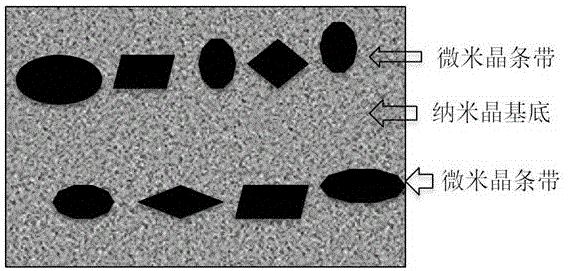
本发明涉及一种高性能铜箔材料的制备方法,尤其是一种兼具高强度与高塑性的铜箔及其制备方法。
背景技术:
:铜箔广泛运用与工业生产中,例如大量用作各种导电极片,以及用作线路板材料等。在线路板材料中,铜箔的强度是比较重要的性能参数。强度越高,则意味着可以制备更薄的铜箔,这样一来可以减少铜箔的用量,降低成本,二来可以提高产品的性能。因此,提高铜箔的强度一直在研究当中。发明CN102925832A提供一种制备超细孪晶铜的大塑性变形法,包括异步叠轧步骤及其后的热处理退火工艺,经过原材料的制备、均匀化退火、表面打磨、异步叠轧变形退火后,即得到超细孪晶铜材。该发明采用大变形异步叠轧技术辅以退火热处理,依靠异步叠轧过程中的剪切应力和累积应变效应促进材料内部的堆垛错排和晶粒的细化,再通过退火热处理工艺促进孪晶的形成,为金属材料的强化技术的深入研究提供一种新的连续制备方法。本发明保持了在加工前后材料的形状及尺寸未发生变化,克服了常规轧制制备板材厚度方向上总应变的限制,增大了变形量,提高了产品表面的质量,具有生产率高,工艺简单,可以生产大尺寸的金属板材,易于实现工业化生产。发明CN102161051A提供一种在金属板材表面形成纳米结构的异步轧制方法,其特征在于:所述方法利用异步轧制的搓轧方式对金属板材进行多道次轧制从而在金属板材表面形成纳米结构,其具体的操作如下:a、选取表面光洁的金属板材作为基材;b、调整异步轧机的上工作辊与下工作辊的周向速比在1∶1.05~1∶1.35之间;c、对金属板材进行多道次轧制,相邻道次之间轧制方向相反;每一道次压下量为金属板材厚度的1~30%。该发明利用异步轧制的方法来解决以往方法中存在的问题,其操作简洁,效果明显,利于在实际的生产中推广应用。技术实现要素::发明目的:为了提高铜箔的力学强度,本发明提供了一种同时提高铜箔强度的方法。本方法结合多次电解制造晶粒度分层的电解铜箔,然后采用微变形异步轧制的方法加工而成。最终铜箔在组织上的特征在于:其显微组织中的晶粒由两种不同粒度范围的晶粒组成,一种为常规的微米晶,一种为纳米晶;纳米晶的粒度范围是10-200纳米,微米晶的粒度范围是0.5微米-10微米。其中纳米晶的体积分数60%以上,微米晶的体积分数在40%以下,微米晶分布在纳米晶中,并且呈显出条带状分布。该铜箔的强度高,而且塑性优异。本发明的技术方案如下:采用可控条件电解的方法,制备不同晶粒大小的铜箔,然后在室温下采用异步轧制的方法,制备一种高强度的铜箔材料。具体制备方法包括以下步骤:1.采用电解的方式制备铜箔,通过控制制备条件,如改变温度、浓度等参数,制备出晶粒大小不均匀的铜箔,晶粒较粗大的一面为铜层1,晶粒较细小的为铜层2。2.启动多功能轧机系统,设定上下轧辊的速比,速比为1.1-1.5;设定每次轧制形变量为1-8%;设定低速辊的速度为0.5-2米/秒;3.启动主传动电机,开始轧制过程。其中晶粒较细小的一面与快速辊接触。4.待一次轧制过后,重复轧制10次以上;5.进行重结晶退火热处理,重结晶温度为该铜箔熔点的250到350摄氏度,时间3-20分钟。步骤1中电解铜箔的制备过程如下:铜箔的制备采用电解方法进行,其装置由阴极、阳极、电解液构成。当向阴、阳极间的电解液通以电流时,铜便从阴极上析出。采用含铜离子的盐溶液作为电解液,例如硫酸铜溶液。当铜达到一定厚度时,然后可以将铜从阴极上剥离。可以通过改变硫酸、铜、氯离子的浓度、电流密度、电解液的温度来调节铜的晶粒度。初始状态:铜的浓度为60-100g/l,硫酸浓度为40-100g/l,Cl的浓度为20-50ppm,温度为40摄氏度,电流密度为40-50A/dm2,当铜箔厚度达到50-500微米时,得到铜层1,然后调整参数,电解得到铜层2。有益的效果:采用本发明制备的铜箔,其组织结构中既有微米晶,又有纳米晶,可以兼具微米晶优秀的塑性与纳米晶优异的强度。事实上,全由纳米晶构成的金属材料,不仅难于制备,而且塑性极差。而本发明制备的材料,不仅强度高,而且塑性高,在强度上甚至要优于纳米晶。其根源在于这种材料结构可以达到极大的背加工硬化,产生明显的包申格效应。此外,本发明采用室温轧制,比较节约能源,成本低、适于大规模生产。