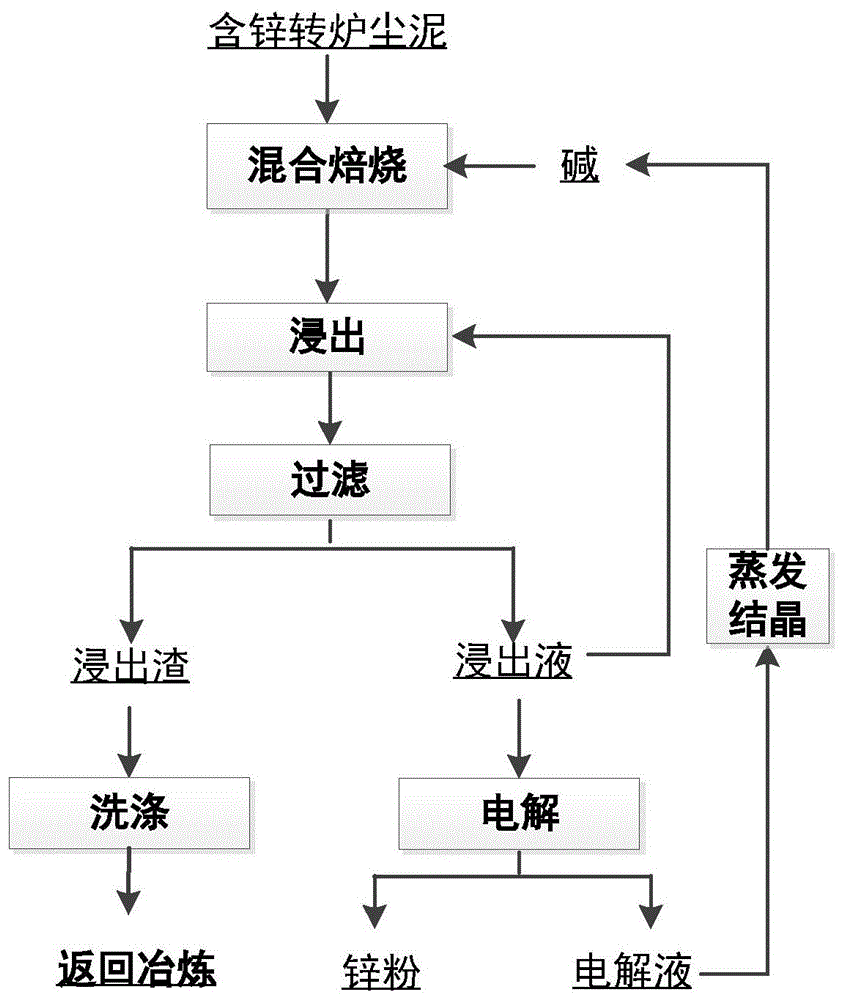
本发明属于冶金尘泥综合利用
技术领域:
,涉及一种含锌转炉尘泥资源化利用的方法。
背景技术:
:转炉炼钢是钢铁生产的主要环节之一,其产生的尘泥量可占到钢铁企业尘泥总量的四分之一。转炉炼钢的收尘工艺有干法和湿法两种,干法采用静电除尘得到干法除尘灰,湿法采用喷淋工艺得到湿法除尘泥。转炉尘泥中近一半为铁元素具有利用价值,因此一直以来转炉尘泥作为配料返回烧结直接利用。随着炼钢时加入的含锌废钢原料的增多,转炉尘泥中的锌含量逐渐升高。锌含量高的尘泥如按原有方式回配利用,锌会在冶炼过程中不断循环富集,容易导致高炉锌负荷超标,对生产顺行和安全长寿造成危害。在冶炼锌负荷接近限值时,含锌转炉尘泥不能再利用,只能堆存,而这种尘泥粒度极细很容易产生扬尘,将对环境造成危害。因此需要采用其他方式处理含锌转炉尘泥,降低其锌含量后再次利用。含锌转炉尘泥的处理难点主要包括:(1)尘泥中的铁含量在50%左右,而锌的含量只有百分之几甚至更低,铁锌比很大,从大量的铁中分离少量锌比较困难;(2)尘泥中锌主要以铁酸锌形式存在,只有少量的氧化锌,铁酸锌性质稳定无法采用现有技术进行选择性锌分离。所以目前尚未有针对含锌转炉尘泥脱锌的处理技术,只能将其与其他含锌冶炼粉尘一起处理。采用转底炉与回转窑等设备还原冶炼是目前最有效的脱锌处理办法,在加入还原剂或者还原气氛的条件下,铁在1100~1300℃被还原,锌以蒸汽形态进入烟道,形成次氧化锌副产物。但从目前处理含锌转炉尘泥的实际情况看,这类设备反应条件苛刻,故障率高,检修周期长;且设备投资较大,运行能耗高,处理成本相对较高;冶炼过程中产生烟气粉尘,容易造成金属二次污染。cn106367600a公开了一种利用回转窑处理高锌含铁尘泥的方法,包括以下步骤:(1)将高炉瓦斯灰,转炉og泥混合造球并干燥预热;(2)球团预热后送入回转窑,回转窑内设粒煤喷枪、残炭喷枪和粒矿喷枪分别喷吹,球团在窑内经过窑温1050~1100℃,90~120min直接还原及高温固结后得到高温金属化球团;(3)高温烟气经二次燃烧进一步重力除尘,待冷却后进入布袋除尘器,回收得到含氧化锌50%~60%的粉尘。该工艺同样是利用回转窑处理含锌废料,但此发明所述含锌转炉尘泥多与其他含锌废料一同处理,由于转炉尘泥中锌含量不到5%,采用回转窑单独处理含锌转炉尘泥可收副产物次氧化锌少,收益降低,且回转窑工艺条件要求高,结圈问题严重,检修维护时间长,用于处理本发明所述含锌转炉尘泥综合处理成本过高。cn108913907a公开了一种利用钙化焙烧-氨浸法从铁酸锌资源中回收锌的方法,通过向铁酸锌资源中加入钙化剂,混匀制粒,在氧化气氛下进行钙化焙烧,使铁酸锌进行矿相重构,转化为氧化锌,得到钙化焙烧产物;将钙化焙烧产物进行破碎处理,通过氨浸处理,使氧化锌溶解浸出,固液分离后,得到锌滤液和浸出渣,但该方法只适用于锌含量较高的铁酸锌资源,而含锌转炉尘泥中锌含量较低,且在原料中较为分散,氧化钙与尘泥中含锌成分接触并反应的机会有限,反而大量钙化剂与氧化铁形成了铁酸钙,未起到分解铁酸锌的作用。综上所述,对于含锌转炉尘泥中锌的分离、回收,需要将难溶盐转化为易溶盐,在回收锌的同时能够回收铁,而且所选操作要较为简单,能耗较低。