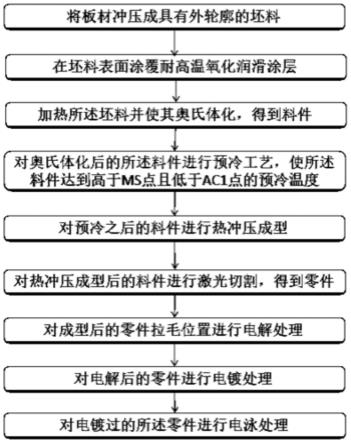
1.本发明涉及了热冲压领域,具体的是一种热冲压成型零件的制备方法。
背景技术:2.目前在热成型领域,在经过高温加热之后,裸板坯料容易产生高硬度的氧化皮,红热料片加热后材料变软,抗拉强度变小,硬度值下降,高硬度的氧化皮颗粒与变软的红热坯料在模具压力作用下,产生划痕、拉伤。行业中,一般的热成型件用铝硅镀层板,铝硅镀层板加热成形后铝镀层较软,产生的是粘着磨损,拉伤问题一般不严重;但是,如果用裸板材料进行热冲压成形后进行电泳后,由于裸板没有防腐效果,拉伤位置跟不拉伤位置的腐蚀效果都一样。而拉伤的裸板热冲压零件为了增加防腐效果,需要在裸板热冲压零件上进行电镀处理,但在进行电镀之后,拉伤位置的镀层厚度小于未拉伤的地方,另外有尖端效应,腐蚀一般都优先发生,导致拉伤地方的防腐性能比未拉伤地方电镀的防腐效果差。
3.对于如何解决热冲压零件电镀以及电泳之后防腐蚀性能较差的问题,目前还没有很好的解决办法。
技术实现要素:4.为了克服现有技术中的缺陷,本发明实施例提供了一种热冲压成型零件的制备方法,其用于解决上述热冲压零件电镀以及电泳之后防腐蚀性能较差的问题。
5.本技术实施例公开了:一种热冲压成型零件的制备方法,包括以下步骤:将板材冲压成具有外轮廓的坯料;在坯料表面涂覆耐高温氧化润滑涂层;加热所述坯料并使其奥氏体化,得到料件;对奥氏体化后的所述料件进行预冷工艺,使所述料件达到高于ms点且低于ac1点的预冷温度;对预冷之后的料件进行热冲压成型;对热冲压成型后的料件进行激光切割,得到零件;对成型后的零件拉毛位置进行电解处理;对电解后的零件进行电镀处理;对电镀过的所述零件进行电泳处理。
6.进一步地,在步骤“在坯料表面涂覆耐高温氧化润滑涂层”中,所述耐高温润滑涂层为六方氮化硼,所述耐高温涂层的厚度在0.5-20um之间,优选在0.5-10um之间。
7.进一步地,在步骤“在坯料表面涂覆耐高温氧化润滑涂层”中,所述耐高温润滑涂层涂覆于所述坯料表面在进行热冲压过程中易产生拉毛的位置。
8.进一步地,在步骤“对奥氏体化后的所述料件进行预冷,使所述料件达到高于ms点且低于ac1点的预冷温度”中,所述预冷温度在500℃-700℃,优选预冷温度在500℃-600℃;
9.进一步地,在步骤“对奥氏体化后的所述料件进行预冷工艺,使所述料件达到高于ms点且低于ac1点的预冷温度”中,所述预冷工艺采用液氮、干冰或水冷却,冷却速率为60-200℃/s,冷却时间为0.5-3s。
10.进一步地,在步骤“对奥氏体化后的所述料件进行预冷工艺,使所述料件达到高于ms点且低于ac1点的预冷温度”中,所述预冷工艺采用氮气冷却,冷却速率为30-60℃/s,冷却时间为3-10s。
11.进一步地,所述料件奥氏体化完成后出加热炉到进入压机中进行热成型的时间小于10s。
12.进一步地,在步骤“对成型后的零件拉毛位置进行电解处理”中,电解电流密度为5-20a/dm2,电解时间为3-20min。
13.进一步地,在步骤“对电解后的零件进行电镀处理”中,在电镀之前对所述零件采用超声波进行处理,以去除附着在所述零件表面的耐高温润滑涂层。
14.进一步地,在步骤“对电解后的零件进行电镀处理”中,镀层为电镀锌层,电镀处理后,对零件进行去氢处理,去氢温度在140-220℃之间,去氢时间在30min-4h之间。
15.本发明的有益效果如下:
16.通过在坯料拉伤位置涂覆耐高温润滑涂层,以及加热出炉后通过预冷工艺以降低零件的入模温度,从而可以减少料件产生的氧化皮、增加坯料冲压时候的强度,进而可以有效的减少热冲压零件的划痕,拉伤问题。然后对热冲压的零件进行电镀和电泳处理,可解决热冲压拉毛零件在电镀以及电泳后拉毛位置镀层过薄的问题,进而使得零件的耐腐蚀性能符合汽车防腐要求。
17.为让本发明的上述和其他目的、特征和优点能更明显易懂,下文特举较佳实施例,并配合所附图式,作详细说明如下。
附图说明
18.为了更清楚地说明本发明实施例或现有技术中的技术方案,下面将对实施例或现有技术描述中所需要使用的附图作简单地介绍,显而易见地,下面描述中的附图仅仅是本发明的一些实施例,对于本领域普通技术人员来讲,在不付出创造性劳动的前提下,还可以根据这些附图获得其他的附图。
19.图1是本发明实施例1中热冲压成型零件局部拉伤位置示意图。
20.图2是本发明实施例2中热冲压成型零件局部拉伤位置示意图。
21.图3是本发明对比例1中热冲压成型零件局部拉伤位置示意图。
22.图4是本发明实施例1中热冲压成型零件局部拉伤位置加速腐蚀实验结果图。
23.图5是本发明对比例1中热冲压成型零件局部拉伤位置加速腐蚀实验结果图。
24.图6是本发明实施例中热冲压成型零件的制备方法的流程图。
具体实施方式
25.下面将结合本发明实施例中的附图,对本发明实施例中的技术方案进行清楚、完整地描述,显然,所描述的实施例仅仅是本发明一部分实施例,而不是全部的实施例。基于本发明中的实施例,本领域普通技术人员在没有做出创造性劳动前提下所获得的所有其他实施例,都属于本发明保护的范围。
26.如图1至图6所示,本实施例的热冲压成型零件的制备方法,包括以下步骤:
27.将板材冲压成具有外轮廓的坯料,从而可以确定坯料的大致形状。
28.在坯料表面涂覆耐高温氧化润滑涂层,从而使得所述耐高温氧化润滑涂层可以对所述坯料起到保护作用,避免坯料直接与空气接触,进而避免了在坯料表面产生氧化皮。此外,由于耐高温氧化润滑涂层的摩擦系数较低,从而在向坯料表面涂覆耐高温氧化润滑涂
层后,减小了零件中的粗糙度,可以在后续热冲压过程中增加所述坯料与热冲压模具之间的润滑性能,减小模具与坯料之间的刮擦,进而可以减少拉毛的产生。所述耐高温氧化润滑涂层可以耐1000摄氏度的高温,从而可以避免其在所述料件奥氏体化的过程中丧失效果。由于本实施例中奥氏体化过程中最高温度在930℃,因此,在本实施例中,所述耐高温氧化润滑涂层可以耐930℃的高温。
29.加热所述坯料并使其奥氏体化,得到料件。
30.对奥氏体化后的所述料件进行预冷工艺,使所述料件达到高于ms点且低于ac1点的预冷温度。由于温度越高的环境中就会使得铁与氧气之间的反应越剧烈,从而生成更多的氧化皮。将预冷温度设定在小于ac1点可以使得坯料中的铁与氧气的反应速度很慢,而由于料件温度低于ms点会使得料件难以成型,因此使所述料件达到高于ms点且低于ac1点的预冷温度,可以降低料件在热冲压成型过程中的温度,有效减小氧化皮的产生,增加料件在后续进行热冲压时的强度。预冷温度可以在500℃-700℃,优选预冷温度可以在500℃-600℃,经发明人反复试验得出,预冷温度在500℃-600℃时的成型性能最优。
31.对预冷之后的料件进行热冲压成型,从而实现将料件成型的效果。
32.对热冲压成型后的料件进行激光切割,得到零件;
33.对成型后的零件拉毛位置进行电解处理,电解电流密度可以为5-20a/dm2,电解时间可以为3-20min。
