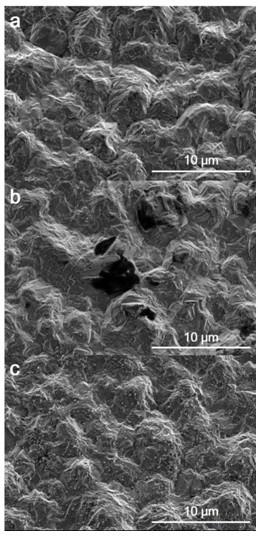
[0001]
本发明涉及电解铜箔技术领域,具体来说,涉及一种改进的平板电沉积铜箔制备方法。
背景技术:[0002]
随着时代进步发展,电解铜箔的生产工艺也需要随之进行不断的优化改进。而当需要对电解铜箔生产工艺进行一些探索性实验时,如果使用生产时的制备方法,一方面由于需要对整个生产线进行调整,涉及人员及环节较多而使得操作较不方便,另一方面因为生产线的大规模运作,会造成时间和成本的很大浪费。因此一般的电解铜箔生产方式并不适用于进行如电解液浓度、添加剂配方等工艺参数的探索实验。
[0003]
平板电镀制备铜箔是比较好的进行探索性实验的方式。但相比于生产线制备,平板电镀需要的手工操作更多,相对较难控制,且操作的要求指标也不同,环境条件并不一定是最优,因此很多时候制备方法的细节会对铜箔质量有着关键的影响。阴极板的表面状态对铜箔的表面状态有直接的影响,尤其是对铜箔的光面。在粗糙度大的表面,其实际面积比表观面积大更多,使得有些区域实际电流密度比表观电流密度小很多,使得铜晶粒的生长条件改变而导致局部的不均匀程度增多,从而粗糙度也就大一些,因此一般阴极板的粗糙度会要求较小一些,但是另一个方面,阴极板粗糙度过小也可能会对铜箔产生不利的影响。此外,其他细节,例如钝化操作时最后的干燥步骤中附着钝化液能否有效去除等,也是直接影响铜箔外观质量和物理性能的重要因素。
[0004]
各研究单位也对平板电镀实验的装置展开了较多研究。专利(申请号:201320377455.6)公开了一种铜箔电镀实验装置,装置包括储液槽、电镀槽、温控仪、供液泵等部件,使用极板固定支架来固定平板电极。专利(申请号:201320596253.0)公开了一种用于研究纳米复合镀工艺条件的实验装置,包括电镀槽槽体、电镀槽槽盖、温控装置、电镀液机械搅拌装置和电极阴阳极间距离调整装置,热电偶、叶片中心轴、阳极电极和阴极电极之间的相对位置可调。。专利(申请号:201320146361.8)公开了一种均匀电镀试验槽,其阴阳极板采用平板结构,设有极板固定架和相应的极板插槽。其着重点一般为实验的操作方便性和参数可调性,本身基本对电解铜箔性能的改变作用较小。
[0005]
此外,由于平板电解条件及添加剂等的影响,一般光面的压应力大于毛面,导致铜箔必须通过向毛面变形翘曲来达到宏观应力的降低平衡。但铜箔翘曲会对后续工艺处理操作产生不便,且可能由于内应力不平衡的关系导致易产生应力集中而影响机械性能。因此在铜箔制备过程中消除应力是获得优质铜箔的重要环节之一。
[0006]
目前较为常见的减小生箔翘曲的方法为使用添加剂。专利(申请号:201910247097.9)公开了一种6μm双光低翘曲电解铜箔用添加剂及该电解铜箔的生产工艺,所述添加剂由浓度为2-6g/l的kh-5水溶液、浓度为4-8g/l的低分子胶水溶液和浓度为4-8g/l的聚二硫二丙烷磺酸钠水溶液组成,且在电沉积生成铜箔时,所述添加剂三种组分的水溶液分别按kh-5为50-100ml/min,低分子胶为50-100ml/min,聚二硫二丙烷磺酸钠为
l/min;一方面保证添加剂充分扩散均匀,循环状态稳定,且极板能被预热到足够温度;另一方面避免控制循环时间过长而降低电解铜箔制备的效率。
[0014]
进一步地,步骤2)所述电解液达到设定温度中设定温度为50-60 ℃;进一步地,步骤2)所述配置电解液,电解液的铜离子浓度为60-110 g/l、硫酸浓度为90-120 g/l、氯离子浓度为15-30 mg/l。
