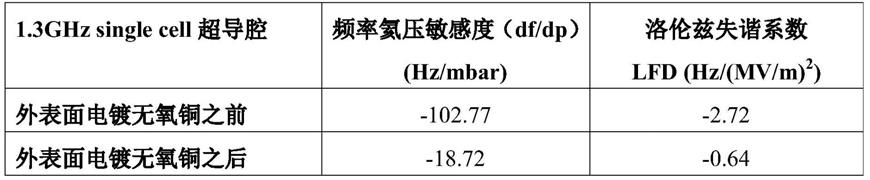
1.本发明涉及超导技术领域,具体涉及一种通过外表面电镀无氧铜研制铜基厚壁铌基超导腔的方法。
背景技术:2.当前的射频超导加速器采用的超导加速腔主要采用rrr(剩余电阻率比值,表征材料的纯度)>300的高纯铌板通过机械冲压、电子束焊接制造。但是受限于铌材4.2k或者2k运行温度下较低的导热能力,纯铌超导腔的壁厚一般不超过3
‑
4mm。一方面,3
‑
4mm壁厚的纯铌超导腔机械稳定性差,对颤噪、洛伦兹失谐、he压波动等外界干扰敏感,容易引起频率失谐;另一方面,纯铌超导腔3
‑
4mm的壁厚导热能力较差,不能及时把超导腔局部的发热传递到液氦,容易引起热不稳定现象。总之,从已有的运行经验以及纯铌超导腔的结构特点来看,纯铌超导腔很难满足强流超导加速器的连续稳定运行需求。
3.超导腔机械稳定性的提高,应在不影响热传导的基础上,通过增加腔体壁厚来实现。铜在4.2k或2k低温下的导热能力比rrr>300的铌材高约一个量级。因此,当前一个重要的突破方向是采用价格更低、热导更好的无氧铜为衬底,研制铜基厚壁纯铌超导腔。
4.当前,铜基厚壁纯铌超导腔的主要制造方法是在厚壁无氧铜腔内表面,通过溅射的方式生长一层2
‑
3μm的铌薄膜(简称铜铌溅射薄膜腔)。但是受制备过程的限制,溅射铌膜的晶粒尺寸小,伴随晶界弱连接、晶界弱耦合等限制因素,使得铜铌溅射薄膜腔的射频性能达不到纯铌超导腔的水平,无法广泛应用于当前的射频超导加速器大科学装置。因此,如何在保证超导腔射频性能的前提下,提高超导腔的机械稳定性与热稳定性,是解决当前和未来高能量、高流强射频超导加速器稳定运行问题的关键。
技术实现要素:5.针对上述问题,本发明的目的是提供一种通过外表面电镀无氧铜制备铜基厚壁纯铌超导腔的方法。该方法可以在保证铜基厚壁纯铌超导腔射频性能达到纯铌腔水平的基础上,显著提升超导腔的机械稳定性和热稳定性,且造价低,可批量生产,尤其适合用于需长时间稳定运行的射频超导加速器大科学装置。
6.为实现上述目的,本发明拟采取以下技术方案:
7.一种通过外表面电镀无氧铜制备铜基厚壁纯铌超导腔的方法,包括下述步骤:
8.1)采用rrr>300、厚度为1.5
‑
2.5mm的高纯铌材料,通过机械冲压、真空电子束焊接加工成薄壁纯铌超导腔;
9.2)对经步骤1)完成的薄壁纯铌超导腔进行真空检漏;
10.3)将经步骤2)真空检漏完成的纯铌超导腔进行超声清洗、晾干;
11.4)对步骤3)完成的纯铌超导腔内表面进行化学抛光处理,抛光厚度为80
‑
150μm(具体如100μm);
12.5)将经步骤4)完成的纯铌超导腔进行超声清洗、晾干;
13.6)将经步骤5)完成的纯铌超导腔放入真空炉内加热,进行高温除气处理;
14.7)将经步骤6)高温除气处理后的纯铌超导腔进行超声波清洗,晾干;
15.8)对步骤7)完成的纯铌超导腔内、外表面均进行化学抛光处理,内、外表面的抛光厚度均为10
‑
40μm(具体如20μm);
16.9)对经步骤8)完成的纯铌超导腔外表面沉积铜层;
17.10)将经步骤9)完成的纯铌超导腔进行超声波清洗,晾干;并用保鲜膜将所述纯铌超导腔所有法兰口以及全部外表面包裹住,洁净保存;
18.11)将步骤10)完成的纯铌超导腔所有法兰口均用氟胶圈进行严格密封,保证镀液无法进入纯铌腔内部而污染腔的内表面;
