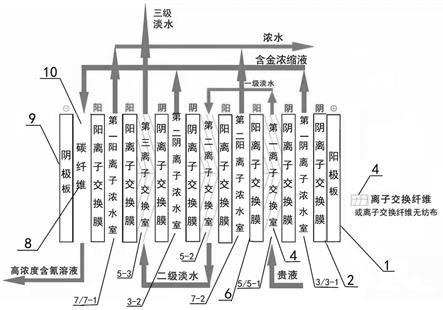
1.本发明涉及提纯黄金技术领域,具体是一种基于电去离子电沉积设备从黄金贵液中提纯黄金的方法。
背景技术:2.贵重金属提取或回收工艺多采用化学沉淀、渗透浸化、活性炭吸附、树脂吸附、锌粉置换、电解等方法,工艺复杂、使用大量酸和碱、产生大量的废水、废气、废渣、环保压力大、生产成本高。
3.目前较为普遍的黄金贵液处理工艺,主要包括化学氧化法、电解法、乳状液膜法和酸化法等方法,通过这些方法来破坏氰化物并使金离子沉淀,使得氰化废水达到排放标准。但是,这些方法普遍存在流程较长、设备酸蚀严重、运行和维护成本高,提纯后黄金含量不高等缺陷。
技术实现要素:4.本发明针对现有技术的不足,开发了一种基于电去离子电沉积设备从黄金贵液中提纯黄金的方法,通过对电去离子设备进行技术改造,将其与离子交换纤维吸附技术进行集成,用来提纯黄金,简化和缩短了黄金提取和回收工艺,达到节能减耗减排,实现清洁生产。
5.实现本发明目的的技术方案是:基于电去离子电沉积设备从黄金贵液中提纯黄金的方法,包括如下步骤:(1)设置电去离子电沉积设备,该设备包括至少二级系统,二级系统由阳极板、两组阴离子交换膜、多个离子交换室、两组阳离子交换膜、离子交换纤维或离子交换纤维无纺布、碳纤维、阴极板和阴极室组成,;所述阳极板的内侧靠设有阴离子交换膜,两组阴离子交换膜与两组阳离子交换膜交替设置在阳极板和阴极板之间,阴离子交换膜之间为阴离子浓水室,阳离子交换膜之间为阳离子浓水室;在二级系统中有二个阴离子浓水室和二个阳离子浓水室,靠近阳极板的阴离子浓水室为第一阴离子浓水室,另一个为第二阴离子浓水室,如有多级系统依次排序;靠近阴极板的阳离子浓水室为第一阳离子浓水室,另一个为第二阳离子浓水室,如有多级系统依次排序;所述多个离子交换室设置在阳极板和阴极板之间,具体设在阳离子交换膜和阴离子交换膜之间,离子交换室内填充有离子交换纤维或离子交换纤维无纺布;在二级系统中设有三个离子交换室,靠近阳极板的离子交换室为第一离子交换室,其他依次为第二离子交接室和第三离子交换室;所述阴极室由阴极板和阳离子交换膜组成,阴极室内填充有碳纤维;(2)将黄金贵液从第一离子交换室底部送入离子交换室,在离子交换室内经离子
交换或吸附,得到一级淡水和浓缩液;一级淡水从设备顶部送到第二离子交换室内经离子交换,得到二级淡水;二级淡水从设备底部送到第三离子交换室内经离子交换,得到三级淡水;三级淡水从设备顶部排出,进行后处理用作工业用水;(3)黄金贵液从第一离子交换室底部送入离子交换室时,其中的阴离子通过第一组阴离子交换膜进入第一阴离子浓水室,得到含金浓缩液,该含金浓缩液从设备顶部送到阴极室内,通过填充在阴极室内的碳纤维和阴极板进行电沉积,得到高浓度含氰溶液;黄金贵液从第一离子交换室底部送入离子交换室时,其中的阳离子通过第二组阳离子交换膜进入第二阳离子浓水室,得到浓水,浓水通过设备顶部排出,进行后处理;(4) 送到第二离子交换室内的一级淡水,其中的阳离子通过第二组阳离子交换膜进入第二阳离子浓水室,得到浓水,浓水通过设备顶部排出,进行后处理;送到第二离子交换室内的一级淡水,其中的阴离子通过第二组阴离子交换膜进入第二阴离子浓水室,得到含金浓缩液,该含金浓缩液从设备顶部送到阴极室内,通过填充在阴极室内的碳纤维和阴极板进行电沉积,得到高浓度含氰溶液;(5) 