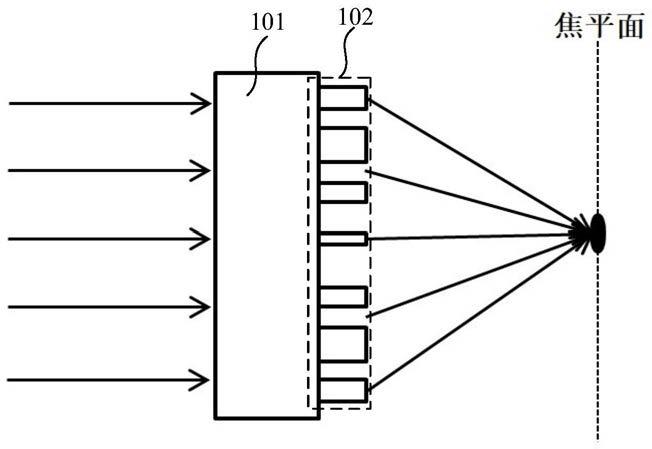
[0001]
本发明涉及微纳光学及光学成像领域,特别是涉及一种双面超表面结构的制备方法,以实现双面超表面结构的高精度对准。
背景技术:[0002]
近年来,微纳结构超表面已经成为一种通过在平面上形成亚波长结构来控制光的新方法,所谓微纳结构超表面指的是亚波长光学散射结构在界面上构成二维阵列,具有特殊的电磁特性和优异的界面操控能力,这种亚波长结构设计能够局部改变入射光的振幅、偏振和相位,且体积小、重量轻,能够实现紧凑的光学结构,因此而备受关注。
[0003]
以下以超表面中的一个应用,超表面透镜为例来说明现有技术及其存在的问题。如图1及图2所示,示出了单面超表面透镜示意图,包括:sio2衬底101、在sio2衬底101上形成的si纳米柱阵列102,根据不同的需求,衬底101的材料不局限于sio2衬底,还可为其他所需半导体材料,如:si、al2o3等,si纳米柱阵列102不局限于图1及图2所示形状,可为各种超表面图形,如:椭圆柱、长方体、不规则图形等,纳米柱阵列102的材料也不局限于si,还可为其他所需材料,如:sio2,tio2,sin、金属等;如图3所示,示出了双面超表面透镜示意图,包括:sio2衬底103;在sio2衬底103两侧形成的si纳米柱阵列104;其中,图1示意的是平行光入射单面超表面透镜的示意图,图2示意的是斜入射的单面超表面透镜的示意图,图3示意的是平行及斜入射的双面超表面透镜的示意图。
[0004]
图1示例中,一束平行光先后经过sio2衬底101及si纳米柱阵列102,聚焦于焦平面,并在焦平面上形成了一个完整的光斑。图2示例中,斜入射的光先后经过sio2衬底101及si纳米柱阵列102后在焦平面上形成了一个有缺陷的光斑,即单面超表面透镜在斜入射时存在像差,无法满足大视角成像。图3示例中,平行入射及斜入射的光先后经过si纳米柱阵列104,sio2衬底103,在焦平面上分别形成一个完整的光斑,能够很好的克服单面超表面透镜斜入射存在的像差问题,可实现大视角成像。因此,双面超表面结构受到越来越多的关注。
[0005]
由于大部分超表面结构最小线宽在百纳米级别,而双面光刻机最小线宽在微米(例如2微米)级别,因此受此双面光刻机最小线宽影响,无法直接使用双面光刻机进行正反套刻,同时大部分超表面结构衬底是不透明的,因此无法实现双面超表面结构高精度对准及对准精度的测量。
[0006]
基于此,对于有双面需求的超表面结构来说,提供一种高精度对准的双面超表面结构的制备方法实属必要。
技术实现要素:[0007]
鉴于以上所述现有技术的缺点,本发明的目的在于提供一种双面超表面结构的制备方法,用于解决现有技术中在制备双面超表面结构中,由于工艺线宽、材料的不透明性等的限制导致形成的双面超表面结构两面图形的对准精度差等的问题。
[0008]
为实现上述目的及其他相关目的,本发明提供一种双面超表面结构的制备方法,所述制备方法包括:
[0009]
提供第一光刻板及第二光刻板,所述第一光刻板上具有第一标记,所述第二光刻板上具有第二标记,所述第一标记与所述第二标记呈镜像关系,所述第一标记与所述第二标记具有正反对准功能、正反偏移误差测量功能及下一工艺步骤对准功能;
[0010]
提供衬底,并采用蒸镀或溅射金属的方式将所述第一光刻板上的所述第一标记的图形及所述第二光刻板上的所述第二标记的图形分别转移至所述衬底的正反两面,得到第一衬底样品;
[0011]
根据所述第一标记与所述第二标记的偏移误差测量功能,筛选出偏移误差在需求范围内的所述第一衬底样品,得到合格的第一衬底样品;
[0012]
提供双面超表面结构图形版图,并将所述合格的第一衬底样品放入下一步骤所用光刻设备中,采用所述光刻设备识别所述合格的第一衬底样品上具有下一工艺步骤对准功能的所述第一标记及所述第二标记,并将所述双面超表面结构图形版图分别转移至所述合格的第一衬底样品的正反两面,得到第二衬底样品;
