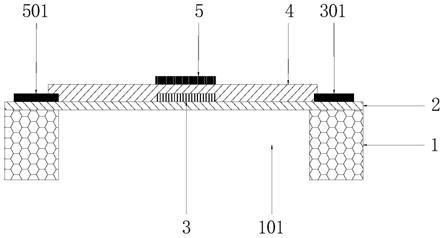
一种陶瓷悬梁式mems微热板及其制造方法
技术领域
[0001]
本发明涉及传感器技术领域,具体涉及一种陶瓷悬梁式mems微热板及其制造方法。
背景技术:[0002]
微热板作为一种常用的微型加热平台,它的基本结构包括悬空介质薄膜以及薄膜电阻线条。当电流通过薄膜电阻线条时,电阻产生的焦耳热一部分用于加热微热板,另一部分以传导、对流和热辐射的形式耗散于周围环境中。
[0003]
随着mems技术和微电子技术的不断发展,微热板因为其阵列化制作工艺、体积小,功耗低并且易于其他材料结合的巨大优势得到广泛应用,比如微型气体传感器,微加速计、微气压计以及薄膜量热卡计等。其中微热板在微型气体传感器的应用中占比最大。
[0004]
在现有技术中,微热板的主要研究重点是尽可能的降低功耗,一方面,通过在加热层底部加入真空隔热层、隔热沟槽或者其他材质的隔热层。例如发明专利201710126277.2和发明专利201420399824.6公开的。另一方面,也有研究者通过降低目标导热的热损,来降低功耗,例如发明专利201920113696.7所公开的在加热电极和插齿电极层中间加入一层即具有极高导热性又绝缘的金刚石层,最终起到减低功耗的效果。
[0005]
这些微热板研究方向中,大多数为悬膜式微热板,因为悬膜式微热板的具有较低的热损而备受追崇。然而悬膜式微热板在使用过程中,因为长期的通电断电导致的热胀冷缩会将悬膜结构变得翘曲不平,从而引起很多不利影响,比如说加热丝阻值变化,气体传感器使用中敏感材料的脱落等。
技术实现要素:[0006]
本发明解决的技术问题是提供一种采用具有更低导入系数和更坚硬的陶瓷作为悬梁结构的mems微热板。
[0007]
本发明解决其技术问题所采用的技术方案是:
[0008]
一种陶瓷悬梁式mems微热板制造方法,其特征在于:包括以下步骤:
[0009]
s1:清洁单晶硅衬底;
[0010]
s2:制备陶瓷悬梁层,印刷:将陶瓷浆料以规则图案印刷在所述单晶硅衬底上;烘干:再将印刷后的所述陶瓷浆料进行初步烘干;煅烧:最后将初步烘干后的所述陶瓷浆料进行煅烧,形成陶瓷层;
[0011]
s3:制备加热丝层及其电极端,在所述陶瓷层上通过匀胶光刻技术定义出加热层及其电极端的形状及位置,在利用磁控溅射技术沉积一层金属加热丝层及其电极端,最后利用剥离工艺去除残留的光刻胶;
[0012]
s4:制备绝缘层,采用气相沉积法在所述加热丝层上沉积一层绝缘层;
[0013]
s5:制备测试层及其电极端,采用所述s5步骤制备测试层及其电极端;
[0014]
s6:蚀刻成型,采用湿法蚀刻,在所述单晶硅衬底背面指定位置用浓硫酸刻穿,得
到所述陶瓷悬梁式微热板。
[0015]
进一步地,所述步骤s2中的所述陶瓷悬梁层的悬梁结构的宽度为所述微热板宽度的2%-30%。
[0016]
进一步地,所述步骤s3中的烘干温度为50-200℃,时间为2-24h;煅烧温度为450-1400℃,时间为2-24h。。
[0017]
一种陶瓷悬梁式mems微热板,其特征在于:包括:单晶硅衬底;
[0018]
陶瓷悬梁层,通过印刷、烘干、煅烧在所述单晶硅衬底上;
[0019]
加热丝层及其电极端,通过磁控溅射沉积在所述陶瓷悬梁层上;
[0020]
绝缘层,通过气相沉积法沉积在所述加热丝层上;
[0021]
测试层及其电极端,通过磁控溅射沉积在所述绝缘层上;
[0022]
所述单晶硅衬底指定位置处刻使所述陶瓷悬梁层的陶瓷悬梁结构悬空成型。
[0023]
进一步地,所述陶瓷悬梁层为i形的两组悬梁或者x形的四组悬梁。
[0024]
进一步地,,所述陶瓷悬梁层的厚度为50-800μm。
[0025]
进一步地,所述加热丝层和所述测试层的厚度为50-500nm。
[0026]
进一步地,所述绝缘层的厚度为100-800nm。
[0027]
进一步地,所述绝缘层为氧化硅层或氮化硅层。
[0028]
本发明的有益效果是:
[0029]
