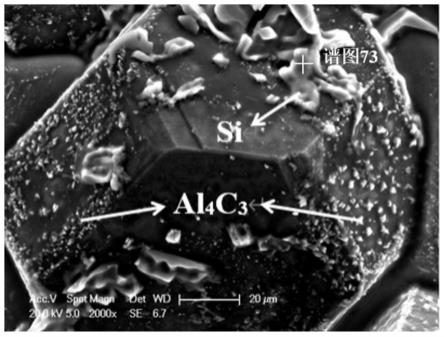
1.本发明涉及一种材料界面腐蚀剂,特别涉及一种用于检验金刚石/铝硅复合材料界面的腐蚀剂及其使用方法。
背景技术:2.金刚石/铝复合材料的热导率高、热膨胀系数低、密度小,特别适合作为芯片半导体gaas、gan等使用的高性能电子封装散热材料。金刚石/铝复合材料的制备方法主要有粉末冶金烧结法和熔体压力浸渗法两大类,其中,后者所制备的复合材料的导热系数更高(金刚石颗粒的体积分数可高达65%)且可形成异形件,因而更具发展前景。就熔体压力浸渗法而言,铝液在浸入金刚石颗粒间隙时,因金刚石/铝液接触处的元素互扩散,通过形核和生长将生成al4c3相,这种界面产物一方面能增加界面结合力因而可有效提高材料的热导率,但另一方面,因al4c3相的热导率较低且具有吸湿性,过多的al4c3相不仅会降低复合材料的热导率,还会降低其长周期服役性能。复合材料的性能在很大程度上取决于其界面组织,为此,必须寻找到一种能有效显示金刚石/铝复合材料界面处al4c3相的形貌及分布的腐蚀剂及其检验方法,通过调整制备工艺,以实现对其组织和性能的有效控制。
3.目前已有若干文献公开了检测金刚石/铝复合材料界面的腐蚀剂及其检测方法:s.kleiner等采用气压熔体浸渗法制备了金刚石/纯铝复合材料,将样品折断,在硝酸水溶液中进行电化学腐蚀以去除铝基体,然后在扫描电镜下可观察到金刚石表面有al4c3相的生成(s.kleiner,effect of diamond crystallographic orientation on dissolution and carbide formation in contact with liquid aluminium,scripta materialia 55(2006)291-294)。但该文献没有说明硝酸水溶液的浓度及电化学腐蚀参数(如被腐蚀面积的电流密度、腐蚀时间等),实际操作时控制的难度较大。i.e.monje等采用气压熔体浸渗法制备了金刚石/纯铝复合材料,设计了一种专用装置对样品进行电化学腐蚀:将棒状样品(阴极)插入铜制空心圆柱体(阳极)中,在空心圆柱体内侧的上下两端采用o型密封圈,将样品与空心圆柱体的径向间距固定为3mm,然后将装置置于10%(体积比)的硝酸水溶液中,腐蚀电流密度控制为2a/cm2,发现腐蚀时间为2.5min时,在扫描电镜下可较好地观察到金刚石表面形成的al4c3相的形貌(i.e.monje,aluminum/diamond composites:apreparative method to characterize reactivity and selectivity at the interface,scripta materialia 66(2012)789-792)。然而该文献提供的电化学腐蚀装置较复杂,特别是圆柱状金刚石/铝复合材料极难加工,实际应用难度很大。此外,上述两例均采用单一硝酸水溶液作为腐蚀剂,界面反应物al4c3相会随铝基体的腐蚀而部分溶于腐蚀液中,难以显示其真实形貌。
4.近年来,金刚石/铝硅复合材料已得到更为广泛的研究,这是因为铝硅合金的熔点低、流动性好,因而浸渗温度显著低于纯铝,可有效控制金刚石/铝基体界面的反应程度,避免过量al4c3相的生成。此外,研究表明硅相还能附着在金刚石的部分表面,既可以减少al4c3相的生成量,还可以进一步增强界面结合力。与纯铝基体相比,金刚石/铝硅复合材料
界面处al4c3相的生成量相对较少,为此必须找到一种新型腐蚀剂及其界面检验方法,首先要避免对al4c3相的腐蚀破坏,同时还要避免对硅相的过度腐蚀,最终能有效显示出这两种相的形貌,以便为复合材料组织和性能的控制提供依据。
