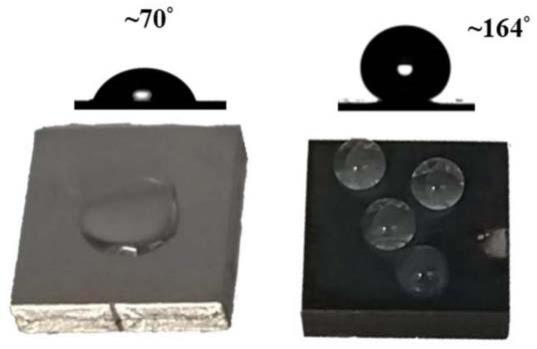
1.本发明涉及金属表面改性领域,特指金属表面一种疏冰涂层的制备方法。
背景技术:2.结冰现象在自然界时有发生,如冬季时电线结冰、飞机机翼结冰、极地环境下的轮船表面发生结冰。在无法改变外界环境,即温度、湿度、压强的情况下,如何减少结冰现象的发生是研究人员需要解决的问题。而金属表面改性作为一种简单、经济的手段,能够有效的降低结冰现象的发生。
3.如中国专利号cn 107245705 b公开的一种“一种tio2复合疏水疏冰涂层及其制备方法”,使得结冰时间延长。但其制备工艺繁琐,制备周期太长,不适宜大面积推广。
技术实现要素:4.本发明目的在于针对上述现有技术中的不足,提供一种金属表面制备疏冰涂层的方法。
5.本发明的目的是通过以下技术方案来实现的:
6.本发明涉及一种金属表面疏冰涂层的制备方法,以铜片为阳极,不锈钢基体作为阴极,置于含铜离子的溶液中,然后接通电源,可在不锈钢基体上获得光亮的铜镀层。接着将含有镀铜层的不锈钢基体作为阴极置于包含镍离子的电镀溶液中,以镍板为阳极,接通电源,使得镍微纳米针锥呈纵横交错状沿着基体纵向生长。最后经过低表面能物质修饰改性即可获得疏冰涂层。所述铜离子由焦磷酸铜提供。所述镍离子由氯化镍提供。
7.该方法具体包括以下步骤:
8.步骤a、将不锈钢基体进行除油除锈;
9.步骤b、将步骤a中处理好的不锈钢基体作为阴极,纯铜片作为阳极,将不锈钢基体置于含铜离子和第一添加剂的电镀溶液中,接通直流电源,形成回路,进行电沉积,在不锈钢基体表面得到光亮铜镀层;
10.步骤c、将步骤b中含有镀铜层的不锈钢基体作为阴极,置于包含镍离子和第二添加剂的电镀溶液中,以镍板作为阳极,接通直流电源,形成回路,进行电沉积,在含有镀铜层的不锈钢基体表面获得镍镀层;
11.步骤d、将步骤c中获得的镍镀层进行低表面能物质修饰改性,得到疏冰涂层。
12.优选的,所述步骤a中,将不锈钢基体表面的油污和氧化膜去除干净。
13.优选的,所述步骤b中,电镀溶液中铜离子由焦磷酸铜提供,第一添加剂包括焦磷酸钾和无水草酸。
14.优选的,所述步骤b中,电镀溶液中铜离子浓度为0.05~3mol/l、焦磷酸钾浓度0.5~2mol/l、无水草酸浓度为0.03~1mol/l。
15.优选的,所述步骤b中,所述电镀溶液温度为10-35℃,ph值为8-9,直流电源采用的电镀电流密度为2-15a/dm2,电沉积时间为0.5~120s。
16.优选的,所述步骤b中,电镀溶液中焦磷酸铜浓度为0.1mol/l、焦磷酸钾浓度为1mol/l、无水草酸浓度为0.4mol/l;电解液温度为25℃,ph值为8.4,电镀采用电流密度为10a/dm2,电沉积时间为60s。
17.优选的,所述步骤c中,电镀溶液中镍离子由氯化镍提供,第二添加剂包括硫酸铵和葡萄糖酸钠。
18.优选的,所述步骤c中,电镀溶液中镍离子浓度为0.02~3mol/l、硫酸铵浓度为0.1~5mol/l、葡萄糖酸钠浓度为0.03~2mol/l;所述电镀溶液温度为10-70℃,ph值为2-5;所述电沉积采用的电流密度0.2-2a/dm2,电沉积时间60~1800s。