34.对电解后的零件进行电镀处理;
35.对电镀过的所述零件进行电泳处理。
36.在本实施例中,在坯料表面涂覆耐高温氧化润滑涂层,由于隔绝了坯料与空气,从而避免了坯料上产生氧化皮。此外,耐高温氧化润滑涂层减小了零件中的粗糙度,可以在后续热冲压过程中增加所述坯料与热冲压模具之间的润滑性能,减小模具与坯料之间的刮擦,进而可以减少拉毛的产生。而在后续的电解效果中,由于电解可以去除尖端位置的拉毛,而在之前的步骤中,由于涂覆了耐高温氧化润滑涂层导致尖端位置拉毛较少,在电解后可以对较少的尖端位置以及其他位置上的拉毛进行去除,从而完全去除拉毛,进而使得拉毛位置在电泳后腐蚀性能较好。即单独的使用电解方式可以去除拉毛尤其是尖端位置的拉毛,但当尖端位置较厚时,采用电解方式无法完全去除拉毛。而单独的涂覆耐高温氧化润滑涂层可以减小拉毛厚度,将二者结合使用,可以减小拉毛的厚度,从而使得电解可以完全去除拉毛,进而能解决电泳后拉毛位置腐蚀性能差的问题。
37.借由上述方法,通过在坯料拉伤位置涂覆耐高温润滑涂层,以及加热出炉后通过预冷工艺以降低零件的入模温度,从而可以减少料件产生的氧化皮、增加坯料冲压时候的强度,进而可以有效的减少热冲压零件的划痕,拉伤问题。然后对热冲压的零件进行电镀和电泳处理,可解决热冲压拉毛零件在电镀以及电泳后拉毛位置镀层过薄的问题,进而使得零件的耐腐蚀性能符合汽车防腐要求。
38.具体的,在步骤“在坯料表面涂覆耐高温氧化润滑涂层”中,所述耐高温润滑涂层为六方氮化硼,由于六方氮化硼的摩擦系数可以低至0.16,且高温下不增大,从而比二硫化钼和石墨等常用的润滑涂层具有更高的耐高温效果。所述耐高温涂层的厚度在0.5-20um之间,优选0.5-10um。经过发明人反复测试得出,在上述厚度范围内,可以使得所述耐高温润滑涂层的厚度既可以覆盖到所述坯料表面,从而达到减小拉毛的效果,也可以防止由于耐
高温润滑涂层太厚而影响零件与热冲压模具的热传导系数,避免出现零件开裂的情况,而将耐高温润滑涂层的厚度控制在10um以内,可以较好的避免上述零件开裂的情况。在本实施例中,所述六方氮化硼的粒径小于2微米,从而可以完全覆盖到坯料表面,优选的,粒径范围在500nm-1um之间。
39.具体的,在步骤“在坯料表面涂覆耐高温氧化润滑涂层”中,所述耐高温润滑涂层涂覆于所述坯料表面在进行热冲压过程中易产生拉毛的位置。从而使得所述耐高温氧化润滑涂层可以精确的涂覆至所述坯料的相应位置,并在后续的热冲压过程中位于易产生拉毛位置进而减小拉毛的产生。
40.具体的,在步骤“对奥氏体化后的所述料件进行预冷工艺,使所述料件达到高于ms点且低于ac1点的预冷温度”中,所述预冷工艺可以采用液氮、干冰或水冷却,冷却速率为60-200℃/s,冷却时间为0.5-3s。
41.具体的,在步骤“对奥氏体化后的所述料件进行预冷工艺,使所述料件达到高于ms点且低于ac1点的预冷温度”中,所述预冷工艺采用氮气冷却,冷却速率为30-60℃/s,冷却时间为3-10s。
42.具体的,所述料件奥氏体化完成后出加热炉到进入压机中进行热成型的时间可以小于10s。从而可以使得所述料件在从加热炉到压机的过程中可以减小与空气的接触时间,进而减小氧化皮的产生。
43.具体的,在步骤“对电解后的零件进行电镀处理”中,可以在电镀之前对所述零件采用超声波进行处理,以去除附着在所述零件表面的耐高温润滑涂层。从而使得电镀镀层可以直接电镀到零件上,提升了电镀效果。
