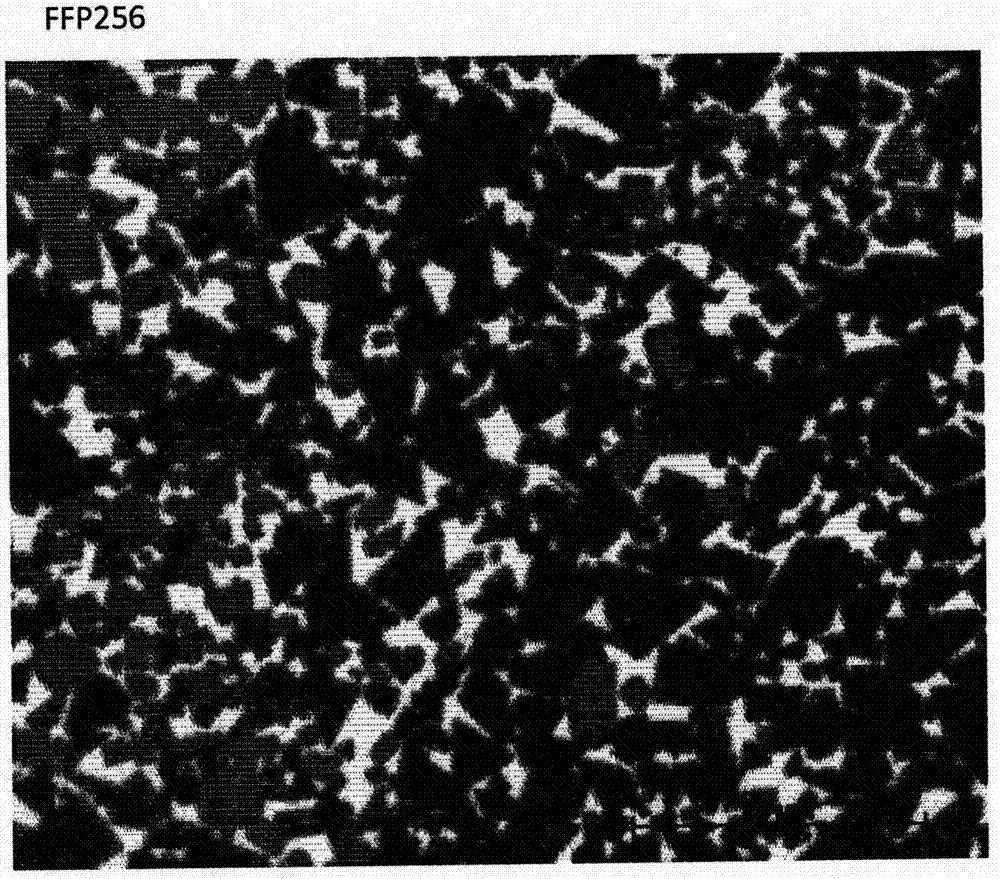
本发明涉及一种岩石钻球齿,包括本体,本体由烧结硬质合金制成,所述烧结硬质合金包括在粘结剂相中的碳化钨(wc)的硬质成分,粘结剂相包括co,其中所述硬质合金包括4-12质量%的co和平衡量(balance)的wc以及不可避免的杂质。
背景技术:
:岩石钻孔是一种
技术领域:
,其中由于钻孔的固有性质,用于在岩石中钻孔的目的的钻球齿(button)经受严峻的腐蚀性条件和重复的冲击两者。不同的钻孔技术将会引起在钻球齿上的不同的冲击载荷。在诸如将岩石钻球齿安装在顶锤(th)装置(top-hammerdevice)或潜孔(dth)钻孔装置(down-the-holedrillingdevice)的岩石钻头本体中的那些的应用中,发现了特别严峻的冲击条件。岩石钻球齿在岩石钻孔期间经受的条件也要求岩石钻球齿具有预定的热导率,以便防止它们达到太高的温度。传统上,岩石钻球齿可以由烧结硬质合金制成的本体构成,该烧结硬质合金包括在粘结剂相中的碳化钨(wc)的硬质成分,粘结剂相包括钴(co)。本发明旨在研究在所述碳化物的压实和烧结之前将铬添加到烧结硬质合金的另外组分的可能性,并且还研究了这样的进一步添加是否将要求对烧结碳化物的任何进一步修改性,以便获得由其制成的功能性岩石钻球齿。在诸如例如于ep1803830中公开的用于金属的切削的切削刀片的
技术领域:
中,已经提出为了在烧结工艺期间减少wc的晶粒生长的目的,在由包括wc和钴的烧结硬质合金制成的切削刀片中包括铬。wc晶粒生长的防止将提高刀片的硬度和强度。然而,具有细晶粒wc的硬质合金不适合用于岩石钻孔,因为它与粗粒硬质合金相比通常太脆,并且具有较低的热导率。冲击式的岩石钻孔要求具有韧性的足够水平的硬质合金。除了使硬质合金晶粒尺寸变小之外,预期铬的添加也会使得粘结剂相变硬,这也降低了总体韧性。技术实现要素:本发明的目的本发明的目的是提出一种岩石钻球齿,在它们具有改善的耐腐蚀性的意义上,这减少了在湿钻孔条件中的磨损,该岩石钻球齿与由wc和co构成的硬质合金制成的现有技术的岩石钻球齿相比得到改进。仍然,硬质合金必须具有可接受的硬度和延展性,以耐受在使用期间其将经受的重复冲击载荷。换言之,它必须不太脆。发明概述本发明的目的借助于岩石钻球齿来实现,该岩石钻球齿包括本体,本体由烧结硬质合金制成,所述烧结硬质合金包括在粘结剂相中的碳化钨(wc)的硬质成分,粘结剂相包括co,其中该硬质合金包括4-12质量%的co和平衡量的wc以及不可避免的杂质,其特征在于,所述硬质合金还以使得cr/co比在0.043-0.19的范围内的量包括cr,且wc晶粒尺寸平均值高于1.75μm。换言之,所述硬质合金由以下构成,4-12质量%的co、使得cr的质量百分比与co的质量百分比之间的关系在0.043-0.19的范围中的量的cr、和平衡量的wc以及不可避免的杂质,其中wc晶粒尺寸平均值高于1.75μm(如用在本文实例部分中所描述的方法所确定的)。