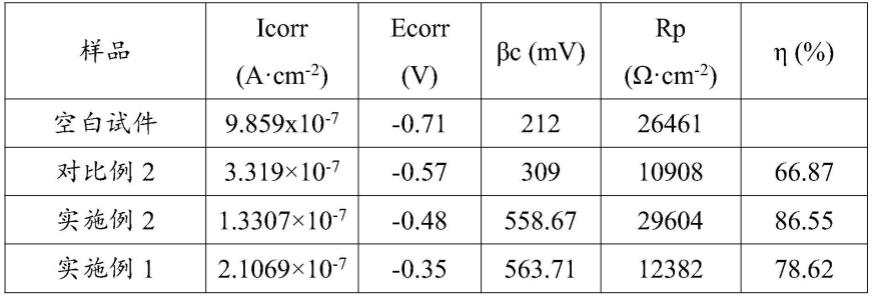
1.本发明属于涂层技术领域,具体涉及一种二合一胶粘型环氧涂层及其制备方法和应用。
背景技术:2.由于环氧树脂涂层具有耐腐蚀性强、耐化学性强和加工性能好等优点,在钢筋上涂覆环氧树脂涂层是一种理想的防腐选择。然而,由于环氧树脂与金属基体之间的结合力弱,而且环氧树脂具有脆性大、易开裂和孔隙率高等缺点,从而限制了环氧树脂涂层的应用。目前,通过提拉浸渍法在钢筋表面制成的硅烷薄膜已被证明可提高钢筋的耐蚀性。虽然传统的提拉浸渍法操作简单,但其制得的硅烷薄膜厚度较小且不均匀,从而导致硅烷涂层的耐腐蚀性降低。
技术实现要素:3.有鉴于此,本发明的目的在于提供一种二合一胶粘型环氧涂层及其制备方法和应用,本发明制备的二合一胶粘型环氧涂层更厚,更均匀,解决了传统提拉浸渍法制得的硅烷膜厚度小不均匀的问题。
4.为了实现上述目的,本发明提供了以下技术方案:
5.本发明提供了一种二合一胶粘型环氧涂层的制备方法,包括以下步骤:
6.将碳钢基材碱洗后,在硅烷溶胶中进行电化学沉积,在碳钢基材表面形成硅烷涂层;
7.将所述表面形成硅烷涂层的碳钢基材浸渍于环氧树脂溶液中,固化后,在碳钢基材表面形成二合一胶粘型环氧涂层。
8.优选的,所述碱洗所用碱溶液包括氢氧化钠溶液。
9.优选的,所述硅烷溶胶的制备方法包括:将3-氨基丙基三乙氧基硅烷、正硅酸乙酯、水和乙醇混合后,调节ph值至4~6,进行水解,得到硅烷溶胶。
10.优选的,所述3-氨基丙基三乙氧基硅烷、正硅酸乙酯、水和乙醇的摩尔比为(1.25~1.75):(1.25~1.75):(1~1.75):1;所述水解的温度为40~50℃;所述水解的时间为4~5h。
11.优选的,所述电化学沉积的方法为恒定电压法;所述电化学沉积的沉积电压为-0.8~-1.0v;所述电化学沉积的时间为500~600s。
12.优选的,所述环氧树脂溶液包括环氧树脂、固化剂和有机溶剂。
13.优选的,所述固化剂包括650聚酰胺树脂;所述有机溶剂为二甲苯和正丁醇的混合溶剂;所述环氧树脂和固化剂的质量比为5:(3~4)。
14.优选的,所述固化的温度为70~80℃;所述固化的时间为48~96h。
15.本发明还提供了上述技术方案所述制备方法制备的二合一胶粘型环氧涂层,包括依次层叠的硅烷层和环氧层。
16.本发明还提供了上述技术方案所述二合一胶粘型环氧涂层在钢筋涂层中的应用。
17.本发明提供了一种二合一胶粘型环氧涂层的制备方法,包括以下步骤:将碳钢基材碱洗后,在硅烷溶胶中进行电化学沉积,在碳钢基材表面形成硅烷涂层;将所述表面形成硅烷涂层的碳钢基材浸渍于环氧树脂溶液中,固化后,在碳钢基材表面形成二合一胶粘型环氧涂层。本发明利用碱催化辅助电沉积法制备得到二合一胶粘型环氧涂层。本发明通过在金属表面施加一个电位,使其周围的ph值增大,生成更多的-oh基,一方面促进硅烷涂层和碳钢表面的连接,另一方面由于其碱性增加,促进了硅烷的缩聚,生成更多的si-o-si,从而使碱催化辅助沉积制备的硅烷涂层较传统的提拉浸渍法制得的硅烷膜的厚度更大、更致密、更均匀,对钢筋的覆盖度更高,解决了传统浸渍法制得的硅烷膜厚度小不均匀的问题。