[0015]
进一步地,步骤3)电解的过程中,保持通过循环泵让电解液循环流动,使铜离子、添加剂在电解过程中分布均匀,循环流速为5 l/min。
[0016]
进一步地,步骤3)所述电流密度为45-65 a/dm
2
进一步地,步骤3)所述设定时间由所需制得的铜箔的厚度确定。
[0017]
进一步地,步骤4)所述钝化的时间为5-8s,所述干燥的步骤为:将铜箔取出置于两张吸水纸之间,均匀按压上层吸水纸5-10 s后移除并立即吹干。
[0018]
采用以上技术方案,本发明可达到以下效果:(1)通过弯曲极板对电解中个的铜箔施加预应力可以有效抵消致使铜箔产生翘曲的内应力,无需另加添加剂即可降低铜箔翘曲。(2)在近似工厂生产的工艺条件下,可以便捷有效地改变如添加剂、铜离子浓度、电流密度等多种工艺参数,并快速获得探索性实验的铜箔样品,节约了时间和成本。(3)明确了制备符合要求的铜箔的阴极板沉积面的粗糙度范围,避免粗糙度过低导致的缺陷。(4)明确并完善了平板电镀中如阴极板处理、电解准备工作、钝化相关处理等的部分细节,使在非超净间等的一般制备条件下的电解铜箔颜色均匀性、针孔情况等稳定可控,减少由于制备方法操作而非电解参数导致的性能减弱。(5)所制备的铜箔物理性能较好,光面粗糙度ra<0.3 μm,毛面粗糙度rz<3.0 μm,常温抗拉强度>270 mpa,常温延伸率>4%。
附图说明
[0019]
图1为所述平板电镀装置(a)和弯曲极板(b)的示意图,其中1为阳极板,2为阴极板,3为循环泵。
[0020]
图2为实施例1的铜箔光面外观(a)和针孔情况(b)及比较例1的铜箔光面外观(c)和针孔情况(d)。
[0021]
图3为实施例1的铜箔毛面外观(a)及比较例2的铜箔毛面外观(b)及针孔区域局部放大图(c)。
[0022]
图4为放置一周后实施例4的铜箔毛面sem图像(a)、比较例4的铜箔毛面sem图像(b)和比较例5的铜箔毛面sem图像(c)。
[0023]
图5为实施例1的铜箔毛面外观(a) 及比较例6的铜箔毛面外观(b)和光面外观(c)。
[0024]
图6为长度及宽度方向弧度值均为0.3(17.19
°
)的极板示意图。该极板曲面曲率为362.5 mm;极板厚为3 mm;极板截面弧高为7.04 mm;极板截面长度为108.34 mm。
[0025]
具体实施方式
[0026]
本发明各实施例及比较例均使用平板电镀装置,所采用的平板电镀装置的结构示意图如附图1(a)所示,电解槽内设置有阳极板槽1、阴极板槽2,极板置于极板槽中且平行相
对,两极板槽中心线距离为10 mm。另外如图中所示,平板电镀装置还附有循环泵3,电解过程中可通过该循环泵使电解液循环流动,从而使铜离子、添加剂等分布均匀。
[0027]
在各实施例及比较例中,阴极板采用纯钛板,阳极板采用镀氧化铱膜的钛板。其中实施例1-6,比较例8使用改变形状的阴极板及阳极板,实施例1-4,比较例1-7均使用平板电极,改变形状的电极板的示意图如附图1(b)所示,阴极板及阳极板形状完全一致,平行放置。如附图6为改变形状的阴极板及阳极板的极板示意图;其中图中所示的极板为长度及宽度方向弧度值均为0.3(17.19
°
),该极板曲面曲率为362.5 mm;极板厚为3 mm;极板截面弧高为7.04 mm;极板截面长度为108.34 mm。
[0028]
下面结合具体的实施例对本发明进行更为具体的说明。
[0029]
