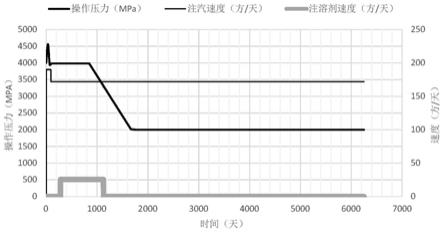
1.本发明涉及稠油水平井注蒸汽开采领域,特别涉及一种蒸汽溶剂混注开采稠油的方法。
背景技术:2.蒸汽辅助重力泄油(sagd)是在油藏底部部署双水平井,从上部水平井连续注蒸汽,下部水平井连续产油。蒸汽在超覆作用下不断向上扩展,遇到冷油藏冷凝,放出潜热,凝结水和受热原油在重力作用下向下部生产井流动,在井下泵抽、气举等举升作用下,油水混合物到达地面,经过破乳油水分离,从而得到超稠油。sagd充分发挥了水平井储层控制能力强、产油速度高的优点,同时结合了重力泄油技术采收率高的优势,是目前开发超稠油的主体技术,在国内外超稠油、油砂的开发中得到了广泛的应用。
3.但由于sagd项目的蒸汽消耗量大,需要燃烧大量天然气产生蒸汽,在高油价时期,投入产出比依然可观。但低油价背景下,部分sagd项目经济效率相对较差的问题逐渐暴露出来,部分油公司纷纷退出了sagd生产经营。同时sagd生产各个环节产生大量温室气体,随着监管逐步趋严,温室气体的排放标准越来越高,技术改进升级势在必行。
4.溶剂与稠油有良好的互溶性,其粘度密度低于稠油,当其溶于稠油时可大幅降低原油粘度,从而加速泄油,减少蒸汽消耗。因此,利用热-溶剂协同降粘的技术思路越来越受到重视。溶剂应用最大的挑战之一是溶剂成本较高,溶剂需要进行分离并循环使用,以降低成本。但溶剂在油藏中存在孔隙表面吸附、溶于油水等过程,导致溶剂的回收率偏低。大部分的溶剂现场试验经验表明,当溶剂的回收率低于90%时,项目盈利能力较弱。溶剂应用的另一个挑战就是投资大,资金回收时间长。因此,提高采油速度、缩短开发周期,也是溶剂技术应用的关键。
技术实现要素:5.为解决以上至少之一的技术问题,本发明提供一种蒸汽溶剂混注开采稠油的方法,能够大幅减少蒸汽用量、提高溶剂回收率。
6.为了实现以上目的,本发明采用以下技术方案:
7.本发明提供一种蒸汽溶剂混注开采稠油的方法,该方法包括以下步骤:
8.s100、进行双水平井井间联通启动;
9.s200、以高压注入蒸汽,加速初期汽腔扩展;
10.s300、当蒸汽腔发育到预定位置时,保持蒸汽的注入速率不变,开始按照一定浓度注入溶剂;产出混合物中的溶剂经粗炼后分离回收;
11.s400、连续注入预定注入量的溶剂后,停止注入溶剂,只注入蒸汽;当汽腔横向扩展30-40米时,开始在恒定降压速率下降压生产;
12.s500、当压力降至比油藏初始压力低0mpa-2mpa时,停止降压,改为低压sagd注采;
13.s600、当瞬时油汽比显著下降时,开始伴注非凝结气,强化溶剂回收。
14.根据本发明的方法,优选地,当双水平井具有相邻井组时,所述方法还包括:
15.s700、当相邻井组开发接近尾声时,从邻近井组注非凝结气驱替,并逐步降低蒸汽腔压力,进一步回收溶剂。
16.如果没有相邻井组,则一直绊注非凝结气,直到经济极限,即注入蒸汽+非凝结气的成本高于产出原油和溶剂的价值时。
17.本发明的蒸汽溶剂混注开采稠油的方法包括以下关键点:
18.1)在开发早期(汽腔还在垂向发育阶段,尚未到顶)开始注溶剂,先高压生产,加速扩腔和泄油;
19.2)在开发中后期降压生产,提高热能利用效率,同时强化溶剂回收;
20.3)溶剂加热后相变,以气相形式进入油藏;在对流作用下到达前缘;冷凝后与原油混合,降低原油粘度;蒸汽溶剂混注,降低蒸汽分压,提高干度,降低沿程管线热损失;
21.4)降压过程中汽腔内部的热水、溶剂发生闪蒸吸热,从而回收部分汽腔内部热能,并运输到泄油前缘;
22.5)降压后溶剂在油水中的溶解度降低,在地层矿物表面的吸附量减少,强化了溶剂的回采。
