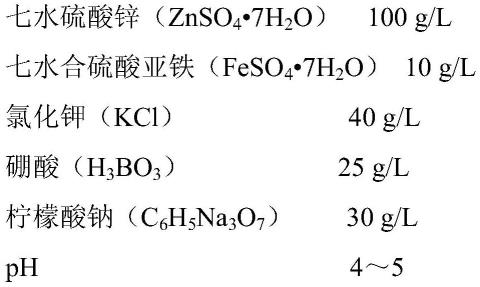
1.本发明属于电镀工艺技术领域,涉及一种闪镀锌铁合金镀液及其电镀方法。
背景技术:2.目前,随着终端客户对家电、汽车等产品外观要求越来越高,电镀锌板成品表面不允许有肉眼明显可见的表面缺陷。这就意味着大部分钢厂在金属表面电镀锌时,不能允许基板表面的质量缺陷影响电镀后电镀锌产品的表面质量,以免造成巨大的经济损失。因此越来越多的先进钢企采用了闪镀前处理,用以遮盖电镀基板的表面缺陷。
3.闪镀是指在短时间内通过使用大电流,在镀件表面尽快镀上一层极薄的镀层,为下一步电镀做好准备。在钢带电镀锌的生产中,目前常见的闪镀技术有闪镀镍,即在电镀前先闪镀一层镍层。但是闪镀镍技术会产生含镍离子的报废槽液和漂洗废水,而镍离子是重金属离子,其毒害性大,对环境污染大。随着国内对污染物排放的要求越来越严格,闪镀镍的应用将受到越来越大的限制。
4.有人开发了闪镀铁工艺(霍胜娟等.闪镀铁镀液及闪镀方法,cn 111424295 a),然而对于现场生产中存在着两方面技术问题,首先闪镀铁技术是电镀锌前在基板上闪镀一层金属铁层,由于与后续的电镀锌镀层属于不同的金属镀层,后续的金属锌镀层与闪镀铁镀层之间存在不同镀层之间的局部内应力,影响锌镀层的镀层结合力,导致镀层结合力差,在客户端使用时可能会造成镀层脱、剥落隐患。其次是镀液中的亚铁离子在现场生产时易氧化成三价铁离子,镀液的不稳定性,会影响闪镀铁的电镀效果,使得闪镀铁层出现厚度不均、结晶粗大、针孔、镀层灰暗等缺陷。为了解决这个问题,有人提出了闪镀锌工艺(黄道兵等.闪镀锌镀液及其制备方法与闪镀方法,cn 111270276 a),但实际操作显示,闪镀锌的活性非常高,且闪镀的镀层非常薄,导致锌在环境中的稳定性很低,很容易在铁锌组成的原电池的作用原理之下具有很短的存在寿命,导致闪镀之后的锌层质量无法得到有效控制,容易出现闪镀锌层消失漏底等镀层不均匀的现象,依然无法改善后续电镀锌层的质量均匀性问题。为此,需要开发出绿色环保且能够与前后体系兼容的中间层来调控钢铁基材表面的不均匀性,是一个比较可靠的中间层设计原则。
技术实现要素:5.本发明的目的就是为了提供一种闪镀锌铁合金镀液及其电镀方法,以克服现有技术中以下缺陷中的至少一种:1)闪镀镍对环境污染大;2)闪镀铁的铁镀层与后续的锌镀层结合力差,镀层易脱落、剥落,同时镀液不稳定,影响电镀效果;3)闪镀锌镀层薄、锌镀层质量无法得到有效控制,镀层不均匀。
6.本发明的目的可以通过以下技术方案来实现:
7.本发明的技术方案之一提供了一种闪镀锌铁合金镀液,该镀液包括以下质量分数的组分:
8.无机锌盐2~15%;
9.无机铁盐0.5~5%;
10.无机电镀添加剂2~8%;
11.络合剂2~5%;
12.其余为溶剂。
13.进一步的,所述无机锌盐包括氯化锌或七水硫酸锌中的一种。
14.进一步的,所述无机铁盐包括氯化亚铁或七水合硫酸亚铁中的一种。
15.进一步的,所述无机电镀添加剂包括硼酸、柠檬酸、硫酸钠或氯化钾中的至少一种。
16.进一步的,所述络合剂包括抗坏血酸、草酸钠或柠檬酸钠中的一种或两种。
17.进一步的,所述溶剂为去离子水。
18.进一步的,所述闪镀锌铁合金镀液的ph值为3~5。
19.本发明的技术方案之二提供了上述闪镀锌铁合金镀液的电镀方法,该电镀处理位于带钢电镀锌机组的前处理与正常电镀区段之间,包括:
20.以可溶性锌板作为阳极,以带钢作为阴极,以上述闪镀锌铁合金镀液作为电沉积液,采用周期换向脉冲法进行电沉积,得到锌铁合金预镀层。
21.进一步的,可溶性锌板在使用前还经过以下预处理:
22.使用砂纸将可溶性锌板的表面磨平,再经洗涤、干燥,即完成预处理。
23.进一步的,带钢在使用前还经过以下预处理:
24.将带钢依次经除油、水洗、酸洗、水洗、活化、水洗多步操作,即完成预处理。
25.进一步的,电沉积时间为5~10s。
26.进一步的,电沉积过程中,正向脉冲电流密度为2.0~8.0a/dm2,正向占空比为60~80%,正向脉冲工作时间为50~100ms,正向周期为40~60ms,反向脉冲电流密度为0.2~0.8a/dm2,反向占空比为60~80%,反向脉冲工作时间为10~20ms,反向周期为1~2ms,且正向脉冲工作时间为反向脉冲工作时间的5~10倍。
27.进一步的,电沉积温度为20~30℃。
28.锌铁合金是一种比较适合兼具钢铁基材和外镀锌层的一种复合镀层,开发一种低成本、镀液稳定的闪镀锌铁镀液及其闪镀工艺可以解决现有钢铁闪镀工艺的不足。
29.本发明闪镀锌铁合金镀液稳定,该镀液经电沉积所得到的闪镀锌铁层(锌铁合金组成:铁含量为31.7wt%-40.3wt%,锌含量为59.7wt%-68.3wt%)均匀致密,耐蚀性好,镀层具有优良的掩盖划痕的能力,有效降低基底表面粗糙度。以通用镀锌配方作为后续镀锌质量的评价体系,经过本发明闪镀锌铁预处理的带钢经电镀锌得到更为光亮、致密、平整、质量优良的镀锌层。
30.本发明在闪镀锌铁过程中,镀液中的锌离子、铁离子传递到作为阴极的带钢表面吸附在带钢表面,通过由整流器提供的阴极电流进行电荷传递反应还原为锌原子、铁原子,并得到闪镀锌铁层。在沉积过程中,通过周期换向参数的设计,可以调节铁离子和锌离子的相对放电速度和改善镀液的分散能力,有利于对缺陷和划痕进行填充。正向沉积的尖端位置的镀层会在反向的过程被优先溶解,进而提高钢铁基材的整体平整性。总之,通过正向电流电镀时,阴极带钢基体上在不断地沉积锌铁合金镀层;当换向通过反向电流电镀时,既可以补充阴极表面消耗掉的部分金属离子,减小浓差极化,而且也可以优先溶解掉表面凸出
的晶粒或毛刺,从而可以细化晶粒,使镀层表面光滑、平整。采用周期换向电镀的过程中,由于正向电流密度和时间远远大于反向电流密度和时间,因为正反电流比大,成核率高,晶核刚形成还来不及生长,又有一批新晶核形成,所以镀层结晶细化,粗糙度较小,从而使镀层具有表面均匀、内应力小、光亮度高和具有优异的表面质量等众多特点,对带钢表面缺陷有明显的遮盖效果。这一操作的结果也获得了铁含量为31.7wt%-40.3wt%、锌含量为59.7wt%-68.3wt%的镀层。该镀层具有良好的衔接基材和后续锌镀层的能力,为下步的电镀锌提供了优良的打底层,有利于后续的电镀锌产品获得优异的表面质量。
31.本发明闪镀锌铁液不仅绿色环保、无污染,而且适用电流密度范围广、主盐离子用量少、无毒无异味、完全水溶,容易得到、成本低。而且经过闪镀锌铁处理的钢铁表面可得到极薄的锌铁镀层,能替代闪镀镍、镀铁或镀锌层为下一步电镀防护锌做好打底工作,用来提高钢铁镀锌层的镀层均匀性和结合力,改善镀锌层的整体外观品质和防护品质。本发明闪镀锌铁镀液和闪镀方法工艺简单,价格便宜,易于实现产业化实施。