19.优选的,所述步骤c中,电镀溶液中氯化镍浓度为0.84mol/l、硫酸铵浓度为0.25mol/l、葡萄糖酸钠浓度为0.15mol/l;所述电解溶液温度为60℃,ph值为4;所述电沉积采用的电流密度1.5a/dm2,电沉积时间900s。
20.优选的,所述步骤d中,所述修饰方法为:将步骤c中获得的镍镀层放入硬脂酸中浸泡0.5-10小时,随后放入马弗炉中在60-150℃温度下保温10-40分钟后,空冷至室温。
21.与现有技术相比,本发明具有如下有益效果:
22.1、电沉积时间较短,且工艺简单,成本较低,效率较高。
23.2、本发明制备的涂层具有较好的超疏水特性。
24.3、本发明制备的涂层能够有效延长结冰时间。
附图说明
25.通过阅读参照以下附图对非限制性实列所作出的详细描述,本发明的其它特征、目的和优点将会变得更明显:
26.图1为金属基体与疏冰涂层静态接触角对比图(左为金属基体,右为疏冰涂层)
27.图2为金属基体与疏冰涂层的覆冰对比图(左为金属基体,右为疏冰涂层)
28.图3为电沉积5min制备的疏冰涂层扫描电镜图;
29.图4为电沉积10min制备的疏冰涂层扫描电镜图;
30.图5为电沉积15min制备的疏冰涂层扫描电镜图;
31.图6为电沉积20min制备的疏冰涂层扫描电镜图;
32.图7为电沉积25min制备的疏冰涂层扫描电镜图。
具体实施方式
33.下面结合附图和具体实例对本发明进行详细说明。以下实施例将有助于本领域的技术人员进一步理解本发明,但不以任何形式限制本发明。应当指出的是,对本领域的普通技术人员来说,在不脱离本发明构思的前提下,还可以做出若干调整和改进。这些都属于本发明的保护范围。
34.实施例1
35.本实施例涉及一种金属表面疏冰涂层的方法,具体步骤如下:
36.步骤a、将不锈钢基体进行除油除锈处理,即将不锈钢表面的油污及氧化膜去除干净。
37.步骤b、用步骤a中处理完毕不锈钢基体作为阴极,纯铜片作为阳极,将不锈钢基体
置于包含铜离子和添加剂的电镀溶液中,接通直流电源,形成回路,进行电沉积得到光亮铜镀层。
38.本实施例步骤b中所用电镀溶液组成为:焦磷酸铜浓度0.1mol/l、焦磷酸钾1mol/l、无水草酸0.4mol/l。所述电解液温度为25℃,ph值为8.4。
39.本实施例步骤b中所述电镀采用电流密度为10a/dm2,电沉积时间为60s。
40.步骤c、将步骤b中含有镀铜层的不锈钢基体作为阴极置于包含镍离子和添加剂的电镀溶液中,以镍板为阳极,接通电源,形成回路,进行电沉积获得镍镀层。
41.本实施例步骤c中所述电镀溶液组成为氯化镍:0.84mol/l、硫酸铵:0.25mol/l、葡萄糖酸钠:0.15mol/l。所述电解液温度为60℃,ph值为4。
42.本实施例步骤c中所述电沉积采用的电流密度1.5a/dm2,电沉积时间300s。
43.步骤d、将步骤c中获得的镍镀层进行低表面能物质硬脂酸进行修饰。
44.本实例步骤d中所述修饰工艺具体为:将步骤c中获得的镍镀层放入0.01mol/l的硬脂酸中浸泡2小时,随后放入马弗炉中130℃保温30分钟,最后空冷至室温,即可获得所需疏冰涂层。
