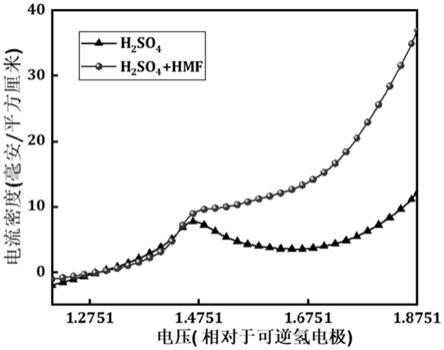
一种
γ
‑
mno2的制备方法及其应用
技术领域
1.本发明属于新材料技术领域,具体涉及一种γ
‑
mno2的制备方法及其应用。
背景技术:2.二氧化锰具有天然储量丰富、成本低廉和对环境友好等优点,并具有特定的化学/物理性质,因此已被广泛应用于催化领域。然而现有的二氧化锰电催化剂的活性较低,难以实现大规模的电催化生产。
3.为了提高二氧化锰的电催化活性,研究人员尝试改变二氧化锰比表面积、晶型、氧化态、形貌等,根据现有研究成果可知,γ相二氧化锰(γ
‑
mno2)的催化活性远高于普通mno2,因此,相较于其他晶型,γ
‑
mno2在电催化氧化生物质及电催化产氧等领域拥有更大的应用前景。
4.从制备方法上来看,γ
‑
mno2材料的制备主要有水热法、化学氧化法、电沉积法和热处理法。例如,hayashi等人通过水热合成的方法合成出了γ
‑
mno2,所得γ
‑
mno2对热催化5
‑
羟甲基糠醛氧化有很好的效果;li等人通过滴涂、空气氛围煅烧等步骤也合成出了γ
‑
mno2,所得γ
‑
mno2在低电位下电解水产氧有良好的促进效果;还有研究者通过在酸液中以clo4‑
氧化沉淀mn
2+
制备了γ
‑
mno2。
5.但是,国内外报道的γ
‑
mno2的制备方法均较为复杂,且所得γ
‑
mno2还具有分散性差、颗粒不均匀等缺点。
技术实现要素:6.本发明旨在至少解决上述现有技术中存在的技术问题之一。为此,本发明提出一种一种γ
‑
mno2的制备方法,由于各步骤的配合,能够通过简单的方法,获取分散性好、颗粒均匀,且催化活性优异的γ
‑
mno2。
7.本发明还提出一种上述γ
‑
mno2的制备方法制备的γ
‑
mno2。
8.本发明还提出一种包含上述γ
‑
mno2的催化电极。
9.本发明还提出一种上述γ
‑
mno2在电催化领域的应用。
10.根据本发明的一个方面,提出了一种γ
‑
mno2的制备方法,包括以下步骤:
11.s1.以酸性的锰盐水溶液为电解液,采用电沉积法,在导电基体上沉积;
12.s2.在200~400℃温度范围内,将步骤s1所得导电基体进行热处理;
13.s3.以步骤s2所得产物为工作电极,以酸性水溶液为电解液,进行计时电压法处理。
14.根据本发明的一种优选的实施方式,至少具有以下有益效果:
15.(1)本发明提供的制备方法条件温和、简单,采用先以硫酸锰溶液电沉积、后进行热处理及计时电压法后处理的办法制得γ
‑
mno2;且所用原料(包括辅料)价格低廉。
16.(2)本发明在电沉积法后增加了热处理以提升γ
‑
mno2的致密度,因此可避免所得γ
‑
mno2从导电基体上脱落、影响其催化活性;
17.本发明还采用了计时电压法处理,以使锰离子发生原位变化,进而形成在酸性条件下稳定的mn离子状态,最终可提升所得γ
‑
mno2的电化学活性。
18.(3)本发明提供的制备方法中,热处理的温度与所得γ
‑
mno2的晶型密切相关,若温度过低则不能促进γ相mno2的生成,若温度过高,则所得γ
‑
mno2会继续转化成其他晶型的二氧化锰。
19.(4)与常规制备方法相比,本发明采用电沉积法所得的γ
‑
mno2,颗粒更加细小而均匀。
20.在本发明的一些实施方式中,步骤s1中,所述酸性的ph为0.4~0.6。
21.在本发明的一些实施方式中,步骤s1中,所述酸性的调节剂为硫酸。
22.在本发明的一些实施方式中,步骤s1中,所述锰盐为硫酸锰。
23.在本发明的一些实施方式中,步骤s1中,所述锰盐水溶液中锰盐的浓度为0.4~0.6mol/l。
