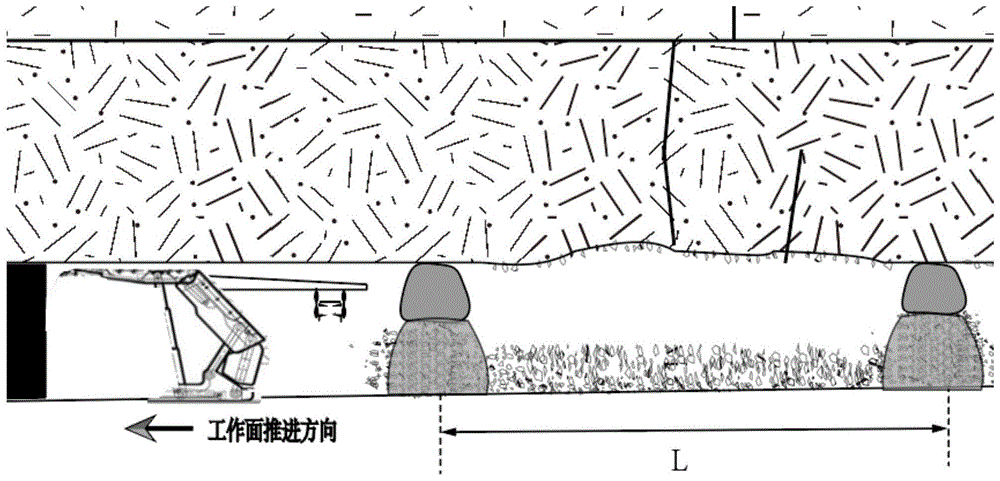
本发明涉及一种间隔式布设矸石充填与囊袋注浆联合支撑减损方法,涉及煤矿开采技术领域。
背景技术:
伴随着近几年煤炭开采向西部地区的转移,导致了西部地区的环境恶化,加剧了西部生态的破坏。特别是西部生态脆弱区,干旱少雨,水资源匮乏,生态环境脆弱,使得大规模开采煤炭资源与生态环境保护的矛盾十分突出。采煤活动引起煤层上覆岩层产生断裂及下沉,导致出现地表沉降、塌陷和开裂等问题,使原有地质条件发生变化,地表生态环境受到破坏,建筑及公路桥梁等基建设施受到损害,地下水流场受到影响,维系地表生态系统的地下水出现渗漏或水位下降,致使生态系统退化,以上问题严重制约着当地煤炭资源开采的可持续发展。
为应对因采煤引起的种种问题,留设保护煤柱开采和充填开采成为该区域最为常见的减损方法。但留设煤柱开采方法一方面造成资源浪费、减少矿井服务年限;另一方面,影响生产布局和煤炭的高效回采。对充填法而言外运建筑材料充填开采的成本投入太高,经济效益性差,诸如此类问题使以上减损方法难以进行大面积推广实施。近年来随着矸石充填液压支架、高速抛干机等相关技术设备的发展,矸石充填技术的实际应用产生了一定的成效。但是,碎胀的矸石经过上部覆岩的压实作用,压实后产生一定的沉降,使得充填效果减弱,地表仍会产生一定的裂缝与变形。因此,进一步探究科学、合理的煤矸石充填减损技术手段成为煤炭资源开采亟待解决的技术难题。
现有技术中,对于传统切顶卸压垮落充填的方法,在顶板垮落后未注浆加固或从地面向下钻孔注浆全断面充填方法,较少有井下间隔式布设囊袋注浆加固形成支护体的方法;其次对于碎胀系数的研究大多在于观测评价,较少有对矸石充填体进行注浆加固方面的探索,并没有针对如何应用碎胀系数研究进行间隔式注浆充填加固的方法;再者对于采空区全断面矸石充填方法产生的二次沉降,并没有采用井下注浆矸石胶结结合囊袋注浆进行间隔式支撑的减损方法。
技术实现要素:
本发明的发明目的在于,针对上述存在的问题,提出一套间隔式布设矸石充填与囊袋注浆联合支撑减损方法,利用采煤作业中产生的大量矸石,采取机械抛射至指定位置堆积,代替原有采空区垮落后全断面注浆充填方法,实现对采空区间隔式布设充填加固的目标;
针对传统矸石未注浆充填的情况,由于上覆岩石的压实作用,采空区会进一步被压实,地面仍会产生部分沉降,因此提出在采空区坚硬顶板处于“悬臂梁”状态时利用破碎矸石进行间隔式充填注浆的加固措施,利用碎胀原理精确计算注浆量,实现间隔式布设注浆充填加固;该方法结合囊袋注浆能有效避免充填的矸石由于压实作用引起的二次沉降问题。同时,该方法一方面充分利用破碎矸石间隔式注浆加固减少了采空区注浆量,不但解决了大量矸石升井和污染问题,又满足了对于充填材料的需求;另一方面,利用囊袋注浆充填解决了矸石胶结的垛桩体与顶板接触问题。最终保证支撑顶板覆岩的稳定性,解决压实沉降问题与顶板覆岩失稳问题。
本发明采用的技术方案如下:
本发明公开了一种间隔式布设矸石充填与囊袋注浆联合支撑减损方法,在采空区顶板未垮落前,采用液压支架后抛矸装置堆填矸石并注浆胶结形成稳固的垛桩体;其解决的具体技术问题包括:(1)针对于顶板较坚硬的薄及中厚煤层采用间隔式垛桩体支撑时须选取合适的间隔距离,利用抛矸装置将矸石向指定位置堆填;(2)对于不同高度的采空区,利用囊袋体积自由膨胀调节充填空间大小,充分填补垛桩体与顶板之间的剩余空间;(3)选取合适的速凝剂控制浆液凝结时间,使注浆囊袋凝固后与矸石胶结垛桩体形成联合支撑体,防止破碎矸石经过上覆岩层压实作用产生沉降,进而控制采空区顶板垮落垮塌引起的地表沉陷及安全问题。
