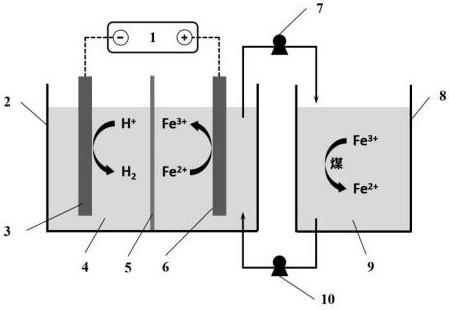
1.本发明属于氢能的制取技术领域,涉及一种电解水煤浆制氢的方法。
背景技术:2.在第75届联合国大会上,中国已向世界庄严承诺,将采取更加有力的政策和措施,co2排放力争于2030年前达到峰值,努力争取2060年前实现碳中和。当前,绿色氢能技术、生物质能利用技术及碳捕捉技术等,均有望支撑碳中和这一战略目标的实现。氢能作为一种清洁、高效、可持续的二次能源,可通过多种途径获取,是未来构建清洁低碳能源结构的重要载体。据预测,到2050年,全球范围内氢能将减少6
×
109吨co2排放,承担全球18%的能源需求。
3.当前,化石能源制氢虽成本低,但碳排放高,煤制氢每生产1kg氢气排放co
2 16kg以上。电解水制氢技术碳排放水平低,有望在短期内获得技术突破。此外,电解水制氢技术,可将h2作为储能介质,进行电网规模级产氢,实现间歇性过剩可再生能源的规模化消纳。当前,主流电解制氢技术包括碱性电解水、pem电解水、固态氧化物电解水,但存在能耗高或技术不成熟等问题。以产业化最广的碱性电解水为例,其电解效率仅为60~75%,制氢电耗达4.5~5.5 kwh/nm
3 h2,竞争力并不高。降低电解制氢电耗,已成为电解水制氢技术规模化发展的关键。
4.当前,主要有两类降低电解水制氢电耗的方法:一种是发展高活性和稳定性的析氢和析氧电催化剂,降低析氢和析氧的过电势,使电极反应尽可能接近理论电势;另一种是采用热力学上更容易发生的阳极反应取代动力学缓慢、高耗能的阳极析氧反应,该方式被称为化学物质辅助电解水制氢。第一种方式只能使电解电压接近于理论电压1.23v,而第二种方式因改变了阳极反应路径,可在低于1.23v电压下进行,显著降低制氢电耗,且可以实现高值化学品的协同制备。我国煤炭资源储量丰富,以煤的氧化反应取代传统电解水体系的阳极析氧反应,既能降低制氢电耗,又有望实现煤的高值转化,是一种有应用前景的新型制氢技术。
5.传统煤浆电解制氢技术中,煤的阳极氧化反应依赖于煤与阳极的物理碰撞,产生的电流小、析氢速率慢。为此,研究者向体系加入“电荷转移载体”fe
3+
/fe
2+
循环,从而使阳极反应以fe
2+
的快速氧化反应为主,煤与fe
3+
的反应则发生在体相电解质。该体系具有更高的电流密度、制氢速率较传统电解水煤浆体系快。然而,煤粒在电解液中的快速搅拌虽加强了传质,但对阳极及质子交换膜磨损加剧,使体系安全性降低、运行成本提高。此外,在运行中,煤表面形成了惰性含氧产物层,阻碍了fe
3+
的高效还原,使体系电流密度随时间快速衰减,无法实现长效制氢。因此,如何在fe循环辅助的基础上,解决其存在的问题,是电解水煤浆技术进一步发展的关键。
技术实现要素:6.为了解决传统煤浆电解制氢体系中煤颗粒搅拌导致的电极、质子交换膜磨损等问
题,本发明提供了一种两步法电解水煤浆制氢的方法。该方法不仅可实现低电耗制氢,还有效避免了煤粒对电解槽内关键组件的磨损,提高了体系安全性,适宜规模化应用和推广。
7.本发明的目的是通过以下技术方案实现的:一种两步法电解水煤浆制氢的方法,包括如下步骤:步骤1:含fe
2+
电解液的配置将亚铁盐加入到酸溶液中,得到含fe
2+
溶液;本步骤中,所述亚铁盐为硫酸亚铁、氯化亚铁、硝酸亚铁、磷酸亚铁中的一种或多种;本步骤中,所述酸溶液为硫酸、磷酸和盐酸中的一种或多种;本步骤中,所述fe
2+
的浓度为100~500mm;步骤2:水煤浆的配置(1)将原煤进行破碎、研磨和筛分,得到煤粉;(2)将煤粉加入酸溶液中,得到水煤浆;本步骤中,所述原煤为褐煤、次烟煤和烟煤中的一种或多种;本步骤中,所述煤粉的粒径<200目(75μm);本步骤中,所述酸溶液为硫酸、磷酸和盐酸中的一种或多种;本步骤中,所述水煤浆的浓度为20~60g/l;步骤3:电解制氢(1)以石墨毡作为阳极,并搭配一个阴极,以步骤1中配置的含fe
