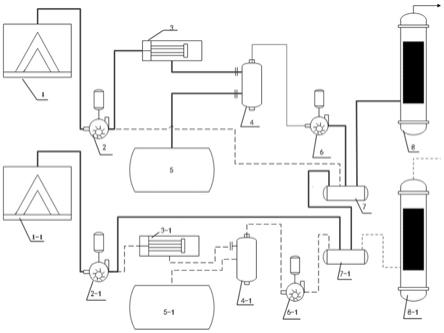
1.本发明涉及有色金属冶金领域,具体是一种用于海绵钛全流程生产中的尾氯处理装置及处理方法。
背景技术:2.目前世界上炼镁有两种方法,电解法和硅热还原法。电解法是将含mgcl2的原料提纯成无水氯化镁或将含mg原料转化成无水氯化镁,在熔融状态下电解出金属镁。电解法是镁生产的主要方法,国外80%的镁是电解法生产的,电解镁技术具有能耗低(较传统工艺降低40%)、副产氯气浓度高(96%以上,可液化)等优势。
3.在海绵钛全流程生产工艺中,金属镁是海绵钛生产的还原剂,钛还原后产生的氯化镁,氯化镁在电解槽内电离后成为液镁和氯气;同时电解出的氯气被送往氯化工序氯化高钛渣生产四氯化钛,如此反复循环,由此循环不断,形成了全流程的生产工艺。镁生产部分包括镁电解、氯压机室、氯气应急处理等部分组成。
4.氯气在常温常压下为黄绿色气体,比重是空气的2.5倍;标准气压、温度20℃时,氯气的密度是3.214
㎏
/m
³
,有剧烈窒息性刺激嗅味、剧毒。车间空气中最高允许浓度为2
㎎
/m3,居住区大气中最高允许浓度一次性为0.1
㎎
/m3,日均为0.03
㎎
/m3。氯气既是海绵钛全流程生产工艺的重要原料之一,也由其剧毒特性,在生产过程中不能向空气中有丝毫泄漏。
5.在电解系统正常运行时,电解氯气经加压后送入氯化炉参与四氯化钛的生产。当氯化炉停工检修或因故障停运时,电解系统产生的氯气就需要经过氯气液化装置的液化,产生的液氯进入储存容器储存,液化中的不凝气体称之为尾氯,尾氯中含有一定量的氯气,不能直接排放,需要投入尾氯处理设备,利用碱液吸收制备次氯酸钠,这样就需要消耗大量的烧碱,也造成尾氯中氯气的浪费,增加企业的处理费用。
技术实现要素:6.本发明的目的是提供一种用于海绵钛全流程生产中的尾氯处理装置及处理方法,该装置包括两个结构相同的处理单元,在其中一个处理单元的氯化炉停运时,可以将尾氯引入另一处理单元,避免氯气或尾氯的泄漏,保障海绵钛全流程生产工艺间物料平衡、降低生产成本、实现企业的生态环境价值。
7.为了实现上述目的,本发明所采用的技术方案是:一种用于海绵钛全流程生产中的尾氯处理装置,包括结构相同的第一处理单元和第二处理单元,每一处理单元包括一个电解系统、一个氯化炉、一条氯气管线和一条尾氯处理管线,所述氯气管线上设有与电解系统连接的氯气压缩机以及与氯化炉连接的分配器,所述尾氯处理管线的入口与氯气压缩机的出口连接,尾氯处理管线的出口与所述分配器连接,尾氯处理管线上设有氯气液化系统,氯气液化系统用于将氯气压缩机加压后的氯气进行液化和气液分离,并使得分离后的液氯进入对应的存储容器、分离后的尾氯进入所在处理单元中的分配器;两个处理单元中的两个分配器之间通过管线双向连通。
8.所述氯气液化装置包括沿生产工艺路线依次设置的液化装置、气液分离装置和抽负增压装置,气液分离装置的进口与液化装置的出口连接,气液分离装置的液体出口和储存容器连接,气液分离装置顶部的气体出口经抽负增压装置与分配器的入口连接。
9.第一处理单元包括第一电解系统、氯气管线、尾氯处理管线和第一氯化炉,氯气管线的一端和尾氯处理管线的一端通过三通阀门与第一氯气压缩机的出口连通,第一氯气压缩机的进口与第一电解系统的氯气出口连通,氯气管线的另一端与第一分配器的氯气入口连接,第一分配器的出口与第一氯化炉通过管线连接;尾氯处理管线上沿工艺路线依次设置第一液化装置、第一气液分离装置和第一抽负增压装置,第一液化装置的出口与第一气液分离装置的进口连接,第一气液分离装置的排液口与用于存储液氯的第一存储容器连接,第一气液分离装置的排气口与第一抽负增压装置的进口连接,第一抽负增压装置的出口与第一分配器上的尾氯入口连接。