32.本发明镀液组分中无机锌盐、无机铁盐为主盐,分别提供锌离子和铁离子。如果主盐的质量浓度过低,则允许电流密度低,沉积速度下降,生产效率低,且镀层光泽差,呈灰暗色;含量过高,则阴极极作用降低,镀层结晶粗糙,低电流区暗区增加。
33.本发明镀液组分无机电镀添加剂硫酸钠、氯化钾能够提高镀液的导电能力,改善镀液性能,促进镀层结晶细致,导电盐的加入能扩大光亮范围。本发明镀液组分无机电镀添加剂中硼酸、柠檬酸作为缓冲剂能稳定镀液的ph值在工艺范围,使镀液相对稳定没有铁和锌的氢氧化物生成,从而保证镀层光亮。
34.本发明镀液组分络合剂是为了与fe
2+
形成配位离子,降低游离亚铁离子浓度,减缓氧化反应速度,避免镀液不稳定而影响镀层质量。
35.本发明电沉积过程中正反向的电流密度的工艺参数直接影响镀层性能的优劣以及镀层的结构和成分:若正向脉冲电流密度过大则阴极沉积速率过快、晶粒粗糙,若正向脉冲电流密度过小则沉积速率过慢难以形成均匀镀层;若反向脉冲电流密度过大或者过小都不利于镀层的平整,在合适的工艺范围内可以溶解掉表面凸出的晶粒或毛刺细化晶粒,同时调整锌铁的溶解速度,在使镀层表面光滑、平整的同时调控镀层中锌铁的含量。
36.本发明电沉积过程中正向占空比为正向通导时间与正向时间的比值,当其它脉冲参数不变时,适当的增大正向占空比会得到均匀、致密、高硬度、高耐蚀性镀层;若正向占空比过大时,会使阴极表面的金属离子过度消耗,在阴极区表面造成浓差极化,使镀层的质量下降、性能降低。
37.与现有技术相比,本发明具有以下优点:
38.(1)本发明闪镀锌铁液绿色环保、无污染,而且适用电流密度范围广;主盐锌离子用量少、无毒无异味、完全水溶,容易得到、成本低,且锌铁镀液稳定性好,能够在较长时间内正常工作,保证了电镀效果;
39.(2)本发明采用周期换向电镀方法进行预镀处理,获得了细致平整的组成为锌含量59.7wt%-68.3wt%、铁含量为31.7wt%-40.3wt%的锌铁合金层,该合金层具有良好的覆盖能力,电镀锌实验证明了该锌铁镀层有效遮盖带钢基体表面的缺陷,使得后续的电镀锌板具有优异的表面质量,可获得表面性能好、光亮均匀、耐蚀性高的电镀锌层,提高了电镀锌层的光亮度和表面外观质量,此外,锌铁合金层与镀锌层结合力强,镀层180
°
折弯无脱
锌。
附图说明
40.图1为对比例1未经闪镀锌铁处理而直接电镀锌的带钢照片;
41.图2为本发明实施例1带钢在经过闪镀锌铁处理后再进行电镀锌得到的表面sem图;
42.图3为本发明实施例2带钢在经过闪镀锌铁处理后再进行电镀锌得到的表面sem图。
具体实施方式
43.下面结合附图和具体实施例对本发明进行详细说明。本实施例以本发明技术方案为前提进行实施,给出了详细的实施方式和具体的操作过程,但本发明的保护范围不限于下述的实施例。
44.以下各实施例中,如无特别说明的原料或处理技术,则表明所采用的均为本领域的常规市售原料产品或常规处理技术。
45.以下各实施例中,所使用的可溶性锌板购自中诺新材,为99.995%高纯锌片状。
46.对比例1:
47.为了体现本发明的优点,在实施例之前,采用常规的恒流电镀方式直接在带钢表面实施镀锌,具体操作步骤如下:
48.1)将纯度大于99.99%的可溶性锌板(中诺新材,99.995%高纯锌片状)进行如下处理后作为阳极板使用:先用粗砂纸进行初步磨平,以除去表面氧化层、污点等,再用蒸馏水洗干净,进行除油后,用蒸馏水冲洗,再用无水乙醇清洗表面,用电吹风吹干待用;
49.2)将带钢经如下处理后作为阴极板使用,将带钢依次经除油
→
水洗
→
酸洗
→
水洗
→
活化
→
水洗等多步操作完成前处理;上述活化步骤为:将带钢浸入5%h2so4溶液中静置3min;
50.3)在镀锌槽液中进行电镀锌,镀锌液中锌离子为90g/l、硫酸5g/l,在常温下电镀,电流密度为10a/dm2,电沉积时间为30s。
51.图1所示照片为带钢直接电镀锌后镀层表面sem照片,图1中显示带钢直接电镀锌后,镀锌层表面存在众多凹坑、起伏不平的缺陷,表明基底表面的缺陷未能被消除,同时肉眼可见不同区域的颜色也存在差异。说明直接电镀锌的操作在获得均匀镀锌层方面存在能力不足的缺陷。
52.实施例1:
53.1)将纯度大于99.99%的可溶性锌板进行如下处理后作为阳极板使用:先用粗砂纸进行初步磨平,以除去表面氧化层、污点等,再用蒸馏水洗干净,进行除油后,用蒸馏水冲洗,再用无水乙醇清洗表面,用电吹风吹干待用;
54.2)将带钢经如下处理后作为阴极板使用,将带钢依次经除油
→
水洗
→
酸洗
→
水洗
→
活化
→
水洗等多步操作完成前处理;
55.上述活化步骤为:将带钢浸入5%h2so4溶液中静置3min,即完成活化过程。
56.3)配制镀液,镀液中各组分及其含量如下:
[0057][0058]
4)将步骤3配制的镀液注入电沉积槽内,以上述步骤1表面处理后的可溶性锌板和步骤2表面处理后的带钢分别作阳极和阴极,阳极和阴极的电极间距为8cm,规格均为80mm
×
50mm
×
0.5mm,采用周期换向电沉积工艺合成锌铁预镀层,周期换向电沉积工艺的参数为:
[0059][0060][0061]
将上述实施例1制备的锌铁合金预镀层进行xps能谱测试,经分析测试得:该锌铁合金镀层中fe的质量百分数在40.3%左右,该合金中锌和铁含量见表1:
[0062]
表1
[0063][0064]
5)将表面沉积上锌铁预镀层的带钢作为阴极,在镀锌槽液中进行电镀锌,镀锌液中锌离子为90g/l、硫酸5g/l,在常温下电镀锌工艺中为电流密度10a/dm2,电沉积时间为30s。
[0065]
将上述实施例1步骤5制备的经过预镀处理的镀锌层以及未经预镀处理的带钢镀锌层表面进行粗糙度测试,其粗糙度结果见表2:
[0066]
表2
[0067][0068]
表2中带钢经过闪镀锌铁预处理后表面粗糙度为0.437μm,相较于未经预处理带钢表面的0.758μm更低;二者经电镀锌处理,测得镀锌层表面粗糙度分别为0.392μm、0.544μm,经过闪镀锌铁预处理的带钢板基底更平整,使得后续电镀锌得到的更为致密平整、质量优良的镀锌层。
[0069]
经上述步骤1~5可以得到光亮、均匀、表面质量优良的电镀锌层。表面镀层光亮、饱满、镀层180
°
折弯无脱锌、72小时盐雾实验表面生锈面积小于1%。
[0070]
图2为带钢在按照上述闪镀锌铁处理后再进行电镀锌得到的表面sem照片。从图2中可以看出:相较于图1中的镀锌层表面有较多凹坑、针孔等缺陷,图2的镀锌层表面则更为平整光滑,缺陷显著减少。综上所述,上述闪镀锌铁处理能够有效消除带钢基底表面的划痕、凹坑等缺陷,使其覆上一层平整致密的预镀层,从而使后续电镀锌层更为致密平整、质量优良。表面镀层光亮、饱满、镀层180
