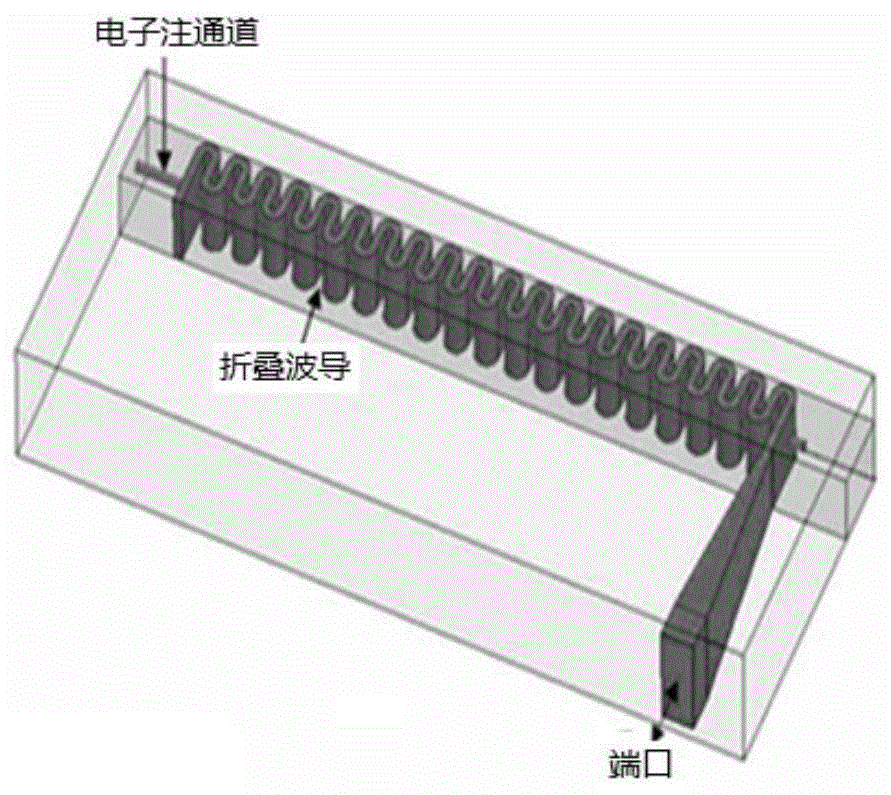
本发明涉及真空电子器件领域。更具体地,涉及一种真空器件用的耐高温的互作用电路零部件的加工方法。
背景技术:
:太赫兹真空器件具有功率大、频带宽等优点,在雷达、制导、战术和战略通信、电子对抗、遥感、辐射测量等方面得到了广泛应用。随着频率的提高,太赫兹真空器件的零部件尺寸已经达到几十微米量级,同时为了减小传输损耗,要求结构表面粗糙度在几十到几百纳米量级,这给研制带来种种困难,特别是太赫兹行波管中采用的电子和电磁场的互作用电路、衰减器和输能耦合系统的加工制造更是如此。电子和电磁场的互作用电路是太赫兹行波管的重要部件之一。为了使行波管能稳定工作,并提供良好的电性能参数,良好的散热,互作用电路必须是全铜结构,能耐高温、耐电子轰击,尺寸精度高,表面光洁度高,传输损耗小等特点,而且还应该具有足够的结构强度和真空密封性能。对于太赫兹行波管而言,电子和电磁波的互作用电路一般采用折叠波导形式,折叠波导结构如图1所示。表1给出频率从94ghz到560ghz不同频率下折叠波导结构的典型尺寸。传统的精密加工方法已经不能满足要求,这就要求采用新的加工技术以保证很高的尺寸精度和表面光洁度。基于mems加工技术的新的加工技术被引入来加工上述频段的折叠波导结构。与mems器件相比,真空用的折叠波导结构有以下几个特点:深宽比不大,一般只能到5左右,但是绝对深度的尺寸(如折叠波导宽边尺寸的一半)比较大,在w波段可以达到950微米,560ghz可以达到150微米;折叠波导结构要有良好的散热,而且在高温焊接时折叠波导结构不产生形变。表1不同频率行波管中互作用电路的典型尺寸频率(ghz)宽边尺寸(μm)窄边尺寸(μm)941900300140135024022076016034050010056030040技术实现要素:基于以上事实,本发明的一个目的在于提供一种真空器件用的耐高温的零部件的加工方法,以解决现有技术中难以获得耐高温性好的太赫兹频段真空电子器件用零部件的技术问题。为达到上述目的,本发明采用下述技术方案:一种真空器件用的耐高温的零部件的加工方法,包括如下步骤:在无氧铜基底上涂覆光刻胶,经曝光、显影,得具有光刻胶图形的无氧铜基底;在所述具有光刻胶图形的无氧铜基底上微电铸一层铜,其中,微电铸的条件包括:微电铸的电铸液中,铜离子含量为18-25g/l,硫酸含量为170-220g/l,氯离子含量为50-70mg/l;去除微电铸后得到的结构中的光刻胶,得所述真空器件用的耐高温的零部件。上述加工方法中,在去除微电铸后得到的结构中的光刻胶后,还可以根据实际需要,选择是否切割外形,以获得所需真空器件用的耐高温的零部件。本发明的加工方法中,微电铸的电铸液(硫酸盐铸铜溶液)中各离子的浓度对前述效果影响明显,在该电铸条件下,得到的电铸层晶粒排列紧密,晶粒细小,可达到194nm以下。通过采用光刻结合微电铸的方法,并进一步结合上述特定的微电铸条件,从而使得电铸层与基底层结合紧密,得到的结构耐高温性以及耐电子轰击效果均好,制备得到的零部件耐高温,高温作业不变形,含氧量低,耐电子轰击效果好,能很好的用于太赫兹频段真空电子器件中。进一步地,所述微电铸的电铸液中,铜离子含量为19-24g/l,硫酸含量为180-210g/l,氯离子含量为50-70mg/l。