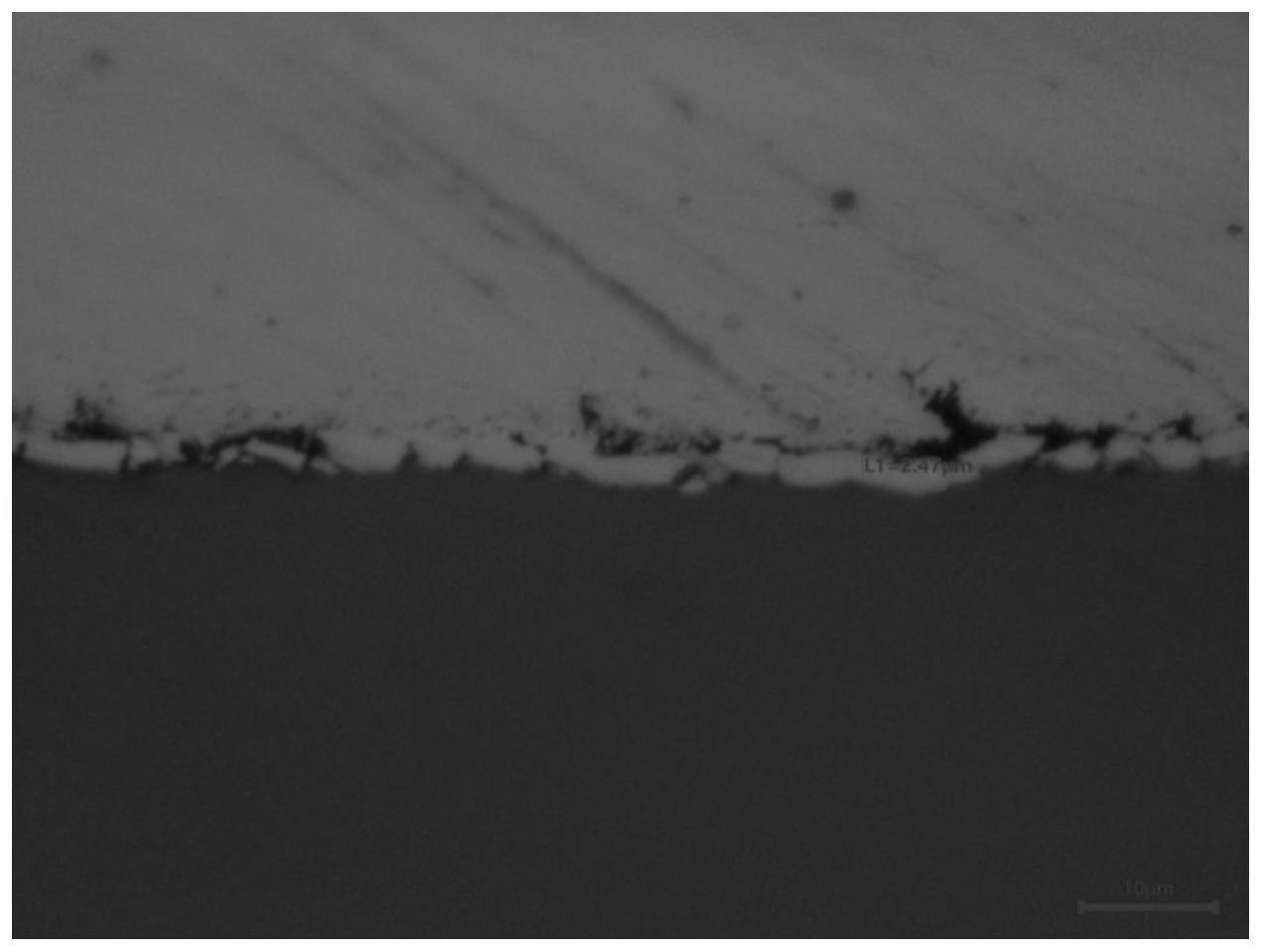
一种ru和pt共改性的铝化物涂层及其制备工艺
技术领域
1.本发明涉及高温防护涂层技术领域,具体涉及一种ru和pt共改性的铝化物涂层及其制备工艺。
技术背景
2.镍基高温合金具有优异的高温力学性能,因此在航空发动机涡轮叶片、导向叶片等热端部件中被大量应用。随着航空发动机向着高推重比、高进口温度的方向发展,特别是燃烧室中的燃气温度和燃气压力不断提高,这对高温合金热端部件的性能提出了更高的要求。经过多年的发展,虽然高温合金的高温力学性能有了很大的提高,但是以牺牲其抗高温氧化及抗热腐蚀性能为代价。为了保证高温合金在苛刻的工作环境中,既具有优异的高温机械性能又兼顾良好的抗高温氧化以及抗热腐蚀性能,必须采取相应的措施来提高其综合性能,最有效的方法就是在高温合金表面上制备高温防护涂层。因此,高温防护涂层技术也成为高性能航空发动机的关键技术之一。
3.高温防护涂层经历了简单铝化物涂层、改性铝化物涂层、mcraly涂层和热障涂层等几代的发展。简单铝化物涂层,因其工艺简单和制备成本低,于20世纪60年代开始被广泛应用于燃气轮机与航空发动机的热端部件防护中。虽然简单铝化物涂层具有优异的抗高温氧化性能,但是也存在一些缺点,例如:抗高温热腐蚀性能差、涂层脆性大和氧化膜较易脱落等。因此,为了进一步提高简单铝化物涂层的性能,研究人员在涂层中添加一定量的si、cr、co、zr、hf、y和pt等元素进行改性,获得改性铝化物涂层以提高简单铝化物涂层的性能。
4.目前,在众多改性铝化物涂层中,pt改性涂层是性能较优异且应用最广泛的改性铝化物涂层。pt元素的添加可以降低涂层生成保护性al2o3膜的临界al含量,降低al2o3膜的生长速率以及提高al2o3膜与涂层的结合力,减缓涂层中al元素的消耗,从而延长涂层的寿命。然而,有研究发现pt改性铝化物涂层在高温氧化之后,涂层表面会发生严重的褶皱现象。当pt改性铝化物涂层作为热障涂层体系的金属粘结层使用时,粘结层表面褶皱的发生极易导致陶瓷顶层脱落,严重影响热障涂层的服役寿命,在一定程度上限制了pt改性铝化物涂层的应用。因此,需要采取相应措施抑制pt改性铝化物涂层在高温氧化条件下表面褶皱的发生。
技术实现要素:5.本发明的目的在于提供一种ru和pt共改性的铝化物涂层及其制备工艺,利用电镀、真空退火处理和化学气相沉积相结合制备了ru和pt共改性铝化物涂层,以综合ru和pt元素添加对铝化物涂层的有益作用,提高简单铝化物涂层的高温性能。
6.为实现上述目的,本发明所采用的技术方案如下:
7.一种ru和pt共改性铝化物涂层的制备工艺,该工艺包括以下步骤:
8.(1)高温合金基体前处理:基体依次进行抛光、喷砂、超声清洗;
9.(2)纯ru层和纯pt层的制备:采用电镀方法在高温合金基体上依次沉积纯ru层和
纯pt层;
10.(3)真空退火处理:电镀纯ru层和纯pt层后在真空退火炉中进行退火,退火处理过程为:首先升温到500~700℃保温1~3h,以除去纯ru层和纯pt层的应力;然后升温到900~1100℃保温3~5h,以使纯ru层和纯pt层与高温合金基体发生元素互扩散,保温程序结束后样品随炉冷却到室温。
11.(4)化学气相渗al:退火处理后,采用化学气相沉积法进行渗al,在高温合金基体上获得ru和pt共改性的铝化物涂层。
12.上述步骤(1)中,高温合金基体前处理具体过程为:分别采用180、240、300和400目的砂纸进行打磨,之后进行喷砂处理,以去除基体表面的氧化皮;然后依次在去离子水中超声30~45min,在丙酮中超声10~30min,以去除可能存在的表面污染物。
13.上述步骤(2)中,采用电镀方法制备纯ru层的过程中,镀液的组成为:三氯化钌(以ru当量计算)4~10g/l,硫酸铵15~45g/l,氯化铵5~10g/l,氨基磺酸8~16g/l,其余为去离子水;镀液ph值为1~3,镀液温度为40~60℃,电流密度为2~8a/dm2,电镀时间为40~80min,电镀过程中,样片能够自转,自转转速为10-50r/min。
14.上述步骤(2)中,采用电镀方法制备纯pt层的过程中,镀液的组成为:二亚硝基二胺合铂(以pt当量计算)4~10g/l,其余为去离子水;镀液ph值为1~3,镀液温度为50~90℃,电流密度为2~8a/dm2,电镀时间为25~60min。
15.上述步骤(3)退火处理过程中:真空退火炉的真空度控制在1.0
×
10-3
以下,升温速率小于10℃/min。
16.上述步骤(3)中,经真空退火处理后,纯ru层和纯pt层与高温合金基体发生元素互扩散,ru和pt元素向高温合金基体的扩散深度为10~25μm。
17.上述步骤(4)中,化学气相沉积渗al过程中,所用渗剂由cral合金(粉体或块体)和活化剂组成,其中:活化剂含量为0.5~3.0wt.%,余量为cral合金;cral合金中cr含量为30~50wt.%;所述活化剂为nh4cl、naf、nh4f或alf3;化学气相沉积的温度为1050~1060℃,沉积时间2~6h,沉积过程中采用ar或h2/ar混合气为保护性气体。
18.本发明设计机理如下:
19.经研究,rual合金的熔点比具有相同化学计量比及相同相结构的镍铝合金高约400℃,并且表现出更优异的高温蠕变性能。本发明通过工艺设计,在基体上依次制备纯ru层和pt层,经退火和渗al后得到ru和pt共改性的铝化物涂层,该涂层的主要相组成为β相。该涂层在高温氧化之后,ru改性铝化物涂层表面没有发生明显的褶皱现象,表明采用本发明工艺添加的ru元素能够抑制nial涂层在高温氧化条件下表面褶皱的发生。本发明综合ru和pt元素添加对铝化物涂层的有益作用,提高了简单铝化物涂层的高温性能。
20.本发明具有以下优点:
21.1、本发明采用电镀、真空退火处理和化学气相沉积相结合,在镍基高温合金上制备出ru和pt共改性铝化物涂层,涂层中的ru和pt元素的含量可精准调控。
22.2、本发明电镀ru过程中,采用传动装置使样片自转并且可以调节样片转速以及正反转方向,镀ru层的均匀性可以得到有效保证,避免由于厚度不均导致应力集中而引起的镀ru层脱落。
23.3、本发明采用化学气相沉积渗al,不受试样的尺寸和形状的影响,通过调控渗铝
工艺可以控制涂层的厚度,涂层的可控性强。
24.4、本发明所制备的ru和pt共改性铝化物涂层具有优异的抗高温氧化性能,能有效的保护基体合金,显著的提高发动机热端部件的使用寿命。
25.5、本发明制备的ru和pt共改性的铝化物涂层可用于镍基高温合金的防护。
附图说明
26.图1为电镀ru层的金相截面图。
27.图2为电镀ru和pt层的金相截面图。
28.图3为真空退火后的金相截面图。
29.图4为ru和pt共改性铝化物涂层的金相截面图。
30.图5为ru和pt共改性铝化物涂层的xrd图谱。
31.图6为pt改性铝化物涂层循环氧化之后的截面形貌。
32.图7为电镀ru样片自转装置示意图。
具体实施方式
33.以下结合附图和实施例详述本发明。
34.实施例1
35.本实施例是在镍基高温合金上制备ru和pt共改性铝化物涂层,所用的镍基高温合金的成分(wt.%):co 10.0%,cr 8.0%,w 11.0%,al 6.0%,ti 1.0%,mo 1.0%,nb 1.5%,c 0.05%,余量为ni,涂层具体制备过程如下:
36.首先,对高温合金基体依次采用180、240、300和400目的砂纸进行打磨抛光,之后进行喷砂处理,以去除基体表面的氧化皮;然后在去离子水和丙酮中依次超声处理30min,以去除可能存在的表面污染物,烘干后待用。
37.然后,进行ru层的制备,以纯铂片为阳极,以基体作为阴极,具体的镀ru工艺如下:镀液温度为55℃,电流密度为2a/dm2,镀液ph为1.5。镀ru液的组成为:三氯化钌(以ru当量计算)8g/l,硫酸铵35g/l,氯化铵5g/l,氨基磺酸12g/l,其余为去离子水。电镀时间为60min,ru层厚度为2μm左右,图1为电镀ru层的金相截面图。