[0013]
采用刻蚀工艺刻蚀所述第二衬底样品正反两面,得到双面超表面结构。
[0014]
可选地,所述第一标记与所述第二标记分别包括正反对准标记、正反偏移误差测量标记及下一工艺步骤对准标记;其中,所述正反对准标记实现正反对准功能,所述正反偏移误差测量标记实现正反偏移误差测量功能,所述下一工艺步骤对准标记实现下一工艺步骤对准功能。
[0015]
可选地,所述正反对准标记包括粗正反对准标记及高精度正反对准标记,所述正反偏移误差测量标记包括套刻标记。
[0016]
可选地,所述高精度正反对准标记的形状包括由十字标记型、梳齿标记型、套刻标记型、圆环标记型构成群组中的一种单标记型或两种以上的复合标记型;所述正反偏移误差测量标记的形状包括由十字标记型、梳齿标记型、套刻标记型、圆环标记型构成群组中的一种单标记型或两种以上的复合标记型。
[0017]
可选地,所述衬底的材料包括硅、二氧化硅、氮化镓、锗或氧化铝。
[0018]
本发明还提供另一种双面超表面结构的制备方法,所述制备方法包括:
[0019]
提供第一光刻板及第二光刻板,所述第一光刻板上具有第一标记,所述第二光刻板上具有第二标记,所述第一标记与所述第二标记呈镜像关系,所述第一标记与所述第二标记具有正反对准功能、正反偏移误差测量功能、下一工艺步骤对准功能及超表面结构对准测量参考功能;
[0020]
提供衬底,并采用蒸镀或溅射金属的方式将所述第一光刻板上的所述第一标记的图形及所述第二光刻板上的所述第二标记的图形分别转移至所述衬底的正反两面,得到第一衬底样品;
[0021]
根据所述第一标记与所述第二标记的偏移误差测量功能,筛选出偏移误差在需求范围内的所述衬底样品,得到合格的第一衬底样品;
[0022]
提供双面超表面结构图形版图,并将所述合格的第一衬底样品放入下一步骤所用光刻设备中,采用所述光刻设备识别所述合格的第一衬底样品上具有下一工艺步骤对准功能的所述第一标记及所述第二标记,并将所述双面超表面结构图形版图分别转移至所述合
格的第一衬底样品的正反两面,得到第二衬底样品;
[0023]
根据所述第一标记与所述第二标记的超表面结构对准测量参考功能,测量并计算出每一面的超表面结构图形与超表面结构对准测量参考功能的标记之间的相对位置偏移,再通过将两面的该相对位置偏移相减得出双面超表面结构之间的相对位置偏移,最后通过所述合格的第一衬底样品的偏移误差与该双面超表面结构之间的相对位置偏移的累加,得出双面超表面结构的对准偏移误差;
[0024]
采用刻蚀工艺刻蚀所述第二衬底样品正反两面,得到双面超表面结构。
[0025]
可选地,所述第一标记与所述第二标记分别包括正反对准标记、正反偏移误差测量标记、下一工艺步骤对准标记及超表面结构对准测量参考标记;其中,所述正反对准标记实现正反对准功能,所述正反偏移误差测量标记实现正反偏移误差测量功能,所述下一工艺步骤对准标记实现下一工艺步骤对准功能,所述超表面结构对准测量参考标记实现超表面结构对准测量的参考;所述超表面结构对准测量参考标记为正方形边框标记,且所述超表面结构图形版图套刻于所述超表面结构对准测量参考标记内部。
[0026]
可选地,采用电子束显微镜测量所述超表面结构图形边缘四个相同位置与所述正方形边框标记的内框之间的位置偏移,以在垂直方向得到两个位置偏移d1、d2,在水平方向得到两个位置偏移d3、d4;通过δx=(d1-d2)
÷
2及δy=(d3-d4)
÷
2得出每一面的超表面结构图形与超表面结构对准测量参考功能的标记之间在水平方向的相对位置偏移δx及垂直方向的相对位置偏移δy。
[0027]
本发明还提供再一种双面超表面结构的制备方法,所述制备方法包括:
[0028]
