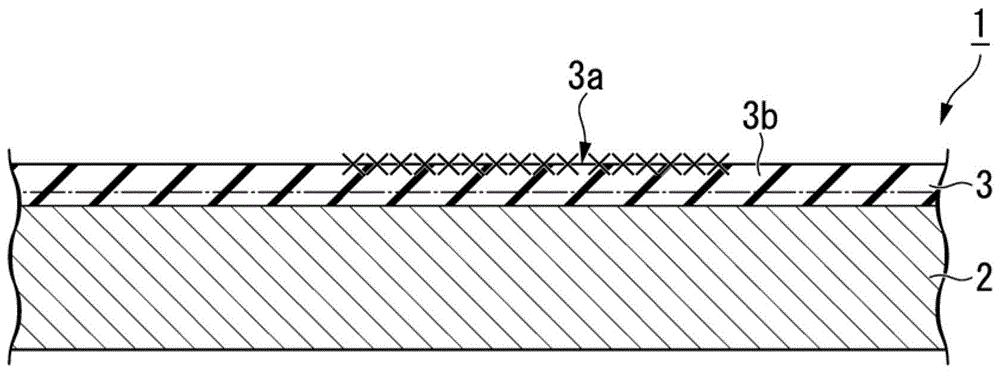
本发明涉及铝制部件的氧化皮膜的再生方法。
背景技术:
:作为用于制造存储器或发光二极管等半导体装置、液晶显示装置或有机el显示装置等显示装置(还称为平板显示器)、太阳能电池、磁性设备、光学膜等的装置,已知有溅射成膜装置、cvd成膜装置(cvd:chemicalvaperdeposition,化学气相沉积)、真空蒸镀装置、灰化装置、蚀刻装置、离子注入装置、退火装置等的各种制造装置。这些制造装置具有腔室,该腔室收容处理对象的基材,并且用于对基材进行成膜、蚀刻、离子注入、退火等。为了顺利进行成膜、蚀刻、离子注入、退火等,在腔室中设置有各种各样的部件。这些部件的一部分使用由铝或铝合金构成的铝制部件。其中,在等离子体环境下加工晶片或薄膜等的蚀刻装置以及形成薄膜的成膜装置(以下,将在等离子体环境下进行处理的装置称为等离子体装置)中,在腔室内使用的金属制部件的大部分为铝制部件。作为铝制部件的例子,具有为了将原料气体、腐蚀气体等均匀地供给到基材上而设置有多个贯穿孔的板。另外,作为另一例子,具有加热器和屏蔽板等。为了进行来自等离子体照射等的保护或赋予电气绝缘性,或者为了提高耐腐蚀性,上述铝制部件一般在其表面具有氧化皮膜。作为在铝制部件的表面形成氧化皮膜的方法,例如具有使用硫酸浴的硫酸阳极氧化处理、以草酸阳极氧化为代表的有机酸阳极氧化处理、使用硫酸与有机酸的混合溶液的混酸阳极氧化处理等。通过这些方法,在铝制部件的表面形成氧化皮膜。但是,如果使用等离子体装置连续或断续进行各种处理,则铝制部件表面的氧化皮膜有可能会逐渐劣化。作为劣化形态,可列举因等离子体中包含的离子、电子、自由基等导致的氧化皮膜表面的腐蚀、因氧化皮膜表面被还原或被氟化而引起的氧化皮膜表面的变质、伴随各种处理发生的反应副产物在氧化皮膜表面堆积这种情况。氧化皮膜的劣化不仅限于等离子体装置,在等离子体装置以外的半导体制造装置或平板显示器制造装置中也有可能会发生氧化皮膜的劣化。这种氧化皮膜的劣化成为各种制造装置中的处理障碍。例如,由于因腐蚀或变质而导致从氧化皮膜剥离的氧化铝脱落,或者变质为氟化物的氧化皮膜从作为其基材的铝脱落,或者堆积在表面的反应副产物脱落,从而成为产生微粒的原因。因此,为了防止这种障碍,关于各种制造装置所使用的铝制部件,需要定期从该制造装置拆卸该铝制部件,通过在完全去除氧化皮膜之后,形成新的氧化皮膜,从而再生铝制部件。作为去除氧化皮膜的方法,具有通过将铝制部件浸渍到蚀刻液而去除氧化皮膜的方法以及通过磨削、研磨等机械手段去除氧化皮膜的方法。关于该机械手段,在专利文献1中记载有如下方法:该方法去除铝制部件的氧化皮膜,并且对去除氧化皮膜的铝制部件实施研磨处理。然而,在将铝制部件浸渍到蚀刻液的方法中,由于以下说明的理由,有时会过度蚀刻铝制部件。即,氧化皮膜的劣化大多为铝制部件的氧化皮膜整体不均匀地劣化的情况。因此,有时会混合存在劣化状态比较轻微的部分和劣化状态比较严重的部分。在此,如果为了去除氧化皮膜中的严重劣化的部位而调整蚀刻条件,则对于轻微劣化的部位来说该蚀刻条件会成为过量条件,有时会直到氧化皮膜的基底为止过度蚀刻。特别是,在使用蚀刻液对设置有多个贯穿孔的板去除氧化皮膜时上述问题很明显。如果在完全去除严重劣化的氧化皮膜的条件下对板进行蚀刻,则在轻微劣化的部位例如贯穿孔的内部,氧化皮膜被蚀刻并且贯穿孔的内周面被过度蚀刻,有可能会扩大贯穿孔的内径。如果反复进行板的氧化皮膜的再生,则虽然期初多个贯穿孔间的内径的偏差较小,但贯穿孔间的内径的偏差会逐渐变大。如上所述,如果使用贯穿孔的形状变化的板例如进行薄膜的形成,则因产生薄膜原料的沉积量分布而薄膜的厚度变得不均匀,有可能会对薄膜的质量带来不良影响。另外,如专利文献1所记载的那样,在通过磨削、研磨等机械手段去除氧化皮膜的情况下,直到氧化皮膜的基底的铝为止过度磨削,铝制部件的形状尺寸发生变化,有可能会成为制造装置中的处理故障的原因。为了防止形状尺寸的变化,可以考虑只去除氧化皮膜的膜厚方向的上层部。然而,即使在不露出基底而残留氧化皮膜的一部分的状态下进行通常的阳极氧化处理,新的氧化皮膜也不会生长,因此氧化皮膜的再生很困难。