23.根据本发明的方法,优选地,s200中所述高压比油藏初始压力高1mpa-2mpa。该步骤高压注蒸汽,强化传热,从而加速扩腔。
24.根据本发明的方法,优选地,s300中所述预定位置为距离油层顶界1/3油层厚度。
25.从加速蒸汽腔垂向发育到顶的角度考虑,一般都会采取高压连续注蒸汽。而本发明选择当蒸汽腔发育到1/3油层厚度时开始伴注溶剂,是考虑了溶剂相态特性,在低浓度伴注条件下,溶剂可以帮助提高产油速度,同时维持较高的汽腔垂向扩展速度,从整个开发生命周期来看,这样做可最大程度的节省蒸汽,提高经济效益。
26.根据本发明的方法,优选地,s300中所述按照一定浓度注入溶剂,其中溶剂的浓度为1mol%-5mol%;溶剂注入的温度与蒸汽温度相同,注入压力与操作压力相同。
27.根据本发明的方法,优选地,s400中所述预定注入量为5%-10%原始油层储量。
28.根据本发明的方法,优选地,s400中所述恒定降压速率为0.5kpa/d-10kpa/d。
29.现有技术中的混注方案一般采取等压操作,即维持注入压力,与注蒸汽操作压力相同或者相近,且连续操作中压力维持不变,这是重力泄油技术的基本特征,优点是易对subcool进行控制。而常规注蒸汽sagd方案则采取前期高压注蒸汽,中后期低压注蒸汽的做法,但压力是阶梯状。而本发明要求在汽腔横向扩展30-40米时,开始在恒定降压速率下降压生产,为连续、线性、缓慢下降,既要确保新注入溶剂充分在原油中溶解、混合,又要尽量促进滞留在油藏中的溶剂回采,提高溶剂回收率。
30.本发明在开发早期开始注溶剂,先高压生产加速扩腔和泄油,在开发中后期降压生产,这样操作的好处包括:早期维持高压操作,快速扩腔、泄油,同时降低油藏压力(随着蒸汽腔和油藏动用规模的扩大,油藏压力不断下降);汽腔充分扩展后降压操作,主要是考虑到溶剂回收,降低成本,同时兼顾产油速度的优化。这样做的有益效果是:采油速度提高、蒸汽消耗减少、油汽比上升,同时将溶剂回收率大幅提升,因而经济效益改善。
31.根据本发明的方法,优选地,目标稠油油藏的条件包括:泥质含量低(<15%,含量越低越好),没有天然裂缝、气顶,盖层完整。
32.根据本发明的方法,优选地,所述溶剂包括c6、苯、甲苯、二甲苯、轻质馏分油中的一种或两种以上。
33.所述溶剂类型选择与现有的混注中溶剂选择条件不同,本发明的溶剂类型选择需要满足以下条件:
34.a)与稠油互溶性好,不易造成沥青质析出;
35.b)取决于油藏压力,所选溶剂在操作温度下与水蒸气饱和蒸汽压相近;
36.c)泄油前缘温度下有良好的降黏能力,溶剂质量分率为2%时溶剂与原油混合物黏度低于10mpa
·
s;
37.d)室温下溶剂黏度0.4mpa
·
s-100mpa
·
s,密度0.7-1.2g/ml;
38.e)溶剂可以为单一组分,如烃类、芳香烃化合物,或者为混合物,如轻质馏分油;
39.f)溶剂在注蒸汽条件下为液相或气相。
40.根据本发明的方法,优选地,s600中所述瞬时油汽比低于0.1时,即可认定为显著下降,开始伴注非凝结气。
41.瞬时油汽比一般指某一天的产油量与注蒸汽量的比值。
42.根据本发明的方法,优选地,s600中所述非凝结气的注入比例从前期的1mol%逐渐增加至后期的4mol%,注入压力与注蒸汽压力相同。
43.本发明所提供的蒸汽溶剂混注开采稠油的方法具有以下有益效果:
44.1)由于早期蒸汽腔规模小,注入溶剂虽然量少,但到达前缘的浓度较高,可充分发挥溶剂协同降粘的优势。有利于加速汽腔的发育和泄油,降低蒸汽用量。
45.2)由于前期高压操作,形成了一定规模的蒸汽腔,实现了对油藏的降压。后期转到降压生产时,油藏天然能量被充分应用,弥补了降压降温带来的泄油速度下降。