技术实现要素:5.发明目的:本发明旨在提供一种用于检验金刚石/铝硅复合材料界面的腐蚀剂,能完整显示出al4c3相和硅相的形貌,为复合材料组织和性能的控制提供依据;本发明的另一目的是提供该腐蚀剂的使用方法。
6.技术方案:本发明的一种用于检验金刚石/铝硅复合材料界面的腐蚀剂,包括腐蚀溶液ⅰ和腐蚀溶液ⅱ,所述腐蚀溶液ⅰ包括硝酸、丙三醇和水;所述腐蚀溶液ⅱ包括氢氟酸、次磷酸、丙三醇和水。
7.所述腐蚀溶液ⅰ中,硝酸能快速去除较厚的铝覆盖层,使金刚石/铝基体界面初步显露出来,而丙三醇能抑制铝基体的点腐蚀,使铝基体的腐蚀去除过程更为均匀。
8.所述腐蚀溶液ⅱ中,氢氟酸和次磷酸将al4c3相周围残余的铝层进一步腐蚀去除干净,同时丙三醇能使铝基体的腐蚀去除过程更为均匀;此外,次磷酸还能防止电解时硅氧化为sio2而被氢氟酸溶解,有助于显示出硅相的真实形貌,且其腐蚀产物次磷酸铝溶于水,可确保腐蚀过程的持续进行。
9.优选的,所述腐蚀溶液ⅰ中,每100ml溶液中包括10~12ml硝酸,8~10ml丙三醇,其余为水;所述硝酸质量分数为65~70%。
10.腐蚀溶液ⅰ的配置:取少量水于烧杯中,量取硝酸缓慢加入烧杯中,用玻璃棒搅拌,使其混合均匀,再加入丙三醇,搅拌均匀,最后加入水混合并定容到100ml。
11.优选的,所述腐蚀溶液ⅱ中,每100ml溶液中包括5~7ml氢氟酸,7~10ml次磷酸,其余为水;所述氢氟酸质量分数35~40%;所述次磷酸质量分数85~85%。
12.腐蚀溶液ⅱ的配置:取少量水于烧杯中,分别量取氢氟酸和次磷酸缓慢加入烧杯中用玻璃棒搅拌,使其混合均匀,再加入丙三醇,搅拌均匀,最后加入水混合并定容到100ml。
13.本发明的腐蚀剂的使用方法,包括以下步骤:
14.(1)将金刚石/铝硅复合材料试样加工成片状样品,打磨,清洗,干燥;
15.(2)将腐蚀试样与直流电源的正极连接,铂电极与负极连接,然后将正极与负极均放入腐蚀溶液ⅰ中,打开直流电源开始电解腐蚀,之后取出试样清洗并烘干;
16.(3)将(2)的试样与直流电源的正极连接,铂电极与负极连接,然后将正极与负极均放入腐蚀溶液ⅱ中,打开直流电源开始电解腐蚀,之后取出试样在酒精中清洗并烘干;
17.(4)在扫描电子显微镜下观察金刚石和铝基体的界面及其反应产物。
18.优选的,步骤(1)中所述的金刚石/铝硅复合材料,其基体中硅的重量百分比为5~9wt%,余量为铝。
19.优选的,步骤(2)中所述的腐蚀溶液ⅰ温度为25℃条件下,电解腐蚀的腐蚀电流密度为2a/cm2,电解时间为10~14s。
20.其中,腐蚀电流密度为直流电源的电流强度除以试样暴露处铝硅基体部分的面积,而试样暴露处铝硅基体的面积百分比等于铝硅基体在金刚石/铝硅复合材料中的体积
百分比。
21.优选的,步骤(3)中所述的腐蚀溶液ⅱ温度为25℃条件下,电解腐蚀的腐蚀电流密度为2a/cm2,电解时间为16~20s。
22.优选的,所述步骤(1)采用激光切割机将金刚石/铝硅复合材料试样加工成片状样品,将切割面进行打磨处理,之后清洗并吹干;然后利用绝缘胶覆盖试样的部分面积,露出电解腐蚀面,制备出腐蚀试样。
23.优选的,步骤(2)中所述的腐蚀试样,其浸入腐蚀溶液的电解腐蚀面积为10mm
×
3mm,其他浸入腐蚀溶液的部分均以绝缘胶覆盖。
24.发明机理:与纯铝相比,由于铝硅合金的熔点低、流动性好,浸渗温度显著低于纯铝,因而金刚石/铝硅复合材料界面处al4c3相的生成量较少,为此,首先要避免对al4c3相的腐蚀破坏,同时还要避免对硅相的过度腐蚀,最终能有效显示出这两种相的形貌。本发明的用于检验金刚石-硅铝复合材料的腐蚀剂包括腐蚀溶液ⅰ和腐蚀溶液ⅱ。腐蚀溶液ⅰ中,硝酸水溶液快速去除较厚的铝覆盖层,使金刚石/铝基体界面初步显露出来,而丙三醇能抑制铝基体的点腐蚀,使铝基体的腐蚀去除过程更为均匀,通过控制电解腐蚀时间从而防止对al4c3相造成腐蚀破坏。腐蚀溶液ⅱ中,氢氟酸和次磷酸将al4c3相周围残余的铝层进一步腐蚀去除干净,同时丙三醇能使铝基体的腐蚀去除过程更为均匀;氢氟酸和次磷酸主要用于腐蚀铝基体,而对al4c3相的腐蚀作用很小;此外,次磷酸还具有较强的还原性,可防止电解时硅氧化为sio2而被氢氟酸溶解,有助于显示出硅相的真实形貌,且其腐蚀产物次磷酸铝溶于水,可确保腐蚀过程的持续进行。