技术实现要素:针对现有技术存在的问题,本发明的目的在于提供一种含锌转炉尘泥资源化利用的方法,所述方法通过含锌转炉尘泥的碱性焙烧,将转炉尘泥中锌化合物转化为可溶性盐,再通过浸出实现锌铁的分离,浸出液经电解得到锌,所述方法实现了锌的快速分离提取,分离程度高,方法简便,易实现大规模操作,处理成本低。为达此目的,本发明采用以下技术方案:本发明提供了一种含锌转炉尘泥资源化利用的方法,所述方法包括以下步骤:(1)将含锌转炉尘泥与碱进行混合焙烧,所得焙烧产物浸出后固液分离,得到浸出渣和浸出液;(2)将步骤(1)得到的浸出液进行电解,回收得到锌粉。本发明中,以含锌转炉尘泥中锌的赋存状态为基础,利用其组分特性通过碱性焙烧破坏了含锌化合物的结构,将其转化为可溶盐,再利用锌铁元素性质的差异,通过浸出分离锌和铁,得到的含锌溶液进一步制备单质锌。所述方法步骤简便,锌从尘泥中分离后,降低了转炉尘泥中的锌含量,使转炉尘泥得以循环利用,同时实现了锌的资源化回收。以下作为本发明优选的技术方案,但不作为本发明提供的技术方案的限制,通过以下技术方案,可以更好地达到和实现本发明的技术目的和有益效果。作为本发明优选的技术方案,步骤(1)所述含锌转炉尘泥包括转炉炼钢生产过程中产生的除尘灰与除尘泥。作为本发明优选的技术方案,步骤(1)所述碱包括氢氧化钠和/或氢氧化钾。优选地,步骤(1)所述含锌转炉尘泥与碱的质量比为1:(0.3~3),例如1:0.3、1:0.5、1:0.8、1:1、1:1.5、1:2、1:2.5或1:3等,但并不仅限于所列举的数值,该数值范围内其他未列举的数值同样适用。优选地,步骤(1)所述焙烧温度为200~800℃,例如200℃、250℃、300℃、400℃、500℃、600℃、700℃或800℃等,但并不仅限于所列举的数值,该数值范围内其他未列举的数值同样适用,优选为300~600℃。优选地,步骤(1)所述焙烧时间为0.5~4h,例如0.5h、1h、1.5h、2h、2.5h、3h、3.5h或4h等,但并不仅限于所列举的数值,该数值范围内其他未列举的数值同样适用。本发明中,碱性焙烧过程中,以氢氧化钠为例,其发生的主要化学反应为:znfe2o4(s)+8naoh(s)=na2zno2(s)+2na3feo3(s)+4h2o;zno(s)+2naoh(s)=na2zno2(s)+h2o。通过上述反应,破坏了铁酸锌化合物的晶相结构,转化为可溶于水的含锌钠盐,便于后续锌铁的分离。作为本发明优选的技术方案,将步骤(1)所述焙烧产物进行冷却、破碎。优选地,步骤(1)所述浸出所用溶剂为水。优选地,步骤(1)所述浸出的固液比为1:(3~30),例如1:3、1:5、1:10、1:15、1:20、1:25或1:30等,但并不仅限于所列举的数值,该数值范围内其他未列举的数值同样适用。本发明中,在湿法冶金领域,固液比通常是指固体质量与液体体积的比例。作为本发明优选的技术方案,步骤(1)所述浸出温度为25~100℃,例如25℃、30℃、40℃、50℃、60℃、80℃或100℃等,但并不仅限于所列举的数值,该数值范围内其他未列举的数值同样适用。