2+
溶液为电解液,组装成电解制氢装置;(2)在电解电压<1.23v、温度为60~100℃、搅拌速率为100~800r/min的条件下进行电解,阴极产生h2,溶液中的fe
2+
被氧化成fe
3+
;本步骤中,所述阴极是可以发生析氢反应的电极;本步骤中,所述电解制氢装置为间歇性的质子交换膜电解槽;本步骤中,所述质子交换膜为nafion 117质子交换膜;本步骤中,所述的控温方式为水浴加热、伴热加热、油浴加热或平台接触式加热;本步骤中,所述搅拌方式为磁力搅拌或机械搅拌;步骤4:含fe
3+
电解液的循环(1)将步骤2中配置的水煤浆加入水热反应器中,得到含水煤浆的水热体系;(2)将电解制氢装置中的含fe
3+
的电解液通过循环泵a转移到含水煤浆的水热体系中;步骤5:水热体系中煤对fe
3+
的还原在温度为60~100℃、搅拌速率为100~800r/min的条件下,水热体系中fe
3+
被煤还原为fe
2+
;步骤6:水热体系中溶液的循环将含fe
2+
的溶液经过循环泵b转移到电解制氢装置中;步骤7:重复步骤3~步骤6。
8.上述技术方案的核心特征是由电解体系、水热体系两个体系组成,其中:电解体系的电解液含fe
2+
,水热体系由煤与fe
3+
的混合液组成,fe
3+
为电解体系fe
2+
的氧化产物,两体
系之间由循环泵连接。相比传统体系,电解槽不含煤粒,传统体系中煤还原fe
3+
的功能由水热体系完成。具体原理如下:本发明针对传统煤浆电解制氢技术中,煤粒对阳极及质子交换膜的磨损导致体系安全性降低、运行成本高的问题,将传统体系中fe
2+
的阳极氧化和煤还原fe
3+
的反应解耦,在电解制氢体系、水热体系中分别进行fe
2+
阳极氧化辅助制氢、fe
3+
的还原。具体地,在电解制氢体系中以fe
2+
的氧化取代煤的氧化反应,在水热体系中fe
3+
被煤还原为fe
2+
,两个体系中的溶液通过循环泵连通。
9.相比于现有技术,本发明具有如下优点:本发明的“两步”法由于将电解体系中煤的主要功能,即煤还原fe
3+
的功能解耦至水热体系,因而避免了在电解制氢体系中加入煤粒,大大简化了电解水煤浆制氢体系的电解液组成,避免了煤粒对电极及质子交换膜的磨损,提高了体系的安全性。此外,在水热体系中进行fe
3+
的还原反应可通过提高温度、强化搅拌等方式实现,不受限于质子交换膜无法在较高电解质温度下工作的缺陷,从而提高了fe
3+
的还原效率。
附图说明
10.图1为两步法电解水煤浆制氢装置图;图2为阳极种类对电解制氢体系fe
2+
阳极氧化的影响;图3为fe
2+
浓度对电解制氢体系fe
2+
阳极氧化的影响;图4为反应温度对电解制氢体系fe
2+
阳极氧化的影响;图5为水热体系中反应时间对fe
3+
还原的影响;图6为水热体系中温度对fe
3+
还原的影响;图7为水热体系中煤浆浓度对fe
3+
还原的影响;图8为水热体系中fe
3+
浓度对fe
3+
还原的影响;图9为水热体系中煤阶对fe
3+
还原的影响;图10为流速对电解制氢电流密度的影响;图11为连续性质子交换膜电解槽电解煤与fe
3+
反应所得的含fe
2+
滤液制氢规律;图中,1-直流电源,2-电解制氢槽,3-阴极,4-电解液,5-质子交换膜,6-阳极,7-蠕动泵a,8-水热反应器,9-水煤浆,10-蠕动泵b。
具体实施方式
11.下面结合实施例对本发明的技术方案作进一步的说明,但并不局限于此,凡是对本发明技术方案进行修改或者等同替换,而不脱离本发明技术方案的精神和范围,均应涵盖在本发明的保护范围中。
12.实施例1向浓度为1m的h2so4溶液中加入一定质量的硫酸亚铁,获得fe
2+