实施例1:具体制备过程包括如下步骤:(1)对阴极板沉积面进行2000目水砂纸打磨、2.5 μm抛光剂抛光至表面粗糙度ra=0.15 μm。极板的弯曲弧度为0.1,弯曲度为1%。
[0030]
(2)使用流水从阴极板的上部向下部进行冲洗,并沿水流方向使用脱脂棉向下略用力进行擦拭。冲洗擦拭约1 min后,使用去离子水针对可见残余颗粒进行局部喷洗,方向依旧为从上到下。至阴极板表面无肉眼可见颗粒物且水膜均匀向下流动无阻碍,后进行乙醇除油及稀硝酸除氧化膜。
[0031]
(3)电解液中铜离子浓度为60-110 g/l,硫酸浓度为100 g/l,氯离子浓度为15-20 mg/l。
[0032]
(4)电解制备铜箔,温度为55-60 ℃,电流密度为48 a/dm
2
,所得铜箔厚度为18 μm。
[0033]
(5)电解完成后,对铜箔表面进行流水冲洗洗去附着的硫酸铜溶液,将表面完全吹干,揭下后依次经过稀盐酸洗、水洗,钝化5-8s后,取出置于两张吸水纸之间,均匀按压上层吸水纸5-10 s后移除并迅速吹干。
[0034]
所得铜箔样品主要物理性能为:光面粗糙度ra=0.134 μm;毛面粗糙度rz=2.487 μm;常温抗拉强度=293 mpa;常温延伸率=6.5%;翘曲为3 mm。
[0035]
实施例2:具体制备过程包括如下步骤:(1)对阴极板沉积面进行2000目水砂纸打磨、2.5 μm抛光剂抛光至表面粗糙度ra=0.2 μm。极板的弯曲弧度为0.2,弯曲度为6%。
[0036]
(2)使用流水从阴极板的上部向下部进行冲洗,并沿水流方向使用脱脂棉向下略用力进行擦拭。冲洗擦拭约1 min后,使用去离子水针对可见残余颗粒进行局部喷洗,方向依旧为从上到下。至阴极板表面无肉眼可见颗粒物且水膜均匀向下流动无阻碍,后进行乙醇除油及稀硝酸除氧化膜。
[0037]
(3)电解液中铜离子浓度为60-110 g/l,硫酸浓度为100 g/l,氯离子浓度为15-20 mg/l,添加剂为糖精钠0.4 mg/l。
[0038]
(4)加入添加剂后,在电解前先对电解液进行15 min的循环,然后电解制备铜箔,温度为55-60 ℃,电流密度为48 a/dm
2
,所得铜箔厚度为18 μm。
[0039]
(5)电解完成后,对铜箔表面进行流水冲洗洗去附着的硫酸铜溶液,将表面完全吹
μm。极板的弯曲弧度为0.1,弯曲度为1%。
[0057]
(2)(3)(4)(5)同实施例1。
[0058]
所得铜箔样品毛面粗糙度rz=2.466 μm,光面有局部不光亮和针孔密集区。
[0059]
比较例2:具体制备过程包括如下步骤:(1)同实施例1。
[0060]
(2)只使用流水普通冲洗,即通常的不控制冲洗水流方向,不进行脱脂棉擦拭,之后直接进行乙醇除油及稀硝酸除氧化膜。
[0061]
(3)(4)(5)同实施例1。
[0062]
比较例3:具体制备过程包括如下步骤:(1)(2)(3)同实施例2。
[0063]
(4)加入添加剂后,在电解前先对电解液进行5 min的循环,然后电解制备铜箔,温度为55-60 ℃,电流密度为48 a/dm
2
,所得铜箔厚度为18 μm。
[0064]
(5)同实施例2。
[0065]
所得铜箔样品毛面粗糙度rz=2.616μm。
[0066]
比较例4:具体制备过程包括如下步骤:(1)(2)(3)(4)同实施例4,(3)中羟乙基纤维素添加剂浓度为0.4 mg/l。
[0067]
(5)电解完成后,对铜箔表面进行流水冲洗洗去附着的硫酸铜溶液,将表面完全吹干,揭下后依次经过稀盐酸洗、水洗,钝化3 s后,取出置于两张吸水纸之间,均匀按压上层吸水纸5-10 s后移除并迅速吹干。