19.12)用设计好的电镀工装把纯铌超导腔装配在电镀槽上,小心揭开纯铌超导腔外表面的保鲜膜,把纯铌超导腔作为阴极,把环绕在纯铌腔周围的铜圆筒作为阳极,然后把电镀溶液注入电镀槽,直至电镀溶液液位面高于所述纯铌超导腔;所述铜圆筒由纯度大于等于99.95%的铜制成;
20.13)让纯铌超导腔在电机带动下,以每分钟10
‑
60转的速度沿轴向方向进行匀速旋转,然后打开电源使得阴阳极之间的电压为3
‑
10v,在纯铌腔外表面电镀无氧铜,至纯铌腔外表面电镀的无氧铜各处厚度均不低于6mm时,停止电镀;
21.14)将经步骤13)完成的电镀铜腔进行超声波清洗、晾干;
22.15)对经步骤14)完成的超导腔外表面进行机械打磨,去除电镀铜层上的尖锐凸起等缺陷,得到光滑平整的无氧铜外表面,即完成铜基厚壁纯铌超导腔的制备。
23.上述方法步骤2)中,所述真空检漏要求漏率低于1x10
‑
10
mbar
·
l/s。所述真空检漏过程中需采用慢速抽真空,真空泵需为无油泵组。
24.上述方法步骤4)和步骤8)中,所述化学抛光处理采用的酸液是由质量分数40%的氢氟酸、质量分数65%的硝酸和质量分数85%的磷酸依次按1:1:2体积比组成的混合酸液。
25.上述方法步骤6)中,所述加热的升温速率为1
‑
6℃/分钟(具体可为3℃/分钟);所述加热至600
‑
850℃(具体可为800℃)高温、真空小于1x10
‑3pa的条件下保温2
‑
10小时(具体可为3小时)。
26.上述方法步骤9)中,所述沉积铜层的方法为电火花沉积方法;所述铜层的厚度为20μm~1mm;具体可为20μm;所述铜层与所述纯铌超导腔外表面之间的结合力不低于50mpa;所述电火花沉积方法中,沉积电压为0~360v,具体可为80~240v;更具体可为180v;沉积频率为0~100000hz,具体可为10~1000hz;更具体可为200hz;沉积电容为30μf~50
×
30μf,具体可为30μf~14
×
30μf;所述电火花沉积方法中,所述纯铌超导腔以1~8000r/min的转速旋转;具体的,所述转速为2~50r/min;所述电火花沉积方法中所用纯铜电极棒长度为5~80mm,具体可为80mm;直径为2~20mm,具体可为10mm;
27.上述方法步骤10)中,所述清洁保存是在不低于万级的洁净环境内进行洁净保存。
28.上述方法步骤11)的操作应在洁净度不低于万级的洁净环境内全程穿戴防护服进行操作,避免对纯铌超导腔外表面的污染。
29.上述方法步骤12)中,所述电镀溶液可从很多试剂厂家购买,比如深圳沈工新科科技有限公司购买。
30.上述步骤12)中,所述阳极的面积应是阴极面积(即纯铌超导腔外表面需电镀无氧
铜层的部分表面积)的1.5
‑
2.5倍(如2倍);所述阳极应采用涤纶布套及阳极框袋装好防止阳极泥渣进入电镀溶液中,所述电镀溶液温度控制在20
‑
50℃(如40℃)。
31.上述步骤13)中,所述电镀采用间歇电镀的方式且伴随净化的空气搅拌,间歇电镀的周期一般为电镀2
‑
8s,停1
‑
2s,可以通过单相全波电源或者直流电源加装间歇设备实现,电流密度为1.5
‑
10a/dm2。
32.上述步骤13)中,所述电镀的过程需严格控制电镀溶液的温度和ph值,需每天用ph计检查电镀溶液ph值,ph值偏低时使用氢氧化钾溶液调整,ph值偏高时可用柠檬酸调整。