1.采用具有更低导热系数和更坚硬的陶瓷材料作为mems微热板的悬梁结构,比传统的开隔热槽单晶硅悬梁微热板而言,隔热效果显著,整体结构更可靠,而且通过陶瓷悬梁有效能够降低自身功耗。
[0030]
2.采用印刷、烘干和煅烧工艺将陶瓷与单晶硅衬底相结合,工艺简单可靠,成本更低。
附图说明
[0031]
图1为本发明的结构示意图;
[0032]
图2为本发明实施例四悬梁制备方法示意图;
[0033]
图3为本发明实施例两组悬梁制备方法示意图;
[0034]
图4为本发明应用示意图;
[0035]
图中标记为:
[0036]
1、单晶硅衬底,2、陶瓷悬梁层,3、加热丝层,4、绝缘层,5、测试层,101、空腔,201、悬梁结构,301、加热丝电极端,501、测试层电极端,6、敏感材料。
具体实施方式
[0037]
为使本发明的上述目的、特征和优点能够更加明显易懂,下面结合附图对本发明的具体实施方式做详细的说明。在下面的描述中阐述了很多具体细节以便于充分理解本发明。但是本发明能够以很多不同于在此描述的其它方式来实施,本领域技术人员可以在不违背本发明内涵的情况下做类似改进,因此本发明不受下面公开的具体实施例的限制。
[0038]
需要说明的是,当元件被称为“固定于”另一个元件,它可以直接在另一个元件上或者也可以存在居中的元件。当一个元件被认为是“连接”另一个元件,它可以是直接连接
到另一个元件或者可能同时存在居中元件。
[0039]
除非另有定义,本文所使用的所有的技术和科学术语与属于本发明的技术领域的技术人员通常理解的含义相同。本文中在本发明的说明书中所使用的术语只是为了描述具体的实施例的目的,不是旨在于限制本发明。本文所使用的术语“及/或”包括一个或多个相关的所列项目的任意的和所有的组合。
[0040]
一种陶瓷悬梁式mems微热板,如图1所示,包括单晶硅衬底1、陶瓷悬梁层2、加热丝层3、绝缘层4和测试层5。陶瓷悬梁层2通过印刷、烘干、煅烧在单晶硅衬底1上,加热丝层3通过匀胶光刻技术定义其形状、在通过磁控溅射技术沉积在陶瓷悬梁层2上,绝缘层4通过pecvd(气相沉积法)沉积在加热丝层2上,测试层5通过匀胶光刻技术定义其形状、在通过磁控溅射技术沉积在陶瓷绝缘层4上,测试层5采用叉齿电极作为测试层,单晶硅衬底1背面刻穿成型形成空腔101,使陶瓷悬梁层2的陶瓷悬梁结构201悬空成型。
[0041]
本发明中,陶瓷悬梁层2可以采用i形的两组陶瓷悬梁,或者采用x形的四组陶瓷悬梁,i形陶瓷悬梁中间宽度扩大作为功能区,x型陶瓷悬梁中间交叉部作为功能区,功能区上面用于制备上述加热层、绝缘层和测试层。
[0042]
前述陶瓷悬梁层2的厚度为50-800μm,加热丝层3和测试层5的厚度为50-500nm,绝缘层4的厚度为100-800nm,绝缘层4采用具有良好结构强度和绝缘隔热性能的氧化硅层或者氮化硅层作为绝缘层。
[0043]
如图2所示,为本发明陶瓷悬梁式mems微热板的制作方法如下:
[0044]
s1:清洁单晶硅衬底1;利用酸溶液、有机溶剂和去离子水等容易对单晶硅衬底进行清洗,然后吹干,单晶硅衬底的尺寸为常用尺寸,可以为2寸、4寸、6寸或8寸等。
[0045]
s2:制备陶瓷悬梁层2,印刷:将陶瓷浆料以规则图案印刷在所述单晶硅衬底上,采用两组悬梁或者四组悬梁结构;将陶瓷浆料通过丝网印刷方式,在单晶硅衬底1上图案化,陶瓷浆料为玻璃、陶瓷材料和有机溶剂按照比例混合而成,印刷厚度为50-800微米,悬梁的样式如图2中的s2所示。其中,陶瓷悬梁层的悬梁结构的宽度为本发明微热板宽度的2%-30%,优先采用宽度为3.4%。烘干:然后将印刷后的所述陶瓷浆料进行初步烘干;烘干温度为50-200℃,时间2-24h。煅烧:最后将初步烘干后的所述陶瓷浆料进行煅烧,形成陶瓷层;煅烧温度为450-1400℃,时间2-24h。煅烧有利于悬梁陶瓷层2紧密坚硬、并且可以与单晶硅衬底1具有良好的附着力,保证陶瓷层的可靠性和稳定性。
[0046]
s3:制备加热丝层3及其电极端301,在所述陶瓷悬梁层上通过匀胶光刻技术定义出加热层及其电极端的形状及位置,在利用磁控溅射技术沉积一层金属加热丝层及其电极端,在利用剥离工艺去除残留的光刻胶;金属加热丝采用金属铂或者金沉积。