此外,有可能会误伤铝制部件,使氧化皮膜产生剥离部、瑕疵或磨损痕。在该情况下,具有想要局部再生氧化皮膜的要求。专利文献1:日本专利公开2004-211128号公报技术实现要素:本发明是鉴于上述情况而提出的,其课题是提供一种铝制部件的氧化膜的再生方法,该铝制部件的氧化膜的再生方法能够再生铝制部件的氧化皮膜。为了解决上述课题,本发明采用以下结构。一种本发明的一方式所涉及的铝制部件的氧化皮膜的再生方法,所述铝制部件具有:由铝或铝合金构成的部件主体;和形成在所述部件主体的表面的氧化皮膜,在所述氧化皮膜的表面具有剥离部、瑕疵及磨损痕中的至少一个,所述铝制部件的氧化皮膜的再生方法包括:再生工序,通过将所述铝制部件浸渍到电解液中进行微弧氧化处理,从而修复所述氧化皮膜。一种本发明的一方式所涉及的铝制部件的氧化皮膜的再生方法,所述铝制部件具有:由铝或铝合金构成的部件主体;和形成在所述部件主体的表面的氧化皮膜,所述铝制部件的氧化皮膜的再生方法包括:去除工序,去除所述铝制部件的所述氧化皮膜的一部分或全部的上层部,或者以残留所述氧化皮膜的一部分的方式进行去除;和再生工序,通过将经过所述去除工序的所述铝制部件浸渍到电解液中进行微弧氧化处理,从而增加被去除的部位的所述氧化皮膜的厚度。在本发明的一方式所涉及的铝制部件的氧化皮膜的再生方法中,所述去除工序也可以为了去除所述氧化皮膜而使用机械研磨处理、喷砂处理或高压水喷射处理。在本发明的一方式所涉及的铝制部件的氧化皮膜的再生方法中,所述去除工序也可以去除表面附着有异物的所述氧化皮膜或表面变质的氧化皮膜的上层部。在本发明的一方式所涉及的铝制部件的氧化皮膜的再生方法中,所述去除工序也可以去除表面附着有异物的部分的所述氧化皮膜或表面变质的部分的氧化皮膜。在本发明的一方式所涉及的铝制部件的氧化皮膜的再生方法中,所述铝制部件也可以是设置在半导体制造装置或平板显示器制造装置的腔室内使用的已使用的铝制部件。在本发明的一方式所涉及的铝制部件的氧化皮膜的再生方法中,所述铝制部件也可以是沿所述部件主体的板厚方向在所述部件主体设置有多个贯穿孔且设置在半导体制造装置或平板显示器制造装置的腔室内来使用的板,对形成在部件主体中的设置有所述贯穿孔的面的一部分或全部的所述氧化皮膜进行所述去除工序。在本发明的一方式所涉及的铝制部件的氧化皮膜的再生方法中,对形成在所述贯穿孔的内表面的所述氧化皮膜不进行所述去除工序。在本发明的一方式所涉及的铝制部件的氧化皮膜的再生方法中,所述再生工序也可以是使所述氧化皮膜的膜厚比再生工序前的膜厚更厚的工序。根据本发明的一方式所涉及的铝制部件的氧化皮膜的再生方法,由于对在氧化皮膜表面具有剥离部、瑕疵及磨损痕中的至少一个的铝制部件进行微弧氧化处理而修复氧化皮膜,因此能够将铝制部件再生为与新品同样。另外,根据本发明的一方式所涉及的铝制部件的氧化皮膜的再生方法,去除铝制部件的氧化皮膜的一部分或全部的上层部,或者以残留氧化皮膜的一部分的方式进行去除,然后对铝制部件进行微弧氧化处理,增加被去除的部位的氧化皮膜的厚度,因此能够将劣化的氧化皮膜替换为新的氧化皮膜,能够再生铝制部件。在本发明中,由于不去除氧化皮膜的厚度方向的全部,而是只去除氧化皮膜的上层部,残留上层部以外的剩余部分,因此不会错误地过度去除铝制部件的部件主体的一部分。另外,通过进行微弧氧化处理,能够对去除上层部后膜厚减少且绝缘电阻变小的氧化皮膜形成新的氧化皮膜,并且能够容易使去除上层部的氧化皮膜恢复到上层部去除前的原始厚度。另外,在本发明的一方式中,不除去氧化皮膜的全部,也可以残留一部分,在该情况下,误伤铝制部件的部件主体的表面全部的危险减少。另外,通过在残留氧化皮膜的一部分的状态下进行微弧氧化处理,从而能够形成与残存的氧化皮膜相等的厚度的氧化皮膜。如上所述,根据本发明,能够再生铝制部件的氧化皮膜。此外,根据本发明一方式所涉及的铝制部件的氧化皮膜的再生方法,在去除工序中,由于为了去除氧化皮膜而采用机械研磨处理、喷砂处理或高压水喷射处理,因此能够局部去除劣化的氧化皮膜,使健全的氧化皮膜残留,能够在再生工序中迅速再生氧化皮膜。