24.在本发明的一些优选的实施方式中,步骤s1中,所述锰盐的阴离子,与所述酸性的调节剂的阴离子相同;作用是阴离子不同带来的杂质干扰。
25.在本发明的一些优选的实施方式中,步骤s1中,所述电解液的体积约为30ml。
26.所述电解液的体积可根据所要形成的γ
‑
mno2的量进行调整,并不限定于30ml。
27.在本发明的一些实施方式中,步骤s1中,所述电沉积法的温度为50~70℃。
28.在本发明的一些优选的实施方式中,步骤s1中,所述电沉积法的温度约为60℃。
29.在本发明的一些实施方式中,步骤s1中,所述电沉积法的温度通过水浴法控制。
30.在本发明的一些实施方式中,步骤s1中,所述电沉积法的电流密度为4~6ma cm
‑2。
31.在本发明的一些优选的实施方式中,步骤s1中,所述电沉积法的电流密度约为5ma cm
‑2。
32.在本发明的一些实施方式中,步骤s1中,所述电沉积法的沉积时间为0.1~1h。
33.在本发明的一些实施方式中,步骤s1中,所述电沉积法的沉积时间约为1h。
34.在本发明的一些实施方式中,步骤s1中,所述电沉积法采用三电极体系。
35.在本发明的一些实施方式中,步骤s1中,所述电沉积的工作电极为所述导电基体。
36.在本发明的一些优选的实施方式中,步骤s1中,所述导电基体选自碳布。
37.在本发明的一些优选的实施方式中,步骤s1中,所述导电基体的面积为1
×
1cm2~1.5
×
1.5cm2。
38.所述面积均为表观面积,并未计算所述导电基体中孔径形成的内面积。
39.在本发明的一些实施方式中,步骤s1中,所述电沉积法的对电极为铂。
40.在本发明的一些实施方式中,步骤s1中,所述电沉积法的对电极为面积为1
×
1cm2~1.5
×
1.5cm2的铂片。在本发明的一些实施方式中,步骤s1中,所述电沉积法的参比电极为汞/硫酸汞。
41.步骤s1所得导电基体上沉积有含锰沉积物。
42.在本发明的一些优选的实施方式中,步骤s2中,所述热处理的温度约为200℃。
43.在本发明的一些实施方式中,步骤s2中,所述热处理的时间为3~5h。
44.在本发明的一些优选的实施方式中,步骤s2中,所述热处理的时间约为4h。
45.在本发明的一些实施方式中,步骤s2中,所述热处理的氛围为空气氛围。
46.在本发明的一些实施方式中,步骤s2中,所述热处理在加热台上进行。
47.步骤s2中,所述热处理使所述含锰沉积物更加致密,也促进了其晶型的转化。
48.在本发明的一些实施方式中,步骤s3中,所述酸性水溶液的溶质为硫酸。
49.在本发明的一些实施方式中,步骤s3中,所述酸性水溶液是浓度为0.4~0.6mol/l的硫酸水溶液。
50.在本发明的一些优选的实施方式中,步骤s3中,所述酸性水溶液是浓度约为0.5mol/l的硫酸水溶液。
51.在本发明的一些实施方式中,步骤s3中,所述计时电压法的电流密度为8~10ma cm
‑2。
52.在本发明的一些优选的实施方式中,步骤s3中,所述计时电压法的电流密度约为10ma cm
‑2。
53.在本发明的一些实施方式中,步骤s3中,所述计时电压法的处理时间为1.5~2h。在本发明的一些优选的实施方式中,步骤s3中,所述计时电压法的处理时间约为2h。
54.在本发明的一些实施方式中,步骤s3中,所述计时电压法采用三电极体系。
55.在本发明的一些实施方式中,步骤s3中,所述计时电压法的对电极为铂。
56.在本发明的一些实施方式中,步骤s3中,所述计时电压法的参比电极为汞/硫酸汞。