°
折弯无脱锌、72小时盐雾实验表面生锈面积小于1%。
[0071]
实施例2:
[0072]
本实施例与实施例1绝大部分均相同,不同之处在于:
[0073]
周期换向电沉积工艺合成锌铁预镀层过程中,采用周期换向电沉积工艺的参数为:
[0074][0075]
将实施例2制备的锌铁合金预镀层进行xps能谱测试,经分析测试得:该锌铁合金
镀层中fe的质量百分数在31.74%左右,该合金中锌和铁含量见表3:
[0076]
表3
[0077][0078]
5)将表面沉积上锌铁预镀层的带钢作为阴极,在镀锌槽液中进行电镀锌,镀锌液中锌离子为90g/l、硫酸5g/l,在常温下电镀锌工艺中为电流密度10a/dm2,电沉积时间为30s。
[0079]
将上述实施例2步骤5制备的经过预镀处理的镀锌层以及未经预镀处理的带钢镀锌层表面进行粗糙度测试,其粗糙度结果见表4:
[0080]
表4
[0081][0082]
表4中带钢经过闪镀锌铁预处理后表面粗糙度为0.406μm,相较于未经预处理带钢表面的0.721μm更低;二者经电镀锌处理,测得镀锌层表面粗糙度分别为0.351μm、0.504μm,经过闪镀锌铁预处理的带钢板基底更平整,使得后续电镀锌得到的更为致密平整、质量优良的镀锌层。
[0083]
图3为带钢在按照上述闪镀锌铁处理后再进行电镀锌得到的表面sem照片。从图3中可以看出:相比于图1中的镀锌层表面有较多凹坑、针孔等缺陷,图3的镀锌层表面更为平整光滑,缺陷显著减少。综上所述,上述闪镀锌铁处理能够有效消除带钢基底表面的划痕、凹坑等缺陷,使其覆上一层平整致密的预镀层,从而使后续电镀锌层更为致密平整、质量优良。表面镀层光亮、饱满、镀层180
°
折弯无脱锌、72小时盐雾实验表面生锈面积小于1%。
[0084]
实施例3:
[0085]
1)将纯度大于99.99%的可溶性锌板采用实施例1中步骤1的方法进行处理后作为阳极板使用;
[0086]
2)将带钢经采用实施例1中步骤2的方法进行处理后作为阴极板使用;
[0087]
3)配制镀液,所述镀液中各组分及其含量如下:
[0088][0089]
4)将步骤3配制的镀液注入电沉积槽内,以上述步骤1表面处理后的可溶性锌板和
步骤2表面处理后的带钢分别作阳极和阴极,阳极和阴极的电极间距为8cm,规格均为80mm
×
50mm
×
0.5mm,采用周期换向电沉积工艺合成锌铁预镀层,周期换向电沉积工艺的参数为:
[0090][0091]
将上述实施例3制备的锌铁合金预镀层进行xps能谱测试,经分析测试得:该锌铁合金镀层中fe的质量百分数在37.85%左右,该合金中锌和铁含量见表5:
[0092]
表5
[0093][0094]
5)将表面沉积上锌铁预镀层的带钢作为阴极,在镀锌槽液中进行电镀锌,镀锌液中锌离子为90g/l、硫酸5g/l,在常温下电镀锌工艺中为电流密度10a/dm2,电积时间为30s。
[0095]
将上述实施例3步骤5制备的经过预镀处理的镀锌层以及未经预镀处理的带钢镀锌层表面进行粗糙度测试,其粗糙度结果见表6:
[0096]
表6
[0097][0098]