另外,与以往的利用蚀刻液的去除处理相比,不会引起过度蚀刻健全的氧化皮膜的形成部位等不良情况。另外,根据本发明的一方式所涉及的铝制部件的氧化皮膜的再生方法,在去除工序中,由于去除表面附着有异物的氧化皮膜或者表面变质的氧化皮膜的上层部,因此能够只将劣化的氧化皮膜替换为新的氧化皮膜,能够迅速再生铝制部件。另外,根据本发明的一方式所涉及的铝制部件的氧化皮膜的再生方法,在去除工序中,由于去除表面附着有异物的部分的氧化皮膜或者表面变质的部分的氧化皮膜,因此能够只将劣化的氧化皮膜替换为新的氧化皮膜,能够迅速再生铝制部件。此外,根据本发明的一方式所涉及的铝制部件的氧化皮膜的再生方法,由于处理对象为铝制部件或设置在半导体制造装置或平板显示器制造装置的腔室内使用的已使用的铝制部件,因此能够再生在腔室内被使用且氧化皮膜的一部分劣化的铝制部件。此外,根据本发明的一方式所涉及的铝制部件的氧化皮膜的再生方法,由于铝制部件为具有多个贯穿孔的板,并且对形成在设置有贯穿孔的面的一部分或全部的所述氧化皮膜实施本发明的再生方法,因此能够选择性地再生该板中劣化严重的部分的氧化皮膜。此外,根据本发明的一方式所涉及的铝制部件的氧化皮膜的再生方法,在去除工序中,由于不去除形成在具有多个贯穿孔的板的贯穿孔的内表面的氧化皮膜,因此即使反复进行本发明的再生方法,贯穿孔的内径也会保持在新板状态,因此不会招致在腔室内因板的贯穿孔的变化而引起的不良情况,例如形成的薄膜的厚度的不均匀性。另外,根据本发明的一方式所涉及的铝制部件的氧化皮膜的再生方法,通过使氧化皮膜的膜厚比再生工序前的膜厚更厚,从而能够利用新的氧化皮膜覆盖铝制部件,能够提高铝制部件的质量。如以上说明的那样,根据本发明,能够提供一种铝制部件的氧化膜的再生方法,该铝制部件的氧化膜的再生方法能够再生劣化的氧化皮膜。附图说明图1a是用于说明实施方式的铝制部件的氧化皮膜的再生方法中的去除工序的剖面示意图。图1b是用于说明实施方式的铝制部件的氧化皮膜的再生方法中的去除工序的剖面示意图。图2a是用于说明实施方式的铝制部件的氧化皮膜的再生方法中的去除工序的剖面示意图。图2b是用于说明实施方式的铝制部件的氧化皮膜的再生方法中的去除工序的剖面示意图。图3a是用于说明实施方式的铝制部件的氧化皮膜的再生方法中的再生工序的剖面示意图。图3b是用于说明实施方式的铝制部件的氧化皮膜的再生方法中的再生工序的剖面示意图。图4a是用于说明实施方式的铝制部件的氧化皮膜的再生方法的另一例的剖面示意图。图4b是用于说明实施方式的铝制部件的氧化皮膜的再生方法的另一例的剖面示意图。图5a是用于说明实施方式的铝制部件的氧化皮膜的再生方法的又一例的剖面示意图。图5b是用于说明实施方式的铝制部件的氧化皮膜的再生方法的又一例的剖面示意图。具体实施方式下面,对作为本发明的实施方式的铝制部件的氧化皮膜的再生方法进行说明。本实施方式的铝制部件的再生方法具备:去除工序,去除铝制部件的氧化皮膜的一部分或全部的上层部,或者以残留氧化皮膜的一部分的方式进行去除;和再生工序,通过微弧氧化处理,增加被去除的部位的氧化皮膜的厚度。下面,对各工序进行说明。作为本实施方式的处理对象的铝制部件具备:由铝或铝合金构成的部件主体;和形成在部件主体的表面的氧化皮膜。本实施方式的铝制部件为设置在各种制造装置的腔室中的部件。各种制造装置例如为半导体制造装置或平板显示器制造装置,更具体而言,可列举溅射装置、cvd成膜装置(cvd:chemicalvaperdeposition)、真空蒸镀装置、灰化装置、蚀刻装置、离子注入装置或退火装置等。另外,上述制造装置的腔室是为了收容处理对象的基材并且对基材进行成膜、蚀刻、离子注入或退火等而能够控制内部气氛的处理室。为了顺利进行成膜、蚀刻、离子注入或退火等,在这些腔室中设置有各种各样的部件。本实施方式的铝制部件为在上述腔室内使用的部件,在制造装置的维护时可从腔室拆卸该铝制部件。作为铝制部件的具体例,例如可列举具有多个贯穿孔的板、加热器或屏蔽部件等。主要在等离子体环境下加工基材或薄膜等的蚀刻装置以及形成薄膜的成膜装置(以下,将在等离子体环境下进行处理的装置称为等离子体装置)中使用这些部件。