45.结果:得到的样品外观为黑色,样品表面扫描电镜图显示,该微纳结构呈现出细小的钟乳石状。在-18℃冰箱中进行疏冰测试,发现其疏冰性能相比于不锈钢基体提高了74%。
46.实施例2
47.本实施例与实施例1的区别在于,步骤c中所述电沉积时间600s。
48.结果:得到的样品外观为黑色,样品表面扫描电镜图显示,该微纳结构呈现出圆锥状或棱锥状纵横交错。在-18℃冰箱中进行疏冰测试,发现其疏冰性能相比于不锈钢基体提高了76%。
49.实施例3
50.本实施例与实施例1的区别在于,步骤c中所述电沉积时间900s。
51.结果:得到的样品外观为黑色,样品表面扫描电镜图显示,该微纳结构呈现出四棱锥或三棱锥纵横交错。在-18℃冰箱中进行疏冰测试,发现其疏冰性能相比于不锈钢基体提高了80%。
52.实施例4
53.本实施例与实施例1的区别在于,步骤c中所述电沉积时间1200s。
54.结果:得到的样品外观为黑色,样品表面扫描电镜图显示,该微纳结构呈现出棱锥状纵横交错。在-18℃冰箱中进行疏冰测试,发现其疏冰性能相比于不锈钢基体提高了79%。
55.实施例5
56.本实施例与实施例1的区别在于,步骤c中所述电沉积时间1500s。
57.结果:得到的样品外观为黑色,样品表面扫描电镜图显示,该微纳结构呈现出圆锥或棱锥纵横交错。在-18℃冰箱中进行疏冰测试,发现其疏冰性能相比于不锈钢基体提高了78%。
58.综上所述,本发明通过电沉积法在金属表面制备了疏冰涂层,具体的工艺如下:
59.步骤a、将不锈钢基体进行除油除锈处理,即将不锈钢表面的油污及氧化膜去除干
净。
60.步骤b、用步骤a中处理完毕不锈钢基体作为阴极,纯铜片作为阳极,将不锈钢基体置于包含铜离子和添加剂的电镀溶液中,接通直流电源,形成回路,进行电沉积得到光亮铜镀层。步骤b中所用电镀溶液组成为:焦磷酸铜浓度0.1mol/l、焦磷酸钾1mol/l、无水草酸0.4mol/l。所述电解液温度为25℃,ph值为8.4。步骤b中所述电镀采用电流密度为10a/dm2,电沉积时间为60s。
61.步骤c、将步骤b中含有镀铜层的不锈钢基体作为阴极置于包含镍离子和添加剂的电镀溶液中,以镍板为阳极,接通电源,形成回路,进行电沉积获得镍镀层。步骤c中所述电镀溶液组成为氯化镍:0.84mol/l、硫酸铵:0.25mol/l、葡萄糖酸钠:0.15mol/l。所述电解液温度为60℃,ph值为4。步骤c中所述电沉积采用的电流密度1.5a/dm2,电沉积时间900s。
62.步骤d、将步骤c中获得的镍镀层进行低表面能物质硬脂酸进行修饰。步骤d中所述修饰工艺具体为:将步骤c中获得的镍镀层放入0.01mol/l的硬脂酸中浸泡2小时,随后放入马弗炉中130℃保温30分钟,最后空冷至室温,即可获得所需疏冰涂层。
63.相比于金属基体延迟结冰时间最长可增加80%,并且本方法的制备工艺简单,成本较低,效率较高,可以在工业上为金属表面制备疏冰涂层的制备提供一条可行路径。
64.尽管本发明的实施方案已公开如上,但其并不仅仅限于说明书和实施方式中所列运用。它完全可以被适用于各种适合本发明的领域。对于熟悉本领域的人员而言,可容易地实现另外的修改。因此在不背离权利要求及等同范围所限定的一般概念下,本发明并不限于特定的细节和这里示出与描述的图例。