送到第三离子交换室内的二级淡水,其中的阳离子通过第二组阳离子交换膜进入第二阳离子浓水室,得到浓水,浓水通过设备顶部排出,进行后处理;送到第三离子交换室内的二级淡水,其中的阴离子通过第二组阴离子交换膜进入第二阴离子浓水室,得到含金浓缩液,该含金浓缩液从设备顶部送到阴极室内,通过填充在阴极室内的碳纤维和阴极板进行电沉积,得到高浓度含氰溶液;设备有二级以上系统,按上述方法循环提纯黄金。
6.步骤(1)中,设备的工作电压为5
‑
30v,工作电流为2
‑
5a。
7.步骤(2)和(3)中,黄金贵液送入第一离子交换室的流速为40
‑
200ml/min。
8.步骤(4)和(5)中,淡水的流速为40ml/min,浓水的流速为100ml/min。
9.本发明基于电去离子电沉积设备,由离子交换纤维与电去离子技术相结合,通过离子交换纤维的离子交换作用和离子交换膜的选择性透过作用,在直流电场的作用下使离子定向迁移,通过对电去离子设备的技术改造,使金离子电解富集于电极板上,其它金属离子通过循环液不断浓缩。本发明方法,可根据金属离子的属性,装填不同种类的离子交换纤维选择性吸附金属离子,同时对离子交换纤维不断进行电再生,这样使得离子交换纤维可以连续使用,从而完成对金属离子持续、深度的提取与回收。
10.本发明设备占地面积小、离子交换纤维用量小;使用电流作用,清洁生产;不增加废酸废碱排放,减少环境污染。
11.本发明基于电去离子电沉积设备从黄金贵液中提纯黄金的方法,可连续对贵重金属进行提取与回收;克服现有电去离子技术浓度极化造成的不良影响及环境污染;能直接电解产出贵重金属,优化、缩短了生产工艺,并减少了生产流程。是一种连续的处理方法,能够实现氰根的快速富集,由于引入阴阳离子交换材料和碳纤维吸附材料,与普通电解法相比电流效率更高。
附图说明
12.图1为本发明电去离子电沉积设备的结构图及本发明方法的工作流程图。
13.图中,1.阳极板 2.阴离子交换膜 3.阴离子浓水室 3
‑
1.第一阴离子浓水室 3
‑
2.第二阴离子浓水室 4. 离子交换纤维或离子交换纤维无纺布 5.离子交换室 5
‑
1.第一离子交换室 5
‑
2.第二离子交换室 5
‑
3.第三离子交换室 6.阳离子交换膜 7.阳离子浓水室 7
‑
1.第一阳离子浓水室 7
‑
2.第二阳离子浓水室 8.碳纤维 9.阴极板 10.阴极室。
具体实施方式
14.下面结合实施例和附图对本发明内容作一步的详细说明,但不是对本发明的限定。
15.实施例1基于电去离子电沉积设备从黄金贵液中提纯黄金的方法,包括如下步骤:(1)如图1所示,设置电去离子电沉积设备,该设备包括至少二级系统,二级系统由阳极板1、两组阴离子交换膜2、多个离子交换室5、两组阳离子交换膜6、离子交换纤维或离子交换纤维无纺布4、碳纤维8、阴极板9和阴极室10组成;所述阳极板1的内侧靠设有阴离子交换膜2,两组阴离子交换膜2与两组阳离子交换膜6交替设置在阳极板1和阳极板9之间,阴离子交换膜2之间为阴离子浓水室3,阳离子交换膜之间为阳离子浓水室7;在二级系统中有二个阴离子浓水室3和二个阳离子浓水室7,靠近阳极板1的阴离子浓水室3为第一阴离子浓水室3
