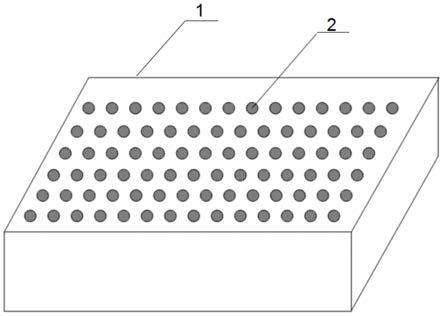
[0001]
本发明属于微电子散热的技术领域,具体而言,涉及一种用于氮化镓功放芯片的玻璃微流道散热器制备方法。
背景技术:[0002]
功率芯片是射频微系统的核心部件,目前,以氮化镓(gan)为代表的第三代半导体技术具有宽禁带的特点,可以承受更高的工作结温,其功率密度可达30w/mm(远高于gaas的0.5w/mm),可是在微波频段,gan器件自热效应相当严重,一些多栅gan基器件在微波频段的输出热流密度甚至达到千瓦每平方厘米量级。因此,散热问题已经成为严重制约gan功放芯片性能发挥的瓶颈问题。
[0003]
采用微流道器件进行散热,通过微尺度的连续流体直接对芯片进行冷却,可以最大限度降低远程散热模式中各热沉间热阻对散热效率的影响,从而大幅度提升芯片的冷却效率,已经成为大功率芯片最近端散热的最佳途径之一,获得广泛关注。
[0004]
现有微流道器件通常采用硅、金属或玻璃基材,其中,硅基器件性能优秀,但多采用如深硅刻蚀、硅-硅键合等半导体工艺,加工难度大、制备成本高;金属基器件基材散热良好,但受限于加工手段,微流道尺寸难以做到很小;玻璃基器件本身材料热阻较大,散热性能受到一定影响,不能满足gan功率放大器良好散热的要求。
技术实现要素:[0005]
鉴于此,为了解决现有技术存在的上述问题,本发明的目的在于提供一种用于氮化镓功放芯片的玻璃微流道散热器制备方法以通过可光刻玻璃实现高深宽比微流道,通过玻璃通孔互联(through via glass,tgv)降低接触热阻,提高散热能力。
[0006]
本发明所采用的技术方案为:一种用于氮化镓功放芯片的玻璃微流道散热器制备方法,该方法包括:
[0007]
s1:准备至少3片可光刻玻璃圆片,分别为:a玻璃圆片、b玻璃圆片和c玻璃圆片;
[0008]
s2:在a玻璃圆片上刻蚀tgv通孔,在b玻璃圆片上刻蚀微流道结构和b进出液口且两者之间通过分流网络连通,在c玻璃圆片上刻蚀c进出液口;
[0009]
s3:对a玻璃圆片作实心电镀工艺,以得到tgv实心互连结构;
[0010]
s4:分别在a玻璃圆片的下表面、b玻璃圆片的两侧表面和c玻璃圆片的上表面设置连接膜层;
[0011]
s5:将a玻璃圆片、b玻璃圆片和c玻璃圆片依次键合形成复合圆片;
[0012]
s6:复合圆片通过分片工艺获得单个微流道散热器。
[0013]
进一步地,在步骤s2之前,分别对a玻璃圆片和c玻璃圆片进行减薄抛光。
[0014]
进一步地,在步骤s3中,所述实心电镀工艺包括:
[0015]
s31:在a玻璃圆片上溅射扩散阻挡层和种子层;
[0016]
s32:通过种子层导电以对a玻璃圆片的各个tgv通孔进行实心电镀铜;
[0017]
s33:对a玻璃圆片作表面化学机械抛光,以获取tgv实心互连结构;
[0018]
通过tgv实心互连结构的设置可降低接触热阻,有效提高散热能力。
[0019]
进一步地,在步骤s4之前,分别对a玻璃圆片、b玻璃圆片和c玻璃圆片进行化学机械抛光,以确保玻璃圆片的表面粗糙度在合理范围之内。
[0020]
进一步地,在步骤s4中,所述连接膜层通过沉积生长或涂覆而成,以扩展工艺方法的可实施性。
[0021]
进一步地,在步骤s5中,通过热压键合工艺对a玻璃圆片、b玻璃圆片和c玻璃圆片进行依次键合,热压键合工艺具备高连接可靠性和高焊接效率的优点。
[0022]
进一步地,所述步骤s5具体包括:
[0023]
s51:将a玻璃圆片的下表面与b玻璃圆片的上表面键合;
[0024]
s52:将b玻璃圆片的b进出液口与c玻璃圆片的c进出液口相对齐并将b玻璃圆片的下表面与c玻璃圆片的上表面键合。
[0025]
进一步地,在步骤s6中,所述分片工艺为砂轮分片工艺或激光分片工艺,具有高精度、高质量的优点。
[0026]
本发明的有益效果为:
[0027]
1.采用本发明所提供的用于氮化镓功放芯片的玻璃微流道散热器制备方法,其利用可光刻玻璃的刻蚀技术和tgv技术优化玻璃微流道结构,由于在芯片装接表面具有tgv结构,可降低接触热阻和有效提高散热能力,同时,在b玻璃圆片中具有高深宽比的微流道结构以及分流网络,能够实现散热热流密度大于300w/cm2。
