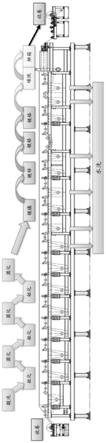
1.本发明涉及一种0.1毫米超幅宽压延铜箔的表面处理工艺。属于压延铜箔表面处理技术领域。
背景技术:2.目前现有的技术都是针对电解厚铜来进行生产,其本身使用的后处理的粗化和固化段经过2道电镀,并且其电流的粗化、固化电流的总量未达20000a,若改为压延铜箔,其粗糙度过低,利用一般的电解厚铜的后处理技术,无法使用在压延铜箔上,会导致其抗剥离不合格。
3.针对压延厚铜(0.01mm以上的铜箔)的后处理工艺技术,排除设备上的张力技术问题,针对后处理的电镀与抗氧化技术来说,一般电解厚铜由于本身粗糙度过高(rz≧8微米)高温延伸低,故其后处理段的粗化、固化需要的电流极低,就能维持相应的抗剥离强度,但变成压延后铜后,其粗糙度极低(rz≦3微米),由于压延铜箔有较高的延伸率和低粗糙度的特色,故在后处理的粗化和固化段需要经过3道以上的电镀,利用多段电镀来增加其粗糙度,并且其电流的粗化、固化电流的总量应达到24000a以上,让其抗剥离强度符合标准(1.1n/mm2以上),且铜箔表面上需涂布了镍、锌、铬,主要是为了追求在ccl压合时所产生的高温(140度以上),故铜箔(光面)杂项金属含量都达到23mg/m2甚至25mg/m2以上。
技术实现要素:4.本发明提出一种利用多段电镀来增加其粗糙度,成品(毛面)rz在3微米以下、高温延伸在15%以上、高温抗拉强度在200n/mm2以上的0.1毫米超幅宽压延铜箔的表面处理工艺,解决现有技术存在的问题。
5.为了解决上述技术问题,本发明的技术方案为:
6.一种0.1毫米超幅宽压延铜箔的表面处理工艺包括前处理端和后处理端;
7.所述前处理端包括以下步骤:
8.步骤一:先将铜熔炼铸造成锭,再经铜块熔融、热轧开胚、双面铣、粗轧、第一次退火、第一次清洗切边、第一次精轧、第二次清洗、第二次退火、第二次精轧、第三次清洗、第三次退火、收卷成品,得到0.10mm的双面光滑铜箔;
9.所述后处理端包括以下步骤:
10.步骤一:酸洗:铜箔用浓度≤20%的稀硫酸酸洗,酸洗温度为30
‑
40℃,酸洗液中h2so4的浓度为150g/l~160g/l;
11.步骤二:一次粗化:铜箔送入粗化槽进行一次粗化处理,粗化槽中盛装cuso4溶液,其中cu
2+
质量浓度为40
‑
50g/l,聚乙烯亚胺质量浓度为10
‑
35g/l,h2so4质量浓度为101
‑
135g/l,温度为30
‑
45℃,电流密度为50
‑
60a/dm2,处理时间为1
‑
5s;用聚乙烯亚胺做添加剂,在铜箔的生产过程中会随着电解液的电镀产生亮斑,提高铜箔的抗拉强度;
12.步骤三:一次固化:进行固化处理,固化所用的电镀液中cu
2+
质量浓度为40
‑
50g/l,
h2so4质量浓度为101
‑
135g/l,温度为45
‑
55℃,电流密度为50
‑
60a/dm2,处理时间为5
‑
10s;
13.步骤四:二次粗化:铜箔送入粗化槽进行二次粗化处理,粗化槽中盛装cuso4溶液,其中cu
2+
质量浓度为40
‑
50g/l,六偏磷酸钠质量浓度为70
‑
80g/l,h2so4质量浓度为101
‑
135g/l,温度为35
‑
60℃,电流密度为55
‑
70a/dm2,处理时间为5
‑
10s;六偏磷酸钠配合有效提高所得铜箔在粗化和固化前的均匀稳定性,同时在成膜时,六偏磷酸钠的遮盖性好,一方面混合物体系稳定,另一方面后期烘烤过程中能提高铜箔的抗剥离强度;