本发明适用于中西部矸石较多的矿区,且顶板较坚硬的薄及中厚煤层,包括以下步骤:
第一步:确定定点矸石充填间距;随着采煤工作面的向前推进,顶板不断裸露并形成悬臂梁状态,按照直接顶初次垮落步距l1计算其间隔式注浆支撑体间距,同时考虑一定的安全储备系数;利用液压支架的短时间支撑效果,在悬臂的顶板未垮落前按照实验室测定的碎胀系数与强度的关系对运输到工作面的矸石进行破碎,以获得岩石最优的碎胀系数;
所述间隔式注浆支撑体间距l=αl1,式中l1-直接顶初次垮落步距,α-安全系数;
所述最优碎胀系数就是破碎后的碎胀体压缩量较小且抗压强度最好的破碎块体所对应的碎胀系数;所述抛矸装置将破碎后的矸石向采空区内预定支撑位置堆砌;
第二步:注浆管道及注浆检测装置设置;通过模拟注浆试验测定最优碎胀系数与胶结强度的变化规律,进行水泥浆性能设计和水泥浆用量计算;将悬臂注浆管伸入至堆砌体上方,利用球面状喷头对矸石堆砌体进行注浆,使之胶结形成稳定的垛桩体,注浆过程中利用水泥浆初凝时间与注浆流量计控制垛桩体注浆情况,防止注浆不足和浆液漫溢,浆液由垛桩体顶端向底部流动过程逐渐凝结,最终达到控制垛桩体注浆效果的目的;
所需水泥浆总注浆量参考水泥浆性能测试国家标准通过前期实验室试验得出所需水泥改性剂配比、凝结时间、水泥浆强度,并根据囊袋极限膨胀体积得到;所述水泥浆改性配比、凝结时间、水泥浆强度通过模拟注浆试验验证后确定,所述囊袋极限膨胀体积按照实际情况挑选尺寸,水泥浆充满囊袋,注浆压力快速升高时,就是极限膨胀尺寸(不发生破损,但注浆量达到最大);
停止注浆依据以下标准判断:(1)当注浆量已达到垛桩体计算注浆量的极限时;(2)注浆初凝时间满足注浆所需初凝条件时;
所述注浆量极限根据岩石碎胀前后的的体积差以及堆积的矸石距采空区覆岩顶板的空间可以大致确定所需注浆的最大值;所述初凝条件根据所选用的速凝剂和实际情况调整;
第三步:对抛入采空区的矸石进行点源注浆;等待胶结堆砌体形成一定强度时,通过悬臂注浆管将注浆囊袋推送至胶结堆砌的垛桩体上部,随后进行注浆作业,利用添加了速凝剂的水泥浆控制其初凝时间,以保证注浆完成后快速形成一定的强度,避免凝结时间过长影响采煤作业进行;
停止注浆按照以下标准判断:(1)当注浆压力急剧增高,可判定注浆囊袋膨胀完全接触顶板时;(2)注浆量已达到囊袋极限膨胀尺寸;所述囊袋囊袋按照实际情况挑选尺寸,水泥浆充满囊袋,注浆压力快速升高时,就是极限膨胀尺寸;
第四步:挂囊袋并注浆充填;当联合支撑体完全凝固并形成一定强度时,收回悬臂注浆管,液压支架连同抛矸装置随采煤方向推进,当推进至下一个间隔距离时重复以上步骤;密切关注间隔式联合支撑减沉效果,必要时,参考井下裂隙带及地表沉降实时监测数据,若发现减损效果不佳,应配合其他减损技术进行补强处理。
本发明的技术效果如下:
目前,防止煤矿上部地层塌陷导致地面生态系统破坏的方法主要以留煤柱和充填开采为主。但是,传统采矿方式中留设煤柱方法与切顶卸压矸石充填方法在允许变形或变形值较低工业建筑的保护方面具有一定的缺陷并且存在失稳的风险。另外,留设煤柱常导致资源浪费。对于采用全断面充填法开采方法,近年来由于充填材料短缺和充填费用的增加,现已较少采用这种方法解决采空区垮落引起的沉陷问题。开采过程中产生的大量煤矸石对于矿区矸石堆放成为制约矿井发展的难题,大量堆放煤矸石,不仅会对采矿作业人员安全产生威胁,而且造成了环境污染。