38.再在ru层表面电镀pt层,将已经镀ru层的样品用去离子水清洗后,将镀ru样品作为阴极放入镀pt液中,具体的镀pt工艺如下:镀液温度85℃,电流密度为3a/dm2,镀液ph为2.0,以纯铂片为阳极。镀pt液的组成为:二亚硝基二胺合铂(以pt当量计算)6g/l,其余为去离子水。电镀时间为25min,pt层厚度为2μm左右,图2为电镀ru和pt层的金相截面图。
39.电镀完成后,将样品进行真空退火处理,以降低基体表面ru和pt元素的含量。退火的具体工艺为:升温速率为8℃/min,首先在680℃条件下保温2h以去除镀层应力,然后在1100℃条件下扩散4h,最后随炉冷却,图3为真空退火后样品的金相截面图,ru和pt元素向基体中的扩散深度为20μm左右。
40.最后进行气相渗al,具体的渗al工艺如下:渗剂为cr含量为50wt.%的cral合金块100g,nh4f作为活化剂1.0g,渗al温度为1060℃,时间为5h,渗al过程中以h2和ar混合气(混合气中h2含量10vol.%)作为保护气,结束后随炉冷却到室温,图4为ru和pt共改性铝化物涂层的金相截面图,涂层分为两层,涂层总厚度在45μm左右;
41.本实施例中,采用xrd检测涂层的相组成。根据图5涂层的xrd图谱分析,涂层主要由β-(ni,pt)al、rual和ptal2相组成。
42.对比例1:
43.与实施例1不同之处在于:省略制备ru层的步骤。
44.图6为对比例1中pt改性铝化物涂层循环氧化之后的截面形貌。从图中可以看出,氧化后pt改性铝化物涂层表面出现明显的褶皱现象,经过测定涂层表面的粗糙度由1.89μm增加到7.57μm,粗糙度的增量高达5.68μm。
45.然而经过测定,实施例1中ru和pt共改性铝化物涂层经循环氧化后表面的粗糙度由1.74μm增加到5.73μm,粗糙度的增量仅为3.99μm,显然,ru元素引入之后有效的降低了pt改性铝化物涂层在高温氧化过程中表面褶皱的发生。
46.本发明实施例1中,电镀ru过程中,采用传动装置使样片自转并且可以调节样片转速(自转速度10-50r/min,实施例1自转速度为30r/min)以及正反转方向,有效保证镀ru层的均匀性,避免由于厚度不均导致应力集中而引起的镀ru层脱落。图7为电镀ru样片自转装置示意图,该装置包括电机、传动轴和控制器,电机输出轴连接传动轴,传动轴也样片相连接,通过控制器控制样片自转转速及自转方向。
47.以上所述仅为发明的较佳实施例而已,并不用以限制本发明,凡在本发明的精神和原则之内,所作的任何修改、等同替换、改进等,均应包含在本发明的保护范围之内。