表6中带钢经过闪镀锌铁预处理后表面粗糙度为0.469μm,相较于未经预处理带钢表面的0.773μm更低;二者经电镀锌处理,测得镀锌层表面粗糙度分别为0.411μm、0.549μm,经过闪镀锌铁预处理的带钢板基底更平整,使得后续电镀锌得到的更为致密平整、质量优良的镀锌层。
[0099]
经上述步骤1~5可以得到光亮、均匀、表面质量优良的电镀锌层。表面镀层光亮、饱满、镀层180
°
折弯无脱锌、72小时盐雾实验表面生锈面积小于1%。
[0100]
实施例4:
[0101]
与实施例1相比,绝大部分均相同,除了本实施例中,将七水硫酸锌替换为等量的氯化锌。
[0102]
镀液中各组分及其含量如下:
[0103][0104]
经实施例1步骤1~5可以得到光亮、均匀、表面质量优良的电镀锌层。表面镀层光亮、饱满、镀层180
°
折弯无脱锌、72小时盐雾实验表面生锈面积小于1%。由外观检查、粗糙度测量、盐雾腐蚀试验等测试表明该实例中闪镀锌铁镀液及电镀方法能够有效消除带钢基底表面的划痕、凹坑等缺陷,使其覆上一层平整致密的预镀层,从而使后续电镀锌层更为致密平整、质量优良。
[0105]
实施例5:
[0106]
与实施例1相比,绝大部分均相同,除了本实施例中,将七水硫酸锌替换为等量的氯化锌,七水合硫酸亚铁替换为等量的氯化亚铁。
[0107]
镀液中各组分及其含量如下:
[0108][0109]
经实施例1步骤1~5可以得到光亮、均匀、表面质量优良的电镀锌层。表面镀层光亮、饱满、镀层180
°
折弯无脱锌、72小时盐雾实验表面生锈面积小于1%。由外观检查、粗糙度测量、盐雾腐蚀试验等测试表明该实例中闪镀锌铁镀液及电镀方法能够有效消除带钢基底表面的划痕、凹坑等缺陷,使其覆上一层平整致密的预镀层,从而使后续电镀锌层更为致密平整、质量优良。
[0110]
实施例6:
[0111]
与实施例1相比,绝大部分均相同,除了本实施例中,将氯化钾替换为等量的硫酸钠。
[0112]
配制镀液,镀液中各组分及其含量如下:
[0113][0114]
经实施例1步骤1~5可以得到光亮、均匀、表面质量优良的电镀锌层。表面镀层光亮、饱满、镀层180
°
折弯无脱锌、72小时盐雾实验表面生锈面积小于1%。由外观检查、粗糙度测量、盐雾腐蚀试验等测试表明该实例中闪镀锌铁镀液及电镀方法能够有效消除带钢基底表面的划痕、凹坑等缺陷,使其覆上一层平整致密的预镀层,从而使后续电镀锌层更为致密平整、质量优良。
[0115]
实施例7:
[0116]
与实施例1相比,绝大部分均相同,除了本实施例中,将柠檬酸钠替换为等量的草酸钠。
[0117]
配制镀液,镀液中各组分及其含量如下:
[0118][0119]
经实施例1步骤1~5可以得到光亮、均匀、表面质量优良的电镀锌层。表面镀层光亮、饱满、镀层180
°
折弯无脱锌、72小时盐雾实验表面生锈面积小于1%。由外观检查、粗糙度测量、盐雾腐蚀试验等测试表明该实例中闪镀锌铁镀液及电镀方法能够有效消除带钢基底表面的划痕、凹坑等缺陷,使其覆上一层平整致密的预镀层,从而使后续电镀锌层更为致密平整、质量优良。
[0120]
上述的对实施例的描述是为便于该技术领域的普通技术人员能理解和使用发明。熟悉本领域技术的人员显然可以容易地对这些实施例做出各种修改,并把在此说明的一般原理应用到其他实施例中而不必经过创造性的劳动。因此,本发明不限于上述实施例,本领域技术人员根据本发明的揭示,不脱离本发明范畴所做出的改进和修改都应该在本发明的保护范围之内。