针对以上问题提出的间隔式布设矸石充填与囊袋注浆联合支撑减损方法。利用开采过程中类似“悬臂梁”结构的顶板的力学特性,在未垮落前,使用破碎装置及抛矸装置将采煤作业产生的矸石进行破碎堆砌,结合碎胀原理及注浆加固技术,在指定位置形成支撑体,而后采用注浆囊袋充分填补沉降空间,避免顶板垮落沉陷。
该方法的优点具体如下:
(1)产能提高。本发明提出的间隔式布设矸石充填与囊袋注浆联合支撑减损方法,在采煤工作进行中即可进行顶板支撑,无需等待顶板垮落或外运支撑材料,节省施工时间,减少由于支撑作业而影响采煤作业的进行,实现采煤和支撑连续进行。
(2)节约成本。本发明提出的利用破碎矸石充填与囊袋间隔式注浆减损方法,利用矸石作为支撑结构的支撑材料,以间隔式布设泵送水泥浆胶结料与矸石破碎体作为支撑材料,整体材料成本较低,且水泥浆便于向巷道内运输施工便利,减少由于大量砌筑材料而产生的开采时间的浪费与占用坑道内矿车降低煤炭输送效率,避免煤炭作为支撑体降低开采产量,煤炭采收率高。
(3)施工便利。本发明采用井下注浆方法,使用注浆囊袋与悬臂注浆管作为施工器械,在采矿作业中应用非常便利,无需增加额外的大型施工机械和复杂器械加工,掌握新工艺新设备所需的培训流程。
(4)绿色环保。本发明提出间隔式布设矸石充填与囊袋注浆联合支撑减损方法避免了地表施工对地表环境的破坏,离层囊袋有效支撑了离层上覆岩层的下沉,导水裂隙带注浆封堵解决了地下水流失的风险,降低地下水污染的风险,减少企业对于达到环保要求治理污染所花费的经济成本,充分体现我国绿色、环保、可持续发展的政策方针。
(5)安全可靠,本发明减损方法可有效控制覆岩不均匀沉降,有效减少覆岩失稳所带来的潜在风险,减少由于充填材料压实影响充填效果产生沉降,使开采区作业时上覆岩层处于稳定状态,并减小覆岩应力地面塌陷巷道坍塌等地质灾害发生的可能性。
附图说明
图1是间隔式布设矸石充填与囊袋注浆联合支撑示意图;
图2是抛矸装置定点抛矸充填示意图;
图3是堆积矸石定点注浆施工示意图;
图4是囊袋注浆施工示意图;
图5球状喷头喷浆效果示意图;
图6是间隔式布设矸石充填与囊袋注浆联合支撑体系技术流程图。
具体实施方式
本说明书中公开的所有特征,或公开的所有方法或过程中的步骤,除了互相排斥的特征和/或步骤以外,均可以以任何方式组合。
本说明书(包括任何附加权利要求、摘要)中公开的任一特征,除非特别叙述,均可被其他等效或具有类似目的的替代特征加以替换。即,除非特别叙述,每个特征只是一系列等效或类似特征中的一个例子而已。
在本发明的描述中,需要理解的是,术语“上”、“下”、“左”、“右”等指示的方位或位置关系为基于附图所示的方位或位置关系,仅是为了便于描述本发明和简化描述,而不是指示或暗示所指的设备或元件必须具有特定的方位、以特定的方位构造和操作,因此不能理解为对本发明的限制。
下面结合附图,对本发明作详细的说明。
本实施例中,如图1-6所示,具体实施步骤为:
第一步,确定定点矸石充填间距;随着采煤工作面的向前推进,顶板不断裸露并形成悬臂梁状态,按照直接顶初次垮落步距l1计算其间隔式注浆支撑体间距,同时考虑一定的安全储备系数(建议参考相关规范取1.25);利用液压支架的短时间支撑效果,在悬臂的顶板未垮落前按照实验室测定的碎胀系数与强度的关系对运输到工作面的矸石进行破碎,以获得岩石最优的碎胀系数;