附图说明
[0028]
图1是本发明所提供的用于氮化镓功放芯片的玻璃微流道散热器制备方法的整体示意图;
[0029]
图2是本发明所提供的用于氮化镓功放芯片的玻璃微流道散热器制备方法的整体剖面图;
[0030]
图3是本发明所提供的用于氮化镓功放芯片的玻璃微流道散热器制备方法在步骤s1中a玻璃圆片、b玻璃圆片和c玻璃圆片的示意图;
[0031]
图4是对图3中a玻璃圆片和c玻璃圆片进行减薄抛光后的结构示意图;
[0032]
图5是本发明所提供的用于氮化镓功放芯片的玻璃微流道散热器制备方法在步骤s2中的状态示意图;
[0033]
图6是本发明所提供的用于氮化镓功放芯片的玻璃微流道散热器制备方法在步骤s3中的状态示意图;
[0034]
图7是对图6中a玻璃圆片、b玻璃圆片和c玻璃圆片的表面进行沉积或涂覆连接膜层的示意图;
[0035]
图8是本发明所提供的用于氮化镓功放芯片的玻璃微流道散热器制备方法在步骤s5中的状态示意图;
[0036]
图9是本发明所提供的用于氮化镓功放芯片的玻璃微流道散热器制备方法在步骤s6中进行分片后所获得的单片微流道散热器的示意图;
[0037]
附图中标注如下:
[0038]
1-a玻璃圆片,2-tgv实心互连结构,3-b玻璃圆片,4-c玻璃圆片,5-微流道,6-tgv通孔,7-b进出液口,8-c进出液口,9-连接膜层。
具体实施方式
[0039]
为使本发明实施例的目的、技术方案和优点更加清楚,下面将结合本发明实施例中的附图,对本发明实施例中的技术方案进行清楚、完整地描述,显然,所描述的实施例是本发明一部分实施例,而不是全部的实施例。通常在此处附图中描述和示出的本发明实施例的组件可以以各种不同的配置来布置和设计。
[0040]
因此,以下对在附图中提供的本发明的实施例的详细描述并非旨在限制要求保护的本发明的范围,而是仅仅表示本发明的选定实施例。基于本发明中的实施例,本领域普通技术人员在没有作出创造性劳动前提下所获得的所有其他实施例,都属于本发明保护的范围。
[0041]
需要说明的是,在不冲突的情况下,本发明中的实施例及实施例中的特征可以相互组合。
[0042]
应注意到:相似的标号和字母在下面的附图中表示类似项,因此,一旦某一项在一个附图中被定义,则在随后的附图中不需要对其进行进一步定义和解释。
[0043]
在本发明实施例的描述中,需要说明的是,指示方位或位置关系为基于附图所示的方位或位置关系,或者是该发明产品使用时惯常摆放的方位或位置关系,或者是本领域技术人员惯常理解的方位或位置关系,或者是该发明产品使用时惯常摆放的方位或位置关系,仅是为了便于描述本发明和简化描述,而不是指示或暗示所指的装置或元件必须具有特定的方位、以特定的方位构造和操作,因此不能理解为对本发明的限制。此外,术语“第一”、“第二”仅用于区分描述,而不能理解为指示或暗示相对重要性。
[0044]
在本发明实施例的描述中,还需要说明的是,除非另有明确的规定和限定,术语“设置”、“连接”应做广义理解,例如,可以是固定连接,也可以是可拆卸连接,或一体地连接;可以是直接连接,也可以通过中间媒介间接连接。对于本领域的普通技术人员而言,可以具体情况理解上述术语在本发明中的具体含义;实施例中的附图用以对本发明实施例中的技术方案进行清楚、完整地描述,显然,所描述的实施例是本发明一部分实施例,而不是全部的实施例。通常在此处附图中描述和示出的本发明实施例的组件可以以各种不同的配置来布置和设计。
[0045]
实施例1
[0046]
如图1所示,在本实施例中具体提供了一种用于氮化镓功放芯片的玻璃微流道散热器制备方法,旨在降低接触热阻和提高散热能力,以满足gan功率放大器良好散热的要求,该方法包括:
[0047]
s1:如图3所示,准备3片表面光滑的可光刻玻璃圆片,分别为:a玻璃圆片1、b玻璃圆片3和c玻璃圆片4,各个玻璃圆片的厚度为500μm,且b玻璃圆片3位于中间,而a玻璃圆片1和c玻璃圆片4分别布置在b玻璃圆片3的两侧。