[0068]
所得铜箔样品主要物理性能为:光面粗糙度ra=0.148 μm;毛面粗糙度rz=2.466 μm;常温抗拉强度=297mpa;常温延伸率=5.5%。
[0069]
比较例5:具体制备过程包括如下步骤:(1)(2)(3)(4)同实施例4,(3)中羟乙基纤维素添加剂浓度为0.3 mg/l。
[0070]
(5)电解完成后,对铜箔表面进行流水冲洗洗去附着的硫酸铜溶液,将表面完全吹干,揭下后依次经过稀盐酸洗、水洗,钝化10s后,取出置于两张吸水纸之间,均匀按压上层吸水纸5-10 s后移除并迅速吹干。
[0071]
所得铜箔样品主要物理性能为:光面粗糙度ra=0.161 μm;毛面粗糙度rz=2.193 μm;常温抗拉强度=283 mpa;常温延伸率=7.8%。
[0072]
比较例6:具体制备过程包括如下步骤:(1)(2)(3)(4)同实施例1。
[0073]
(5)电解完成后,对铜箔表面进行流水冲洗洗去附着的硫酸铜溶液,将表面完全吹干,揭下后依次经过稀盐酸洗、水洗,钝化6 s后,取出直接吹干。
[0074]
比较例7:具体制备过程包括如下步骤:
μm,与实施例相差0.4μm,更接近无添加剂的实施例1的值。由此可见,对加入添加剂、放入极板后的电解液需要进行一定时间循环,使得添加剂在电解液中扩散均匀,在极板上有效吸附,同时通过电解液传热于极板使之达到要求的温度,才能保证所制备铜箔性能的稳定可靠。
[0086]
图4为一周后实施例4的铜箔毛面sem图像(a)、比较例4的铜箔毛面sem图像(b)和比较例5的铜箔毛面sem图像(c),其制备方法的区别仅在于钝化处理的时间。对比各sem图可以发现,钝化时间为3 s的铜箔在铜颗粒的峰顶出现了絮状黑色物质,为铜箔被氧化生成的氧化物,宏观表现为铜箔表面局部颜色变深;钝化时间为10 s的铜箔,在铜颗粒表面附着有较为密集的白色颗粒,为多余的钝化液成分,宏观表现为铜箔发白。上述二者均不利于铜箔微观形貌的观察和铜箔的外观质量。而实施例4的铜箔均无上述现象,且质量良好。
[0087]
图5为实施例1的铜箔毛面外观(a)及比较例6的铜箔毛面外观(b)和光面外观(c),二者制备方法的区别仅在于钝化后先使用上下两层吸水纸按压吸去液体还是直接吹干。从图中可以直观地看出,未使用吸水纸而是直接吹干的铜箔表面水渍分布较多,颜色不均匀,并且光面发白,直接影响铜箔外观。水渍区域的铜箔也更易发生氧化,对性能也较为不利。而使用吸水纸按压吸收液体,一方面可以减少吹干步骤的时间,使水分更易挥发,有效减少水渍的残留;另一方面使用吸水纸可以除去附着在铜箔上的多余的钝化液,防止水分吹干后钝化液未使用成分的残留而影响铜箔表面。
[0088]
实施例1极板弯曲弧度为0.1时,比较比较例8的无弯曲极板,翘曲减小了3 mm;实施例6极板弯曲弧度为0.3时,比较比较例9的无弯曲极板,翘曲减小了10 mm;比较例7相比实施例6则翘曲的减小量基本相同,但弯曲程度更大的比较例7出现了毛面不均匀现象。由此可以看出,相比于一般的平板电极电镀,使用改进后的弯曲程度在所述范围内的极板对电解铜箔施加的力向光面弯曲的力,确实能够抵消一定的向毛面弯曲的电解残余应力,从而使翘曲减小。在一定范围内,弯曲弧度越大,对翘曲的改善程度越好,但当弯曲程度再继续增大时,一方面对于翘曲的降低效果基本不在增加,另一方面由于极板弯曲程度过大,不能近似为一般平板电镀,会导致极板间水流的流速分布不再均匀,局部区域贫铜从而出现颜色不均匀甚至是烧焦现象。