46.3)随着降压过程的实施,汽腔内部分热水、溶剂闪蒸并流向泄油前缘,回收汽腔内部分热能。同时降压操作强化了溶剂的回收,提高溶剂回收率。
47.4)本发明方案可大幅提高油汽比,节省蒸汽用量,促进溶剂回收,提高经济效率。
附图说明
48.图1为实施例中模拟过程的操作压力曲线图。
49.图2为实施例中模拟过程中416天的温度场图。
50.图3为实施例中模拟过程中1590天的温度场图。
51.图4为实施例中模拟过程中2500天的温度场图。
52.图5为实施例中模拟过程中416天的含油饱和度场图。
53.图6为实施例中模拟过程中1590天的含油饱和度场图。
54.图7为实施例中模拟过程中2500天的含油饱和度场图。
55.图8为实施例中模拟过程中416天的溶剂饱和度场图。
56.图9为实施例中模拟过程中1590天的溶剂饱和度场图。
57.图10为实施例中模拟过程中2500天的溶剂饱和度场图。
58.图11为实施例中模拟过程的开发生产动态图。
59.图12为实施例中模拟过程的采出程度图。
60.图13为实施例中模拟过程的开发生产效果图。
61.图14为实施例中不同开发方式的开发效果对比图。
具体实施方式
62.为了更清楚地说明本发明,下面结合优选实施例对本发明做进一步的说明。本领域技术人员应当理解,下面所具体描述的内容是说明性的而非限制性的,不应以此限制本发明的保护范围。
63.本发明所有数值指定(例如温度、时间、浓度及重量等,包括其中每一者的范围)通常可是适当以0.1或1.0的增量改变(+)或(-)的近似值。所有数值指定均可理解为前面有术语“约”。
64.实施例1
65.本实施例对以下稠油油藏进行蒸汽溶剂混注开采
66.该稠油油藏埋深440米,50℃脱气原油黏度106000mpa
·
s,孔隙度30%,渗透率1.4达西,含油饱和度90%,油藏厚度25m,单井组控制储量25
×
100
×
400
×
0.3
×
0.85=25.5万吨原始油藏储量,
67.该稠油油藏泥质含量1.5%,测井解释未发现天然裂缝、气顶,油藏顶部发育连续厚度大于5米的泥质盖层。满足本发明方法适用的稠油油藏条件。
68.双水平井水平段长400米,井眼直径8.5in,井间距5米,水平生产井位于底部基底岩石上方1米处,井内下入测温、测压点;水平井筛管内下入长短管柱。
69.循环预热阶段注汽压力4mpa,井下蒸汽流量95方/井/天(两井共190方/天),井口蒸汽干度95%,循环3个月后判断联通良好。
70.转半sagd过渡后转至正常sagd生产282天。循环预热阶段短时可高于4mpa,本实施例中短时达到4.65mpa,转至正常sagd后压力为4mpa。
71.然后开始蒸汽溶剂混注,保持蒸汽注入速率,溶剂注入浓度为2mol%,溶剂总注入量为原始油层储量的10%。溶剂注入的温度与蒸汽温度相同,注入压力与操作压力相同(4mpa)。溶剂为c6、苯、甲苯、二甲苯等有机溶剂的一种或多种的混合物(此实施例中选用c6+甲苯)。
72.开发850天后进入降压生产阶段,降压速率为2.4kpa/d,降压生产2年后,稳定在2mpa压力下进行低压生产。
73.对以上过程进行模拟,操作压力曲线如图1所示,前期操作压力4mpa,后按恒定降压速率降压生产,中后期转为2mpa低压生产。整个过程溶剂回收率为97%。相对于纯蒸汽过程,节省蒸汽用量58%。
74.模拟过程中416天(汽腔发育到顶)、1590天(汽腔扩展到边部)、2500天(汽腔下降到油藏厚度的1/2)的温度场如图2-图4所示。