进一步地,所述微电铸的温度为20-40℃,阳极电流密度0.5-1.5a/dm2。进一步地,所述微电铸的频率为500hz-5khz,更优选地,所述微电铸的频率为1khz-2khz。采用该较小的特定的电铸频率,结合电铸液条件,从而使得得到的电铸层晶粒排列紧密,晶粒更细小。进一步地,所述无氧铜基底表面粗糙度ra为2nm-50nm。其中,可通过研磨抛光来控制无氧铜基底的表面粗糙度。为了便于加工,无氧铜基底的形状可为圆柱形,厚度为5-10mm,直径为3英寸或4英寸。进一步地,所述光刻胶可为az系列,su8系列的光刻胶。可以理解,当光刻胶为正光刻胶时,经曝光、显影后得到的光刻胶图案与掩膜板的形状相同;当光刻胶为负光刻胶时,经曝光、显影后得到的光刻胶图案与掩膜板的形状互补。进一步地,在所述曝光前,还包括前烘的步骤,所述前烘的温度为95-130℃,时间为0-20小时。进一步地,在所述曝光后、显影前,还包括后烘的步骤,所述后烘的温度为50-95℃,时间为0.5-4小时。通过光刻、显影在无氧铜基底上形成光刻胶图形,从而能更好的保证后续的微电铸的质量。进一步地,微电铸的过程中,电铸上的铜层的厚度与光刻胶图形的厚度相同。再通过研磨抛光,获得实际需要的铜层的厚度,同时可控制铜层表面粗糙度ra为2nm-50nm。进一步地,在无氧铜基底上涂覆的光刻胶的厚度为0-1000μm,优选为0.1-1000μm。进一步地,所述零部件为电子和电磁场互作用的电路。示例性地电子和电磁场互作用的电路为折叠波导。本发明的有益效果如下:本发明的加工方法可以加工尺寸在0-1000μm之间的铜材质零部件,加工得到的零部件能耐高温、耐电子轰击,尺寸精度高,表面光洁度高,传输损耗小,而且还具有足够的结构强度和真空密封性能,可很好的用于太赫兹频段的真空器件中,满足太赫兹行波管器件的应用需求,解决了现有技术中无能加工微米量级的太赫兹零部件的问题。且该方法加工的零部件可以和其他零部件进行高温焊接,扩大了所述方法在太赫兹真空电子器件应用的范围。附图说明下面结合附图对本发明的具体实施方式作进一步详细的说明。图1示出太赫兹折叠波导的结构示意图。图2示出本发明实施例1制备得到的太赫兹真空器件用的折叠波导的结构示意图。图3示出无氧铜基底上涂敷一层光刻胶后的样品。图4示出经光刻工艺后在无氧铜基底上形成的光刻胶图形。图5示出经微电铸、研磨抛光后形成的样品。图6示出经研磨抛光后形成的样品。图7示出电铸铜层的电镜照片,晶粒大小为194nm。图8示出实施例1频率为94ghz行波管的互作用电路的显微镜图片。图9示出实施例194ghz行波管输出功率的测试数据,输出功率大于100w。图10示出实施例2频率为340ghz行波管的互作用电路的显微镜图(a)和扫描电镜图(b)。图11示出实施例2频率为340ghz行波管的互作用电路的传输损耗系数。图12示出实施例3二次谐波行波管互作用电路的显微镜图(a)和扫描电镜图(b)。图13示出二次谐波行波管的测试结果,输出功率为100mw图14示出对比例1的电铸铜层的电镜照片,高温焊接后,高频结构发生形变。图15示出对比例2的电铸铜层的电镜照片,电铸铜有许多空洞。具体实施方式为了更清楚地说明本发明,下面结合优选实施例和附图对本发明做进一步的说明。附图中相似的部件以相同的附图标记进行表示。