提供第一光刻板及第二光刻板,所述第一光刻板上具有第一标记,所述第二光刻板上具有第二标记,所述第一标记与所述第二标记呈镜像关系,所述第一标记与所述第二标记具有正反对准功能、正反偏移误差测量功能及下一工艺步骤对准功能;
[0029]
提供衬底,并采用蒸镀或溅射金属的方式将所述第一光刻板上的所述第一标记的图形及所述第二光刻板上的所述第二标记的图形分别转移至所述衬底的正反两面,得到第一衬底样品;
[0030]
根据所述第一标记与所述第二标记的偏移误差测量功能,筛选出偏移误差在需求范围内的所述衬底样品,得到合格的第一衬底样品;
[0031]
提供双面超表面结构图形版图,且在所述双面超表面结构图形版图镜像相同的空余位置设置超表面结构对准测量参考标记,并将所述合格的第一衬底样品放入下一步骤所用光刻设备中,采用所述光刻设备识别所述合格的第一衬底样品上具有下一工艺步骤对准功能的所述第一标记及所述第二标记,并将所述双面超表面结构图形版图分别转移至所述合格的第一衬底样品的正反两面,得到第二衬底样品;
[0032]
根据镜像的所述超表面结构对准测量参考标记直接测量得出双面超表面结构的对准偏移误差;
[0033]
采用刻蚀工艺刻蚀所述第二衬底样品正反两面,得到双面超表面结构。
[0034]
可选地,所述超表面结构对准测量参考标记的形状包括由十字标记型、梳齿标记型、套刻标记型、圆环标记型构成群组中的一种单标记型或两种以上的复合标记型。
[0035]
如上所述,本发明的双面超表面结构的制备方法,采用该制备方法制得的双面超表面结构的精度高;另外还可对双面超表面结构的对准精度进行测量并量化;最后,对双面
超表面结构对准精度的测量和量化方法简单,易于操作。
附图说明
[0036]
图1显示为现有技术中单面超表面结构聚焦水平入射平面电磁波的示意图。
[0037]
图2显示为现有技术中单面超表面结构聚焦斜入射平面电磁波的示意图。
[0038]
图3显示为现有技术中双面超表面结构聚焦水平入射与斜入射电磁波的示意图。
[0039]
图4显示为本发明实施例一的双面超表面结构的制备方法中第一光刻板上的第一标记设计示意图。
[0040]
图5显示为本发明实施例一的双面超表面结构的制备方法中第二光刻板上的第二标记设计示意图。
[0041]
图6显示为本发明实施例一的双面超表面结构的制备方法中第一光刻板上的第一标记与第二光刻板上的第二标记对准后的整体效果结构示意图。
[0042]
图7显示为本发明实施例二的双面超表面结构的制备方法中超表面结构对准测量参考标记示意图。
[0043]
图8显示为本发明实施例二的双面超表面结构的制备方法中第一光刻板上的第一标记与第二光刻板上的第二标记对准后的整体效果结构示意图。
[0044]
图9显示为本发明实施例二的双面超表面结构的制备方法中超表面结构图形与超表面结构对准测量参考标记相对位置示意图。
[0045]
图10显示为图9中虚线框a1处的放大图。
[0046]
图11显示为图10中虚线框b处的放大图。
[0047]
图12显示为本发明实施例三的双面超表面结构的制备方法中超表面结构版图示意图。
[0048]
元件标号说明
[0049]
101、103
ꢀꢀꢀꢀꢀꢀꢀꢀꢀꢀꢀꢀꢀꢀꢀ
sio2衬底
[0050]
102、104
ꢀꢀꢀꢀꢀꢀꢀꢀꢀꢀꢀꢀꢀꢀꢀ
si纳米柱阵列
[0051]
10
ꢀꢀꢀꢀꢀꢀꢀꢀꢀꢀꢀꢀꢀꢀꢀꢀꢀꢀꢀꢀꢀ
第一标记
[0052]
20
ꢀꢀꢀꢀꢀꢀꢀꢀꢀꢀꢀꢀꢀꢀꢀꢀꢀꢀꢀꢀꢀ
第二标记
[0053]
11、21
ꢀꢀꢀꢀꢀꢀꢀꢀꢀꢀꢀꢀꢀꢀꢀꢀꢀ
正反对准标记
[0054]
110、210
ꢀꢀꢀꢀꢀꢀꢀꢀꢀꢀꢀꢀꢀꢀꢀ
粗正反对准标记
[0055]
111、211
ꢀꢀꢀꢀꢀꢀꢀꢀꢀꢀꢀꢀꢀꢀꢀ
高精度正反对准标记
[0056]
12、22
ꢀꢀꢀꢀꢀꢀꢀꢀꢀꢀꢀꢀꢀꢀꢀꢀꢀ