根据一个实施例,wc晶粒尺寸高于1.8μm,且根据又一实施例高于2.0μm。优选地,至少岩石钻球齿的主要部分、且优选的是其旨在用于与所操作的岩石接合的活动部分包括硬质合金,该硬质合金具有在上文和/或在下文限定的特征并且对于本发明是必不可少的特征。根据一个实施例,该岩石钻球齿包括全部贯穿其本体的、具有在上文和/或在下文限定的特征的硬质合金。借助于将包含硬质合金元素的粉末碾磨并压实成随后被烧结的压坯(compact)的工艺生产岩石钻球齿。cr的添加导致co-粘结剂相的耐腐蚀性的改善,这减少了在湿钻孔条件下的磨损。cr也使得粘结剂相在钻孔期间倾向于从fcc转变为hcp,这将吸收钻孔操作中产生的一些能量。该转变将由此硬化该粘结剂相并减少钻球齿在其使用期间的磨损。如果cr/co比过低,则所提到的cr的积极效果将会过小。另一方面,如果cr/co比过高,则会形成其中溶解有钴的碳化铬,由此粘结剂相的量减少且硬质合金变得过脆。通过具有高于1.75μm、或高于1.8μm或高于2.0μm的wc晶粒尺寸平均值,实现了硬质合金的足够的热导率和非脆性。如果wc晶粒尺寸过大,则材料变得难以烧结。因此,优选地是,wc晶粒尺寸平均值小于15μm,优选小于10μm。根据优选实施例,cr/co比等于或高于0.075。根据又一优选实施例,cr/co比等于或高于0.085。根据另一优选实施例,cr/co比等于或小于0.15。根据又一优选实施例,cr/co比等于或小于0.12。优选地,在所述硬质合金中的cr的含量等于或高于0.17质量%,优选等于或高于0.4质量%。根据又一实施例,在所述硬质合金中的cr的含量等于或低于2.3质量%,优选等于或低于1.2质量%。形成粘结剂相的钴应适当地能够在1000℃下溶解烧结硬质合金中存在的全部铬。在硬质合金中可以允许至多低于3质量%、优选至多低于2质量%的碳化铬。然而,优选地,cr以溶解在钴中的形式而存在于粘结剂相中。优选地,全部的铬溶解在钴中,且烧结硬质合金基本上没有碳化铬。优选地,为了避免即将出现这样的碳化铬,cr/co比应该足够得低,以保证铬的最大含量不超过在1000℃下铬在钴中的溶解度极限。优选地,烧结硬质合金不含任何石墨,也不含任何η相。为了避免在粘结剂相中碳化铬或石墨的产生,添加的碳的量应该处于足够低的水平。本发明的岩石钻球齿必须不易于因脆性相关问题而失效。因此,根据本发明的岩石钻球齿的硬质合金具有不高于1500hv3的硬度。根据一个实施例,将根据本发明的岩石钻球齿安装在顶锤(th)装置或潜孔(dth)钻孔装置的岩石钻头本体中。本发明还涉及岩石钻孔装置,特别是顶锤装置或潜孔钻孔装置,以及在这样的装置中的根据本发明的岩石钻球齿的用途。根据又另一实施例,在该硬质合金中存在m7c3。在这种情况下,m是cr、co和w的组合,即(cr,co,w)7c3。co溶解度能够达到高达38at%的m7c3碳化物中金属含量。cr:co:w的精确平衡量由硬质合金的总碳含量决定。