延伸方向均匀开有若干个径向设置的平衡通道ⅱ,所述的平衡通道ⅱ与隔板体上的汽道口ⅰ相通;在隔板外环上沿其弧形延伸方向均匀开有若干个轴向设置的平衡通道ⅲ,所述平衡通道ⅱ的数量为平衡通道ⅲ数量的2倍;隔板外环上平衡通道ⅱ平均分成两部分,其中一部分平衡通道ⅱ通过若干个平衡通道ⅰ与密封腔ⅰ相通,另一部分平衡通道ⅱ通过若干个平衡通道ⅲ与密封腔ⅱ相通,故密封腔ⅰ与密封腔ⅱ相通。
15.进一步的,所述的上半罩环上朝向转动环的一侧向内凹陷,并且在上半罩环朝向转动环外环的内侧壁上分别设置有两道弹性密封条,所述的两道弹性密封条同轴径向布置,并分别处于上半罩环内壁凹陷处的上方及下方;所述的弹性密封条对上半罩环与转动环外环之间产生挤压力。
16.进一步的,所述的隔板外环与隔板静叶片之间采用焊接的方式进行连接,隔板静叶片与隔板内环之间采用焊接的方式进行连接。
17.进一步的,所述的隔板体、转动环和罩环的材质均为铬钼合金钢。
18.本实用新型与现有技术相比产生的有益效果是:
19.1、本技术的隔板体由原来的铸造结构形式改为焊接结构形式,可以减小隔板体内的残余应力;同时隔板体、转动环以及罩环采用铬钼合金钢,便于机械加工及焊接,而且铬钼合金钢耐温可达500℃,本技术在处于400℃下可长期安全运行,可以避免隔板体、转动环以及罩环由于热变形引起的旋换隔板卡涩的问题。
20.2、本技术通过设置压力平衡室,使得转动环两侧的压力保持平衡,减小转动环对
隔板体的正压力,从而减少了转动环与隔板体之间转动摩擦副的摩擦力,进一步减小转动环的开启力矩。同时,由于两个压力平衡室的对称布置,使得两个压力平衡室中的相对的平衡通道也处于对称布置,压力平衡室中合理、对称布置平衡通道的位置及结构尺寸,使其既能满足平衡连通作用,又不会因平衡通道布置不合理导致转动环轴向受力不均而产生变形翘曲,同时还应降低了平衡通道对旋转隔板强度的削弱,从而保证旋转隔板安全运行需求。而且罩环和转动环之间设置弹性密封条,在保证密封腔ⅰ和密封腔ⅱ的密封效果的前提下,使得转动环与罩环之间还具有足够退让能力,避免转动环和罩环碰磨变形,引起旋换隔板的卡涩。
附图说明
21.附图作为本技术的一部分,用来提供对本实用新型的进一步的理解,本实用新型的示意性实施例及其说明用于解释本实用新型,但不构成对本实用新型的不当限定。
22.图1是本技术进汽侧的轴侧示意图;
23.图2是本技术出汽侧的轴侧示意图;
24.图3是本技术内部结构示意图;
25.图4是本技术主视图;
26.图5是隔板体的结构示意图;
27.图6是本技术的侧视图;
28.图7是图4中a-a处的剖视图;
29.图8是压力平衡室中隔板体、罩环与密封腔ⅰ相通的示意图;
30.图9是压力平衡室中隔板体与密封腔ⅱ相通的示意图;
31.图10是旋转隔板温度场云图;
32.图11是旋转隔板等效应力云图;
33.图12是转动环径向变形云图;
34.图13是转动环轴向变形云图。
35.附图标记说明:1、汽封圈;2、汽封体;3、隔板体;301、隔板外环;302、隔板内环;303、隔板静叶片;304、摩擦带ⅰ;305、摩擦带ⅱ;306、平衡通道ⅱ;307、平衡通道ⅲ;4、转动环;401、转动环外环;402、转动环内环;403、转动环静叶片;404、摩擦带ⅲ;405、摩擦带ⅳ;406、转动柄;5、罩环;501、上半罩环;502、下半罩环;504、平衡通道ⅰ;6、压力平衡室;601、密封腔ⅰ;602、密封腔ⅱ;7、弹性密封条。
具体实施方式
36.为使本实用新型实施例的目的、技术方案和优点更加清楚,下面将结合本实用新型实施例中的附图,对实施例中的技术方案进行清楚、完整地描述,以下实施例用于说明本实用新型,但不用来限制本实用新型的范围。
37.在本实用新型的描述中,需要说明的是,术语“上”、“下”、“内”、“外”等指示的方位或位置关系为基于附图所示的方位或位置关系,仅是为了便于描述本实用新型和简化描述,而不是指示或暗示所指的装置或元件必须具有特定的方位、以特定的方位构造和操作,因此不能理解为对本实用新型的限制。
38.在本实用新型的描述中,需要说明的是,除非另有明确的规定和限定,术语“安装”、“连接”应做广义理解,例如,可以是固定连接,也可以是可拆卸连接,或一体地连接;可以是机械连接,也可以是电连接;可以是直接相连,也可以通过中间媒介间接相连。对于本领域的普通技术人员而言,可以具体情况理解上述术语在本实用新型中的具体含义。