优选地,步骤(1)所述浸出时间为0.5~6h,例如0.5h、1h、2h、3h、4h、5h或6h等,但并不仅限于所列举的数值,该数值范围内其他未列举的数值同样适用。本发明中,碱性焙烧后,将焙烧产物浸出,可溶性盐溶解于水中,而铁酸盐水解形成氢氧化铁,以固相形式存在,实现锌与铁的分离,浸出过程中的主要化学反应为:na2zno2(s)+2na3feo3(s)+5h2o=na2zn(oh)4(aq.)+fe(oh)3(s)+6naoh(aq.)。作为本发明优选的技术方案,步骤(1)所述浸出渣洗涤后干燥,返回作为冶炼原料。优选地,所述洗涤用水质量是浸出渣的1~5倍,例如1倍、2倍、3倍、4倍或5倍等,但并不仅限于所列举的数值,该数值范围内其他未列举的数值同样适用。优选地,步骤(1)所述浸出液返回用于焙烧产物的浸出或直接进行步骤(2)。本发明中,由于尘泥中锌含量相对较低,所得浸出液中锌浓度较低,可以将浸出液返回作为焙烧产物的浸出剂,富集到更多的锌后再进行电解。作为本发明优选的技术方案,步骤(2)所述浸出液电解前维持氢氧根离子的浓度为0.5~7mol/l,例如0.5mol/l、1mol/l、2mol/l、3mol/l、4mol/l、5mol/l、6mol/l或7mol/l等,但并不仅限于所列举的数值,该数值范围内其他未列举的数值同样适用。本发明中,维持足够的碱浓度,能够使得锌以zn(oh)42-的形式存在,而非转化为zn(oh)2沉淀,否则锌难以被电积。优选地,步骤(2)所述电解温度为10~80℃,例如10℃、20℃、30℃、40℃、50℃、60℃、70℃或80℃等,但并不仅限于所列举的数值,该数值范围内其他未列举的数值同样适用。优选地,步骤(2)所述电解时间5~200min,例如5min、10min、20min、50min、80min、100min、150min或200min等,但并不仅限于所列举的数值,该数值范围内其他未列举的数值同样适用。作为本发明优选的技术方案,步骤(2)所述电解时电流密度为500~2200a/m2,例如500a/m2、700a/m2、1000a/m2、1200a/m2、1500a/m2、1800a/m2、2000a/m2或2200a/m2等,但并不仅限于所列举的数值,该数值范围内其他未列举的数值同样适用。优选地,步骤(2)所述电解时电极间的距离为0.5~4.5cm,例如0.5cm、1cm、1.5cm、2cm、2.5cm、3cm、4cm或4.5cm等,但并不仅限于所列举的数值,该数值范围内其他未列举的数值同样适用。作为本发明优选的技术方案,步骤(2)所述电解后阴极析出得到锌。本发明中,电解时,可采用钛或钛合金作为阴极板,不锈钢作为阳极板,其发生的电极反应分别为:阴极反应:zn(oh)42-+2e=zn+4oh-;阳极反应:2oh--2e=h2o+1/2o2。优选地,步骤(2)所述电解后得到的溶液蒸发结晶,得到固体碱。优选地,所述碱返回步骤(1)用于与含锌转炉尘泥混合焙烧。