14.步骤五:二次固化:进行固化处理,固化所用的电镀液中cu
2+
质量浓度为40
‑
50g/l,h2so4质量浓度为101
‑
135g/l,温度为45
‑
55℃,电流密度为50
‑
60a/dm2,处理时间为5
‑
10s;
15.步骤六:三次粗化:铜箔送入粗化槽进行二次粗化处理,粗化槽中盛装cuso4溶液,其中cu
2+
质量浓度为40
‑
50g/l,2
‑
巯基吡啶质量浓度为80
‑
90g/l,h2so4质量浓度为101
‑
135g/l,温度为35
‑
60℃,电流密度为55
‑
70a/dm2,处理时间为5
‑
10s;2
‑
巯基吡啶的亮度偏低,粗度太高,也有提升抗拉的效果;
16.步骤七:三次固化:进行固化处理,固化所用的电镀液中cu
2+
质量浓度为40
‑
50g/l,h2so4质量浓度为101
‑
135g/l,温度为45
‑
55℃,电流密度为50
‑
60a/dm2,处理时间为5
‑
10s;
17.步骤八:镀镍:电镀液中的镍离子的浓度为3.0g/l~4.5g/l,ph为10
‑
11.5,电镀液的温度为35℃~40℃,电流密度为0.8
‑
1.5a/dm2;
18.步骤九:镀锌:电镀液中的锌离子的浓度为5.0g/l~7.0g/l,ph为10
‑
11.5,电镀液的温度为35℃~40℃,电流密度为0.5
‑
0.9a/dm2;
19.步骤九:一次镀铬:电镀液中的铬离子的浓度为1.5g/l~2.5g/l,ph为10
‑
11.5,电镀液的温度为20℃~25℃,电流密度为0.8
‑
1.5a/dm2;
20.步骤十:二次镀铬:电镀液中的铬离子的浓度为1.5g/l~2.5g/l,ph为10
‑
11.5,电镀液的温度为30℃~35℃,电流密度为0.8
‑
1.5a/dm2;
21.步骤十一:涂硅烷:在铜箔最外层的镀锌镍铬防氧化层外喷涂硅烷偶联剂;
22.步骤十二:烘烤收卷。
23.所述后处理端中步骤十二得到的压延铜箔的厚度为0.05mm~0.10mm,所述压延铜箔的表面粗糙度rz值为0.05μm~0.3μm。
24.所述前处理端中步骤一第一次退火的退火温度为400℃~500℃,升温时间为4~5h,保温时间为4~6h,第二次退火的退火温度为300℃~400℃,升温时间为4~5h,保温时间为4~6h,第三次退火温度为250℃~300℃,升温时间为4~5h,保温时间为4~6h。
25.所述前处理端中步骤一粗轧的轧制力为440n~460n,轧制速度为800m/min,铜箔的入侧厚度为0.1500mm,出侧厚度为0.0620mm,弯辊力为3mpa。
26.所述前处理端中步骤一第一次精轧的轧制力为440n~460n,轧制速度为750m/min,铜箔的入侧厚度为0.0620mm,出侧厚度为0.0212mm,弯辊力为2mpa。
27.所述前处理端中步骤一第二次精轧的轧制力为450n~500n,轧制速度为700m/min,铜箔入侧厚度为0.0212mm,出侧厚度为0.0091mm,弯辊力为1mpa。
28.本发明涉及的一种0.1毫米超幅宽压延铜箔的表面处理工艺由于压延铜箔有较高的延伸率和低粗糙度的特色,故在后处理的粗化和固化段需要经过3道以上的电镀,利用多段电镀来增加其粗糙度,并且其电流的粗化、固化电流的总量应达到24000a以上,让其抗剥离强度符合标准(1.1n/mm2以上),且铜箔表面上需涂布了镍、锌、铬,主要是为了追求在ccl