33.上述步骤13)中,所述纯铌超导腔外壁上电沉积的无氧铜是电镀液中的铜离子沉积的效果。
34.需每周化验一次电镀溶液并及时按照分析结果调整,每过~7天用浓度为30%的双氧水和活性炭过滤镀液,每天清洗过滤机,维护好镀槽及镀液,每天对铌腔外表面电镀铜层进行清理。
35.上述方法步骤14)之后步骤15)之前,还包括对超导腔进行钝化处理的步骤。具体钝化处理的方法如下:由重铬酸钾(30
‑
50g/l)、冰醋酸(用于调ph值,目标值3
‑
3.5)配置成的室温溶液中进行1
‑
3分钟的钝化处理,或者是放置于~15g/l的室温苯丙三氮唑溶液中浸泡2
‑
3分钟,此步是为了防止电镀铜层外表面发生氧化而影响其导热能力。
36.上述方法步骤3)、步骤5)、步骤6)和步骤10)中,所述超声清洗、晾干的具体方法如下:将所述纯铌超导腔放置于超声波清洗池内,且加入超声清洗液,用超纯水超声清洗30
‑
60分钟,水温50
‑
60℃(优选55℃),超声功率密度为25
‑
35w/gal;然后用超纯水将纯铌超导加速腔内外表面均冲洗干净,再将纯铌超导加速腔晾干;所述超声清洗液一般为micro
‑
90或者citranox亦或liqui
‑
nox,用量为每升超纯水加入10
‑
20ml超声清洗液;所述超声波清洗在不低于万级的洁净环境中进行。
37.上述方法步骤14)中,所述超声清洗、晾干的具体方法如下:将所述电镀铜腔放置于超声波清洗池内,且加入超声清洗液,用超纯水超声清洗不低于40分钟,水温50
‑
60℃(优选55℃),超声功率密度为25
‑
35w/gal;然后用超纯水将电镀铜腔外表面冲洗干净、晾干;所述超声清洗液一般为micro
‑
90或者citranox亦或liqui
‑
nox,用量为每升超纯水加入10
‑
20ml超声清洗液;所述超声波清洗在不低于万级的洁净环境中进行。此步是为了去除残留在电镀无氧铜层上的电镀溶液残留。
38.本发明中rrr值表示剩余电阻率比值,是指高纯铌材300k环境下电阻率与4k环境下电阻率比值。
39.与现有技术相比,本发明的具有以下优点:通过本发明方法研制的铜基厚壁超导腔机械稳定好,热稳定好,为超导加速器的连续稳定运行提供前提条件。且本发明方法可批量生产铜基厚壁超导腔。
附图说明
40.图1为本发明电镀过程结构示意图;
41.图2为本发明方法流程图;
42.图3为实施例1中1.3ghz single cell纯铌超导腔外表面电镀无氧铜后束管位置的温度探头同步响应赤道处的温升;
43.图4为实施例1中电镀无氧铜后1.3ghz single cell纯铌超导腔2k低温下的垂直测试性能。
具体实施方式
44.下面结合实施例对本发明的具体实施方式作进一步描述,以下实施例仅用于更加清楚地说明本发明的技术方案,而不能以此来限制本发明的保护范围。
45.下述实施例中使用的纯铌超导加速腔可按照下述文献中的方法进行制备:the international linear collider technical design report 2013,volume 3.i:accelerator r&d。
46.本发明的流程如图2所示,下面结合图2对这种通过外表面电镀无氧铜研制铜基厚壁超导腔的方法做详细介绍。
47.下述实施例中使用的rrr>300、厚度为1.5
‑
2.5mm的高纯铌材料购自宁夏东方超导科技有限公司。