作为本发明优选的技术方案,所述方法包括以下步骤:(1)将质量比为1:(0.3~3)的含锌转炉尘泥与碱进行混合焙烧,焙烧温度为200~800℃,焙烧时间为0.5~4h,得到焙烧产物;所得焙烧产物冷却、破碎后浸出,浸出的固液比为1:(3~30),浸出温度为25~100℃,浸出时间为0.5~6h,然后固液分离,得到浸出渣和浸出液,浸出渣洗涤后干燥,返回作为冶炼原料,浸出液返回用于焙烧产物的浸出或直接进入下一步骤;(2)将步骤(1)得到的浸出液进行电解,电解前维持氢氧根离子的浓度为0.5~7mol/l,电解温度为10~80℃,电解时间5~200min,电解时电流密度为500~2200a/m2,电极间的距离为0.5~4.5cm,阴极析出得到锌,电解后的溶液蒸发结晶,得到固体碱。与现有技术相比,本发明具有以下有益效果:(1)本发明所述方法通过碱性焙烧将含锌转炉尘泥中的锌化合物转化为可溶盐,再通过浸出实现锌和铁的分离,选择性好,分离率可达92%以上,所得锌的纯度达到90%以上;(2)本发明含锌转炉尘泥中铁的损失极小,回收率高,且电解后溶液可回收碱,产品利用程度高;(3)本发明所述方法中焙烧不产生烟气烟尘,无需除尘,不造成二次污染,全程无新的固体废弃物排放,环境友好绿色清洁。附图说明图1是本发明具体实施方式提供的含锌转炉尘泥资源化利用方法的工艺流程图;图2是本发明实施例1提供的锌粉的xrd图;图3是本发明实施例1提供的锌粉的sem图。具体实施方式为更好地说明本发明,便于理解本发明的技术方案,下面对本发明进一步详细说明,但下述的实施例仅是本发明的简易例子,并不代表或限制本发明的权利保护范围,本发明保护范围以权利要求书为准。本发明具体实施方式部分提供了一种含锌转炉尘泥资源化利用的方法,所述方法的工艺流程图如图1所示,包括以下步骤:(1)将含锌转炉尘泥与碱进行混合焙烧,所得焙烧产物浸出后固液分离,得到浸出渣和浸出液;(2)将步骤(1)得到的浸出液进行电解,回收得到锌粉。以下为本发明典型但非限制性实施例:实施例1:本实施例提供了一种含锌转炉尘泥资源化利用的方法,所述含锌转炉尘泥由钢铁厂转炉炼钢湿法收尘得到,其主要元素组成如表1所示。表1实施例1中含锌转炉尘泥的主要元素组成表元素fecaznkmgnasimnal含量/wt%50.1113.123.640.683.640.131.560.710.27所述方法包括以下步骤:(1)将所述含锌转炉尘泥与氢氧化钠进行混合焙烧,含锌转炉尘泥与氢氧化钠的质量比为1:0.9,焙烧温度为450℃,焙烧时间为2.5h,得到焙烧产物;(2)将步骤(1)得到的所得焙烧产物冷却、破碎后用水浸出,浸出的固液比为1:10,浸出温度为80℃,浸出时间为3h,然后过滤分离,得到浸出渣和浸出液,浸出渣用3倍的水量洗涤后干燥,得到的脱锌浸出渣返回作为冶炼原料,浸出液返回用于焙烧产物的浸出,再进行4次浸出,累积得到高浓度浸出液;(3)将步骤(2)得到的浸出液进行电解,电解前氢氧根离子的浓度为5.25mol/l,电解温度为30℃,电解时间120min,电解时电流密度为1200a/m2,电极间的距离为1cm,阴极析出得到锌粉,电解后的溶液蒸发结晶,得到氢氧化钠用于步骤(1)焙烧处理。将步骤(3)中得到的锌粉进行xrd测试,其xrd图如图2所示,并进行微观结构表征,其sem图如图3所示。本实施例中,通过测量步骤(2)中得到的脱锌浸出渣的质量及锌含量,浸出渣中的锌含量降至0.19%,计算得出锌的脱除率达到94.7%;由图2可知,xrd图中的特征峰与锌的特征峰相符合,并进一步测试得到锌粉的纯度为95.63%;由图3可知,锌粉为几微米至几十微米的簇状大颗粒,有明显的沉积纹路。