压合时所产生的高温(140度以上),故铜箔(光面)杂项金属含量都达到23mg/m2甚至25mg/m2以上,压延铜箔的铜箔成品(毛面)rz需在3微米以下、高温延伸应该在15%以上、高温抗拉强度应在200n/mm2以上。
附图说明
29.为了更清楚地说明本发明实施例或现有技术中的技术方案,下面将对实施例或现有技术描述中所需要使用的附图作简单地介绍,显而易见地,下面描述中的附图仅仅是本发明的一些实施例,对于本领域普通技术人员来讲,在不付出创造性劳动性的前提下,还可以根据这些附图获得其他的附图。
30.图1为本发明一种0.1毫米超幅宽压延铜箔的表面处理工艺的工艺流程图;
31.图2为一般铜箔的扫描电子显微镜的sem图;
32.图3为本发明一种0.1毫米超宽压延铜箔的的扫描电子显微镜的sem图。
具体实施方式
33.下面结合附图对本发明的具体实施方式作进一步说明。在此需要说明的是,对于这些实施方式的说明用于帮助理解本发明,但并不构成对本发明的限定。此外,下面所描述的本发明各个实施方式中所涉及的技术特征只要彼此之间未构成冲突就可以相互组合。
34.一种0.1毫米超幅宽压延铜箔的表面处理工艺包括前处理端和后处理端;
35.所述前处理端包括以下步骤:
36.步骤一:先将铜熔炼铸造成锭,再经铜块熔融、热轧开胚、双面铣、粗轧、第一次退火、第一次清洗切边、第一次精轧、第二次清洗、第二次退火、第二次精轧、第三次清洗、第三次退火、收卷成品,得到0.10mm的双面光滑铜箔;所述前处理端中步骤一第一次退火的退火温度为400℃~500℃,升温时间为4~5h,保温时间为4~6h,第二次退火的退火温度为300℃~400℃,升温时间为4~5h,保温时间为4~6h,第三次退火温度为250℃~300℃,升温时间为4~5h,保温时间为4~6h。
37.所述前处理端中步骤一粗轧的轧制力为440n~460n,轧制速度为800m/min,铜箔的入侧厚度为0.1500mm,出侧厚度为0.0620mm,弯辊力为3mpa。所述前处理端中步骤一第一次精轧的轧制力为440n~460n,轧制速度为750m/min,铜箔的入侧厚度为0.0620mm,出侧厚度为0.0212mm,弯辊力为2mpa。所述前处理端中步骤一第二次精轧的轧制力为450n~500n,轧制速度为700m/min,铜箔入侧厚度为0.0212mm,出侧厚度为0.0091mm,弯辊力为1mpa。
38.所述后处理端包括以下步骤:
39.步骤一:酸洗:铜箔用浓度≤20%的稀硫酸酸洗,酸洗温度为30
‑
40℃,酸洗液中h2so4的浓度为150g/l~160g/l;
40.步骤二:一次粗化:铜箔送入粗化槽进行一次粗化处理,粗化槽中盛装cuso4溶液,其中cu
2+
质量浓度为40
‑
50g/l,聚乙烯亚胺质量浓度为10
‑
35g/l,h2so4质量浓度为101
‑
135g/l,温度为30
‑
45℃,电流密度为50
‑
60a/dm2,处理时间为1
‑
5s;用聚乙烯亚胺做添加剂,在铜箔的生产过程中会随着电解液的电镀产生亮斑,提高铜箔的抗拉强度;
41.步骤三:一次固化:进行固化处理,固化所用的电镀液中cu
2+
质量浓度为40
‑
50g/l,h2so4质量浓度为101
‑
135g/l,温度为45
‑
55℃,电流密度为50
‑
60a/dm2,处理时间为5
‑
10s;
42.步骤四:二次粗化:铜箔送入粗化槽进行二次粗化处理,粗化槽中盛装cuso4溶液,其中cu
2+
质量浓度为40
‑
50g/l,六偏磷酸钠质量浓度为70
‑
80g/l,h2so4质量浓度为101
‑