具有多个贯穿孔的板是沿部件主体的板厚方向在部件主体设置有多个贯穿孔的部件。贯穿孔的内径为0.1~2mm左右,贯穿孔的数量是根据部件主体的大小而定的,该贯穿孔的数量为几千到几万个。构造铝制部件的部件主体由铝或铝合金构成。铝或铝合金不受特别限制,例如,可举例说明jis合金编号的1000系列的纯铝、2000系列、3000系列、4000系列、5000系列、6000系列或7000系列的铝合金。另外,作为铝合金,也可以使用al-si系合金、al-mg系合金、al-cu-si系合金、al-cu-mg-si系合金或al-mg-si系合金等。部件主体的形状不受特别限制。如上所述的板那样,也可以是设置有多个贯穿孔的部件。构成铝制部件的氧化皮膜最好为以氧化铝为主成分的氧化皮膜。氧化皮膜并非为自然氧化膜,而是以有目的地形成在部件主体上的氧化皮膜为处理对象。构成铝制部件的氧化皮膜也可以是通过后述的微弧氧化处理形成的氧化皮膜。另外,氧化皮膜也可以是通过各种阳极氧化法形成的阳极氧化膜。作为阳极氧化法,可列举使用硫酸浴的硫酸阳极氧化处理、以草酸阳极氧化为代表的有机酸阳极氧化处理、使用硫酸与有机酸的混合溶液的混酸阳极氧化处理等。另外,构成铝制部件的氧化皮膜也可以是通过氧化铝膜处理形成的氧化皮膜。构成铝制部件的氧化皮膜优选形成在部件主体的整个面。例如,优选在板的贯穿孔的内周面也形成有氧化皮膜。构成铝制部件的氧化皮膜的厚度例如在5~20μm的范围内即可。关于氧化皮膜的厚度,通过使铝制部件的任意部位的剖面露出,并且使用光学显微镜或扫描型电子显微镜,测定该剖面中的氧化皮膜的厚度即可。在厚度不均匀的情况下,例如在剖面上以10mm间隔测定10个点的氧化皮膜的厚度,将该剖面中的氧化皮膜的厚度设为这10个点的测定值的平均值即可。接着,对去除工序进行说明。提供于去除工序的铝制部件为氧化皮膜劣化的部件。在此,所谓氧化皮膜的劣化,例如可列举在氧化膜的表面附着有污染物的状态或者氧化皮膜的表面变质的状态。所谓污染物附着在表面的状态,例如可列举伴随上述制造装置的各种处理产生的反应副产物堆积在氧化皮膜表面的状态。所谓氧化皮膜的表面变质的状态,例如可列举氧化皮膜的表面因等离子体中包含的离子、电子或自由基等而腐蚀的状态、或者氧化皮膜的表面因氧化皮膜的表面被还原或被氟化而变质的状态。能够通过肉眼观察氧化皮膜的外观来判别氧化皮膜有无劣化。在确认到氧化皮膜的变色或氧化皮膜表面的粗面化的情况下,能够判断为氧化皮膜正在劣化。例如,由于铝制部件设置在上述制造装置的腔室内使用,因此在确认到氧化皮膜的一部分或全部变色的情况下,视为氧化皮膜劣化,能够将这种铝制部件(已使用的铝制部件)作为本实施方式的再生方法的再生对象。另外,有可能会误伤铝制部件,导致氧化皮膜形成剥离部、瑕疵及磨损痕中的至少一个的情况。能够用肉眼确认这种氧化皮膜的不良部位。因此,在观察氧化皮膜的外观的结果,确认到不良部位的情况下,也能够判断氧化皮膜劣化。这种铝制部件也能够成为本实施方式的再生方法的对象。另外,形成有剥离部、瑕疵或磨损部的铝制部件也可以是在各种制造装置中使用前的部件,也可以是使用后的部件。另外,在本实施方式中,作为处理对象(再生对象)的铝制部件并不限定于上述部件,该铝制部件在上述各种制造装置中被使用,能够应用表面劣化到成为处理障碍的程度的全部铝制部件。去除工序为去除铝制部件的氧化皮膜的一部分或全部的上层部或者以残留所述氧化皮膜的一部分的方式进行去除的工序。在氧化皮膜的劣化停留在氧化皮膜的一部分的情况下,去除劣化的氧化皮膜的上层部即可,也可以不去除健全的部位的氧化皮膜的上层部。另外,在氧化皮膜的劣化涉及到整个氧化皮膜的情况下,将氧化皮膜的全部上层部作为去除对象即可。此外,在氧化皮膜的劣化停留在氧化皮膜的一部分的情况下,也可以残留未劣化的氧化皮膜而去除劣化的氧化皮膜(在该情况下也可以不仅去除上层部还去除厚度方向上的全部)。去除氧化皮膜的上层部时的去除范围包括氧化皮膜的变色部位、粗面化部位、剥落部位或发生划痕部位等的劣化部位,并且设为包括这些劣化部位的周围在内的区域的氧化皮膜的上层部即可。另外,在劣化部位分布于氧化皮膜的大范围的情况下,去除氧化皮膜的全部上层部即可。