浓度为100mm的溶液。使用石墨毡为工作电极,pt片为对电极,hg/hg2so4为参比电极,水浴加热控温方式,在-0.3v~1.2v vs. hg/hg2so4范围内进行循环伏安曲线扫描,电流密度随电位变化的关系曲线如图2所示。
13.实施例2
向浓度为1m的h2so4溶液中加入一定质量的硫酸亚铁,获得fe
2+
浓度为300mm的溶液。使用石墨毡为工作电极,pt片为对电极,hg/hg2so4为参比电极,水浴加热控温方式,在-0.3v~1.2v vs. hg/hg2so4范围内进行循环伏安曲线扫描,电流密度随电位变化的关系曲线如图3所示。
14.实施例3向浓度为1m的h2so4溶液中加入一定质量的硫酸亚铁,获得fe
2+
浓度为300mm的溶液。使用石墨毡为工作电极,pt片为对电极,hg/hg2so4为参比电极,水浴加热控温方式,在0.3 v vs. hg/hg2so4恒电位下进行电解制氢。当温度为60℃时,电流密度随时间的变化如图4所示。
15.实施例4在水热体系中,控制温度为90℃、搅拌速率为800r/min、煤浆浓度为50 g/l,其中煤种为霍林河褐煤。向水热体系中加入硫酸铁使fe
3+
初始浓度为500mm。反应6h后,fe
3+
可被煤浆有效还原,得到的fe
2+
浓度达到190.2mm,如图5所示。
16.实施例5在水热体系中,控制搅拌速率为800r/min、煤浆浓度为60g/l,其中煤种为霍林河褐煤。向水热体系中加入硫酸铁使fe
3+
初始浓度为100mm,反应时间为6h。当温度为100℃时,fe
3+
可被煤浆有效还原,得到的fe
2+
浓度为62.3mm,如附图6所示。
17.实施例6在水热体系中,控制温度为90℃、搅拌速率为800r/min。向其中加入硫酸铁使fe
3+
初始浓度为100mm,反应时间为6h。当煤浆浓度为50g/l时、煤种为霍林河褐煤时,fe
3+
可被煤浆有效还原,得到的fe
2+
浓度为70.6mm,如图7所示。
18.实施例7在水热体系中,控制温度为90℃、搅拌速率为800r/min、煤浆浓度为50g/l,其中煤种为霍林河褐煤。当向其中加入硫酸铁使fe
3+
初始浓度为400mm时,反应6h后,得到的fe
2+
浓度为176.1mm,如图8所示。
19.实施例8在水热体系中,控制温度为90℃、煤浆初始浓度为50g/l,其中煤种为准冬次烟煤。向其中加入硫酸铁使fe
3+
初始浓度为500mm时,反应6h后,得到的fe
2+
浓度为138.7mm,如图9所示。
20.实施例9在电解体系中进行电解制氢。首先,在1m的h2so4溶液中配置浓度为300mm的含fe
2+
溶液,fe
2+
由硫酸亚铁提供。其次,由循环泵将浓度为300mm的fe
2+
溶液持续泵入电解体系中,控制电解槽电解电位恒定为1.2v(低于水的理论分解电压1.23v),使用电化学工作站记录制氢电流密度。如图10所示,当转速为4r/min时,制氢电流密度可达到194ma/cm2并稳定1800s以上。
21.实施例10步骤1:在水热体系中,控制温度为90℃、搅拌速率为800r/min、煤浆浓度为50g/l,其中煤种为霍林河褐煤。向其中加入硫酸铁使fe
3+
初始浓度为500mm时,反应6h后,得到含fe
2+
的煤浆。
22.步骤2:将上述混合液进行过滤,去除煤粒,得到含fe
2+
的滤液。
23.步骤3:在电解体系中使用上述含fe
2+
的滤液电解制氢。在1.2v电解电压(低于水的理论分解电压1.23v)、温度90℃条件下,使用电化学工作站记录制氢电流密度。如图11所示,制氢电流密度可达149ma/cm2。
24.步骤4:电解后的滤液按步骤1进行fe
3+
的再生,并重复步骤2、步骤3。在4次循环过程中,制氢电流密度分别为153ma/cm2、154ma/cm2、143ma/cm2、136ma/cm2。