39.参见图1至图13,本技术实施例提供一种适用于超临界工业抽汽用的旋转隔板,它包括汽封圈1、汽封体2、隔板体3、转动环4和罩环5;为了配合汽轮机的结构形式,所述的汽封圈1、汽封体2、隔板体3、转动环4和罩环5均为环形结构;为了方便旋转隔板的装配,所述的汽封体2、隔板体3、转动环4和罩环5均为上下两半的结构形式,其中隔板体3和转动环4的中分面均通过螺栓进行连接,并形成一个完整的环形结构,所述的罩环5为分体的环形结构;
40.如图2和图6所示,所述的汽封圈1安装在隔板体3的内环面上,用于保证隔板体3与转子之间的汽封间隙,降低漏气损失,提高整机的热效率。
41.如图5所示,所述隔板体3的材质为铬钼合金钢,其安装在汽轮机内静止不动,所述的隔板体3包括隔板外环301、隔板内环302和多片隔板静叶片303,其中,所述的隔板外环301是由两个相同的半环体组装而成,隔板内环302是由两个相同的半环体组装而成;所述的隔板外环301同轴套在隔板内环302外并与隔板内环302之间形成环形汽道ⅰ,所述的多片隔板静叶片303均匀间隔的分布到环形汽道ⅰ内,并将环形汽道分隔成多个汽道口ⅰ,即相邻的两片隔板静叶片303之间形成一道汽道口ⅰ;其中,所述的隔板外环301与隔板静叶片303之间采用焊接的方式进行连接,隔板静叶片303与隔板内环302之间采用焊接的方式进行连接;所述的隔板静叶片303为自带围带的铣制叶片,所述隔板内环302的半环体的纵截面为l形,即隔板内环302的进汽侧同轴设置有一体制成的环形圈。
42.所述的汽封体2同轴安装在隔板体3的隔板外环301的出汽侧,优选采用焊接的方式进行连接,即汽封体2的进汽侧端面焊接在隔板体3的隔板外环301的出汽侧端面上,同样也用于保证隔板体3与转子之间的汽封间隙,降低漏气损失,提高整机的热效率。
43.如图3所示,所述转动环4的材质为铬钼合金钢,其包括转动环外环401、转动环内环402和多片转动环静叶片403,所述的转动环外环401同轴套在转动环内环402外并与转动环内环402之间形成环形汽道,所述的多片转动环静叶片403均匀间隔的分布到环形汽道内,并将环形汽道分隔成多个汽道口ⅱ,即相邻的两片转动环静叶片403之间形成一道汽道口ⅱ;其中所述的转动环外环401与转动环静叶片403之间采用焊接的方式进行连接,转动环静叶片403与转动环内环402之间采用焊接的方式进行连接,所述转动环静叶片403的数量、汽道口ⅱ的数量与隔板体3上汽道口ⅰ的数量相同,故隔板体3与转动环4之间形成单圈窗口的结构型式,且每片转动环静叶片403的截面积等于每道汽道口ⅰ的通流面积。
44.如图5所示,所述的转动环4同轴设置在隔板体3的进汽侧,即转动环4套在隔板内环302上的环形圈上,转动环4的外径小于隔板体3的外径,故转动环4的外环面与隔板体3的边缘处留有一定的空间,此空间用于安装罩环5;所述的转动环4与隔板体3的进汽侧端面之间形成转动摩擦副,即隔板体3的进汽侧端面上同轴设置有两条环形的摩擦带,所述的摩擦带为与隔板体3一体制成的两条环形凸起ⅰ,所述的环形凸起ⅰ上堆焊司太立合金;所述的两条摩擦带分别为摩擦带ⅰ304和摩擦带ⅱ305,所述的摩擦带ⅰ304处于隔板外环301上并靠近环形汽道ⅰ处设置,所述的摩擦带ⅱ305处于隔板内环302上并靠近环形汽道ⅰ处设置;如图7
307数量的2倍;隔板外环301上平衡通道ⅱ306平均分成两部分,其中一部分平衡通道ⅱ306通过若干个平衡通道ⅰ504与密封腔ⅰ601相通,即平衡通道ⅱ306的一端与平衡通道ⅰ504的一端相通,平衡通道ⅰ504的另一端与密封腔ⅰ601相通;另一部分平衡通道ⅱ306通过若干个平衡通道ⅲ307与密封腔ⅱ602相通,即平衡通道ⅱ306的中间段与平衡通道ⅲ307的一端相通,平衡通道ⅲ307的另一端与密封腔ⅱ602相通,由于两部分平衡通道ⅱ306均与隔板体3上的汽道口ⅰ相通,因此达到密封腔ⅰ601与密封腔ⅱ602相通的目的;即所述的密封腔ⅰ601与密封腔ⅱ602依次通过若干个平衡通道ⅰ504、其中一部分平衡通道ⅱ306、隔板体3上的汽道口ⅰ、另一部分平衡通道ⅱ306和若干个平衡通道ⅲ307相通,即因此两部分平衡通道ⅱ306通过汽道口ⅰ相通,达到密封腔ⅰ601与密封腔ⅱ602相通的目的。