将去除范围设为氧化皮膜的上层部的理由如下所述。氧化皮膜的劣化大多停留在氧化皮膜的表面或者表面附近,劣化到达氧化皮膜与部件主体的界面侧的情况较少。因此,上层部以外的部分未劣化,处于健全的状态。如果将这些健全的部分包含在去除范围内,则去除工序复杂,生产率下降。因此,将氧化皮膜的去除范围设为劣化的氧化皮膜的上层部。另外,通过将氧化皮膜的去除范围设为劣化的氧化皮膜的上层部,从而在进行去除工序到再生工序的期间,不会使基底的部件主体露出,能够通过残存的氧化皮膜来保护部件主体。另外,在去除氧化皮膜时,也不会存在误伤部件主体的危险。下面,对去除氧化皮膜的上层部的情况进行说明。图1a示出去除工序前的铝制部件的局部剖面示意图。如图1a所示,去除工序前的铝制部件1具备部件主体2和形成在部件主体2的表面的氧化皮膜3。另外,氧化皮膜3的一部分具有劣化部位3a。在该例子的去除工序中,去除包括劣化部位3a的周围在内的区域的氧化皮膜的上层部3b。此外,在图1a中,用“×”表示劣化部位。在图2a及图2b中也同样。图1b示出去除工序后的铝制部件1的局部剖面示意图。如图1b所示,经过去除工序,氧化皮膜3的厚度局部变小。在此,优选在去除氧化皮膜3的上层部3b时,如图1b所示,在将去除前的氧化皮膜3的厚度设为t时,以去除上层部3b后的氧化皮膜3的厚度t’在0.2t~0.5t的范围内的方式去除上层部3b。由于去除后的氧化皮膜3的厚度t’为0.2t以上,因此在再生工序中能够缩短为了增加氧化皮膜的厚度而所需的时间,因此优选。另外,由于去除后的氧化皮膜3的厚度t’为0.5t以下,因此能够完全去除劣化部位,因此优选。在去除工序中去除上层部后残存的氧化皮膜的表面无需是平坦面,也可以有波纹。即,残存膜厚也可以存在偏差。例如,在将去除前的氧化皮膜3的厚度设为t时,残存膜厚的偏差范围在0.2t~0.5t的范围内即可。在本实施方式的再生工序中实施的微弧氧化处理能够根据设定的电压值来调整膜厚,能够使再生后的膜厚均匀。因此,即使在去除工序中残存的氧化皮膜的膜厚存在偏差,也能够通过再生工序再生为均匀膜厚的氧化皮膜。此外,图1a及图1b所示的例子是去除氧化皮膜的一部分的上层部的例子。在劣化部位3a分布于氧化皮膜3的大范围的情况下,去除氧化皮膜3的全部上层部3b即可。去除工序为去除上层部3b的方法,能够采用机械研磨处理、喷砂处理或高压水喷射处理。作为机械研磨处理例如可列举将包含研磨材的研磨液涂布在氧化皮膜表面进行研磨的研磨处理、利用包含研磨材的刷子或布对氧化皮膜表面进行研磨的研磨处理、或者利用硬质研磨材对氧化皮膜表面进行研磨的研磨处理。作为喷砂处理可列举将干冰粉末喷射到氧化皮膜表面的喷砂处理。作为高压水喷射处理可列举将高压水喷射到氧化皮膜表面并去除劣化部位的处理。此外,在本实施方式的去除工序中,最好不进行利用蚀刻液的蚀刻处理。这是因为有可能过度蚀刻部件主体。在铝制部件为具有多个贯穿孔的板的情况下,可以以如下方式实施去除工序。如图2a的放大剖面示意图所示,去除工序前的板11具备部件主体12、沿部件主体12的厚度方向设置的多个贯穿孔12a、以及形成在部件主体12的表面及贯穿孔12a的内周面的氧化皮膜13。氧化皮膜13具有:氧化皮膜13a,形成在设置有部件主体12的贯穿孔12a的面;和氧化皮膜13b,设置在贯穿孔12a的内周面。在氧化皮膜13a、13b上具有劣化部位13c。图2b示出去除工序后的板11的放大剖面示意图。对板11进行的去除工序去除位于设置有部件主体12的贯穿孔12a的面上的氧化皮膜13a的上层部,而不去除形成在贯穿孔12a的内表面的氧化皮膜13b。由此,如图2b所示,去除工序后的板11与去除工序前相比,氧化皮膜13a的膜厚减少,而氧化皮膜13b的膜厚未减少。虽然在位于贯穿孔12a的内部的氧化皮膜13b中残留有劣化部位13c,但即便残留也不会在制造装置中的处理时发生不良情况,因此也可以不去除该劣化部位13c。此外,在进行去除工序之前,为了去除附着在铝制部件上的溶解性附着物,也可以利用水或有机溶剂对铝制部件进行清洗处理。接着,对再生工序进行说明。