[0047]
s6:制备绝缘层4,采用气相沉积法在所述加热丝层上沉积一层绝缘层;采用pecvd技术,保持单晶硅衬底温度为100-380℃,沉积一层厚度为100-800nm的氧化硅层或者氮化硅层。
[0048]
s7:制备测试层5及其电极端501,采用所述s5步骤制备测试层及其电极端;沉积测试层后,也通过玻璃工艺去除残留的光刻胶。
[0049]
s8:蚀刻成型,采用湿法蚀刻,在所述单晶硅衬底背面制定位置用浓硫酸刻穿,得到所述陶瓷悬梁式微热板。
[0050]
如图3所示,为本发明两组陶瓷悬梁结构的制备方法流程示意图。
[0051]
如图4所示,为本发明应用示意图,后期再测试层5上涂覆敏感材料6,即可形成陶瓷悬梁气体传感器,再将其进行封装成型即可。
[0052]
实施例1:
[0053]
s1:清洁单晶硅衬底1;选择8寸的单晶硅衬底,利用酸溶液、有机溶剂和去离子水等容易对单晶硅衬底进行清洗,然后吹干。
[0054]
s2:制备陶瓷悬梁层2,印刷:将陶瓷浆料以规则图案印刷在当晶硅衬底1上,规则图案的中为x形四悬梁结构,印刷厚度为50-100μm,悬梁的样式如图2中的s2所示。烘干:之后将印刷后的所述陶瓷浆料进行初步烘干;烘干温度为200℃。煅烧:最后将初步烘干后的所述陶瓷浆料进行煅烧,形成陶瓷层;煅烧温度为1200℃。煅烧有利于悬梁陶瓷层2紧密坚硬、并且可以与单晶硅衬底1具有良好的附着力,保证陶瓷层的可靠性和稳定性。
[0055]
s3:制备加热丝层3及其电极端301,在所述陶瓷悬梁层上通过匀胶光刻技术定义出加热层及其电极端的形状及位置,在利用磁控溅射技术沉积一层50-100nm的金属加热丝层及其电极端,在利用剥离工艺去除残留的光刻胶;金属加热丝采用金属铂或者金沉积。
[0056]
s6:制备绝缘层4,采用气相沉积法在所述加热丝层上沉积一层绝缘层;采用pecvd技术,保持单晶硅衬底温度为100-380℃,沉积一层厚度为100-200nm的氧化硅层或者氮化硅层。
[0057]
s7:制备测试层5及其电极端501,采用所述s5步骤制备测试层及其电极端;沉积测试层后,也通过玻璃工艺去除残留的光刻胶。
[0058]
s8:蚀刻成型,采用湿法蚀刻,在所述单晶硅衬底背面制定位置用浓硫酸刻穿,得到所述陶瓷悬梁式微热板。
[0059]
实施例2:
[0060]
s1:清洁单晶硅衬底1;选择8寸的单晶硅衬底,利用酸溶液、有机溶剂和去离子水等容易对单晶硅衬底进行清洗,然后吹干。
[0061]
s2:制备陶瓷悬梁层2,印刷:将陶瓷浆料以规则图案印刷在当晶硅衬底1上,规则图案的中为x形四悬梁结构,印刷厚度为700-800μm,悬梁的样式如图2中的s2所示。烘干:之后将印刷后的所述陶瓷浆料进行初步烘干;烘干温度为200℃。煅烧:最后将初步烘干后的所述陶瓷浆料进行煅烧,形成陶瓷层;煅烧温度为1200℃。煅烧有利于悬梁陶瓷层2紧密坚硬、并且可以与单晶硅衬底1具有良好的附着力,保证陶瓷层的可靠性和稳定性。
[0062]
s3:制备加热丝层3及其电极端301,在所述陶瓷悬梁层上通过匀胶光刻技术定义出加热层及其电极端的形状及位置,在利用磁控溅射技术沉积一层400-500nm的金属加热丝层及其电极端,在利用剥离工艺去除残留的光刻胶;金属加热丝采用金属铂或者金沉积。
[0063]
s6:制备绝缘层4,采用气相沉积法在所述加热丝层上沉积一层绝缘层;采用pecvd技术,保持单晶硅衬底温度为100-380℃,沉积一层厚度为700-800nm的氧化硅层或者氮化硅层。
[0064]
s7:制备测试层5及其电极端501,采用所述s5步骤制备测试层及其电极端;沉积测试层后,也通过玻璃工艺去除残留的光刻胶。
[0065]
s8:蚀刻成型,采用湿法蚀刻,在所述单晶硅衬底背面制定位置用浓硫酸刻穿,得到所述陶瓷悬梁式微热板。
[0066]
以上所述的具体实施例,对本发明的目的、技术方案和有益效果进行了进一步详
细说明,所应理解的是,以上所述仅为本发明的具体实施例而已,并不用于限制本发明,凡在本发明的精神和原则之内,所做的任何修改、等同替换、改进等,均应包含在本发明的保护范围之内。