44.具体的,在步骤“对电解后的零件进行电镀处理”中,电镀处理时的镀层可以为电镀锌层,由于与其他金属相比,锌是相对便宜而又易镀覆的一种金属。从而使得电镀锌层可以较好的起到保护零件的作用。电镀处理后,对零件进行去氢处理,去氢温度在140-220℃之间,去氢时间在30min-4h之间。对在此温度和时间内对零件进行去氢处理,可以消除电镀后零件中的氢脆问题,从而提升零件强度。
45.下面通过实施例,详细说明本发明:
46.实施例1:
47.首先将1.4mm的热冲压板材22mnb5板材落料成门槛坯料;
48.接着在门槛坯料上表面拉毛位置涂覆耐高温氧化润滑涂层六方氮化硼,涂层厚度3um;
49.然后在真空炉内加热所述坯料,加热温度在930℃,加热时间4min,得到料片;
50.接着对加热奥氏体化后的料片出炉后转入到模具内,整个转运时间9s;
51.对热冲压成型后的料片进行激光切割,得到零件;
52.然后对零件进行超声波处理去除氮化硼后,再进行电镀锌,将电镀后的零件进行去氢处理,去氢温度200℃,去氢时间2h,最后对零件进行电泳处理。
53.实施例2:
54.首先将1.4mm的热冲压板材22mnb5板材落料成门槛坯料;
55.接着在门槛坯料上表面拉毛位置涂覆耐高温氧化润滑涂层六方氮化硼,涂层厚度3um;
56.然后在真空炉内加热所述坯料,加热温度在930℃,加热时间4min,得到料片;
57.接着对加热奥氏体化后的料片进行预冷:加热料片出炉后进行喷氮气,喷氮气时间7s,预冷后温度为620℃,然后将预冷后的坯料放入模具内进行热冲压成型,其中入模温度在600℃,从料片出炉到入模,整个转运时间9s;
58.对热冲压成型后的料片进行激光切割,得到零件;
59.然后对零件进行超声波处理后,再进行电镀锌,将电镀后的零件进行去氢处理,去氢温度200℃,去氢时间2h,最后对零件进行电泳处理。
60.对比例1:
61.首先将1.4mm的热冲压板材22mnb5板材落料成门槛坯料;
62.接着在门槛坯料气氛保护炉内加热所述坯料,加热温度在930℃之间,加热时间4min,得到料片;
63.接着对加热奥氏体化后的料片进行热冲压成型,其中坯料入模温度为750℃,转运时间9s;
64.对热冲压成型后的料片进行激光切割跟抛丸去除氧皮处理,得到零件;
65.然后对零件进行电镀处理,将电镀后的零件进行去氢处理,去氢温度200℃,去氢时间2h,最后对零件进行电泳处理。
66.把实施例1,2和对比例1的热冲压后的零件如图1-图3所示,然后分别对三个零件进行粗糙度测试,测试结果如下:
[0067] rarzrtrmax实施例11.16.37.497.01实施例21.05.96.96.3对比例11.6710.9112.8711.97
[0068]
从粗糙度测试看,涂覆耐高温氧化润滑涂层六方氮化硼之后可以有效的减小粗糙度,进而减少拉毛。
[0069]
把实施例1和对比例1的电泳后的零件截取部分进行电泳漆加速腐蚀测试,测试结果分别对应图4和图5所示。
[0070]
由图4和图5可知,没有涂氮化喷之后拉毛程度严重的零件在做在做电泳漆加速腐蚀测试后,有腐蚀点产生,而经过涂覆氮化喷之后拉毛程度减轻的零件在做电泳漆加速腐蚀测试后,未有腐蚀点产生。
[0071]
本发明中应用了具体实施例对本发明的原理及实施方式进行了阐述,以上实施例的说明只是用于帮助理解本发明的方法及其核心思想;同时,对于本领域的一般技术人员,依据本发明的思想,在具体实施方式及应用范围上均会有改变之处,综上所述,本说明书内容不应理解为对本发明的限制。