135g/l,温度为35
‑
60℃,电流密度为55
‑
70a/dm2,处理时间为5
‑
10s;六偏磷酸钠配合有效提高所得铜箔在粗化和固化前的均匀稳定性,同时在成膜时,六偏磷酸钠的遮盖性好,一方面混合物体系稳定,另一方面后期烘烤过程中能提高铜箔的抗剥离强度;
43.步骤五:二次固化:进行固化处理,固化所用的电镀液中cu
2+
质量浓度为40
‑
50g/l,h2so4质量浓度为101
‑
135g/l,温度为45
‑
55℃,电流密度为50
‑
60a/dm2,处理时间为5
‑
10s;
44.步骤六:三次粗化:铜箔送入粗化槽进行二次粗化处理,粗化槽中盛装cuso4溶液,其中cu
2+
质量浓度为40
‑
50g/l,2
‑
巯基吡啶质量浓度为80
‑
90g/l,h2so4质量浓度为101
‑
135g/l,温度为35
‑
60℃,电流密度为55
‑
70a/dm2,处理时间为5
‑
10s;2
‑
巯基吡啶的亮度偏低,粗度太高,也有提升抗拉的效果;
45.步骤七:三次固化:进行固化处理,固化所用的电镀液中cu2+质量浓度为40
‑
50g/l,h2so4质量浓度为101
‑
135g/l,温度为45
‑
55℃,电流密度为50
‑
60a/dm2,处理时间为5
‑
10s;
46.步骤八:镀镍:电镀液中的镍离子的浓度为3.0g/l~4.5g/l,ph为10
‑
11.5,电镀液的温度为35℃~40℃,电流密度为0.8
‑
1.5a/dm2;
47.步骤九:镀锌:电镀液中的锌离子的浓度为5.0g/l~7.0g/l,ph为10
‑
11.5,电镀液的温度为35℃~40℃,电流密度为0.5
‑
0.9a/dm2;
48.步骤九:一次镀铬:电镀液中的铬离子的浓度为1.5g/l~2.5g/l,ph为10
‑
11.5,电镀液的温度为20℃~25℃,电流密度为0.8
‑
1.5a/dm2;
49.步骤十:二次镀铬:电镀液中的铬离子的浓度为1.5g/l~2.5g/l,ph为10
‑
11.5,电镀液的温度为30℃~35℃,电流密度为0.8
‑
1.5a/dm2;
50.步骤十一:涂硅烷:在铜箔最外层的镀锌镍铬防氧化层外喷涂硅烷偶联剂;
51.步骤十二:烘烤收卷。
52.所述后处理端中步骤十二得到的压延铜箔的厚度为0.05mm~0.10mm,所述压延铜箔的表面粗糙度rz值为0.05μm~0.3μm。
53.实施例1:
54.一种0.1毫米超幅宽压延铜箔的表面处理工艺包括前处理端和后处理端;
55.所述前处理端包括以下步骤:
56.步骤一:先将铜熔炼铸造成锭,再经铜块熔融、热轧开胚、双面铣、粗轧、第一次退火、第一次清洗切边、第一次精轧、第二次清洗、第二次退火、第二次精轧、第三次清洗、第三次退火、收卷成品,得到0.10mm的双面光滑铜箔;所述前处理端中步骤一第一次退火的退火温度为400℃,升温时间为4h,保温时间为4h,第二次退火的退火温度为300℃℃,升温时间为4h,保温时间为4h,第三次退火温度为250℃℃,升温时间为4h,保温时间为4h。
57.所述前处理端中步骤一粗轧的轧制力为460n,轧制速度为800m/min,铜箔的入侧厚度为0.1500mm,出侧厚度为0.0620mm,弯辊力为3mpa。所述前处理端中步骤一第一次精轧的轧制力为460n,轧制速度为750m/min,铜箔的入侧厚度为0.0620mm,出侧厚度为0.0212mm,弯辊力为2mpa。所述前处理端中步骤一第二次精轧的轧制力为500n,轧制速度为700m/min,铜箔入侧厚度为0.0212mm,出侧厚度为0.0091mm,弯辊力为1mpa。