此外,碱催化辅助沉积制备的硅烷涂层可与碳钢表面和环氧涂层通过氢键连接,碱催化沉积增大了硅烷涂层和碳钢表面的连接,所以硅烷涂层可以增加环氧涂层和碳钢表面之间的连接,减少环氧涂层的开裂,增强环氧涂层对碳钢基材(钢筋)的保护作用。本发明将硅烷涂层和环氧涂层有效地结合起来,还解决了环氧涂层易开裂,与碳钢基材(钢筋)结合较弱等问题。
附图说明
18.图1为本发明中覆盖实施例1~3制备的二合一胶粘型环氧涂层、对比例1得到的浸渍法二合一胶粘型环氧涂层和对比例2得到的单一环氧涂层的试件和空白试件的表面接触角;
19.图2为本发明中覆盖实施例1~3制备的二合一胶粘型环氧涂层、对比例1得到的浸渍法二合一胶粘型环氧涂层和对比例2得到的单一环氧涂层的碳钢试件和空白碳钢试件的低频(0.01hz)阻抗值随时间的变化曲线图;
20.图3为本发明中覆盖实施例1~2制备的二合一胶粘型环氧涂层和对比例2制备的单一环氧涂层的碳钢电极和空白碳钢电极在腐蚀溶液中浸泡7d后的动电位极化曲线图;
21.图4为本发明中实施例2制备的二合一胶粘型环氧涂层和对比例2的单一环氧涂层在腐蚀溶液中浸泡5d后的machu试验数据图,其中a为对比例2,b为实施例2。
具体实施方式
22.本发明提供了一种二合一胶粘型环氧涂层的制备方法,包括以下步骤:
23.将碳钢基材碱洗后,在硅烷溶胶中进行电化学沉积,在碳钢基材表面形成硅烷涂层;
24.将所述表面形成硅烷涂层的碳钢基材浸渍于环氧树脂溶液中,固化后,得到在碳钢基材表面形成二合一胶粘型环氧涂层。
25.如无特殊说明,本发明对所用制备原料的来源没有特殊要求,采用本领域技术人员所熟知的市售商品即可。
26.本发明将碳钢基材进行碱洗。
27.本发明对所述碳钢基材没有特殊的限定,本领域熟知的碳钢基材均可;在本发明的实施例中,将所述碳钢基材制成碳钢电极作使用;所述碳钢电极的制备方法优选为将碳钢基材依次进行清洗和干燥后,焊接铜线,并封装在模具内,然后将露出的表面进行抛光,
最后醇洗,得到碳钢电极。在本发明中,所述清洗优选包括依次进行的醇洗和水洗;所述醇洗所用溶剂为乙醇;所述清洗的方式优选为超声清洗;所述醇洗和水洗的时间均优选为60~100s,更优选为60~80s;本发明对所述干燥的过程没有特殊限定,采用本领域数值的干燥过程即可;本发明对所述焊接的过程没有特殊限定,采用本领域熟知的焊接过程即可;所述封装的过程优选为采用环氧树脂和固化剂将焊接铜线后的碳钢样品密封在模具中,使碳钢样品的一个表面露出;所述固化剂优选为二乙烯三胺;所述二乙烯三胺的质量浓度优选为7~10%,更优选为7~8%;所述抛光的过程优选为依次使用400目、800目、1200目和1500目的砂纸进行抛光。
28.在本发明中,所述碱洗的温度优选为常温;所述碱洗的过程优选为将碳钢基材浸泡在碱溶液中;所述碱溶液优选包括氢氧化钠溶液;所述氢氧化钠溶液的质量浓度优选为10~15%,更优选为10~13%;所述碱洗的时间优选为2~4h,更优选为2~3h。