本领域技术人员应当理解,下面所具体描述的内容是说明性的而非限制性的,不应以此限制本发明的保护范围。实施例1一种太赫兹真空器件用的折叠波导(其结构示意图如图2所示)的加工方法,包括如下步骤:a.对无氧铜1片进行研磨抛光,无氧铜片表面粗糙度ra在2nm-50nm之间;b.在无氧铜1表面涂覆一层su8光刻胶2,光刻胶厚度为1000μm,如图3所示;c.对光刻胶3进行前烘,曝光,后烘,显影,在无氧铜1片上形成光刻胶图形3-1,如图4所示,其中,前烘温度105℃,前烘时间为18小时,后烘温度为95℃,后烘时间为1小时;d.在带有图形3-1的无氧铜1片上微电铸一层铜2-1,如图5所示,采用硫酸盐铸铜溶液进行电铸,溶液中铜离子含量为20g/l,硫酸含量为200g/l,氯离子含量为60mg/l,温度为25℃,阳极电流密度为0.8a/dm2,采用脉冲波形进行电铸,电铸频率为1khz;微电铸铜层厚度为1000μm,;e.对微电铸的铜2-1层表面进行研磨抛光至器件的高度2,表面粗糙度ra在2nm~50nm之间,如图6所示;f.采用顺流化学方法去除微电铸铜层内的光刻胶;g.切割外形,形成所需要的真空电子器件的零部件。所得零部件电铸层晶粒排列紧密,晶粒细小,可达到194nm,如图7所示,耐850℃高温焊接,耐电子轰击,含氧量为0.00035%。实施所得的零部件如图8所示,该零部件用于94ghz频段的行波管中,测得输出功率如图9所示,输出功率大于100w。实施例2一种太赫兹真空器件用的折叠波导的加工方法,包括如下步骤:a.对无氧铜片进行研磨抛光,无氧铜片表面粗糙度ra在2nm-50nm之间;b.在无氧铜表面涂覆一层su8光刻胶,光刻胶厚度为400μm;c.对光刻胶进行前烘,曝光,后烘,显影,在无氧铜片上形成光刻胶图形,前烘温度105℃,前烘时间为6小时,后烘温度为95℃,后烘时间为0.5小时;d.在带有图形的无氧铜片上微电铸一层铜,采用硫酸盐铸铜溶液进行电铸,溶液中铜离子含量为20g/l,硫酸含量为200g/l,氯离子含量为60mg/l,温度为25℃,阳极电流密度为0.8a/dm2,采用脉冲波形进行电铸,电铸频率为1.5khz;微电铸铜层厚度为400μm;e.对微电铸的铜层表面进行研磨抛光至器件的高度,表面粗糙度ra在2nm~50nm之间;f.采用化学顺流方法去除微电铸铜层内的光刻胶;g.切割外形,形成所需要的真空电子器件的零部件。所得零部件电铸层晶粒排列紧密,晶粒细小,可达到194nm,耐850℃高温焊接,耐电子轰击,含氧量为0.00035%。实施所得的零部件的显微镜图片和扫描电镜图如图10中a和b所示,该零部件可用于340ghz频段的行波管中,测得输出功率大于100w。图11在频段336-346ghz内,传输损耗系数:4-5.3db/cm。实施例3一种太赫兹真空器件用的折叠波导的加工方法,包括如下步骤:a.对无氧铜片进行研磨抛光,无氧铜片表面粗糙度ra在2nm-50nm之间;b.在无氧铜表面涂覆一层su8光刻胶,光刻胶厚度为600μm;c.对光刻胶进行前烘,曝光,后烘,显影,在无氧铜片上形成光刻胶图形,前烘温度105℃,前烘时间为8小时,后烘温度为95℃,后烘时间为45分钟;d.