58.所述后处理端包括以下步骤:
59.步骤一:酸洗:铜箔用浓度≤20%的稀硫酸酸洗,酸洗温度为30℃,酸洗液中h2so4的浓度为150g/l;
60.步骤二:一次粗化:铜箔送入粗化槽进行一次粗化处理,粗化槽中盛装cuso4溶液,其中cu
2+
质量浓度为40g/l,聚乙烯亚胺质量浓度为10g/l,h2so4质量浓度为101g/l,温度为30℃,电流密度为50a/dm2,处理时间为1s;用聚乙烯亚胺做添加剂,在铜箔的生产过程中会随着电解液的电镀产生亮斑,提高铜箔的抗拉强度;
61.步骤三:一次固化:进行固化处理,固化所用的电镀液中cu
2+
质量浓度为50g/l,h2so4质量浓度为135g/l,温度为55℃,电流密度为60a/dm2,处理时间为10s;
62.步骤四:二次粗化:铜箔送入粗化槽进行二次粗化处理,粗化槽中盛装cuso4溶液,其中cu
2+
质量浓度为40g/l,六偏磷酸钠质量浓度为80g/l,h2so4质量浓度为135g/l,温度为60℃,电流密度为70a/dm2,处理时间为10s;六偏磷酸钠配合有效提高所得铜箔在粗化和固化前的均匀稳定性,同时在成膜时,六偏磷酸钠的遮盖性好,一方面混合物体系稳定,另一方面后期烘烤过程中能提高铜箔的抗剥离强度;
63.步骤五:二次固化:进行固化处理,固化所用的电镀液中cu
2+
质量浓度为50g/l,h2so4质量浓度为135g/l,温度为55℃,电流密度为60a/dm2,处理时间为10s;
64.步骤六:三次粗化:铜箔送入粗化槽进行二次粗化处理,粗化槽中盛装cuso4溶液,其中cu
2+
质量浓度为50g/l,2
‑
巯基吡啶质量浓度为90g/l,h2so4质量浓度为135g/l,温度为60℃,电流密度为70a/dm2,处理时间为10s;2
‑
巯基吡啶的亮度偏低,粗度太高,也有提升抗拉的效果;
65.步骤七:三次固化:进行固化处理,固化所用的电镀液中cu2+质量浓度为50g/l,h2so4质量浓度为135g/l,温度为55℃,电流密度为60a/dm2,处理时间为10s;
66.步骤八:镀镍:电镀液中的镍离子的浓度为4.5g/l,ph为10,电镀液的温度为40℃,电流密度为1.5a/dm2;
67.步骤九:镀锌:电镀液中的锌离子的浓度为7.0g/l,ph为11.5,电镀液的温度为40℃,电流密度为0.9a/dm2;
68.步骤九:一次镀铬:电镀液中的铬离子的浓度为2.5g/l,ph为11.5,电镀液的温度为25℃,电流密度为1.5a/dm2;
69.步骤十:二次镀铬:电镀液中的铬离子的浓度为2.5g/l,ph为11.5,电镀液的温度为35℃,电流密度为1.5a/dm2;
70.步骤十一:涂硅烷:在铜箔最外层的镀锌镍铬防氧化层外喷涂硅烷偶联剂;
71.步骤十二:烘烤收卷。
72.所述后处理端中步骤十二得到的压延铜箔的厚度为0.10mm,所述压延铜箔的表面粗糙度rz值为0.05μm
73.实施例2:
74.一种0.1毫米超幅宽压延铜箔的表面处理工艺包括前处理端和后处理端;
75.所述前处理端包括以下步骤:
76.步骤一:先将铜熔炼铸造成锭,再经铜块熔融、热轧开胚、双面铣、粗轧、第一次退火、第一次清洗切边、第一次精轧、第二次清洗、第二次退火、第二次精轧、第三次清洗、第三