在再生工序中,通过将经过去除工序的铝制部件浸渍到电解液中,进行微弧氧化处理,从而使去除上层部的氧化皮膜的厚度增加。微弧氧化处理为伴随火花放电的阳极氧化处理,通过对在去除工序中去除上层部后膜厚变薄的氧化皮膜进行绝缘破坏而使新的氧化膜生长,并且直到氧化皮膜的膜厚增加并绝缘电阻提高为止继续进行氧化皮膜的生长。通过进行微弧氧化处理,能够在膜厚减少的氧化皮膜上形成新的氧化皮膜。由此,能够使去除上层部的氧化皮膜恢复到去除上层部之前的原始厚度。下面,对微弧氧化处理的优选条件进行说明。在本实施方式中,通过采用以下条件1或条件2中的任一条件来再生氧化皮膜,但本实施方式并不限定于该条件1、2。(条件1)在条件1中,将经过去除工序的铝制部件浸渍到电解液中,以规定的电流密度进行微弧氧化处理,在达到规定的电压之后,维持电压恒定。虽然在将电压设为恒定之后,电流密度逐渐下降,但在电流密度相对于电压恒定的处理开始时的电流密度为1/100~1/10的时刻,结束处理即可。微弧氧化处理时的电流密度优选为1~6a/dm2,更优选为1~4a/dm2。如果微弧氧化处理时的电流密度为1a/dm2以上,则放电充分,如果微弧氧化处理时的电流密度为6a/dm2以下,则在去除工序中未去除的氧化皮膜与新形成的氧化皮膜之间的边界上膜质均匀。另外,电解液的温度优选为-10~65℃。这是因为能够使用冷却器等小规模的冷却设备形成稳定的氧化皮膜而不使用大型冷却设备。作为电解液,例如可使用将磷酸氢二钠、三聚磷酸钠、磷酸二氢钠、超聚磷酸钠、硅酸钠、氢氧化钾、二磷酸钠、磷酸三钠、铝酸钠、偏硅酸钠及氢氧化钠等中的一种或它们中的混合物溶解在水中而成的物质。另外,如具有贯穿孔的板那样,在想要再生氧化皮膜的区域为大面积的情况下,也可以分多次进行微弧氧化处理。即,作为第一次处理,通过将铝制部件的一部分浸渍到电解液中进行微弧氧化处理,从而在浸渍的部位形成氧化皮膜。接着,作为第二次处理,将与第一次形成的氧化皮膜的部位不同的其他部位(剩余部位)浸渍到电解液中形成氧化皮膜。如此,也可以对需要再生氧化皮膜的部位分多次形成氧化皮膜。在第二次的氧化皮膜的形成时,由于第一次的氧化皮膜为绝缘膜,因此在第二次处理中,只在未形成第一次的氧化皮膜的部位集中形成氧化皮膜。(条件2)在条件2中,将经过去除工序的铝制部件浸渍到电解液中进行微弧氧化处理,但此时进行以下工序:直到200v以上的第一电压为止以恒定电流密度进行的第一工序;第二工序,不进行第一工序的利用第一电压的恒定电压处理,而是从第一电压到比第一电压低的电压的第二电压为止,在规定的时间使电压线性或阶段性地下降,进行微弧氧化处理;以及以第二电压进行恒定电压处理的第三工序。在第一工序中,利用第一电压的处理时间延续到成为200v以上的第一电压为止。另外,第一电压的处理开始时的电流密度优选在1a/dm2~20a/dm2的范围内。如果第一电压的处理开始时的电流密度为1a/dm2以上,则能够使电压充分上升并放电。另外,通过将电流密度设为20a/dm2以下,从而能够防止形成的氧化皮膜因放电而破坏,并且使皮膜结构致密并提高耐腐蚀性。第二工序为如下工序:在第一工序中成为第一电压之后,不进行利用第一电压的恒定电压处理,从第一电压到比第一电压低的电压的第二电压为止,在规定的时间使电压线性或阶段性地下降,进行微弧氧化处理。由此,能够避免在利用第一电压的恒定电压处理中的氧化皮膜的绝缘破坏,进而能够抑制功率消耗。优选在第二工序与第三工序之间,进行将电压从第二电压提高到第一电压的中间工序,将第二工序和中间工序作为一组工序,在第一工序之后反复进行多次该一组工序。由此,能够提高氧化皮膜的膜质。另外,“阶段性”是指利用第一电压与第二电压之间的电压进行至少一个恒定电压处理,在使电压阶段性地下降的情况下,优选将至少一个阶段的电压保持30秒以上。这是因为在难以形成氧化皮膜的部分形成氧化皮膜时需要时间。此外,该时间的上限最长为10小时。这是因为在超过10小时的情况下氧化皮膜因电解或电解液而腐蚀。另外,关于施加的电压及电流的波形,可以是交流、直流及交流与直流的叠加中的任一种,在交流的情况下,电流或电压可以是正弦波,也可以不是正弦波。