57.本发明步骤s3所采用的计时电压法处理,虽然也以酸的水溶液作为电解液,但是与直接以酸处理的机理不相同;具体的,直接以酸处理,酸更多的是氧化钝化的作用,而本发明的计时电压法处理,则是利用电位对γ
‑
mno2进行处理,以获得在酸性条件下的活性离子,进而提升催化活性。
58.步骤s3所得产物中,所述γ
‑
mno2负载于所述导电基体表面。
59.根据本发明的再一个方面,提出了一种所述γ
‑
mno2的制备方法制备得到的γ
‑
mno2。
60.在本发明的一些实施方式中,所述γ
‑
mno2对hmf的转化效率≥59.34%。
61.根据本发明的再一个方面,提出了所述γ
‑
mno2在电催化领域的应用。
62.在本发明的一些实施方式中,所述电催化领域包括电催化氧化生物质和电催化产氧。
63.根据本发明的再一个方面,提出了一种催化电极,包括导电基体和所述γ
‑
mno2;所述γ
‑
mno2负载于所述导电基体上。
64.本发明提供的催化电极,可以用于电催化领域。
65.若无特殊说明,本发明中“约”表示误差范围在
±
2%,例如温度约为200℃,表示温度为196~204℃之间。
附图说明
66.下面结合附图和实施例对本发明做进一步的说明,其中:
67.图1为本发明实施例1所得γ
‑
mno2的tem图;
68.图2为本发明实施例1所得γ
‑
mno2的eds mapping图;
69.图3为本发明实施例1所得γ
‑
mno2的线性扫描伏安测试图谱;
70.图4为本发明实施例1和对比例1~3所得γ
‑
mno2作为工作电极对hmf催化6h时hmf的总转化效率统计结果;
71.图5为本发明实施例1和对比例1~3所得γ
‑
mno2作为工作电极对hmf催化6h时hmf转化产物的比例统计结果。
具体实施方式
72.以下将结合实施例对本发明的构思及产生的技术效果进行清楚、完整地描述,以充分地理解本发明的目的、特征和效果。显然,所描述的实施例只是本发明的一部分实施例,而不是全部实施例,基于本发明的实施例,本领域的技术人员在不付出创造性劳动的前提下所获得的其他实施例,均属于本发明保护的范围。
73.实施例1
74.本实施例制备了一种γ
‑
mno2,具体过程为:
75.d1.称取21.13g硫酸锰配制成250ml水溶液;以浓硫酸(98wt%)调节硫酸锰水溶液的ph至0.5;
76.d2.在60℃的水浴加热下,将30ml步骤d1所得溶液作为电解质溶液倒入电解池中,以1.5
×
1.5cm2的碳布作为工作电极,1
×
1cm2的铂片为对电极,汞/硫酸汞为参比电极,以5ma cm
‑2的电流密度进行计时电压法电沉积1h;
77.d3.将步骤d2得到的碳布电极置于200℃的加热台上加热4h,加热完毕后冷却;
78.d4.将步骤d3所得碳布电极作为工作电极,1
×
1cm2的铂片为对电极,汞/硫酸汞为参比电极,往电解池中加入30ml浓度为0.5mol/l的硫酸作为电解液,以10ma cm
‑2的电流密度进行计时电压法预处理2h,制得γ
‑
mno2。
79.对比例1
80.本对比例制备了一种γ
‑
mno2,具体过程与实施例1的区别为:
81.不进行步骤d3,即直接将步骤d2所得碳布电极置于30ml浓度为0.5mol/l的硫酸中进行步骤d4的计时电压法处理。
82.对比例2
83.本对比例制备了一种γ
‑
mno2,具体过程与实施例1的区别为:
84.不进行步骤d4,即直接将步骤d3所得碳布电极(负载有γ
‑
mno2的碳布)进行电化学测试。
85.对比例3
86.本对比例制备了一种γ
‑
mno2,具体过程与实施例1的区别为:
87.不进行步骤d3~d4,即直接将步骤d2电沉积所得的碳布电极(负载有γ
‑
mno2的碳布)进行电化学测试。
88.试验例
89.本试验例测试了实施例1和对比例1~3制备γ
‑
mno2的形貌、元素组成和催化活性。其中:形貌及元素组成,依托透射电镜及其与eds测试结果结合获得;催化活性通过线性扫描伏安法在1.2
‑
1.85v(vs.rhe)的扫描电压范围内电催化氧化hmf(5
‑
羟甲基糠醛)进行表征;其中线性扫描伏安法的电解液ph≈1,扫速为5mv s
‑1,每个具体实施方式所得γ
‑
mno2共进行了6h的催化活性;计算了hmf的总转化率,以及hmf转化产物的比例。测试结果如图1
~5所示。
90.实施例1所得γ
‑
mno2的透射电镜结果(图1)显示,本发明制备的γ
‑
mno2颗粒均匀,高度分散;从图1中测量得到的晶面间距及其与标准谱图中峰位的对应关系如表1所示;由表1所得结果可知,本发明制备的二氧化锰确是γ
‑
mno2。
91.表1实施例1所得γ
‑
mno2的透射电镜图中显示的晶面间距
92.位点晶面间距对应位点10.245nmγ
‑
mno2的(131)20.208nmγ
‑
mno2的(002)30.167nmγ
‑
mno2的(160)40.397nmγ
‑
mno2的(120)50.231nmγ
‑
mno2的(230)60.260nmγ
‑
mno2的(031)70.210nmγ
‑
mno2的(300)
93.实施例1所得γ
‑
mno2的eds mapping图谱(图2)显示,本发明制备的γ
‑
mno2高度分散在导电基体上,其中的原子重量比例如表2所示,结合表1的结果以及氧和锰的相对原子质量计算可知,氧和锰的原子个数比为2.38≈2(由于导电基体中含有一定的氧,因此氧的测试值会较二氧化锰的真实值偏高),说明本发明制备的材料确为二氧化锰。
94.表2实施例1所得γ
‑
mno2的原子重量比例
[0095] wt%o40.02s2.39mn57.59
[0096]
实施例1所得γ
‑
mno2的线性扫描伏安测试图谱(图3)显示,本发明制备的γ
‑
mno2对于酸性下hmf的氧化(电解液为硫酸和hmf的混合水溶液)有比竞争性产氧反应(电解液为硫酸)更低的过电位(相同电流强度下的电压),且hmf氧化的过电位较低(峰起始位置的电位)。
[0097]
以实施例1和对比例1~3所得γ
‑
mno2为工作电极,对hmf催化氧化6h时,hmf的总转化效率统计结果(图4)显示,实施例1所得γ
‑
mno2的催化活性最高,6h内hmf的转化效率为59.34%,显著高于未进行热处理(对比例1 51.21%)、未进行计时电压法处理(对比例2 42.51%),以及仅以电沉积法获得(对比例3 37.53%)的γ
‑
mno2的催化活性。这进一步说明了,本发明提供的制备方法中,电沉积、热处理以及计时电压处理发生了协同作用,若进行缺省,则会显著降低所得γ
‑
mno2的催化活性。
[0098]
以实施例1和对比例1~3所得γ
‑
mno2作为工作电极,对hmf催化6h时,hmf转化产物的比例统计(图5)结果也显示,实施例1制备的γ
‑
mno2拥有最高的电催化活性,反应6小时后dff的产率为21.24%;每个实施例对应的三组数据,从低到高依次是2h、4h和6h时各产物的产率。
[0099]
上面结合附图对本发明实施例作了详细说明,但是本发明不限于上述实施例,在所属技术领域普通技术人员所具备的知识范围内,还可以在不脱离本发明宗旨的前提下作出各种变化。此外,在不冲突的情况下,本发明的实施例及实施例中的特征可以相互组合。