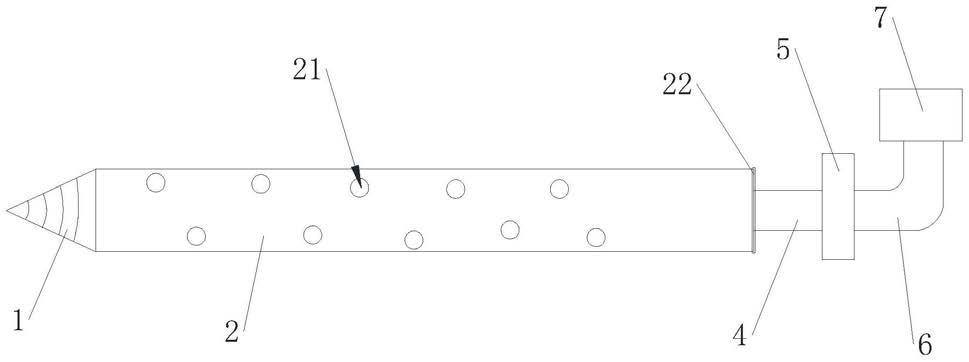
[0001]
本实用新型涉及建筑施工的技术领域,尤其是涉及一种隧道超前注浆小导管。
背景技术:[0002]
超前小导管,是隧道工程掘进施工过程中的一种工艺方法,主要用于自稳时间短的软弱破碎带、浅埋段、洞口偏压段、砂层段、砂卵石段、断层破碎带等地段的预支护。小导管来源于新奥法地下洞室施工,其意图是在围岩软弱地段隧道开挖前沿隧道设计轮廓线外顺轴线方向预先环向施工带有外插角的超前小导管,在小导管内注浆,通过浆液扩散预先将开挖轮廓线附近围岩内部形成一道比较围岩致密的拱形结构,加上小导管自身刚度产生的径向力,使灌浆加固的围岩和小导管共同作用在围堰内部形成一个比较完成的承载体。这个承载体直接承受由于隧道开挖而引起的围岩应力重分布从而保持围岩的稳定,从而大大降低了软弱围岩开挖过程中出现塌方的风险。隧道开挖完成后在及时进行钢架、系统锚杆、挂钢筋网及喷混凝土联合支护施工,确保了隧道在混凝土二次衬砌施工前安全稳定的运行。
[0003]
目前,授权公告号为cn208502792u的专利文件公开了一种超前注浆小导管,包括导管本体,导管本体长度为4.5m-5m,直径为42mm-45mm,壁厚为4mm-6mm,导管本体包括注浆段和止浆段,导管本体底部以上30cm-40cm为止浆段,止浆段未设置注浆孔,止浆段以上为注浆段,注浆段沿导管本体轴线设置有注浆孔,导管本体注浆段的侧壁上设置有若干水泥砂浆溢口。该小导管小导管注浆后对隧道周围围岩形成较好的保护拱,能保障围岩的稳定性,控制施工引起的位移。但是当注浆孔过小或注浆压力不足时,从注浆孔流出的浆液较少,影响注浆效果。
技术实现要素:[0004]
本实用新型的目的是提供一种隧道超前注浆小导管,其通过设置加压组件,使混凝土更容易从注浆孔内流出,注浆效果更好,从而加强了围岩的稳定性。
[0005]
本实用新型的上述发明目的是通过以下技术方案得以实现的:
[0006]
一种隧道超前注浆小导管,包括管头和管身,管头和管身一体设置,所述管身远离管头的一端设置有加压组件,所述加压组件包括顶塞、连接杆、推板和进料管,顶塞位于管身内部,连接杆的一端固定连接在顶塞远离管头的侧壁上,连接杆的长度方向与管身的长度方向平行,连接杆的另一端与推板固定连接,进料管与推板远离连接杆的一端固定连接,推板和顶塞与连接杆连接的侧壁上均开设有通孔,连接杆沿其长度方向上也设置有通孔,通孔贯穿连接杆内部,各个通孔间相互连通,进料管通过通孔与管身连通。
[0007]
优选地,所述管身内设置有螺纹钢,螺纹钢沿管身的长度方向穿设在管身内部,螺纹钢的一端通过顶塞上的通孔伸入连接杆内。
[0008]
优选地,所述进料管设置为l型,进料口设置在进料管的竖直端。
[0009]
优选地,所述进料管的进料口端的外侧壁上设置有螺纹,进料管上螺纹连接有旋
盖,旋盖的外壁上设置有防滑纹。
[0010]
优选地,所述管头设置为锥形,管头的的外侧壁上设置有外螺纹。
[0011]
优选地,所述管身采用直径42mm或50mm、壁厚5mm的热轧无缝钢管,长2-6m,管身中部范围均匀设置梅花形注浆孔,注浆孔的孔径为8mm,孔间距为15cm,管身尾部40-60cm不钻孔,同时在管身尾部采用直径为6mm的钢筋焊接成钢筋加强箍,螺纹钢的直径为20-22mm。
[0012]
优选地,所述顶塞设置为圆柱形,顶塞与管身内壁接触的侧壁上固定设置有防护层,防护层与管身侧壁相抵接,防护层采用橡胶材料。
[0013]
综上所述,本实用新型的有益技术效果为:
[0014]