‑
1,另一个为第二阴离子浓水室3
‑
2,如有多级系统,以此类推串联;靠近阴极板9的阳离子浓水室7为第一阳离子浓水室7
‑
1,另一个为为第二阳离子浓水室7
‑
1,如有多级系统,以此类推串联;所述多个离子交换室4设置在阳极板1和阴极板9之间,具体设在阳离子交换膜6和阴离子交换膜2之间,离子交换室5内填充有离子交换纤维或离子交换纤维无纺布4;在二级系统中设有三个离子交换室5,靠近阳极板1的离子交换室为第一离子交换室5
‑
1,其他依次为第二离子交接室5
‑
2和第三离子交换室5
‑
3;所述阴极室10由阴极板9和阳离子交换膜6组成,阴极室10内填充有碳纤维8;(2)将黄金贵液从第一离子交换室5
‑
1底部送入离子交换室5,其在第一离子交换室5
‑
1内经离子交换或吸附,得到一级淡水和浓缩液;一级淡水从设备顶部送到第二离子交换室5
‑
2内经离子交换,得到二级淡水;二级淡水从设备底部送到第三离子交换室5
‑
3内经离子交换,得到三级淡水;三级淡水从设备顶部排出,进行后处理用作工业用水;(3)黄金贵液从第一离子交换室5
‑
1底部送入离子交换室5时,其中的阴离子通过第一组阴离子交换膜2进入第一阴离子浓水室3
‑
1,得到含金浓缩液,该含金浓缩液从设备顶部送到阴极室10内,通过填充在阴极室10内的碳纤维8和阴极板9进行电沉积,得到高浓度含氰溶液;黄金贵液从第一离子交换室5
‑
1底部送入离子交换室5时,其中的阳离子通过第二组阳离子交换膜6进入第二阳离子浓水室7
‑
1,得到浓水,浓水通过设备顶部排出,进行后处理;(4) 送到第二离子交换室5
‑
2内的一级淡水,其中的阳离子通过第二组阳离子交换膜6进入第二阳离子浓水室7
‑
2,得到浓水,浓水通过设备顶部排出,进行后处理;
送到第二离子交换室5
‑
2内的一级淡水,其中的阴离子通过第二组阴离子交换膜2进入第二阴离子浓水室3
‑
2,得到含金浓缩液,该含金浓缩液从设备顶部送到阴极室10内,通过填充在阴极室10内的碳纤维8和阴极板9进行电沉积,得到高浓度含氰溶液;(5) 送到第三离子交换室5
‑
3内的二级淡水,其中的阳离子通过第二组阳离子交换膜6进入第一阳离子浓水室7
‑
1,得到浓水,浓水通过设备顶部排出,进行后处理;送到第三离子交换室内5
‑
3的二级淡水,其中的阴离子通过第二组阴离子交换膜2进入第二阴离子浓水室3
‑
2,得到含金浓缩液,该含金浓缩液从设备顶部送到阴极室内,通过填充在阴极室10内的碳纤维8和阴极板9进行电沉积,得到高浓度含氰溶液;设备有二级以上系统,按上述方法循环提纯黄金。
16.本实施例以冶炼厂黄金贵液提取为例,设备的工作电压为12v,工作电流为3a。
17.黄金贵液总处理量为500l,黄金贵液送入第一离子交换室5
‑
1的流速为40ml/min,设备中离子交换纤维的装填量为43克。
18.淡水的流速为40ml/min,淡水中金浓度≤0.05mg/m3,浓水的流速为100ml/min。提纯后金泥中金含量≥100000g/t。