29.本发明通过碱洗增加碳钢表面的-oh基,从而通过碳钢表面的-oh基和硅烷的-oh基缩合成氢键来增强碳钢与硅烷之间的连接。
30.碱洗完成后,本发明优选将所述碱洗后的碳钢基材进行干燥。在本发明中,所述干燥的方式优选为烘干;本发明对所述烘干的过程没有特殊限定,采用本领域熟知的烘干过程即可。
31.本发明将所述碱洗后的碳钢基材在硅烷溶胶中进行电化学沉积,在碳钢基材表面形成硅烷涂层。
32.在本发明中,所述硅烷溶胶的制备方法优选包括将3-氨基丙基三乙氧基硅烷、正硅酸乙酯、水和乙醇混合后,调节ph值至4~6,进行水解,得到硅烷溶胶。
33.在本发明中,所述3-氨基丙基三乙氧基硅烷、正硅酸乙酯、水和乙醇的摩尔比优选为(1.25~1.75):(1.25~1.75):(1~1.75):1,更优选为(1.25~1.5):(1.25~1.5):1:1;所述调节ph值所用的试剂优选为乙酸;所述水解的温度优选为40~50℃,更优选为40~45℃;所述水解的时间优选为4~5h,更优选为4~4.5h;所述水解反应的设备优选为恒温水浴锅;所述水解反应优选在搅拌的条件下进行;所述搅拌的速率优选为1000~1500r/min,更优选为1000~1300r/min。
34.在本发明中,所述电化学沉积的方法为恒定电压法;所述电化学沉积的沉积电压优选为-0.8~-1.0v,更优选为-0.9~-1.0v;所述电化学沉积的时间优选为500~600s,更优选为550~600s;所述电化学沉积的设备优选为电化学工作站;所述电化学沉积优选采用三电极体系进行;所述三电极体系优选为以碳钢基材为工作电极,饱和甘电极为参比电极,铂片为对电极。
35.电化学沉积完成后,本发明优选将所述碳钢基材垂直拉出硅烷溶胶,进行干燥,得到包覆在碳钢基材表面的硅烷涂层。在本发明中,所述干燥包括自然晾干和烘干;所述自然晾干的时间优选为30~50min,更优选为30~40min;所述烘干的设备优选为烘箱;所述烘干的温度优选为70~80℃,更优选为75~80℃;所述烘干的时间优选为2~3h,更优选为2h。
36.得到硅烷涂层后,本发明将所述表面形成硅烷涂层的碳钢基材浸渍于环氧树脂溶液中。
37.在本发明中,所述环氧树脂溶液优选包括环氧树脂、固化剂和有机溶剂。
38.在本发明中,所述固化剂优选包括650聚酰胺树脂;所述有机溶剂优选为二甲苯和
正丁醇的混合溶剂;所述二甲苯和正丁醇的体积比优选为3:(5~7),更优选为3:(6~7);所述环氧树脂和固化剂的质量比优选为5:(3~4),更优选为5:4;所述环氧树脂和有机溶剂的质量比优选为(3~4):5,更优选为1:1.5。
39.在本发明中,所述环氧树脂溶液的制备方法优选包括将环氧树脂和固化剂溶解于有机溶剂中,得到环氧树脂溶液;所述溶解优选在超声的条件下进行;所述超声的时间优选为20~30min,更优选为25~30min;本发明对所述超声功率没有特殊限定,采用本领域熟知的超声功率即可。
40.在本发明中,所述浸渍的时间优选为60~100s,更优选为60~80s。浸渍完成后,本发明优选将所述环氧树脂溶液倾斜去除。