实施例2:本实施例提供了一种含锌转炉尘泥资源化利用的方法,所述含锌转炉尘泥元素组成及含量与实施例1相同,所述方法包括以下步骤:(1)将所述含锌转炉尘泥与氢氧化钾进行混合焙烧,含锌转炉尘泥与氢氧化钠的质量比为1:1.2,焙烧温度为750℃,焙烧时间为0.5h,得到焙烧产物;(2)将步骤(1)得到的所得焙烧产物冷却、破碎后用水浸出,浸出的固液比为1:15,浸出温度为100℃,浸出时间为1h,然后过滤分离,得到浸出渣和浸出液,浸出渣用5倍的水量洗涤后干燥,得到的脱锌浸出渣返回作为冶炼原料,浸出液返回用于焙烧产物的浸出,再进行2次浸出,累积得到高浓度浸出液;(3)将步骤(2)得到的浸出液进行电解,电解前氢氧根离子的浓度为2.5mol/l,电解温度为50℃,电解时间40min,电解时电流密度为900a/m2,电极间的距离为2.5cm,阴极析出得到锌粉,电解后的溶液蒸发结晶,得到氢氧化钠用于步骤(1)焙烧处理。本实施例中,通过测量步骤(2)中得到的脱锌浸出渣的质量及锌含量,脱锌浸出渣中锌含量为0.18%,计算得出锌的脱除率达到95.2%;测试步骤(3)中得到的锌粉的纯度达到92.13%。实施例3:本实施例提供了一种含锌转炉尘泥资源化利用的方法,所述含锌转炉尘泥由钢铁厂转炉炼钢干法收尘得到,其主要元素组成如表2所示。表2实施例3中含锌转炉尘泥的主要元素组成表元素fecaznkmgnasimnal含量/wt%52.337.661.531.682.631.130.780.980.68所述方法包括以下步骤:(1)将所述含锌转炉尘泥与氢氧化钾进行混合焙烧,含锌转炉尘泥与氢氧化钾的质量比为1:0.5,焙烧温度为450℃,焙烧时间为4h,得到焙烧产物;(2)将步骤(1)得到的所得焙烧产物冷却、破碎后用水浸出,浸出的固液比为1:6,浸出温度为30℃,浸出时间为6h,然后过滤分离,得到浸出渣和浸出液,浸出渣用1.2倍的水量洗涤后干燥,得到的脱锌浸出渣返回作为冶炼原料,浸出液返回用于焙烧产物的浸出,再进行5次浸出,累积得到高浓度浸出液;(3)将步骤(2)得到的浸出液进行电解,电解前氢氧根离子的浓度为3.4mol/l,电解温度为80℃,电解时间80min,电解时电流密度为2000a/m2,电极间的距离为4.5cm,阴极析出得到锌粉,电解后的溶液蒸发结晶,得到氢氧化钾用于步骤(1)焙烧处理。本实施例中,通过测量步骤(2)中得到的脱锌浸出渣的质量及锌含量,脱锌浸出渣中锌含量为0.12%,计算得出锌的脱除率达到92.1%;测试步骤(3)中得到的锌粉的纯度达到91.98%。实施例4:本实施例提供了一种含锌转炉尘泥资源化利用的方法,所述含锌转炉尘泥的主要元素组成如表3所示。