48.下述实施例中使用的电镀液购自深圳沈工新科科技有限公司。
49.实施例1、通过外表面电镀无氧铜制备铜基厚壁纯铌超导腔
50.一、薄壁纯铌超导腔的机械冲压、电子束后焊接加工,主要是得到用于外表面电镀铜的衬底铌腔,主要流程包括:
51.①
采用rrr>300、厚度为1.5
‑
2.5mm的高纯铌材料,通过冲压模具制作出所需形状的薄壁超导腔零件与束管,采用1.5
‑
2.5mm的高纯铌板是为了通过减少超导腔的壁厚来降低铌材的热阻,采用铌钛合金材料,用车床加工出与束管对接的法兰;
52.②
用超声清洗装置,对经步骤
①
完成的零件进行超声清洗,清洗时间不少于40分钟,目的是对超导腔零件进行除油处理。
53.③
用由氢氟酸(质量分数40%)、硝酸(质量分数65%)、磷酸(质量分数85%)按1:1:2体积比组成的混合酸液对经步骤
②
完成的纯铌零件进行化学清洗,化学清洗的酸温控制在20℃以内,清洗时间10
‑
40分钟,目的是进一步去除焊缝附近的可能污染,保证焊接质量。
54.④
用电阻率不小于18mω
·
cm的超纯水清洗经步骤
③
完成的零件,并在优于1000级的洁净间中晾干。
55.⑤
利用真空电子束焊机对经步骤
④
完成的零件进行电子束焊接,得到薄壁纯铌超导腔,真空电子束焊机的工作电压为60kv,电子束流强为5
‑
15ma。
56.二、纯铌超导加速腔电镀前的后处理,主要是外表面电镀无氧铜前的准备条件,主要流程包括:
57.①
对上述制备的薄壁纯铌超导腔进行真空检漏,真空泵需为无油泵组,漏率需要低于1x10
‑
10
mbar
·
l/s。
58.②
将经步骤
①
检漏完成的纯铌超导腔放置于超声波清洗池(不低于万级的洁净环境)内,且加入超声清洗液,用超纯水超声清洗30
‑
60分钟,水温55℃左右,然后用超纯水将纯铌超导加速腔内外表面均冲洗干净,然后将纯铌超导加速腔晾干。
59.③
用由氢氟酸(质量分数40%)、硝酸(质量分数65%)、磷酸(质量分数85%)按1:1:2体积比组成的混合酸液对经步骤
②
完成的纯铌超导腔内表面进行化学抛光处理,抛光
厚度约为100μm。
60.④
对经步骤
③
完成的纯铌超导腔进行超声波清洗,清洗时间30
‑
60分钟,用超纯水将纯铌超导加速腔内外表面均冲洗干净,然后将纯铌超导加速腔晾干。
61.⑤
将经步骤
④
完成的纯铌超导腔放入真空炉内开始加热,升温速率约为3℃/分钟,在800℃高温、真空好于1x10
‑3pa的条件下保温3个小时,进行高温除气处理。
62.⑥
对经步骤
⑤
完成的纯铌超导腔进行超声波清洗,清洗时间30
‑
60分钟,用超纯水将纯铌超导加速腔内外表面均冲洗干净,然后将纯铌超导加速腔晾干。
63.⑦
用由氢氟酸(质量分数40%)、硝酸(质量分数65%)、磷酸(质量分数85%)按1:1:2体积比组成的混合酸液对经步骤
⑥
完成的纯铌超导腔内、外表面均进行化学抛光处理,内、外表面的抛光厚度均约为20μm;本步操作是为了使纯铌超导腔外表面各处具有相同的表面特性,方便后续结合力良好铜层的沉积。
64.⑧
将经步骤
⑦
完成的纯铌超导腔放置于超声波清洗池(不低于万级的洁净环境)内,用超纯水超声清洗30
‑
60分钟,水温55℃左右,然后用超纯水将纯铌超导加速腔内外表面均冲洗干净,然后将纯铌超导加速腔晾干。
65.⑨