硬质合金中的比cr/m7c3(cr作为重量%且m7c3作为体积%)适当地等于或高于0.05、或等于或高于0.1、或等于或高于0.2、或等于或高于0.3、或等于或高于0.4。在硬质合金中的比cr/m7c3(cr作为重量%且m7c3作为体积%)适当地等于或小于0.5、或等于或小于0.4。m7c3的含量被定义为体积%,因为这就是该含量是如何被实际测量的。不能令人惊讶地看到由m7c3的存在带来的岩石钻孔中的预期的负面影响。在岩石钻孔中的这样的负面影响曾将是由于附加的碳化物所导致的硬质合金的脆性以及在形成m7c3时由于粘结剂相(co)含量的降低所导致的减小的韧性。因此,由于能够接受m7c3,所以在硬质合金的生产期间碳含量的可接受范围能够更宽。这是很大的生产优势。附图说明将参考附图呈现实例,在附图上:图1a-1c示出了标记为ffp121、ffp256和ffp186的测试样品材料的烧结结构,借助于利用常规硬质合金方法抛光的样品横截面的光学图像,其中利用软布上的1微米金刚石膏进行最终抛光,图2是在测试中使用的岩石钻球齿的几何形状的示意表示,图3是示出标记为ffp122的参考例1和标记为ffp121的发明实例2的在钻孔期间钻头直径变化的图,和图4示出了标记为ffp122的参考例1和标记为ffp121的发明实例2的蠕变曲线(施加应力900mpa,温度1000℃)。具体实施方式实例实例1,参考根据既定的硬质合金工艺,制造具有6.0重量%(wt%)的co和平衡量的wc的材料。将26.1kgwc、1.72kgco和208gw的粉末在球磨机中碾磨总共11.5小时。在碾磨期间,添加16.8gc以达到所需的碳含量。碾磨在湿条件下进行,在30升磨机中,使用乙醇,加上作为有机粘结剂的2重量%聚乙二醇(peg80),和120kgwc-co钢段(cylpebs)。在碾磨后,将浆料在n2气氛中喷雾干燥。通过单轴压制生产生坯,并且通过在55bar氩气压力中、在1410℃下使用烧结-热等静压(sinter-hip)烧结1小时。关于烧结材料的细节在表1中所示。按照fsss测量的wc晶粒尺寸是在碾磨之前的5.6μm。实例2,发明根据既定的硬质合金工艺,制造具有6.0重量%co、0.6重量%cr和平衡量wc的材料。将25.7kgwc、1.72kgco、195gcr3c2和380gw的粉末在球磨机中碾磨总共13.5小时。在碾磨期间,添加28.0gc以达到所需的碳含量。碾磨在湿条件下进行,在30升磨机中,使用乙醇,加上作为有机粘结剂的2重量%聚乙二醇(peg80),和120kgwc-co钢段。在碾磨后,将浆料在n2气氛中喷雾干燥。通过单轴压制生产生坯,并且通过在55bar氩气压力中、在1410℃下使用sinter-hip烧结1小时。在表1中给出了烧结后的组分,标记为ffp121,且烧结结构示出在图1a中。该材料基本上没有碳化铬析出。按照fsss测量的wc晶粒尺寸是在碾磨之前的6.25μm。表1关于根据实例1-3所生产的材料的细节*根据iso/dis28079的palmqvist断裂韧性实例3,发明根据既定的硬质合金工艺,制造具有11.0重量%co、1.1重量%cr和平衡量wc的材料。