正反偏移误差测量标记
[0057]
13、23
ꢀꢀꢀꢀꢀꢀꢀꢀꢀꢀꢀꢀꢀꢀꢀꢀꢀ
下一工艺步骤对准标记
[0058]
14、24
ꢀꢀꢀꢀꢀꢀꢀꢀꢀꢀꢀꢀꢀꢀꢀꢀꢀ
超表面结构对准测量参考标记
[0059]3ꢀꢀꢀꢀꢀꢀꢀꢀꢀꢀꢀꢀꢀꢀꢀꢀꢀꢀꢀꢀꢀꢀ
超表面结构图形
具体实施方式
[0060]
以下通过特定的具体实例说明本发明的实施方式,本领域技术人员可由本说明书所揭露的内容轻易地了解本发明的其他优点与功效。本发明还可以通过另外不同的具体实施方式加以实施或应用,本说明书中的各项细节也可以基于不同观点与应用,在没有背离
本发明的精神下进行各种修饰或改变。
[0061]
请参阅图4至图12。需要说明的是,本实施例中所提供的图示仅以示意方式说明本发明的基本构想,遂图示中仅显示与本发明中有关的组件而非按照实际实施时的组件数目、形状及尺寸绘制,其实际实施时各组件的型态、数量及比例可为一种随意的改变,且其组件布局型态也可能更为复杂。
[0062]
实施例一
[0063]
本实施例提供一种双面超表面结构的制备方法,所述制备方法包括:
[0064]
如图4至图6所示,首先进行步骤s1,提供第一光刻板及第二光刻板,所述第一光刻板上具有第一标记10(如图4所示),所述第二光刻板上具有第二标记20(如图5所示),所述第一标记10与所述第二标记20呈镜像关系,所述第一标记10与所述第二标记20具有正反对准功能、正反偏移误差测量功能及下一工艺步骤对准功能。
[0065]
这里需要说明的是,所述第一标记10及所述第二标记20还可以具有上述功能之外的其他功能,具体根据实际需要进行设置。
[0066]
所述第一标记10及所述第二标记20可以设置为一个标记多个功能,或者每个标记一个功能,标记的图形可根据工艺或精度任意设计,只要后续显微镜可以观察即可。
[0067]
如图4及图5所示,作为示例,所述第一标记10与所述第二标记20分别包括正反对准标记11、21、正反偏移误差测量标记12、22及下一工艺步骤对准标记13、23;其中,所述正反对准标记11、21实现正反对准功能,所述正反偏移误差测量标记12、22实现正反偏移误差测量功能,所述下一工艺步骤对准标记13、23实现下一工艺步骤对准功能。为进一步提高正反对准精度,所述正反对准标记11、21包括粗正反对准标记110、210及高精度正反对准标记111、211。这里需要指出的是,所述高精度正反对准标记111、211及所述正反偏移误差测量标记12、22在设计上有很大的灵活性,其形状可以采用现有的十字标记型、梳齿标记型、套刻标记型或圆环标记型的单标记型,也可是将单标记型进行组合形成的复合标记型。
[0068]
如图4及图5所示,本实施例中选择所述正反偏移误差测量标记12、22为套刻型标记,正反两个套刻型标记的线宽,在设计上设计为存在差值a,通过将线宽较窄的套刻型标记(如图5所示)套在线宽较宽的套刻型标记内,即可在显微镜下控制筛选出双面对准精度小于1/2a的样品。
[0069]
所述下一工艺步骤对准标记13、23在设计上灵活性也很大,其形状可以采用现有的十字标记型、梳齿标记型、套刻标记型或圆环标记型的单标记型,也可是将单标记型进行组合形成的复合标记型,如图4及图5所示,本实施例中选择所述下一工艺步骤对准标记13、23为适于ebl(电子束曝光)的十字标记型。另外,所述下一工艺步骤对准标记13、23并不仅限于图4及图5中所示的设置于所述正反对准标记11、21及所述正反偏移误差测量标记12、22附近一侧,其可根据实际情况设置于所述第一光刻板及第二光刻板上任意适宜的位置,在此不作限制。正反对准套刻后,正反面的完整标记如图6所示,此时根据所述正反偏移误差测量标记12、22筛选出高精度样品为后续双面超表面结构对准及测量的关键。
[0070]