10.进一步的,第二处理单元包括第二电解系统、氯气管线、尾氯处理管线和第二氯化炉,氯气管线的一端和尾氯处理管线的一端通过三通阀门与第二氯气压缩机的出口连通,第二氯气压缩机的进口与第二电解系统的氯气出口连通,氯气管线的另一端与第二分配器的氯气入口连接,第二分配器的出口与第二氯化炉通过管线连接;尾氯处理管线上沿工艺路线依次设置第二液化装置、第二气液分离装置和第二抽负增压装置,第二液化装置的出口与第二气液分离装置的进口连接,第二气液分离装置的排液口与用于存储液氯的第二存储容器连接,第二气液分离装置的排气口与第二抽负增压装置的进口连接,第二抽负增压装置的出口与第二分配器上的尾氯入口连接。
11.更进一步的,第一分配器上设有尾氯进出口,第二分配器上也设有尾氯进出口,两个分配器的两个尾氯进出口通过回收管线连接。
12.本发明还包括利用上述尾氯处理装置的尾氯处理方法,该方法主要用于应对两个处理单元中的任一氯化炉的停运,具体步骤为:首先关闭停运氯化炉和所连接分配器之间的阀门,然后启动停运氯化炉对应的氯气液化装置,并打开两个分配器之间管线上的阀门,使得氯气液化装置中分离出的液氯进入储存容器、分离出的尾氯经抽负增压装置进入本处理单元的分配器,接着再进入另一处理单元的分配器,最后与该分配器中的氯气混合后进入对应的氯化炉。
13.本发明的有益效果是:本发明所提供的处理装置和处理方法可以将两套电解系统和两个氯化炉组成两个处理单元,正常情况下,电解产生的氯气,可以通过处理单元内的管线直接进入对应的氯化炉,参与四氯化钛的生产;在任一处理单元中的氯化炉出现故障或停运检修时,可以通过该处理单元的氯气液化装置将电解产生的氯气液化后再气液分离,分离的液氯可以存储起来,分离出的尾氯则可以通过分配器进入另一单元的分配器,进而进入另一个氯化炉,参与四氯化钛的生产,这样就可以消耗掉停运氯化炉对应的电解系统的电解氯气,从而达到海绵钛全流程生产工艺间物料平衡、降低生产成本目的,并且完全避免烧碱和氯气外溢污染环境的可能。
14.本发明在气液分离装置后增设抽负增压装置,可以使得氯气液化运行时的泵后压力由0.28
‑
0.3mpa降低至0.23
‑
0.25mpa,氯气压缩机使用寿命延长了15%,备件消耗成本得到控制。
15.本发明在本公司投用后,企业外购液碱、外购液氯、次氯酸钠处理的费用共计节约
470万元,而且镁电解系统的运行稳定性得到较大提升,企业达到了物料平衡、降低生产成本目的。
附图说明
16.图1为本发明的结构示意图;图中标记:1、第一电解系统,2、第一氯气压缩机,3、第一液化装置,4、第一气液分离装置,5、第一储存容器,6、第一抽负增压装置,7、第一分配器,8、第一氯化炉;1
‑
1、第二电解系统,2
‑
1、第二氯气压缩机,3
‑
1、第二液化装置,4
‑
1、第二气液分离装置,5
‑
1、第二储存容器,6
‑
1、第二抽负增压装置,7
‑
1、第二分配器,8
‑
1、第二氯化炉。
具体实施方式
17.下面结合附图和实施例对本发明作进一步的详细说明,但并不作为对发明做任何限制的依据。
18.参照附图所示,一种用于海绵钛全流程生产中的尾氯处理装置,包括第一处理单元和第二处理单元。