所述间隔式注浆支撑体间距l=αl1,式中l1-直接顶初次垮落步距,α-安全系数;
所述最优碎胀系数就是破碎后的碎胀体压缩量较小且抗压强度最好的破碎块体所对应的碎胀系数;所述抛矸装置将破碎后的矸石向采空区内预定支撑位置堆砌;
第二步,注浆管道及注浆检测装置设置;通过模拟注浆试验测定最优碎胀系数与胶结强度的变化规律,进行水泥浆性能设计和水泥浆用量计算;将悬臂注浆管伸入至堆砌体上方,利用球面状喷头对矸石堆砌体进行注浆,使之胶结形成稳定的垛桩体,注浆过程中利用水泥浆初凝时间与注浆流量计控制垛桩体注浆情况,防止注浆不足和浆液漫溢,浆液由垛桩体顶端向底部流动过程逐渐凝结,最终达到控制垛桩体注浆效果的目的;
所需水泥浆总注浆量参考水泥浆性能测试国家标准通过前期实验室试验得出所需水泥改性剂配比、凝结时间、水泥浆强度,并根据囊袋极限膨胀体积得到;所述水泥浆改性配比、凝结时间、水泥浆强度通过模拟注浆试验验证后确定,所述囊袋极限膨胀体积按照实际情况挑选尺寸,囊袋注满,注浆压力快速升高时,就是极限膨胀尺寸(不发生破损,但注浆量达到最大);
停止注浆依据以下标准判断:(1)当注浆量已达到垛桩体计算注浆量的极限时;(2)注浆初凝时间满足注浆所需初凝条件时;
所述注浆量极限根据岩石碎胀前后的的体积差以及堆积的矸石距采空区覆岩顶板的空间可以大致确定所需注浆的最大值;所述初凝条件根据所选用的速凝剂和实际情况调整;
第三步,对抛入采空区的矸石进行点源注浆;等待胶结堆砌体形成一定强度时,通过悬臂注浆管将注浆囊袋推送至胶结堆砌的垛桩体上部,随后进行注浆作业,利用添加了速凝剂的水泥浆控制其初凝时间,以保证注浆完成后快速形成一定的强度,避免凝结时间过长影响采煤作业进行;
停止注浆按照以下标准判断:(1)当注浆压力急剧增高,可判定注浆囊袋膨胀完全接触顶板时;(2)注浆量已达到囊袋极限膨胀尺寸;所述囊袋囊袋按照实际情况挑选尺寸,囊袋注满,注浆压力快速升高时,就是极限膨胀尺寸;
第四步,挂囊袋并注浆充填;当联合支撑体完全凝固并形成一定强度时,收回悬臂注浆管,液压支架连同抛矸装置随采煤方向推进,当推进至下一个间隔距离时重复以上步骤;密切关注间隔式联合支撑减沉效果,必要时,参考井下裂隙带及地表沉降实时监测数据,若发现减损效果不佳,应配合其他减损技术进行补强处理。
本实施例中,对采空区进行充填,但不是全部充填,而是局部间隔式充填采空区,达到支撑采空区上覆岩层的目的;
本实施例中,所述碎胀原理就是岩石破碎后体积与原体积发生变化,这种膨胀现象就是碎胀;所述注浆加固技术是破碎后的岩石中间有很大的空隙,注浆后能填补这些空隙,凝结这些碎石,使之成为具有一定强度的加固体。
本实施例中,岩石破碎后形成的堆积体比原来未破碎时提及增大,岩石碎胀前后体积变化的性质就用岩石的碎胀系数描述,本实施例就是利用岩石碎胀体积增大效应进行注浆,达到支撑的目的;此外碎胀系数决定了注浆作业如何进行,同时通过碎胀系数的试验可以得知碎胀体的支撑力(支撑力决定了跨落布局内应当如何布置、如数量、截面积)和竖向压缩量,指导注浆作业所需要的注浆量。
以上所述仅是本发明的优选实施方式,并不用以限制本发明,凡在本发明的精神和原则之内所做的任何修改、等同替换和改进等,均应包含在本发明的保护范围之内。