25.有益效果:与现有技术相比,本发明具有如下显著优点:(1)腐蚀剂能清晰完整地显示出金刚石/铝硅复合材料界面处al4c3相和硅相的形貌,效率高,重现性好;(2)通过腐蚀剂ⅰ和ⅱ配方的调整,以及两步电解工艺,保证了界面处al4c3相的完整显示,避免了采用单一硝酸水溶液长时间腐蚀时对al4c3相形貌的破坏;(3)该腐蚀剂的使用方法操作简单,效率高,重现性好。
附图说明
26.图1为实施例1中金刚石/铝硅复合材料界面照片;
27.图2为实施例1中金刚石/铝硅复合材料界面处si颗粒的eds能谱图;
28.图3为实施例2中金刚石/铝硅复合材料界面照片;
29.图4为实施例3中金刚石/铝硅复合材料界面照片;
30.图5为对比例1中金刚石/铝硅复合材料界面照片。
具体实施方式
31.下面结合实施例对本发明的技术方案作进一步说明。
32.实施例1
33.本发明的用于检验金刚石/铝硅复合材料界面的腐蚀剂,包括腐蚀溶液ⅰ和腐蚀溶液ⅱ,腐蚀溶液ⅰ包括:质量分数68%的硝酸11ml,纯度为99%的丙三醇8ml,余量为去离子水;腐蚀溶液ⅱ包括:质量分数35%的氢氟酸7ml,质量分数80%的次磷酸10ml,纯度为99%的丙三醇9ml,余量为去离子水。
34.腐蚀溶液ⅰ的配制:取少量去离子水于烧杯中,量取11ml硝酸缓慢加入烧杯中,用玻璃棒搅拌,使其混合均匀,再加入8ml丙三醇,搅拌均匀,最后加入去离子水混合并定容到100ml。
35.腐蚀溶液ⅱ的配制:取少量去离子水于烧杯中,分别量取7ml氢氟酸和10ml次磷酸缓慢加入烧杯中,用玻璃棒搅拌,使其混合均匀,再加入9ml丙三醇,搅拌均匀,最后加入去离子水混合并定容到100ml。
36.本发明的用于检验金刚石/铝硅复合材料界面的腐蚀剂的使用方法包括以下步骤:
37.(1)电解腐蚀试样制备:
38.试样1为金刚石/铝硅复合材料(金刚石体积分数为65vol%;基体为al-9wt%si合金),采用气压浸渗制备(浸渗温度为630℃,气压为1.5mpa,金刚石/铝液接触时间为3min)。用激光切割机将复合材料切割成10mm
×
10mm
×
2mm的片状,将切割面进行打磨处理,之后清洗并吹干;然后利用绝缘胶覆盖试样的部分面积,露出10mm
×
3mm的电解腐蚀面(其中金属基体面积占复合材料面积的35%),获得腐蚀试样。
39.(2)将腐蚀试样与直流电源的正极连接,铂电极片与负极连接,然后将正极与负极均放入25℃的腐蚀溶液ⅰ中,保证样品的电解腐蚀面完全浸没于腐蚀溶液,打开直流电源,调节电压,使腐蚀样品暴露处金属基体的腐蚀电流密度达到2a/cm2,电解时间为10s,之后取出试样在酒精中清洗并烘干;
40.(3)将(2)腐蚀后的试样与直流电源的正极连接,铂电极与负极连接,然后将正极与负极均放入25℃的腐蚀溶液ⅱ中,保证样品的电解腐蚀面完全浸没于腐蚀溶液,打开直流电源,调节电压,使腐蚀样品暴露处金属基体的腐蚀电流密度达到2a/cm2,电解时间为18s,之后取出试样在酒精中清洗并烘干;
41.(4)在扫描电子显微镜下观察金刚石和铝基体的界面,结果如图1。