19.第一处理单元包括第一电解系统、氯气管线、尾氯处理管线和第一氯化炉,氯气管线的一端和尾氯处理管线的一端通过三通阀门与第一氯气压缩机的出口连通,由三通阀门控制加压后的氯气进入氯气管线或者进入尾氯处理管线,第一氯气压缩机的进口与第一电解系统的氯气出口连通,氯气管线的另一端与第一分配器的氯气入口连接,第一分配器的出口与第一氯化炉通过管线连接;尾氯处理管线上沿工艺路线依次设置第一液化装置、第一气液分离装置和第一抽负增压装置,第一液化装置的出口与第一气液分离装置的进口连接,第一气液分离装置的排液口与用于存储液氯的第一存储容器连接,第一气液分离装置的排气口与第一抽负增压装置的进口连接,第一抽负增压装置的出口与第一分配器上的尾氯入口连接。
20.第二处理单元包括第二电解系统、氯气管线、尾氯处理管线和第二氯化炉,氯气管线的一端和尾氯处理管线的一端通过三通阀门与第二氯气压缩机的出口连通,由三通阀门控制加压后的氯气进入氯气管线或者进入尾氯处理管线,第二氯气压缩机的进口与第二电解系统的氯气出口连通,氯气管线的另一端与第二分配器的氯气入口连接,第二分配器的出口与第二氯化炉通过管线连接;尾氯处理管线上沿工艺路线依次设置第二液化装置、第二气液分离装置和第二抽负增压装置,第二液化装置的出口与第二气液分离装置的进口连接,第二气液分离装置的排液口与用于存储液氯的二存储容器连接,第二气液分离装置的排气口与第二抽负增压装置的进口连接,第二抽负增压装置的出口与第二分配器上的尾氯入口连接。
21.第一分配器上设有尾氯进出口,第二分配器上也设有尾氯进出口,两个分配器的两个尾氯进出口通过回收管线连接,第一处理单元中的尾氯进入第一分配器后,经回收管线进入第二分配器,与其中的氯气混合进入第二氯化炉。同样的,第二处理单元中的尾氯进入第二分配器后,经回收管线进入第一分配器,与其中的氯气混合进入第一氯化炉。
22.在利用上述尾氯处理装置的过程中,如果其中第一氯化炉因故停止运行,或者需要停运检修,此时需要首先关闭第一氯化炉和第一分配器之间的阀门,然后启动氯气液化
系统,包括第一液化装置、第一气液分离装置、第一抽负增压装置,同时还需要通过三通阀门控制第一电解系统产生的氯气经第一氯气压缩机加压后进入第一液化装置,并打开两个分配器之间管线上的阀门;氯气进入第一液化装置液化后再通过第一气液分离装置的分离,分离出的液氯进入第一存储容器储存,分离的尾氯则经第一抽负增压装置进入第一分配器,接着再进入第二分配器,最后与第二分配器中的氯气混合后进入第二氯化炉。
23.如果停运的是第二氯化炉,则可以按照上述方法步骤,使得第二电解系统的氯气、尾氯得到妥善的处理,以避免泄漏。
24.需要说明的是,在图1中,同一处理单元中的虚线管线和实线管线不能同时投入使用,因此采用虚线、实线的形式加以区分。
25.此外,在利用上述尾氯处理装置的过程中,当氯化炉均正常运行时,通过第一处理单元的三通阀门控制第一电解系统产生的氯气经第一氯气压缩机的加压进入第一分配器后再进入第一氯化炉,同样的通过第二处理单元的三通阀门控制第二电解系统产生的氯气经第二氯气压缩机的加压进入第二分配器后再进入第二氯化炉。
26.本发明在某海绵钛生产企业进行了试验应用,与传统的尾氯处理工艺相比,充分显示了其优越性。
27.1、生产成本大大降低。减少外购烧碱成本减少364.956万元/年,减少外购液氯采购成本45.83万元/年,减少次氯酸钠处理成本45.83万元/年。
28.2、生产稳定性大大提高,镁锭采购成本得到降低。液镁外购采购成本1395.36万元/年。
29.3、氯气液化运行时的泵后压力由0.28
‑
0.3mpa降低至0.23
‑
0.25mpa,氯气压缩机使用寿命延长了15%,备件消耗成本得到有效控制。
30.以上实施例仅用以说明本发明的技术方案而非对其进行限制,所属领域的普通技术人员应当理解,参照上述实施例可以对本发明的具体实施方式进行修改或者等同替换,这些未脱离本发明精神和范围的任何修改或者等同替换均在申请待批的权利要求保护范围之内。