将37.7kgwc、3.15kgco、358gcr3c2和863gw的粉末在球磨机中碾磨总共9小时。在碾磨期间,添加19.6gc以达到所需的碳含量。碾磨在湿条件下进行,在30升磨机中,使用乙醇,加上作为有机粘结剂的2重量%的聚乙二醇(peg40),和120kgwc-co钢段。在碾磨后,将浆料在n2气氛中喷雾干燥。通过单轴压制生产生坯,并且通过在55bar氩气压力中、在1410℃下使用sinter-hip烧结1小时。在表1中给出了关于烧结材料的细节,且结构示出在图1b中,标记为ffp256。该材料基本上没有碳化铬析出。按照fsss测量的wc晶粒尺寸是在碾磨之前的15.0μm。实例1-3的烧结样品的wc晶粒尺寸由显示烧结材料ffp121、ffp122和ffp256的代表性横截面的sem显微照片来确定这些材料(实例1-3)的wc晶粒尺寸。样品制备的最终步骤是通过利用在软布上1μm的金刚石膏抛光,后面用murakami蚀刻来进行。以背散射电子模式、倍率2000x、高电压15kv、和工作距离~10mm来拍摄sem显微照片。测量图像表面的总面积并且对晶粒的数目手动计数。为了消除由显微照片边框切割的半晶粒的影响,在分析中包括沿两侧的所有晶粒,并且在两个相反侧上的晶粒完全被从分析中排除。通过将总图像面积乘以wc的近似体积分数并且与晶粒的数目相除来计算平均晶粒尺寸。计算等效圆直径(即具有与平均晶粒尺寸等效的面积的圆的直径)。应该注意的是,所报道的晶粒直径对于晶粒的随机二维横截面是有效的,并且不是三维晶粒的真实直径。表2示出了结果。表2样品材料wc晶粒尺寸(等效圆直径)ffp122(根据实例1)1.8μmffp121(根据实例2)2.1μmffp256(根据实例3)2.5μm实例4,超出发明(outsideinvention)根据既定的硬质合金工艺,制造具有11.0重量%co、1.1重量%cr和平衡量wc的材料。将87.8gwc、11.3gco、1.28gcr3c2和0.14gc的粉末在球磨机中碾磨8小时。碾磨在湿条件下进行,使用乙醇,加上作为有机粘结剂的2重量%聚乙二醇(peg40),和800gwc-co钢段。在碾磨之后,浅盘干燥(pandried)浆料,并且通过单轴压制生产坯料,并且通过在55bar氩气压力中、在1410℃下使用sinter-hip烧结1小时。烧结结构示出在图1c中,标记为ffp186。由于过度量的添加的碳,烧结材料具有碳化铬和石墨析出两者,并且由此超出本发明。根据本发明,只要含量小于3重量%、优选小于2重量%,则可能允许碳化铬析出。然而,不允许石墨析出。根据fsss测量的wc晶粒尺寸是在碾磨之前的15.0μm。实例5根据实例1和实例2中的说明,分别压制和烧结钻头刀片(岩石钻球齿)。根据本领域中已知的标准工艺将刀片翻转(tumble),并且此后将其安装在具有3个前部刀片(φ9mm,球形前部)和9个保径刀片(gageinsert)(φ10mm,球形前部)的φ48mm钻头中。