在带有图形的无氧铜片上微电铸一层铜,采用硫酸盐铸铜溶液进行电铸,溶液中铜离子含量为20g/l,硫酸含量为200g/l,氯离子含量为60mg/l,温度为25℃,阳极电流密度为0.8a/dm2,采用脉冲波形进行电铸,电铸频率为2khz;微电铸铜层厚度为600μm;e.对微电铸的铜层表面进行研磨抛光至器件的高度,表面粗糙度ra在2nm-50nm之间;f.采用化学顺流方法去除微电铸铜层内的光刻胶;g.切割外形,形成所需要的真空电子器件的零部件。所得零部件电铸层晶粒排列紧密,晶粒细小,可达到194nm,耐850℃高温焊接,耐电子轰击,含氧量为0.00035%。实施所得的零部件如图12所示,该零部件已用于二次谐波行波管中,测得输出功率如图13所示,输出功率为100mw。对比例1一种太赫兹真空器件用的折叠波导的加工方法,包括如下步骤:a.对无氧铜片进行研磨抛光,无氧铜片表面粗糙度ra在2nm-50nm之间;b.在无氧铜表面涂覆一层su8光刻胶,光刻胶厚度为1000μm;c.对光刻胶进行前烘,曝光,后烘,显影,在无氧铜片上形成光刻胶图形,前烘温度105℃,前烘时间为18小时,后烘温度为95℃,后烘时间为1小时;d.在带有图形的无氧铜片上微电铸一层铜,采用硫酸盐铸铜溶液进行电铸,溶液中铜离子含量为40g/l,硫酸含量为200g/l,氯离子含量为52mg/l,温度为25℃,阳极电流密度为0.8a/dm2,采用脉冲波形进行电铸,电铸频率为2khz;微电铸铜层厚度为600μm;;e.对微电铸的铜层表面进行研磨抛光至器件的高度,表面粗糙度ra在2nm~50nm之间;f.采用顺流化学方法去除微电铸铜层内的光刻胶;g.切割外形,形成所需要的真空电子器件的零部件。所得零部件电铸层的应力大,高温焊接时,零部件发生形变,形变后互作用电路的电镜照片如图14所示,该电路无法应用到真空太赫兹器件中。对比例2一种太赫兹真空器件用的折叠波导的加工方法,包括如下步骤:a.对无氧铜片进行研磨抛光,无氧铜片表面粗糙度ra在2nm-50nm之间;b.在无氧铜表面涂覆一层su8光刻胶,光刻胶厚度为1000μm;c.对光刻胶进行前烘,曝光,后烘,显影,在无氧铜片上形成光刻胶图形,前烘温度105℃,前烘时间为18小时,后烘温度为95℃,后烘时间为1小时;d.在带有图形的无氧铜片上微电铸一层铜,采用硫酸盐铸铜溶液进行电铸,溶液中铜离子含量为40g/l,硫酸含量为200g/l,氯离子含量为40mg/l,温度为25℃,阳极电流密度为0.8a/dm2,采用脉冲波形进行电铸,电铸频率为2khz;微电铸铜层厚度为600μm;;e.对微电铸的铜层表面进行研磨抛光至器件的高度,表面粗糙度ra在2nm~50nm之间;f.采用顺流化学方法去除微电铸铜层内的光刻胶;g.切割外形,形成所需要的真空电子器件的零部件。用扫描电镜观察零部件表面,表面的电镜照片如图15所示,从图15可以看出,所得零部件电铸层晶粒排列疏松,中间有空洞,电子轰击时,释放气体,使真空太赫兹器件的真空度急剧升高,器件性能受损。显然,本发明的上述实施例仅仅是为清楚地说明本发明所作的举例,而并非是对本发明的实施方式的限定,对于所属领域的普通技术人员来说,在上述说明的基础上还可以做出其它不同形式的变化或变动,这里无法对所有的实施方式予以穷举,凡是属于本发明的技术方案所引伸出的显而易见的变化或变动仍处于本发明的保护范围之列。当前第1页12