41.浸渍完成后,本发明将所述浸渍后的表面形成硅烷涂层的碳钢基材进行固化,在碳钢基材表面形成二合一胶粘型环氧涂层。
42.在本发明中,所述固化的温度优选为70~80℃,更优选为75~80℃;所述固化的时间优选为48~96h,更优选为48~72h;所述固化的方式优选为加热。
43.本发明还提供了上述技术方案所述制备方法制备的二合一胶粘型环氧涂层,包括依次层叠的硅烷层和环氧层。在本发明中,所述硅烷层的厚度优选为7~10μm,更优选为7~9μm;所述环氧层的厚度优选为10~15μm,更优选为10~14μm。
44.本发明还提供了上述技术方案所述二合一胶粘型环氧涂层在钢筋涂层中的应用。本发明对所述二合一胶粘型环氧涂层在钢筋涂层制备领域中的应用方式没有特殊限定,采用本领域熟知的应用方式即可。
45.下面将结合本发明中的实施例,对本发明中的技术方案进行清楚、完整地描述。
46.实施例1
47.将3-氨基丙基三乙氧基硅烷、正硅酸乙酯、水和乙醇按摩尔比1.25:1.25:1:1混合后,用乙酸调节ph值至4,然后将混合溶液倒入三颈烧瓶中,利用恒温水浴锅在40℃下以1000r/min搅拌5h进行水解,得到硅烷溶胶;
48.将q235碳钢样品(尺寸为10mm
×
10mm
×
10mm)分别用乙醇和去离子水超声清洗60s,并快速干燥以防止腐蚀,然后将碳钢样品和铜线焊接并封装在模具中,用环氧树脂和7%的二乙烯三胺密封,碳钢样品的一个表面露出,然后将露出的表面依次用400、800、1200和1500目的砂纸进行抛光,最后用无水乙醇洗涤,得到碳钢电极;
49.将所述碳钢电极在常温下浸泡在10wt.%的氢氧化钠溶液中浸泡2h,再烘干;然后,将碳钢电极置于硅烷溶胶中,使用电化学工作站,采用三电极体系将硅烷沉积到碳钢表面,以碳钢电极为工作电极,饱和甘电极为参比电极和铂片为对电极,硅烷溶胶作为沉积液,以-1.0v的沉积电压沉积600s,沉积完成后,将碳钢电极垂直缓慢地拉出硅烷溶胶,然后自然晾干30min,最后将碳钢电极置于80℃烘箱内固化2h,在碳钢电极表面制得硅烷涂层;
50.将环氧树脂e-44和650聚酰胺树脂以质量比5:4加到二甲苯和正丁醇的混合溶液中(二甲苯和正丁醇的体积比为3:7,环氧树脂与二甲苯和正丁醇的混合溶液的质量比为1:1.5),然后超声30min直到环氧树脂完全溶解,得到环氧树脂溶液;
51.将表面带有硅烷涂层的碳钢电极浸渍于环氧树脂溶液中60s,然后将环氧树脂溶液缓慢地倾斜去除,再在80℃下加热48h进行固化,在碳钢电极表面制得二合一胶粘型环氧涂层(其中硅烷层的厚度为7~8μm,环氧层的厚度为10~12μm)。
52.实施例2
53.将3-氨基丙基三乙氧基硅烷、正硅酸乙酯、水和乙醇按摩尔比1.5:1.5:1:1混合后,用乙酸调节ph值至4,然后将混合溶液倒入三颈烧瓶中,利用恒温水浴锅在40℃下以1000r/min搅拌5h进行水解,得到硅烷溶胶;
54.将q235碳钢样品(尺寸为10mm
×
10mm
×