在管身远离管头的一端设置有加压组件,加压组件包括顶塞、连接杆、推板和进料管,顶塞位于管身内部,连接杆的一端固定连接在顶塞远离管头的侧壁上,连接杆的长度方向与管身的长度方向平行,连接杆的另一端与推板固定连接,进料管与推板远离连接杆的一端固定连接,推板和顶塞与连接杆连接的侧壁上均开设有通孔,连接杆沿其长度方向上也设置有通孔,通孔贯穿连接杆内部,各个通孔间相互连通,进料管通过通孔与管身连通,通过设置加压组件,使混凝土更容易从注浆孔内流出,注浆效果更好,从而加强了围岩的稳定性。
附图说明
[0015]
图1是本实用新型的整体结构示意图;
[0016]
图2是本实用新型的内部结构示意图;
[0017]
图3是图2中a部分的局部放大示意图。
[0018]
图中,1、管头;2、管身;21、注浆孔;22、加强筋;3、顶塞;31、防护层;4、连接杆;5、推板;6、进料管;7、旋盖;8、螺纹钢;9、通孔。
具体实施方式
[0019]
以下结合附图对本实用新型作进一步详细说明。
[0020]
参考图1-图3,为本实用新型公开的一种隧道超前注浆小导管,包括管头1和管身2,管头1和管身2一体设置,管头1长为10cm,管头1设置为锥形,管头1的外侧壁上设置有外螺纹,在将小导管伸入在钻孔内时更加容易。管身2采用直径50mm、壁厚5mm的热轧无缝钢管,管身2长2-6m,管身2中部范围均匀设置梅花形注浆孔21,浆液从注浆孔21内流出。注浆孔21的孔径为8mm,孔间距为15cm,管身2尾部50cm不钻孔,防止注浆过程漏浆。同时在管身2尾部采用直径为6mm的钢筋焊接成钢筋加强箍22,起到搭接前后两排小导管的作用。
[0021]
管身2远离管头1的一端设置有加压组件,加压组件包括顶塞3、连接杆4、推板5和进料管6。顶塞3位于管身2内部,顶塞3设置为圆柱形,顶塞3与管身2内壁接触的侧壁上固定设置有防护层31,防护层31与管身2侧壁相抵接,防护层31采用橡胶材料,通过设置防护层31,使顶塞3的侧壁与管身2内壁贴合更紧密,防止浆液从两者的缝隙中流出,同时保护顶塞3的侧壁与管身2内壁间不受磨损。连接杆4的一端固定连接在顶塞3远离管头1的侧壁上,连接杆4的长度方向与管身2的长度方向平行,连接杆4的另一端与推板5固定连接,进料管6与推板5远离连接杆4的一端固定连接。进料管6设置为l型,进料口设置在进料管6的竖直端。同时,进料管6的进料口端的外侧壁上设置有螺纹,进料管6上螺纹连接有旋盖7,旋盖7的外
壁上设置有防滑纹。通过将进料管6设置为l型,并加设旋盖7,起到防止加压过程中浆液从进料管6的进料口端溢出的作用。推板5和顶塞3与连接杆4连接的侧壁上均开设有通孔9,连接杆4沿其长度方向上也设置有通孔9,通孔9贯穿连接杆4内部,各个通孔9间相互连通,进料管6通过通孔9与管身2连通,通过进料管6的进料口端可以向管身2内注浆。管身2内设置有螺纹钢8,螺纹钢8的直径为20-22mm,螺纹钢8沿管身2的长度方向穿设在管身2内部,起到加强小导管强度的作用。螺纹钢8的一端通过顶塞3上的通孔9伸入连接杆4内,在推动顶塞3时,不会阻碍顶塞3移动。在向管身2内注浆时,拧开旋盖7,将浆液从进料管6的进料口端注入,浆液会顺着进料管6和通孔9依次流过推板5、连接杆4和顶塞3,进而流入管身2内,在注浆一段时间后,拧紧旋盖7,对推板5朝着顶塞3的方向夯实,管身2内的浆液会在顶塞3压力的作用下更容易从注浆孔21内流出,使注浆效果更好。
[0022]
显然,上述实施例仅仅是为清楚地说明本实用新型所作的举例,而并非是对本实用新型的实施方式的限定。对于所属领域的普通技术人员来说,在上述说明的基础上还可以做出其它不同形式的变化或变动。这里无需也无法对所有的实施方式予以穷举。而这些属于本实用新型的精神所引伸出的显而易见的变化或变动仍处于本实用新型的保护范围之中。