42.由图1可见,al4c3相呈细颗粒状稀疏附着在金刚石表面生长,且在不同表面呈选择性的非均匀分布。相关研究表明,al4c3相在金刚石的(1 1 1)晶面上容易生长,而在(1 0 0)晶面上较难生长(i.e.monje,aluminum/diamond composites:a preparative method to characterize reactivity and selectivity at the interface,scripta materialia 66(2012)789-792),这与图1的结果吻合。在图1中还可看到在金刚石表面附着有粗大的颗粒,经eds能谱表征(图2),其为硅颗粒。可见,本发明的腐蚀剂及其检验方法能方便有效地检验金刚石/铝硅复合材料的界面组织。
43.实施例2
44.本发明的用于检验金刚石/铝硅复合材料界面的腐蚀剂,包括腐蚀溶液ⅰ和腐蚀溶液ⅱ,腐蚀溶液ⅰ包括:质量分数70%的硝酸10ml,纯度为99%的丙三醇9ml,余量为去离子水;腐蚀溶液ⅱ包括:质量分数38%的氢氟酸6ml,质量分数83%的次磷酸9ml,纯度为99%的丙三醇10ml,余量为去离子水。
45.腐蚀溶液ⅰ的配制:取少量去离子水于烧杯中,量取10ml硝酸缓慢加入烧杯中,用玻璃棒搅拌,使其混合均匀,再加入9ml丙三醇,搅拌均匀,最后加入去离子水混合并定容到100ml。
46.腐蚀溶液ⅱ的配制:取少量去离子水于烧杯中,分别量取6ml氢氟酸和9ml次磷酸
缓慢加入烧杯中,用玻璃棒搅拌,使其混合均匀,再加入10ml丙三醇,搅拌均匀,最后加入去离子水混合并定容到100ml。
47.本发明的用于检验金刚石/铝硅复合材料界面的腐蚀剂的使用方法包括以下步骤:
48.(1)电解腐蚀试样制备:
49.试样2为金刚石/铝硅复合材料(金刚石体积分数为64vol%;基体为al-5wt%si合金),采用气压浸渗制备(浸渗温度为700℃,气压为1.5mpa,金刚石/铝液接触时间为3min)。用激光切割机将复合材料切割成10mm
×
10mm
×
2mm的片状,将切割面进行打磨处理,之后清洗并吹干;然后利用绝缘胶覆盖试样的部分面积,露出10mm
×
3mm的电解腐蚀面(其中金属基体面积占复合材料面积的36%),获得腐蚀试样。
50.(2)将腐蚀试样与直流电源的正极连接,铂电极片与负极连接,然后将正极与负极均放入25℃的腐蚀溶液ⅰ中,保证样品的电解腐蚀面完全浸没于腐蚀溶液,打开直流电源,调节电压,使腐蚀样品暴露处金属基体的腐蚀电流密度达到2a/cm2,电解时间为14s,之后取出试样在酒精中清洗并烘干;
51.(3)将(2)腐蚀后的试样与直流电源的正极连接,铂电极与负极连接,然后将正极与负极均放入25℃的腐蚀溶液ⅱ中,保证样品的电解腐蚀面完全浸没于腐蚀溶液,打开直流电源,调节电压,使腐蚀样品暴露处金属基体的腐蚀电流密度达到2a/cm2,电解时间为20s,之后取出试样在酒精中清洗并烘干;
52.(4)在扫描电子显微镜下观察金刚石和铝基体的界面,结果如图3。
53.由图3可以看出,al4c3相和硅相在金刚石表面的附着,其中al4c3相在金刚石不同表面呈选择性的非均匀分布。与实施例1相比,本实施例的浸渗温度较高(700℃),而硅含量降低(5wt%si),因而al4c3相尺寸有所增大,而硅相的分布密度降低。可见,本发明的腐蚀剂及其检验方法能方便有效地检验金刚石/铝硅复合材料的界面组织。
54.实施例3
55.本发明的用于检验金刚石/铝硅复合材料界面的腐蚀剂,包括腐蚀溶液ⅰ和腐蚀溶液ⅱ,腐蚀溶液ⅰ包括:质量分数65%的硝酸12ml,纯度为99%的丙三醇10ml,余量为去离子水;腐蚀溶液ⅱ包括:质量分数40%的氢氟酸5ml,质量分数85%的次磷酸7ml,纯度为99%的丙三醇8ml,余量为去离子水。
56.腐蚀溶液ⅰ的配制:取少量去离子水于烧杯中,量取12ml硝酸缓慢加入烧杯中,用玻璃棒搅拌,使其混合均匀,再加入10ml丙三醇,搅拌均匀,最后加入去离子水混合并定容到100ml。