10mm)分别用乙醇和去离子水超声清洗60s,并快速干燥以防止腐蚀,然后将碳钢样品和铜线焊接并封装在模具中,用环氧树脂和7%的二乙烯三胺密封,碳钢样品的一个表面露出,然后将露出的表面依次用400、800、1200和1500目的砂纸进行抛光,最后用无水乙醇洗涤,得到碳钢电极;
55.将所述碳钢电极在常温下浸泡在10wt.%的氢氧化钠溶液中浸泡2h,再烘干;然后,将碳钢电极置于硅烷溶胶中,使用电化学工作站,采用三电极体系将硅烷沉积到碳钢表面,以碳钢电极为工作电极,饱和甘电极为参比电极和铂片为对电极,硅烷溶胶作为沉积液,以-1.0v的沉积电压沉积600s,沉积完成后,将碳钢电极垂直缓慢地拉出硅烷溶胶,然后自然晾干30min,最后将碳钢电极置于80℃烘箱内固化2h,在碳钢电极表面制得硅烷涂层;
56.将环氧树脂e-44和650聚酰胺树脂以质量比5:4加到二甲苯和正丁醇的混合溶液中(二甲苯和正丁醇的体积比为3:7,环氧树脂与二甲苯和正丁醇的混合溶液的质量比为1:1.5),然后超声30min直到环氧树脂完全溶解,得到环氧树脂溶液;
57.将表面带有硅烷涂层的碳钢电极浸渍于环氧树脂溶液中60s,然后将环氧树脂溶液缓慢地倾斜去除,再在80℃下加热48h进行固化,在碳钢电极表面制得二合一胶粘型环氧涂层(其中硅烷层的厚度为7~8μm,环氧层的厚度为10~12μm)。
58.实施例3
59.将3-氨基丙基三乙氧基硅烷、正硅酸乙酯、水和乙醇按摩尔比1.75:1.75:1.75:1混合后,用乙酸调节ph值至4,然后将混合溶液倒入三颈烧瓶中,利用恒温水浴锅在40℃下以1000r/min搅拌5h进行水解,得到硅烷溶胶;
60.将q235碳钢样品(尺寸为10mm
×
10mm
×
10mm)分别用乙醇和去离子水超声清洗60s,并快速干燥以防止腐蚀,然后将碳钢样品和铜线焊接并封装在模具中,用环氧树脂和7%的二乙烯三胺密封,碳钢样品的一个表面露出,然后将露出的表面依次用400、800、1200和1500目的砂纸进行抛光,最后用无水乙醇洗涤,得到碳钢电极;
61.将所述碳钢电极在常温下浸泡在10wt.%的氢氧化钠溶液中浸泡2h,再烘干;然后,将碳钢电极置于硅烷溶胶中,使用电化学工作站,采用三电极体系将硅烷沉积到碳钢表面,以碳钢电极为工作电极,饱和甘电极为参比电极和铂片为对电极,硅烷溶胶作为沉积液,以-1.0v的沉积电压沉积600s,沉积完成后,将碳钢电极垂直缓慢地拉出硅烷溶胶,然后自然晾干30min,最后将碳钢电极置于80℃烘箱内固化2h,在碳钢电极表面制得硅烷涂层;
62.将环氧树脂e-44和650聚酰胺树脂以质量比5:4加到二甲苯和正丁醇的混合溶液中(二甲苯和正丁醇的体积比为3:7,环氧树脂与二甲苯和正丁醇的混合溶液的质量比为1:1.5),然后超声30min直到环氧树脂完全溶解,得到环氧树脂溶液;
63.将表面带有硅烷涂层的碳钢电极浸渍于环氧树脂溶液中60s,然后将环氧树脂溶液缓慢地倾斜去除,再在80℃下加热48h进行固化,在碳钢电极表面制得二合一胶粘型环氧涂层(其中硅烷层的厚度为7~8μm,环氧层的厚度为10~12μm)。
64.对比例1