次退火、收卷成品,得到0.10mm的双面光滑铜箔;所述前处理端中步骤一第一次退火的退火温度为500℃,升温时间为4~5h,保温时间为6h,第二次退火的退火温度为400℃,升温时间为5h,保温时间为6h,第三次退火温度为300℃,升温时间为5h,保温时间为6h。
77.所述前处理端中步骤一粗轧的轧制力为440nn,轧制速度为800m/min,铜箔的入侧厚度为0.1500mm,出侧厚度为0.0620mm,弯辊力为3mpa。所述前处理端中步骤一第一次精轧的轧制力为440nn,轧制速度为750m/min,铜箔的入侧厚度为0.0620mm,出侧厚度为0.0212mm,弯辊力为2mpa。所述前处理端中步骤一第二次精轧的轧制力为450nn,轧制速度为700m/min,铜箔入侧厚度为0.0212mm,出侧厚度为0.0091mm,弯辊力为1mpa。
78.所述后处理端包括以下步骤:
79.步骤一:酸洗:铜箔用浓度≤20%的稀硫酸酸洗,酸洗温度为40℃,酸洗液中h2so4的浓度为160g/l;
80.步骤二:一次粗化:铜箔送入粗化槽进行一次粗化处理,粗化槽中盛装cuso4溶液,其中cu
2+
质量浓度为50g/l,聚乙烯亚胺质量浓度为35g/l,h2so4质量浓度为135g/l,温度为45℃,电流密度为60a/dm2,处理时间为5s;用聚乙烯亚胺做添加剂,在铜箔的生产过程中会随着电解液的电镀产生亮斑,提高铜箔的抗拉强度;
81.步骤三:一次固化:进行固化处理,固化所用的电镀液中cu
2+
质量浓度为40g/l,h2so4质量浓度为101g/l,温度为45℃,电流密度为50a/dm2,处理时间为5s;
82.步骤四:二次粗化:铜箔送入粗化槽进行二次粗化处理,粗化槽中盛装cuso4溶液,其中cu
2+
质量浓度为50g/l,六偏磷酸钠质量浓度为70g/l,h2so4质量浓度为101g/l,温度为35℃,电流密度为70a/dm2,处理时间为5s;六偏磷酸钠配合有效提高所得铜箔在粗化和固化前的均匀稳定性,同时在成膜时,六偏磷酸钠的遮盖性好,一方面混合物体系稳定,另一方面后期烘烤过程中能提高铜箔的抗剥离强度;
83.步骤五:二次固化:进行固化处理,固化所用的电镀液中cu
2+
质量浓度为50g/l,h2so4质量浓度为101g/l,温度为45℃,电流密度为50a/dm2,处理时间为5s;
84.步骤六:三次粗化:铜箔送入粗化槽进行二次粗化处理,粗化槽中盛装cuso4溶液,其中cu
2+
质量浓度为40g/l,2
‑
巯基吡啶质量浓度为80g/l,h2so4质量浓度为101g/l,温度为35℃,电流密度为55a/dm2,处理时间为5s;2
‑
巯基吡啶的亮度偏低,粗度太高,也有提升抗拉的效果;
85.步骤七:三次固化:进行固化处理,固化所用的电镀液中cu2+质量浓度为40g/l,h2so4质量浓度为135g/l,温度为45℃,电流密度为50a/dm2,处理时间为5s;
86.步骤八:镀镍:电镀液中的镍离子的浓度为3.5g/l,ph为11.5,电镀液的温度为35℃,电流密度为1.5a/dm2;
87.步骤九:镀锌:电镀液中的锌离子的浓度为5.0g/l,ph为10,电镀液的温度为40℃,电流密度为0.5a/dm2;
88.步骤九:一次镀铬:电镀液中的铬离子的浓度为1.5g/l,ph为11.5,电镀液的温度为20℃,电流密度为0.8a/dm2;
89.步骤十:二次镀铬:电镀液中的铬离子的浓度为1.5g/l,ph为10,电镀液的温度为30℃,电流密度为0.8a/dm2;
90.步骤十一:涂硅烷:在铜箔最外层的镀锌镍铬防氧化层外喷涂硅烷偶联剂;
91.步骤十二:烘烤收卷。