纯铌超导腔外表面结合力良好铜层的制备;由于铜铌不互溶,因此如果直接在纯铌超导腔外表面电镀无氧铜,电镀铜层和腔外表面之间的结合力无法满足实用需求;因此本步处理主要是通过在纯铌超导腔外表面先沉积一层结合力良好的铜层,再在铜层外表面电镀无氧铜,解决电镀铜层和纯铌超导腔外表面之间结合力不足的问题;具体制备步骤如下:
66.1)采用氟胶圈把步骤
⑧
完成的纯铌超导腔的所有出口均严格密封;此步操作是为了确保后续对纯铌超导腔外表面沉积铜层过程中,保护纯铌超导腔内表面不被污染;
67.2)在纯铌超导腔外表面沉积结合力良好的铜层;铜层的厚度可为20μm~1mm;本实施例具体的厚度为20μm;铜层与纯铌超导腔外表面之间的结合力不低于50mpa;铜层的沉积采用电火花沉积方法。
68.本实施例中,该步骤的具体操作和条件如下:
69.①
将纯铌超导腔加持在工装上,腔体在工装控制下按照设定速度旋转,转速为50r/min;
70.②
电火花沉积电源为商用电源,包括电源本体和焊枪,焊枪前段夹持电极并能输出氩气保护气体;
71.③
准备好纯铜电极棒(纯度≥99.99%),长度80mm,直径电极为正极,腔体接负极;
72.④
将焊枪夹持在夹持结构上,并将夹持结构固定在驱动系统上,实现焊枪电极围绕纯铌超导腔外表面的旋转运动及周期性放电,最终实现电极材料在纯铌超导腔外表面的沉积;
73.⑤
上述沉积电压为180v;上述沉积频率为200hz;上述沉积电容为210μf。
74.⑩
用保鲜膜将经步骤
⑨
完成的纯铌超导腔所有法兰口以及整个外表面全部包裹住,并放于不低于万级的洁净环境内进行洁净保存。
75.三、纯铌超导腔外表面电镀无氧铜阶段,在此阶段将在纯铌超导腔外表面生成厚壁无氧铜层,主要流程包括:
76.①
将纯铌超导腔所有法兰口均用氟胶圈进行严格密封,保证电镀溶液无法进入纯铌腔内部而污染腔的内表面,此步操作应在洁净度不低于万级的洁净环境内全程穿戴防护服进行操作,避免对纯铌超导腔外表面的污染。
77.②
小心拆除纯铌超导腔外表面的保鲜膜,用设计好的电镀工装把纯铌超导腔装配在镀槽上作为阴极,把环绕在纯铌腔周围的电解铜或无氧铜圆筒作为阳极,阳极的面积应是阴极面积(即超导腔外表面需电镀无氧铜层的部分表面积)的约2倍,阳极应采用涤纶布套及阳极框袋装好防止阳极泥渣进入镀液中,镀液温度控制在40℃左右。
78.③
在电机带动下,使纯铌超导腔以每分钟30转的速度沿轴向方向进行匀速旋转,然后打开电源使得阴阳极之间的电压为5v,开始在纯铌腔外表面电镀无氧铜,电镀采用间歇电镀的方式且伴随净化的空气搅拌,间歇电镀的周期一般为电镀6s,停1s,可以通过单相全波电源或者直流电源加装间歇设备实现,电流密度为4.5a/dm2。
79.④
电镀过程需严格控制镀液的温度和ph值,需每天用ph计检查镀液ph值,ph值偏低时使用氢氧化钾溶液调整,ph值偏高时可用柠檬酸调整。
80.⑤
需每周化验一次镀液并及时按照分析结果调整,每过~7天用浓度为30%的双氧水和活性炭过滤镀液,每天清洗过滤机,维护好镀槽及镀液,每天对铌腔外表面电镀铜层进行清理。
81.四、纯铌超导腔外表面电镀无氧铜后的处理,此阶段主要目的是去除电镀铜层外表面的残留镀液,防止电镀铜层快速氧化,以及得到光滑、平整的铜基厚壁纯铌超导腔,主要流程包括:
82.①
将完成无氧铜电镀的超导腔放置于超声波清洗池(不低于万级的洁净环境)内,加超声清洗剂进行清洗,水温55℃左右,清洗时间不低于40分钟,用超纯水将电镀超导腔内外表面均冲洗干净,然后将电镀超导腔晾干,此步是为了去除残留在电镀无氧铜层上的电镀溶液残留。