65.将3-氨基丙基三乙氧基硅烷、正硅酸乙酯、水和乙醇按摩尔比1.5:1.5:1:1混合后,用乙酸调节ph值至4,然后将混合溶液倒入三颈烧瓶中,利用恒温水浴锅在40℃下以1000r/min搅拌5h进行水解,得到硅烷溶胶;
66.将q235碳钢样品(尺寸为10mm
×
10mm
×
10mm)分别用乙醇和去离子水超声清洗60s,并快速干燥以防止腐蚀,然后将碳钢样品和铜线焊接并封装在模具中,用环氧树脂和7%的二乙烯三胺密封,碳钢样品的一个表面露出,然后将露出的表面依次用400、800、1200和1500目的砂纸进行抛光,最后用无水乙醇洗涤,得到碳钢电极;
67.将所述碳钢电极在常温下浸泡在10wt.%的氢氧化钠溶液中浸泡2h,再烘干。然后,将碳钢电极浸渍于硅烷溶胶中120s后垂直缓慢地拉出硅烷溶胶。自然晾干30min,最后将碳钢电极置于85℃烘箱内固化2h,在碳钢电极表面制得硅烷涂层;
68.将环氧树脂e-44和650聚酰胺树脂以质量比5:4加到二甲苯和正丁醇的混合溶液中(二甲苯和正丁醇的体积比为3:7,环氧树脂与二甲苯和正丁醇的混合溶液的质量比为1:1.5),然后超声30min直到环氧树脂完全溶解,得到环氧树脂溶液;
69.将表面带有硅烷涂层的碳钢电极浸渍于环氧树脂溶液中60s,然后将环氧树脂溶液缓慢地倾斜去除,再在85℃下加热48h进行固化,在碳钢电极表面制得浸渍法二合一胶粘型环氧涂层(其中硅烷层的厚度为5~7μm,环氧层的厚度为10~12μm)。
70.对比例2
71.将q235碳钢样品(尺寸为10mm
×
10mm
×
10mm)分别用乙醇和去离子水超声清洗60s,并快速干燥以防止腐蚀,然后将碳钢样品和铜线焊接并封装在模具中,用环氧树脂和7%的二乙烯三胺密封,碳钢样品的一个表面露出,然后将露出的表面依次用400、800、1200和1500目的砂纸进行抛光,最后用无水乙醇洗涤,得到碳钢电极;将所述碳钢电极在常温下浸泡在10wt.%的氢氧化钠溶液中浸泡2h,再烘干。
72.将环氧树脂e-44和650聚酰胺树脂以质量比5:4加到二甲苯和正丁醇的混合溶液中(二甲苯和正丁醇的体积比为3:7,环氧树脂与二甲苯和正丁醇的混合溶液的质量比为1:1.5),然后超声30min直到环氧树脂完全溶解,得到环氧树脂溶液;
73.将烘干后的碳钢电极浸渍于环氧树脂溶液中60s,然后将环氧树脂溶液缓慢地倾斜去除,再在85℃下加热48h进行固化,在碳钢电极表面制得单一环氧涂层(环氧层的厚度为10~12μm)。
74.性能测试
75.(1)对覆盖实施例1~3制备的二合一胶粘型环氧涂层、对比例1得到的浸渍法二合一胶粘型环氧涂层和对比例2得到的单一环氧涂层的试件和空白试件进行表面接触角测试,具体测试过程为:使用静态接触角仪测量试件表面与水珠的接触角,结果如图1所示。
76.由图1可知,未经过硅烷表面处理的空白试件的接触角为34.12
°
,通过普通提拉法制成的硅烷薄膜试件接触角为72.83
°
;通过碱催化辅助沉积的硅烷膜的表面接触角显著提升,实施例1为102.02
°
、实施例2、3分别为107.3
°
和82.42