[0048]
s2:如图4所示,通过打磨、抛光工艺分别对a玻璃圆片1和c玻璃圆片4进行减薄抛光,减薄后的a玻璃圆片1和b玻璃圆片3的厚度为200μm;
[0049]
s3:如图5所示,利用光刻腐蚀工艺在a玻璃圆片1上刻蚀若干个tgv通孔6;
[0050]
在b玻璃圆片3上刻蚀微流道结构和b进出液口7且两者之间通过分流网络连通,其中,微流道结构设置有若干个且每个微流道结构的两侧则布置有b进出液口7,优选的,在微流道结构的两侧各设有一个b进出液口7;所述微流道结构包括多个呈平行设置的微流道5,各个微流道5通过分流网络连通至b进出液口7,且所述微流道5为高深宽比,在本实施例中,微流道5的宽度为50μm,深度为500μm;高深宽比的微流道结构以及分流网络,能够实现散热热流密度大于300w/cm2;
[0051]
在c玻璃圆片4上刻蚀c进出液口8,c玻璃圆片4上刻蚀的c进出液口8应当分别与各个b进出液口7对齐连通,以通过两侧的进出液口实现对冷却工质的有效循环,进而确保良好的散热能力,确保输出功率保持稳定。
[0052]
s4:如图6所示,对a玻璃圆片1作实心电镀工艺,以得到tgv实心互连结构2;所述实心电镀工艺包括:
[0053]
s41:在a玻璃圆片1上溅射扩散阻挡层和种子层,其中,扩散阻挡层可选用tin、ta、tan;而种子层则为金属导电层;
[0054]
s42:通过种子层导电以对a玻璃圆片1的各个tgv通孔6进行实心电镀铜,实心电镀铜填满各个tgv通孔6;
[0055]
s43:对a玻璃圆片1作表面化学机械抛光,以获取tgv实心互连结构2,即各个tgv通孔6经过实心电镀铜之后具有良好的导热特性。
[0056]
s5:分别对a玻璃圆片1、b玻璃圆片3和c玻璃圆片4进行化学机械抛光,并使a玻璃圆片1、b玻璃圆片3和c玻璃圆片4的表面粗糙度小于5nm。
[0057]
s6:如图7所示,分别在a玻璃圆片1的下表面、b玻璃圆片3的两侧表面和c玻璃圆片4的上表面设置连接膜层9,例如:连接膜层9为玻璃封接浆料;优选的,所述连接膜层9通过沉积生长或涂覆而成。
[0058]
s7:如图8所示,通过热压键合工艺对a玻璃圆片1、b玻璃圆片3和c玻璃圆片4进行依次键合并最终形成复合圆片;该步骤方法具体包括:
[0059]
s71:通过热压键合工艺将a玻璃圆片1的下表面与b玻璃圆片3的上表面键合;
[0060]
s72:将b玻璃圆片3的b进出液口7与c玻璃圆片4的c进出液口8相对齐并通过热压键合工艺将b玻璃圆片3的下表面与c玻璃圆片4的上表面键合;
[0061]
s73:最终形成复合圆片。
[0062]
s8:将上述的复合圆片通过分片工艺获得单个微流道散热器,如图2、图9所示,优选的,分片工艺为砂轮分片工艺或激光分片工艺。
[0063]
通过上述所形成的微流道散热器,在使用过程中,将氮化镓功放芯片焊接在微流道散热器的上表面,再将微流道散热器焊接在微波盒体内,在工作时,使用乙二醇水溶液作为液冷工质,当氮化镓功放芯片的热流密度为300w/cm2时,氮化镓功放芯片能够在环境温度-10℃~60℃保证工作正常,以确保输出功率保持稳定。
[0064]
实施例2
[0065]
在实施例1中,是准备3片表面光滑的可光刻玻璃圆片,在本实施例中,提供用于氮化镓功放芯片的玻璃微流道散热器制备方法,先准备4片表面光滑的可光刻玻璃圆片,分别为a玻璃圆片1、b1玻璃圆片、b2玻璃圆片和c玻璃圆片4,其中,b1玻璃圆片和b2玻璃圆片的加工工艺参照实施例1中的b玻璃圆片3,在后期键合时,则先将a玻璃圆片1的下表面与b1玻
璃圆片的上表面键合、b1玻璃圆片的下表面与b2玻璃圆片的上表面键合、b2玻璃圆片的下表面键合与c玻璃圆片4的上表面键合,以实现b1玻璃圆片和b2玻璃圆片叠加,其所起功能与实施例1中的b玻璃圆片3相同,其他制备方法与实施例1的方法相同,此处不再赘述。
[0066]
本发明不局限于上述可选实施方式,任何人在本发明的启示下都可得出其他各种形式的产品,但不论在其形状或结构上作任何变化,凡是落入本发明权利要求界定范围内的技术方案,均落在本发明的保护范围之内。