表3实施例4中含锌转炉尘泥的主要元素组成表元素fecaznkmgnasimn含量/wt%49.885.364.561.461.370.871.840.89所述方法包括以下步骤:(1)将所述含锌转炉尘泥与氢氧化钠进行混合焙烧,含锌转炉尘泥与氢氧化钠的质量比为1:2,焙烧温度为500℃,焙烧时间为2h,得到焙烧产物;(2)将步骤(1)得到的所得焙烧产物冷却、破碎后用水浸出,浸出的固液比为1:20,浸出温度为50℃,浸出时间为4h,然后过滤分离,得到浸出渣和浸出液,浸出渣用2倍的水量洗涤后干燥,得到的脱锌浸出渣返回作为炼钢原料,浸出液返回用于焙烧产物的浸出,再进行3次浸出,累积得到高浓度浸出液;(3)将步骤(2)得到的浸出液进行电解,电解前氢氧根离子的浓度为5.6mol/l,电解温度为27℃,电解时间160min,电解时电流密度为650a/m2,电极间的距离为3cm,阴极析出得到锌粉,电解后的溶液蒸发结晶,得到氢氧化钠用于步骤(1)焙烧处理。本实施例中,通过测量步骤(2)中得到的脱锌浸出渣的质量及锌含量,脱锌浸出渣中锌含量为0.24%,计算得出锌的脱除率达到94.7%;测试步骤(3)中得到的锌粉的纯度达到93.03%。实施例5:本实施例提供了一种含锌转炉尘泥资源化利用的方法,所述含锌转炉尘泥的元素组成及含量与实施例4相同;所述方法包括以下步骤:(1)将所述含锌转炉尘泥与氢氧化钾进行混合焙烧,含锌转炉尘泥与氢氧化钾的质量比为1:1.8,焙烧温度为650℃,焙烧时间为1h,得到焙烧产物;(2)将步骤(1)得到的所得焙烧产物冷却、破碎后用水浸出,浸出的固液比为1:30,浸出温度为60℃,浸出时间为2h,然后过滤分离,得到浸出渣和浸出液,浸出渣用4倍的水量洗涤后干燥,得到的脱锌浸出渣返回作为炼钢原料,浸出液返回用于焙烧产物的浸出,再进行1次浸出,累积得到高浓度浸出液;(3)将步骤(2)得到的浸出液进行电解,电解前氢氧根离子的浓度为2.8mol/l,电解温度为50℃,电解时间20min,电解时电流密度为700a/m2,电极间的距离为2cm,阴极析出得到锌粉,电解后的溶液蒸发结晶,得到氢氧化钾用于步骤(1)焙烧处理。本实施例中,通过测量步骤(2)中得到的脱锌浸出渣的质量及锌含量,脱锌浸出渣中锌含量为0.28%,计算得出锌的脱除率达到93.8%;测试步骤(3)中得到的锌粉的纯度达到92.77%。对比例1:本对比例提供了一种含锌转炉尘泥资源化利用的方法,所述含锌转炉尘泥元素组成及含量与实施例1相同,所述方法参照实施例1中的方法,区别仅在于:步骤(1)中焙烧时不加入氢氧化钠。本对比例中,由于未加入碱进行焙烧,含锌转炉尘泥中锌化合物无法转化成可溶性盐的形式被浸出分离,锌的脱除率极低,不足1%。综合上述实施例和对比例可以看出,本发明所述方法利用锌的两性化学性质,通过碱性焙烧破坏含锌转炉尘泥中含锌化合物的结构使其转化为可溶性盐,再通过浸出将铁留在浸出渣中,实现锌和铁的分离,锌的分离率可达92%以上,浸出液电解所得锌的纯度达到90%以上;尘泥中铁的损失极小,铁回收率高,经脱锌后的转炉尘泥可以原有方式返回系统配料利用,电解后溶液中的碱可结晶后再度混合焙烧,产品利用程度高;所述方法中焙烧不产生烟气烟尘,无需除尘,不产生新的固废,不造成二次污染,环境友好绿色清洁。申请人声明,本发明通过上述实施例来说明本发明的详细方法,但本发明并不局限于上述详细方法,即不意味着本发明必须依赖上述方法才能实施。所属
技术领域:
的技术人员应该明了,对本发明的任何改进,对本发明所用原料、操作的等效替换及辅助原料、操作的添加,具体方式的选择等,均落在本发明的保护范围和公开范围之内。当前第1页1 2 3