°
,对比例1和2的表面接触角分别为72.83
°
和21.95
°
。说明本发明制备的二合一胶粘型环氧涂层中硅烷涂层对钢筋的疏水性提高作用明显,从而提高了钢筋的耐蚀性。
77.(2)对覆盖实施例1~3制备的二合一胶粘型环氧涂层、对比例1得到的浸渍法二合一胶粘型环氧涂层和对比例2得到的单一环氧涂层的碳钢试件和空白碳钢试件进行电化学
阻抗测试,具体测试过程为:利用电化学工作站和三电极体系,测试浸泡在腐蚀溶液中的碳钢电极的阻抗谱,将低频阻抗值随时间的变化绘制成曲线,结果如图2所示。
78.由图2可知,与未经过硅烷表面处理的空白碳钢试件相比,经过实施例1~3制备的二合一粘胶型环氧涂层覆盖的碳钢的低频阻抗值始终较高,且阻抗值随时间的增加下降较缓,说明本发明提供的硅烷膜有效地提高了混凝土钢筋的防腐性能,抑制了腐蚀溶液对碳钢的侵蚀,从而增强混凝土的耐久性。
79.(3)对覆盖实施例1~2制备的二合一胶粘型环氧涂层和对比例2制备的单一环氧涂层的碳钢电极和空白碳钢电极进行动电位极化测试,具体测试过程为:利用电化学工作站和三电极体系,测试浸泡在腐蚀溶液中的碳钢电极的动电位极化,结果如图3和表1所示。
80.表1各处理碳钢电极的耐腐蚀性能
[0081][0082]
由表1可知,单一环氧涂层和二合一粘胶型环氧涂层的保护效率分别为66.87%和86.55%,这说明了碱催化辅助沉积硅烷膜能有效提高环氧涂层的长期稳定性。空白组裸钢的腐蚀电流密度为9.859
×
10-7
,二合一粘胶型环氧涂层下的碳钢的腐蚀电流密度为1.3307
×
10-7
,这说明二合一粘胶型环氧涂层显著降低了碳钢的腐蚀速度。二合一粘胶型环氧涂层下的碳钢的腐蚀电位也较空白试样和单一环氧涂层下碳钢的腐蚀电位明显上升,说明二合一粘胶型环氧涂层降低了碳钢被腐蚀的可能性。
[0083]
由图3可知,对比例2的单一环氧涂层和二合一粘胶型涂层碳钢(实施例2、实施例1)的保护效率分别为66.87%、86.55%和78.62%。这说明了碱催化辅助沉积硅烷膜能有效提高环氧涂层的长期稳定性。
[0084]
(4)对实施例2制备的二合一胶粘型环氧涂层和对比例2的单一环氧涂层进行machu试验,具体测试过程为:采用machu实验法,将在腐蚀溶液浸泡5d后的涂层用小刀划线,用透明胶带沿划线方向拉下涂层,涂层的剥落面积作为整个涂层粘结性指标(深色区域为涂层覆盖区域,浅色区域为涂层被剥落碳钢裸露的区域),结果如图4所示。
[0085]
由图4可知,环氧涂层a在划痕处有明显得腐蚀产物,且大部分涂层被剥落。表明浸泡后环氧涂层与碳钢基体之间的粘附性差易脱落。而二合一粘胶型环氧涂层b仅有少量腐蚀产物,且只有少部分涂层被剥落,与碳钢的结合力更强。两种涂层的剥落面积直接证明了硅烷涂层的加入可显著增加环氧涂层与碳钢之间的粘结。本发明制备的二合一胶粘型环氧涂层对钢筋的粘结性更强。
[0086]
尽管上述实施例对本发明做出了详尽的描述,但它仅仅是本发明一部分实施例而不是全部实施例,人们还可以根据本实施例在不经创造性前提下获得其他实施例,这些实施例都属于本发明保护范围。