通过加热钢钻头并插入碳化物刀片来安装碳化物钻头。在瑞典北部的矿中测试了这些钻头。测试钻机是装备有ac2238或ac3038锤的atlascopco双臂钻车(atlascopcotwinboom)。用根据实例2(本发明,标记为ffp121)的一个钻头和根据实例1(参考,表示为ffp122)的一个参考钻头同时进行钻孔,每个臂上一个。在用每个钻头钻孔大致20-25米(~4-5个钻孔)之后,钻头在左臂和右臂之间切换,以最小化变化的岩石条件的影响,并且用各钻头再钻孔~20-25米。然后,在再次钻孔前,将钻头重新研磨,以重新获得球形前部。钻头钻到由于过小的直径(<45.5mm)而寿命终止为止。钻头直径磨损是碳化物性能的主要量度。在钻孔前后两者(在研磨前)测量钻头直径,测量相对的保径钻球齿(gagebutton)之间的所有三个直径,并将这三个值中的最大值报告为钻头直径。测试结果表明,根据本发明的碳化物比参考材料遭受了更小的磨损,参见表3。ffp121钻头每个钻头钻孔平均576米,而相比较,对于参考ffp122是449钻孔米。在用每个钻头的全部钻孔期间的总直径磨损在图2中示出。应该注意的是,不包括由于研磨损失引起的直径减小。参考材料ffp122每钻孔米磨损0.0055mm,而本发明ffp121每钻孔米仅磨损0.0035mm。上述数字被转化,以获得每mm钻头磨损的钻孔长度;参考材料每毫米钻头磨损已钻出~183钻孔米,并且本发明每毫米钻头磨损已经完成了~286钻孔米。表3所有测试钻头的现场测试结果。*钻头号22因为钻杆断裂而丢失,且因此在计算每钻头平均钻孔米时被排除。图2在钻孔期间钻头直径变化。实例6除了在这个实例中在干袋压机中压制生坯以外,制备了根据标记为ffp122的参考例1和标记为ffp121的发明实例2的测试实心杆。制造杆,以测试参考例1和发明实例2的高温压缩蠕变强度。在测试期间,温度是1000℃,并且应力是900mpa。注意以下结果(见表4):表4对于每种材料测试总共4个试件,两个具有10%变形,并且两个具有20%变形。氩气被用作保护气体。结果示出在图3中。根据本发明的钻头刀片与根据现有技术的钻头刀片相比呈现更好的性能。实例7磨耗测试在磨耗测试中已经对根据实例1和2的岩石钻头刀片(φ10mm,球形前部)进行了测试,其中在转动操作中,样品末端抵靠旋转的花岗岩块(log)对立表面而被磨损。在测试中,施加到每个刀片的载荷是200n,转速是270rpm,并且水平进给速率是0.339mm/转。将在每个测试中的滑动距离固定为230m,并通过水的连续流冷却样品。评估每种材料三个样品,并在测试之前和之后仔细对每个样品称重。从测量的质量损失和样品密度计算样品体积损失,并将样品的体积损失用作磨损的度量。磨耗测试清楚地显示了,与参考材料ffp122相比,根据本发明的材料(ffp121)的显着增加的耐磨性,参见表5中的结果。表5在磨耗测试中测量的样品磨损的结果当前第1页12