83.②
将经步骤
①
完成的电镀超导腔放置于由重铬酸钾(30
‑
50g/l)、冰醋酸(用于调ph值,目标值3
‑
3.5)配置成的室温溶液中进行1
‑
3分钟的钝化处理,或者是放置于~15g/l的室温苯丙三氮唑溶液中浸泡2
‑
3分钟,此步是为了防止电镀铜层外表面发生氧化而影响其导热能力。
84.③
将经步骤
②
完成的电镀超导腔放置于超声波清洗池(不低于万级的洁净环境)内,加超声清洗剂进行清洗,水温55℃左右,清洗时间不低于40分钟,用超纯水将电镀超导腔内外表面均冲洗干净,然后用高纯氮气将将电镀超导腔内外表面快速吹干。
85.④
对经步骤
③
完成的超导腔电镀铜层外表面进行机械打磨,去除电镀铜层上的尖锐凸起等缺陷,得到光滑平整的外表面。
86.⑤
通过外表面电镀无氧铜方法研制的铜基厚壁纯铌超导腔完成。
87.对上述方法制备的铜基厚壁纯铌超导腔的性能进行测试:
88.1、电镀前后超导腔的性能;图3为1.3ghz single cell纯铌超导腔外表面电镀无氧铜后束管位置的温度探头对赤道温升的响应图,由图3可知赤道处发热产生的温度升高,被束管位置的温度探头很快相应,说明赤道处产生的热量很快传递到束管位置,表明了电镀无氧铜后超导腔良好的热稳定性。图4为电镀无氧铜后1.3ghz single cell超导腔2k低温下的垂直测试性能,由图4可知电镀无氧铜后的超导腔,2k下的无载品质因子达到
1.3e10,峰值电场强度达到44mv/m,表明了电镀无氧铜后的超导腔依然有良好的射频性能。
89.2、电镀前后超导腔的频率随外部压力敏感性对比测试,见表1;
90.3、电镀前后超导腔的洛伦兹失谐系数对比测试,见表1。
91.表1 1.3ghz single cell纯铌超导腔外表面电镀无氧铜前后的机械稳定性测量对比
[0092][0093]
上述洛伦兹失谐系数的定义为:由于腔内磁场与腔壁上的电流相互作用产生的力,作用在腔壁上,使腔壁产生形变,从而使超导腔发生频率偏移。具体的测量方法为:在低温下保持超导腔周围液氦的氦压不变,增大超导腔内的场强,则超导腔的频率变化随超导腔内部场强的比值即为洛伦兹失谐系数。
[0094]
上述液氦氦压波动对超导腔频率影响df/dp的定义为:由于超导腔周围液氦压力的变化施加到超导腔外壁导致其微变形,微变形会导致超导腔的频率随之变化,超导腔频率变化量与液氦压力变化量之间的比值为df/dp。上述超导腔在4.2k下的q值表示超导腔的内表面在一定的加速梯度下对应的腔壁损耗大小,其定义为q=ωu/p,其中ω为超导腔的谐振圆频率,u为超导腔内的储能,p为超导腔内表面的功率损耗,通过测量超导腔储能随时间的衰减情况就可以得到衰减时间,进而得到超导腔在不同的加速梯度下的q值。
[0095]
本发明制备的铜基厚壁纯铌超导腔在保证铜基厚壁纯铌超导腔射频性能达到纯铌腔水平的基础上,显著提升了超导腔的机械稳定性和热稳定性。
[0096]
以上所述仅为本发明的优选实施例而已,并不用于限制本发明,尽管参照前述实施例对本发明进行了详细的说明,对于本领域的技术人员来说,其依然可以对前述各实施例所记载的技术方案进行修改,或者对其中部分技术特征进行等同替换。凡在本发明的精神和原则之内,所作的任何修改、等同替换、改进等,均应包含在本发明的保护范围之内。