如上所述,通过以恒定电压进行处理,从而能够在电流容易流动的地方即未形成氧化皮膜的地方依次形成氧化皮膜。第三工序为利用第二工序结束时的电压即第二电压进行规定时间的恒定电压处理的工序。处理时间优选为5分钟~10小时。在处理时间小于5分钟的情况下,氧化皮膜不能充分生长。另外,在处理时间超过10小时的情况下,氧化皮膜有可能会因电解或电解液而腐蚀。在第二条件中,如具有贯穿孔的板那样,在想要再生氧化皮膜的区域成为大面积的情况下,也可以分多次进行微弧氧化处理。图3a示出再生工序前的铝制部件1的剖面示意图,图3b示出再生工序后的铝制部件1的剖面示意图。由于进行微弧氧化处理,氧化皮膜3中的未去除上层部的部分3a即使经过再生工序其膜厚也几乎不发生变化,但在去除上层部后膜厚减少的部分3b中生长新的氧化皮膜而膜厚增加,优选增加到与部分3a相同的膜厚。为了调整新形成的氧化皮膜3的膜厚,优选以氧化膜生长至原始氧化膜的膜厚为止的方式调整微弧氧化处理的条件。具体而言,适当设定电压即可。在此,在图3b所示的例子中,未发现部件主体2在再生工序的前后发生较大的变化,但还具有部件主体2在再生工序的前后稍微变化的情况。即,由于微弧氧化处理为以基底的铝或铝合金为氧化皮膜的原料的成膜工艺,因此在膜厚减少的部分3b生长新的氧化皮膜时,膜厚减少的部分3b的正下方的部件主体2的表层也会从铝或铝合金替换为氧化皮膜。此外,图3a及图3b所示的例子为对去除氧化皮膜3的一部分上层部后的铝制部件1实施再生工序的例子。在对去除氧化皮膜3的全部上层部后的铝制部件实施再生工序的情况下,直到氧化皮膜的全部厚度为原始厚度为止使该氧化皮膜生长即可。在该情况下,还优选调整微弧氧化处理的条件。具体而言,适当设定电压即可。另外,在该情况下,去除上层部后部位的正下方的部件主体2的表层也会从铝或铝合金替换为氧化皮膜。即使在部件主体2的表层从铝或铝合金替换为氧化皮膜的情况下,也由于其替换量极少,因此不会在半导体制造装置或平板显示器制造装置的各种处理中产生故障。由于在去除工序中残存的氧化皮膜和在再生工序中新形成的氧化皮膜的膜质几乎相同,并且成为在再生前后几乎相同的膜厚,因此具有铝制部件所需的、对等离子体照射的耐久性、电气绝缘性及耐腐蚀性。此外,通过本实施方式的再生方法再生的板沿部件主体的板厚方向在部件主体设置有多个贯穿孔,在包括贯穿孔的内周面在内的部件主体的整个面形成有氧化皮膜,贯穿孔的内周面的氧化皮膜处于劣化的状态,除此以外的氧化皮膜处于未劣化的状态。因此,通过确认贯穿孔的内周面的氧化皮膜的状态,能够判断本实施方式的再生方法是否适用于板。如上所述,根据本实施方式,在对作为氧化皮膜的基底的部件主体不实施磨削或研磨的情况下,能够再生劣化的氧化皮膜。在以上说明的实施方式中说明了在去除氧化皮膜的上层部之后再生氧化皮膜的方法,但在本发明中,如图4a所示,在去除氧化皮膜3中的劣化部位的氧化皮膜的厚度方向全部13b之后,如图4b所示,也可以通过微弧氧化处理再生氧化皮膜3。与图1a及图1b所示的情况同样,此时的氧化皮膜的去除范围包括氧化皮膜的变色部位、粗面化部位、剥落部位或发生划痕部位等的劣化部位,并且设为包括这些劣化部位的周围在内的区域的氧化皮膜即可。即使在去除劣化的部位13b的氧化皮膜的厚度方向全部的情况下,也可以采用机械研磨处理、喷砂处理或高压水喷射处理,但最好设为不损伤作为氧化皮膜3的基底的部件主体2的处理条件。在去除工序之后,通过与上述实施方式同样进行利用微弧氧化处理的再生工序,从而能够再生氧化皮膜。另外,在以上说明的实施方式中,将在各种制造装置中使用且具有表面附着有异物的氧化皮膜或表面变质的氧化皮膜的铝制部件作为再生方法的对象。在以下说明的例子中,将具有表面产生不良部位的氧化皮膜的铝制部件作为对象。作为这种铝制部件,例如可举例说明如下部件:该部件在铝制部件的处理过程中,在氧化皮膜上产生剥离部、擦痕或凹痕等瑕疵或者磨损痕等不良部位。不良部位以外的氧化皮膜处于健全的状态。图5a示出具有凹痕24b的氧化皮膜3。虽然也可以对这种铝制部件进行如上所述的去除工序和再生工序,但还可以省略氧化皮膜的去除工序而进行再生工序。产生凹痕24b的氧化皮膜3为在凹痕24b的部分厚度局部减少的氧化皮膜。