然后进行步骤s2,提供衬底,并采用蒸镀或溅射金属的方式将所述第一光刻板上的所述第一标记10的图形及所述第二光刻板上的所述第二标记20的图形分别转移至所述衬底的正反两面,得到第一衬底样品。
[0071]
作为示例,不限制所述衬底的材料,例如可以为硅、二氧化硅、氧化镓、锗或氧化铝
等任意适合的材料。本实施例中选择所述衬底的材料为硅。
[0072]
这里以所述衬底为硅衬底为例对该步骤进行详细说明:在s1步骤完成所述第一光刻板及所述第二光刻板的制版后,使用其中一块光刻板,例如第一光刻板对硅衬底的其中一面进行光刻、显影并采用电子束蒸发的方式蒸镀约20nm厚的金层,蒸发完成后进行剥离、清洗后得到洁净的有第一标记10的结构的样品;然后在硅衬底的另一面进行上述步骤,得到洁净的有第二标记20的结构的样品,至此实现所述第一标记10的图形及所述第二标记20的图形在硅衬底两侧的转移。
[0073]
接着进行步骤s3,根据所述第一标记10与所述第二标记20的偏移误差测量功能,筛选出偏移误差在需求范围内的所述第一衬底样品,得到合格的第一衬底样品。
[0074]
这里以所述衬底为硅衬底为例对该步骤进行详细说明:由于常规显微镜下硅衬底不透明,无法观察到硅衬底反面图形,在红外显微镜下硅衬底透明,金属不透明,所以在红外显微镜下能清楚观察到硅衬底正反两面的金材料层标记。例如选择所述正反偏移误差测量标记12、22为套刻型标记,光刻板设计时,设计正反两个套刻型标记的线宽相差a,通过筛选线宽较窄的套刻型标记套在线宽较宽的套刻型标记内的第一衬底样品,能够确定正反面标记偏移误差小于1/2a。
[0075]
接着进行步骤s4,提供双面超表面结构图形版图,并将所述合格的第一衬底样品放入下一步骤所用光刻设备中,采用所述光刻设备识别所述合格的第一衬底样品上具有下一工艺步骤对准功能的所述第一标记10及所述第二标记20,并将所述双面超表面结构图形版图分别转移至所述合格的第一衬底样品的正反两面,得到第二衬底样品。
[0076]
这里以采用ebl工艺为例对该步骤进行详细说明:步骤s3结束后,将所述合格的第一衬底样品放入下一步骤所用ebl光刻设备中,先识别其中一面的下一工艺步骤对准标记,根据不同的光刻设备,选择不同的标记及其图形,本实施例选择ebl光刻设备,选择使用十字形标记作为对准标记;然后采用电子束光刻并显影,通过电子束蒸发的方式,蒸发厚度约20nm厚的铬层作为硬掩膜层,剥离清洗完成后,实现将双面超表面结构图形版图中的一面图形转移至所述合格的第一衬底样品上;然后在所述合格的第一衬底样品的另一面上进行上述步骤,实现将双面超表面结构图形版图中的另一面图形转移至所述合格的第一衬底样品上,至此实现所述双面超表面结构图形版图转移至所述合格的第一衬底样品的正反两面。
[0077]
最后进行步骤s5,采用刻蚀工艺刻蚀所述第二衬底样品正反两面,得到双面超表面结构。
[0078]
这里需要注意的是,在对所述第二衬底样品的一面进行刻蚀工艺时,要注意对其另一面的图案进行保护。
[0079]
采用本实施例的双面超表面结构的制备方法,能够成功制作出高精度对准的双面超表面结构,从而提高双面超表面结构的性能。
[0080]
实施例二
[0081]
本实施例提供一种双面超表面结构的制备方法,该制备方法与实施例一基本相同,不同在于:步骤s1中提供的第一光刻板上的第一标记10及第二光刻板上的第二标记20还具有超表面结构对准测量参考功能;在得到第二衬底样品后,可以根据该超表面结构对准测量参考功能的标记,得出双面超表面结构的对准偏移误差,具体地:根据所述第一标记
10与所述第二标记20的超表面结构对准测量参考功能,测量并计算出每一面的超表面结构图形与超表面结构对准测量参考功能的标记之间的相对位置偏移,再通过将两面的该相对位置偏移相减得出双面超表面结构之间的相对位置偏移,最后通过所述合格的第一衬底样品的偏移误差与该双面超表面结构之间的相对位置偏移的累加,得出双面超表面结构的对准偏移误差。