57.腐蚀溶液ⅱ的配制:取少量去离子水于烧杯中,分别量取5ml氢氟酸和7ml次磷酸缓慢加入烧杯中,用玻璃棒搅拌,使其混合均匀,再加入8ml丙三醇,搅拌均匀,最后加入去离子水混合并定容到100ml。
58.本发明的用于检验金刚石/铝硅复合材料界面的腐蚀剂的使用方法包括以下步骤:
59.(1)电解腐蚀试样制备
60.试样3为金刚石/铝硅复合材料(金刚石体积分数为63vol%;基体为al-7wt%si合金),采用气压浸渗制备(浸渗温度为750℃,气压为1.5mpa,金刚石/铝液接触时间为3min)。
用激光切割机将复合材料切割成10mm
×
10mm
×
2mm的片状,将切割面进行打磨处理,之后清洗并吹干;然后利用绝缘胶覆盖试样的部分面积,露出10mm
×
3mm的电解腐蚀面(其中金属基体面积占复合材料面积的37%),获得腐蚀试样。
61.(2)将腐蚀试样与直流电源的正极连接,铂电极片与负极连接,然后将正极与负极均放入25℃的腐蚀溶液ⅰ中,保证样品的电解腐蚀面完全浸没于腐蚀溶液,打开直流电源,调节电压,使腐蚀样品暴露处金属基体的腐蚀电流密度达到2a/cm2,电解时间为12s,之后取出试样在酒精中清洗并烘干;
62.(3)将(2)腐蚀后的试样与直流电源的正极连接,铂电极与负极连接,然后将正极与负极均放入25℃的腐蚀溶液ⅱ中,保证样品的电解腐蚀面完全浸没于腐蚀溶液,打开直流电源,调节电压,使腐蚀样品暴露处金属基体的腐蚀电流密度达到2a/cm2,电解时间为16s,之后取出试样在酒精中清洗并烘干;
63.(4)在扫描电子显微镜下观察金刚石和铝基体的界面,结果如图4。
64.由图4可以看出,al4c3相和硅相在金刚石表面的附着,其中al4c3相在金刚石不同表面呈选择性的非均匀分布。由于本实施例的浸渗温度很高(750℃),al4c3相尺寸明显增大,且密集分布在金刚石表面,而硅相分布情况介于实施例1和实施例2之间。可见本发明的腐蚀剂及其检验方法能方便有效地检验金刚石/铝硅复合材料的界面组织。
65.对比例1
66.(1)电解腐蚀试样制备:
67.与实施例2完全相同。
68.(2)腐蚀剂配制及腐蚀方法:
69.参照了i.e.monje的论文(i.e.monje,aluminum/diamond composites:a preparative method to characterize reactivity and selectivity at the interface,scripta materialia 66(2012)789-792)中用于金刚石/纯铝复合材料界面显示的腐蚀剂及检验方法:
70.a.腐蚀剂:取少量去离子水于烧杯中,量取10ml质量百分比为68%的硝酸缓慢加入烧杯中,用玻璃棒搅拌,使其混合均匀,再加入去离子水混合并定容到100ml。
71.b.电化学腐蚀:将腐蚀试样与直流电源的正极连接,铂电极片与负极连接,然后将正极与负极均放入25℃的腐蚀溶液中,保证样品的电解腐蚀面完全浸没于腐蚀溶液,打开直流电源,调节电压,使腐蚀样品暴露处金属基体的腐蚀电流密度达到2a/cm2,电解时间为2.5min,之后取出试样在酒精中清洗并烘干;
72.c.在扫描电子显微镜下观察金刚石和铝基体的界面,结果如图5。
73.由图5可见,在金刚石表面看不到al4c3相的存在,只见到密集分布的腐蚀凹坑,这应该是界面反应物al4c3相被腐蚀去除或脱落后留下的凹坑。在金刚石表面可看到硅相颗粒,但其尺寸比实施例2中的略小,说明硅颗粒也受到一定的腐蚀作用。
74.通过三个实施例的金刚石/铝硅复合材料界面的电解腐蚀效果图对比分析可知,随浸渗温度升高,al4c3颗粒逐渐粗化,在界面的分布从稀疏逐渐变为密集;随铝硅合金中硅含量的升高,金刚石表面的硅相数量也逐步增多。本发明方法可以较好检测出不同浸渗温度及不同硅含量制备的金刚石/铝硅复合材料的界面差异,为复合材料的研究和生产提供了有效的检测手段。