92.所述后处理端中步骤十二得到的压延铜箔的厚度为0.05mm,所述压延铜箔的表面粗糙度rz值为0.3μm
93.实施例3:
94.与实施例2相比,少了后处理端的步骤二和步骤三。
95.实施例4:
96.与实施例2相比,少了后处理端的步骤三和步骤四。
97.实施例5:
98.与实施例2相比,少了后处理端的步骤五和步骤六。
99.实施例6:
100.与实施例2相比,少了后处理端的步骤十。
101.对实施例1
‑
6进行实验:
102.(1)抗剥离强度测定:
103.以实施例1
‑
6制备得到的压延铜箔通过层压机与树脂基板压合制成覆铜板,然后通过拉力试验机测试实施例和对比例中压延铜箔与树脂基板之间的抗剥离强度(n/mm),记录最小负荷(lm,n)值和被测试样条宽度(ws,mm),每个实验组测量10次重复,取平均最小负荷(lm,n)值和平均被测试样条宽度(ws,mm)作为最终的结果。
104.表1
[0105][0106]
从表1可以看出,实施例1
‑
7中的压延铜箔的抗剥离强度(n/mm2)为1.12(n/mm2)以上,实施例4的效果要低于实施例3和实施例5。采用本发明所得到的压延铜箔具有更好的抗剥离强度,与基板之间的结合性更好。
[0107]
(2)耐热性能测试:
[0108]
实施例1
‑
6制备得到的压延铜箔分别置于150℃、200℃以及250℃的溶液中浸泡30min,取出后观察试样有没有发现起泡现象。
[0109]
通过耐热性能测试实验发现,实施例1
‑
6制备得到的压延铜箔在150℃、200℃的环境下浸泡30min后均无异象;但在250℃的环境下浸泡1h后,发生起泡现象,采用本发明所得到的压延铜箔具有较好的耐热性能。
[0110]
(3)杂项金属含量检测:
[0111]
实施例1
‑
6制备得到的压延铜箔,进行表面的金属含量检测得到:
[0112]
实施例1的压延铜箔镍含量8.2mg/m2、锌含量5.1mg/m2、铬含量10.1mg/m2。
[0113]
实施例2的压延铜箔镍含量7.3mg/m2、锌含量6.2.mg/m2、铬含量9.7mg/m2。
[0114]
实施例3的压延铜箔镍含量7.9.mg/m2、锌含量5.2mg/m2、铬含量9.9mg/m2。
[0115]
实施例4的压延铜箔镍含量8.1mg/m2、锌含量5.8mg/m2、铬含量10.3mg/m2。
[0116]
实施例5的压延铜箔镍含量8.2mg/m2、锌含量6.1mg/m2、铬含量10.2mg/m2。
[0117]
实施例6的压延铜箔镍含量7.5mg/m2、锌含量5.4mg/m2、铬含量10.8mg/m2。
[0118]
(4)高温抗拉强度测试
[0119]
实施例1
‑
6制备得到的压延铜箔通过高温抗拉强度(120℃)性能测试实验发现,实施例1的压延铜箔的高温抗拉强度220n/mm2。实施例2的压延铜箔的高温抗拉强度240n/mm2。实施例3的压延铜箔的高温抗拉强度212n/mm2。实施例4的压延铜箔的高温抗拉强度2390n/mm2。实施例5的压延铜箔的高温抗拉强度208n/mm2。实施例6的压延铜箔的高温抗拉强度235n/mm2。实施例4的效果要高于实施例3和实施例5。采用本发明所得到的压延铜箔具有较好的抗拉强度。
[0120]
以上结合附图对本发明的实施方式作了详细说明,但本发明不限于所描述的实施方式。对于本领域的技术人员而言,在不脱离本发明原理和精神的情况下,对这些实施方式进行多种变化、修改、替换和变型,仍落入本发明的保护范围内。