[0082]
如图7所示,作为示例,所述第一光刻板上的第一标记10及所述第二光刻板上的第二标记20上设有超表面结构对准测量参考功能标记14、24。
[0083]
如图7至图9所示,下面以采用直径约为500μm的超表面结构图形3、所述正反偏移误差测量标记12、22为套刻型标记、所述超表面结构对准测量参考功能标记14、24为边长稍大于超表面结构图形3直径的正方形边框为例对双面超表面结构的对准偏移误差的测量和计算进行描述:如图9所示,采用电子束显微镜测量一面所述超表面结构图形边缘四个相同位置(如图中的虚线框a1、a2、a3、a4)与所述正方形边框标记的内框之间的位置偏移(如图11所示),以在垂直方向得到两个位置偏移d1、d2,在水平方向得到两个位置偏移d3、d4;通过δx=(d1-d2)
÷
2及δy=(d3-d4)
÷
2得出该面的超表面结构图形3与超表面结构对准测量参考功能标记14之间在水平方向的相对位置偏移δx1及垂直方向的相对位置偏移δy1,同理获得另一面的超表面结构图形3与超表面结构对准测量参考功能标记24之间在水平方向的相对位置偏移δx2及垂直方向的相对位置偏移δy2;再通过将两面的该相对位置偏移相减,得出双面超表面结构之间在水平方向及垂直方向的相对位置偏移δx1-δx2、δy1-δy2;然后通过所述合格的第一衬底样品的偏移误差(例如小于1/2a)与该双面超表面结构之间在水平方向及垂直方向的相对位置偏移的累加,得出双面超表面结构在水平方向及垂直方向的对准偏移误差。
[0084]
采用本实施例的双面超表面结构的制备方法,不仅能够成功制作出高精度对准的双面超表面结构,并能对双面超表面结构的对准精度进行测量并量化。
[0085]
实施例三
[0086]
如图12所示,本实施例提供一种双面超表面结构的制备方法,该制备方法与实施例一基本相同,不同在于:步骤s4中,本实施例提供的双面超表面结构图形版图,在所述双面超表面结构图形版图镜像相同的空余位置还设置有超表面结构对准测量参考标记;在得到第二衬底样品后,可根据镜像的所述超表面结构对准测量参考标记直接测量双面超表面结构的对准偏移误差。
[0087]
作为示例,所述超表面结构对准测量参考功能标记14、24在设计上灵活性很大,其形状可以采用现有的十字标记型、梳齿标记型、套刻标记型或圆环标记型的单标记型,也可是将单标记型进行组合形成的复合标记型(如图12所示),只要显微镜下能够分辨出或读出偏移误差即可,例如,可以选择所述超表面结构对准测量参考功能标记14、24为套刻标记型,使正反两个套刻标记型的线宽,在设计上设计为存在差值b,当线宽较窄的套刻型标记套在线宽较宽的套刻型标记内时,即可在显微镜下测量出双面超表面结构的对准偏移误差小于1/2b。本实施例中选择所述超表面结构对准测量参考功能标记14、24为复合标记型,以提高测量精度。
[0088]
采用本实施例的双面超表面结构的制备方法,不仅能够成功制作出高精度对准的双面超表面结构,并能对双面超表面结构的对准精度进行测量并量化,另外本实施例对双
面超表面结构对准精度的测量和量化方法简单,易于操作。
[0089]
综上所述,本发明提供一种双面超表面结构的制备方法,采用本制备方法制得的双面超表面结构的精度高;另外还可对双面超表面结构的对准精度进行测量并量化;最后,对双面超表面结构对准精度的测量和量化方法简单,易于操作。所以,本发明有效克服了现有技术中的种种缺点而具高度产业利用价值。
[0090]
上述实施例仅例示性说明本发明的原理及其功效,而非用于限制本发明。任何熟悉此技术的人士皆可在不违背本发明的精神及范畴下,对上述实施例进行修饰或改变。因此,举凡所属技术领域中具有通常知识者在未脱离本发明所揭示的精神与技术思想下所完成的一切等效修饰或改变,仍应由本发明的权利要求所涵盖。