具体实施方式下面通过结合附图与实施例详细描述本发明的制备方法,但不构成对本发明的限制。图1为本发明的显微组织图,较大的为微米晶,呈条带状分布在细小的纳米晶中。实施例11.配置硫酸铜溶液:铜的浓度为60g/l,硫酸浓度为70g/l,Cl的浓度为30ppm,温度为40摄氏度,电流密度为40A/dm2,当铜箔厚度达到到250微米时,得到铜层1,然后将电流密度改为60A/dm2,得到铜层2,厚度260微米;2.启动多功能轧机系统,设定上下轧辊的速比,速比为1.3;设定每次轧制形变量为2%;设定低速辊的速度为2米/秒;3.启动主传动电机,开始轧制过程,其中铜层2与快速辊接触;4.待一次轧制过后,重复轧制10次;5.进行重结晶退火热处理,重结晶温度为280摄氏度,时间10分钟;组织分析:微米晶的平均晶粒大小为3微米,纳米晶的平均粒径为130纳米。实施例21.配置硫酸铜溶液:铜的浓度为100g/l,硫酸浓度为60g/l,Cl的浓度为50ppm,温度为40摄氏度,电流密度为50A/dm2,当铜层厚度达到120微米时,得到铜层1,然后将电流密度改为80A/dm2,得到铜层2,厚度130微米;2.启动多功能轧机系统,设定上下轧辊的速比,速比为1.2;设定每次轧制形变量为2%;设定低速辊的速度为1米/秒;3.启动主传动电机,开始轧制过程,其中铜层2与快速辊接触;4.待一次轧制过后,重复轧制12次;5.进行重结晶退火热处理,重结晶温度为280摄氏度,时间3分钟。组织分析:微米晶的平均晶粒大小为8.5微米,纳米晶的平均粒径为80纳米。实施例31.配置硫酸铜溶液:铜的浓度为60g/l,硫酸浓度为40g/l,Cl的浓度为20ppm,温度为40摄氏度,电流密度为50A/dm2,当铜箔厚度达到50微米时,得到铜层1,然后将电流密度改为60A/dm2,得到铜层2,厚度60微米;2.启动多功能轧机系统,设定上下轧辊的速比,速比为1.1;设定每次轧制形变量为6%;设定低速辊的速度为2米/秒;3.启动主传动电机,开始轧制过程,其中铜层2与快速辊接触;4.待一次轧制过后,重复轧制15次;5.进行重结晶退火热处理,重结晶温度为300摄氏度,时间3分钟。组织分析:微米晶的平均晶粒大小为2.2微米,纳米晶的平均粒径为180纳米。实施例41.配置硫酸铜溶液:铜的浓度为60g/l,硫酸浓度为100g/l,Cl的浓度为50ppm,温度为40摄氏度,电流密度为50A/dm2,当铜箔厚度达到350微米时,得到铜层1,然后将电流密度改为80A/dm2。得到铜层2,厚度300微米。2.启动多功能轧机系统,设定上下轧辊的速比,速比为1.2;设定每次轧制形变量为4%;设定低速辊的速度为0.5米/秒;3.启动主传动电机,开始轧制过程,其中铜层2与快速辊接触;4.待一次轧制过后,重复轧制13次;5.进行重结晶退火热处理,重结晶温度为280摄氏度,时间10分钟。组织分析:微米晶的平均晶粒大小为0.94微米,纳米晶的平均粒径为36纳米。实施例51.配置硫酸铜溶液:铜的浓度为90g/l,硫酸浓度为50g/l,Cl的浓度为40ppm,温度为40摄氏度,电流密度为40A/dm2,当铜箔厚度达到500微米时,得到铜层1,然后将电流密度改为80A/dm2,得到铜层2,厚度490微米;2.启动多功能轧机系统,设定上下轧辊的速比,速比为1.5;设定每次轧制形变量为1%;设定低速辊的速度为0.5米/秒;3.启动主传动电机,开始轧制过程,其中铜层2与快速辊接触;4.待一次轧制过后,重复轧制15次;5.进行重结晶退火热处理,重结晶温度为250摄氏度,时间20分钟。组织分析:微米晶的平均晶粒大小为1.7微米,纳米晶的平均粒径为68纳米。性能测试:采用万能试验机进行铜箔拉伸试验,其结果如下表所示。可以看出,本发明的铜箔在大幅度提高强度的同时,保持了优异的塑性。实施例1实施例2实施例3实施例4实施例5常规铜纳米铜屈服强度(MPa)876910854930905200-400~800延伸率39%37%41%41%38%30~40<3以上所述仅是本发明实施方式的一些例子,应当指出:对于本
技术领域:
的技术人员来说,在不脱离本发明原理的前提下,还可以做出若干改进和润饰,这些改进和润饰也应视为本发明的保护范围。当前第1页1 2 3