49.本实施例采用单圈窗口的结构形式,且隔板体3由原来的铸造结构形式改为焊接结构形式,可以减小隔板体3内的残余应力;同时隔板体3、转动环4以及罩环5采用铬钼合金钢,便于机械加工及焊接,而且铬钼合金钢耐温可达500℃,本技术在处于400℃下可长期安全运行,可以避免隔板体3、转动环4以及罩环5由于热变形引起的旋换隔板卡涩的问题。
50.本实施例中,所述的转动环4与隔板体3之间形成转动摩擦副,用于承担着转动环4的前后压差,摩擦副的摩擦面采用先进热喷涂耐磨涂层技术,即在转动环4的出汽侧喷涂nicr-cr2c3涂层,在隔板体3侧堆焊司太立合金,使新型摩擦副具有较高的高温硬度、优异的高温耐磨性、耐蚀性、抗氧化性及较高的结合强度,可广泛应用于高温磨粒磨损、腐蚀磨损和冲蚀磨损工况下工作的零件。
51.本实施例中,通过设置压力平衡室6,即通过在转动环4的进汽侧与出汽侧设置相通的密封腔ⅰ601与密封腔ⅱ602,转动环4两侧的压力保持平衡,与以往的设计形式相比可减小转动环4对隔板体3的正压力,从而减少了转动环4与隔板体3之间转动摩擦副的摩擦力,进一步减小转动环4的开启力矩。同时,由于两个压力平衡室6的对称布置,使得两个压力平衡室6中的相对的平衡通道也处于对称布置,压力平衡室6中合理、对称布置平衡通道的位置及结构尺寸,使其既能满足平衡连通作用,又不会因平衡通道布置不合理导致转动环4轴向受力不均而产生变形翘曲,同时还应降低了平衡通道对旋转隔板强度的削弱,从而保证旋转隔板安全运行需求。而且罩环5和转动环4之间设置弹性密封条7,在保证密封腔ⅰ601和密封腔ⅱ602的密封效果的前提下,使得转动环4与罩环5之间还具有足够退让能力,避免转动环4和罩环5碰磨变形,引起旋换隔板的卡涩。
52.本实施例中,对于转动环4的旋转,采用了足够大的油动机进行驱动,保证转动力矩的富余,使得旋转隔板运动自如,安全可靠;新型旋转隔板可用于大容量高抽汽参数汽轮机的抽汽调节需求。
53.以下对本实用新型的工作过程做进一步的说明,以进一步展示本实用新型的工作原理和优点:
54.本技术的旋转隔板在安装时,隔板体3固定在汽轮机内的隔板套上,转动环4套装在隔板体3上,当需要调节汽轮机进汽量时,转动环4通过连杆与油动机连接,油动机上下往复运动,带动转动环4以隔板体3的中轴线为轴小角度转动,即转动环4与隔板体3之间构成转动副,在此过程中转动环4上的每片转动环静叶片403和隔板体3上的每道汽道口ⅰ产生相对错位,改变了旋转隔板进汽的通流面积(转动环上的汽道口ⅱ与隔板体上的汽道口ⅰ重叠时,旋转隔板的通流面积最大,汽轮机的进汽量最大;转动环静叶片403与隔板体上的汽道
口ⅰ完全重叠时,旋转隔板的通流面积最小,汽轮机的进汽量最小);从而实现抽汽调节。通过合理选择转动环4与隔板体3间的冷态安装间隙,使隔板转动副在高温高压环境下仍有足够的运动间隙。由于隔板体3与转动环4之间存在转动摩擦副,所以在汽轮机进汽时,由于高温高压蒸汽对转动环4产生一定的压力,所以使得转动环4对隔板体3的进汽侧端面存在一定的正压力;在旋转隔板的通流面积不变的情况下,由于转动环4、隔板体3与罩环5间存在压力平衡室6,所以即使在转动环4转动的过程中,也可以保证转动环4对隔板体3的正压力保持恒定不变,从而保证转动环4与隔板体3之间的转动摩擦副的摩擦力不变,保证转动环4的开启力矩不变;同时,转动环4在压力平衡室6的作用下受力均匀,不会产生变形。
55.本实施例进行有限元及摩擦副模拟实验,如图10~13所示,优化后的旋转隔板强度及刚度满足使用要求,同时转动环变形均匀,不会产生明显翘曲现象。
56.虽然在本文中参照了特定的实施方式来描述本实用新型,但是应该理解的是,这些实施例仅仅是本实用新型的原理和应用的示例。因此应该理解的是,可以对示例性的实施例进行许多修改,并且可以设计出其他的布置,只要不偏离所附权利要求所限定的本实用新型的精神和范围。应该理解的是,可以通过不同于原始权利要求所描述的方式来结合不同的从属权利要求和本文中所述的特征。还可以理解的是,结合单独实施例所描述的特征可以使用在其他所述实施例中。