75.场图中有一对黑点位于模型中央,靠近模型底部。其中带箭头的那个点代表注汽水平井,下部的点为生产水平井。场图右侧色标用不同阶颜色指示温度范围(22-250℃)。场图中蓝色为室温22℃,红色部分为4mpa对应的蒸汽温度250℃,橙色为2mpa对应蒸汽温度212℃。
76.282天时,蒸汽腔发育到油藏厚度的2/3处,开始蒸汽溶剂混注。
77.到416天时,蒸汽腔已到达顶部,蒸汽腔下部为蒸汽饱和温度,而顶部的温度略低,
说明溶剂在顶部有一定的富集,导致蒸汽分压下降。蒸汽腔整体形态像一个立着的鸡蛋。
78.到850天时,开始执行恒定降压速度的降压操作。
79.到1126天时,完成溶剂的伴注过程,停止溶剂注入。
80.1590天时,蒸汽腔已扩展到边部。
81.2500天时,汽腔下降到油藏厚度的1/2处。
82.模拟过程中416、1590、2500天的含油饱和度场如图5-图7所示。
83.场图中有一对黑点位于模型中央,靠近模型底部。其中带箭头的那个点代表注汽水平井,下部的点为生产水平井。场图右侧色标用不同阶颜色指示含油饱和度范围(0-1)。场图中红色为原始含油饱和度0.9,绿色部分为残余油饱和度。
84.到416天时,蒸汽腔内部原油采出程度高,含油饱和度较低(由内向外为绿色-红色),饱和度场与温度场有一定的对应关系。
85.1590天时,蒸汽腔已扩展到边部,在靠近泄油前缘的位置出现一个异常的条带(黄色),该条带的含油饱和度相对蒸汽腔内其他区域(绿色)高,为溶剂的富集带。
86.2500天时,汽腔下降到油藏厚度的1/2处,蒸汽腔内部的含油饱和度大幅降低,平均为0.16,上部的含油饱和度最低,为0.04。两侧底角残余油受重力泄油技术特点影响,无法采出。根据油汽比,此时可结束原油采出过程。
87.模拟过程中416、1590、2500天的溶剂在气相中的摩尔浓度场图如图8-图10所示。
88.场图中有一对黑点位于模型中央,靠近模型底部。其中带箭头的那个点代表注汽水平井,下部的点为生产水平井。场图右侧色标用不同阶颜色指示溶剂在气相中的浓度范围(0-1)。场图中蓝色为溶剂未分布区域,浓度为0;溶剂在气相中的摩尔浓度场图清晰展示了溶剂的分布特征。
89.到416天时,蒸汽腔发育到顶,呈鸡蛋形状。汽腔内主要是蒸汽和溶剂,还有少量残余油。溶剂由于其相态特征,在前缘出现富集,形成蛋壳。
90.1590天时,蒸汽腔已扩展到边部,溶剂在汽腔内部的分布较少(场图中的蓝色部分),主要聚集在靠近泄油前缘的位置(绿色)。
91.2500天时,汽腔下降到油藏厚度的1/2处,蒸汽腔内部的溶剂含量非常低,少量残余在汽腔前缘,说明绝大部分的溶剂已经被采出。
92.模拟过程的开发生产动态图如图11所示,采出程度图如图12所示,效果图如图13所示。
93.不同开发方式的开发效果对比图如图14所示。说明:本发明代表降压方案,具体过程及参数为本发明以上实施例;而常规为对比方案,其操作参数与本发明以上实施例完全一致,除了降压操作部分(常规为全程维持4mpa开发)。两种方案在生产约8年(2920天)后,采出程度很接近(说明不管降压与否,累积产油相近),约为70%(一般重力泄油技术的最终采收率);累积油汽比也十分相近(因为累积注汽完全相同,累积产油相近),为0.33;但溶剂采出率差异非常大,本发明为0.97,而常规为0.35,这个差异对开发成本影响非常大(因为溶剂成本相对较高),本发明对比常规混注方案具有非常有利的经济效益。
94.显然,本发明的上述实施例仅仅是为清楚地说明本发明所作的举例,而并非是对本发明的实施方式的限定,对于所属领域的普通技术人员来说,在上述说明的基础上还可以做出其它不同形式的变化或变动,这里无法对所有的实施方式予以穷举,凡是属于本发
明的技术方案所引伸出的显而易见的变化或变动仍处于本发明的保护范围之列。