通过对这种氧化皮膜进行微弧氧化处理,从而能够在凹痕24b的部位形成新的氧化皮膜,由此能够消除凹痕24b并再生铝制部件。另外,在上述实施方式中说明了在再生工序中调整新形成的氧化皮膜的膜厚时,优选以氧化皮膜生长至成为原始氧化皮膜的膜厚的方式调整微弧氧化处理的条件,但本发明并不限于此,还可以以氧化皮膜生长至超过原始氧化皮膜的膜厚的膜厚的方式调整微弧氧化处理的条件。由此,能够利用新的氧化皮膜覆盖铝制部件整体,并且能够提高铝制部件的质量。[实施例]下面,根据实施例对本发明进行更详细说明。此外,以下说明的实施例示出本发明的一方式,本发明并不限定于该实施例。准备长1100mm、宽900mm、厚20mm的板。在板中设置有内径为0.69mm的多个贯穿孔。另外,该板为在铝合金制的部件主体上以平均15μm的厚度形成有氧化皮膜的板。通过微弧氧化处理法形成氧化皮膜。此时,在贯穿孔的内周面也形成有氧化皮膜。将上述板安装在作为平板显示器制造装置的等离子体成膜装置的腔室内,供给原料气体的同时对多张玻璃基板进行成膜处理。另外,在成膜处理的间歇时,适当进行将氟气流入腔室内的清洁处理。直到板的使用上限时间为止进行成膜处理和清洁处理,在经过使用上限时间之后,从腔室中取出板。在板的氧化皮膜的表面,通过氧化铝和氟气发生反应而形成氟化铝。作为去除工序,利用研磨布对板进行机械研磨处理,去除氧化皮膜的上层部。虽然去除范围以形成在板表面的全部氧化皮膜为对象,但不去除贯穿孔内的氧化皮膜。氧化皮膜的残存膜厚度为3~6μm的范围,存在若干偏差。在将原始氧化皮膜厚度设为t(15μm)时,,氧化皮膜的残存膜厚在0.2t~0.5t的范围内。接着,作为再生工序,将去除工序后的板浸渍到电解液中进行微弧氧化处理。作为电解液使用以将氢氧化钾、甲硅酸钠及磷酸三钠分别成为3g/l的方式溶解在纯水中而成的碱性电解液。将上述电解液放入设置有碳制相对电极的电解槽中,以直流的恒定电流进行微弧氧化处理。在直到达到450v为止以电流密度6.0a/dm2形成氧化皮膜之后,直到成为电流密度0.28a/dm2为止以450v进行恒定电压处理。电解液的温度为65℃以下。如此,再生氧化皮膜。与上述同样,将再生后的板安装在等离子体成膜装置的腔室内,与上述同样进行成膜处理和清洁处理,在经过使用上限时间之后,从腔室中取出板,与上述同样进行去除工序和再生工序。重复进行该一系列作业总计三次。将如此反复进行氧化皮膜的再生的板作为实施例的板。另一方面,作为去除工序,除了通过将氢氧化钠水溶液作为蚀刻液且将已使用的板浸渍到该蚀刻液中而去除全部氧化皮膜以外,以与上述实施例同样的方式调制比较例的簇射极板。对实施例及比较例的板调查氟化铝附着量少的区域的贯穿孔的内径变化。任意选择10个贯穿孔来测定内径,求出其平均值。在三次再生工序之后分别进行贯穿孔的内径测定。将结果示于下述表1。[表1]单位:mm使用前第一次再生第二次再生第三次再生实施例0.700.690.690.69比较例0.690.740.790.83如表1所示,可知实施例的板在反复进行再生的情况下,贯穿孔的内径也几乎没有变化,与此相对地,比较例的板在反复进行再生时内径扩大,贯穿孔的形状发生变化。另外,实施例的板虽然通过在去除工序中去除氧化皮膜的上层部而残留氧化皮膜的剩余部分并未露出部件主体,但由于在再生工序中进行微弧氧化处理,因此能够形成新的氧化皮膜。在实施例中,在去除工序中残存的氧化皮膜与新形成的氧化皮膜之间未确认到界面等的明确的边界,残存的氧化皮膜与新的氧化皮膜一体化。另外,实施例的板虽然在去除工序中产生氧化皮膜的去除量的偏差,但再生后的氧化皮膜的膜厚几乎为15μm,不产生膜厚的偏差。此外,对于实施例的板来说,由于在去除工序中残存氧化皮膜,因此通过残存的氧化皮膜来保护部件主体,部件主体不会产生划痕等。另一方面,对于比较例的板来说,由于在去除工序中去除全部氧化皮膜,因此再生工序的作业时间比实施例的情况长。附图标记说明1…铝制部件;2、12…部件主体;3…氧化皮膜;3b…氧化皮膜的上层部;11…板;12a…贯穿孔;13a…设置有贯穿孔的面的氧化皮膜;13b…形成在贯穿孔的内表面的氧化皮膜。当前第1页12