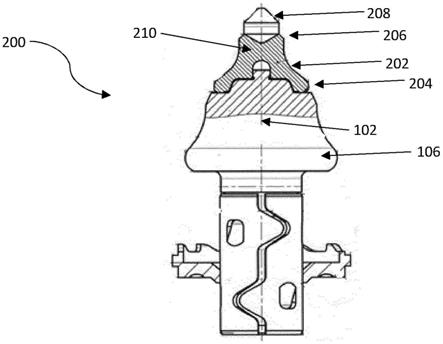
1.本发明涉及一种用于采掘、铣削和掘进的耐磨挖掘工具。特别地但非排他地,挖掘工具可以包括尖端,該尖端包括多晶金刚石(pcd)材料。
背景技术:2.挖掘工具通常用于破碎、钻孔或以其他方式粉碎如岩石、沥青、煤或混凝土等坚硬或磨蚀性主体,并且可以用于如道路修复、采掘、挖沟和施工等应用中。
3.由于挖掘工具的操作环境,挖掘工具可能以多种方式经历极端的磨损和故障,因而必须频繁更换。例如,在道路修复操作中,可以在可旋转滚筒上安装多个挖掘工具,并且可以使得该多个挖掘工具随着滚筒旋转而使道路沥青破碎。例如在采煤中,可以采用类似的方法来使岩层破碎。
4.一些挖掘工具包括工作尖端,该工作尖端包括合成金刚石材料,这种包括合成金刚石材料的工作尖端可能比由烧结碳化钨材料形成的工作尖端更耐磨。然而,合成和天然金刚石材料倾向于比烧结金属碳化物材料更脆且更不抗断裂,并且这倾向于降低其在挖掘操作中潜在的实用性。
5.需要提供一种具有更长工作寿命的挖掘工具。
6.特别地,需要提供具有烧结金属碳化物冲击尖端的挖掘工具,该烧结金属碳化物冲击尖端帮助没有额外成本地保护钢支撑体。
技术实现要素:7.根据本发明,提供了一种挖掘工具,该挖掘工具包括中心轴线、冲击尖端以及支撑体,该冲击尖端的近端在非平面界面处结合至该支撑体,该非平面界面包括同轴且环形的两个界面表面,外界面表面的宽度等于或小于内界面表面的宽度,该冲击尖端在其远端处包括超硬钻头。
8.这种构型提供了大的铜焊表面,这增加了铜焊之后的压缩应力。这引起更高的抗剪强度。
9.当外界面表面的宽度等于或小于内界面表面的宽度时,促使铜焊材料在铜焊过程期间径向地向内流动,这还有助于实现铜焊后更高的抗剪强度。
10.此外,整个挖掘工具的耐磨性显著提高。这避免了尽管碳化物尖端仍具有剩余使用寿命、但挖掘工具因钢支撑体磨损而发生故障的情况。通过这种构型,由于实现了碳化物冲击尖端完整的使用寿命,因而对碳化物冲击尖端的投资得以实现。
11.另外,由于铜焊表面区域较大,因而就制造公差而言,铜焊过程更加灵活。这种布置还产生了更可靠的铜焊过程。
12.最后,由于在对样品进行切片以检查焊接质量之前不需要准备样品,因而更易于对挖掘工具进行质量检查。
13.从属权利要求2至20中提供了本发明优选的和/或可选的特征。
附图说明
14.将参考附图描述挖掘工具的非限制性的示例性布置,在附图中:
15.图1示出了结合现有技术挖掘工具的典型的道路铣削机的下侧;
16.图2示出了现有技术挖掘工具的前透视图;
17.图3示出了图2的现有技术挖掘工具的前透视图,其中示出了冲击尖端与支撑体之间的界面的部分截面;
18.图4示出了在冲击尖端脱落之前(左图)和脱落之后(右图)的已磨损的现有技术挖掘工具的示例;
19.图5示出了本发明的一个实施例中的挖掘工具的前透视图;
20.图6示出了图5的挖掘工具的截面视图;
21.图7示出了图5中方形e部分的放大视图;并且还描画了图2的现有技术挖掘工具的截面轮廓;
22.图8示出了图5的冲击尖端的透视图;
23.图9示出了图5的冲击尖端的底视图;
24.图10示出了图5的冲击尖端的侧视图;
25.图11示出了本发明的另一实施例中的挖掘工具的前透视图;
26.图12示出了图11的挖掘工具的部分截面视图;
27.图13示出了图11的冲击尖端的从上方看的透视图;
28.图14示出了图11的冲击尖端的从下方看的透视图;
29.图15示出了图11的冲击尖端的侧视图;
30.图16示出了图15的冲击尖端的沿着线a
‑
a的截面视图;
31.图17示出了用于图11的挖掘工具中的替代性冲击尖端的截面视图;并且
32.图18示出了另一替代性实施例的冲击尖端的放大视图。
33.在所有附图中,相同附图标记指代大体相同的特征。
具体实施方式
34.图1示出了典型的道路铣削机10的下侧。铣削机可以是沥青或路面刨机,该沥青或路面刨机用于在放置新的路面层之前粉碎路基,比如路面12。多个挖掘工具14被附接至可旋转滚筒16。滚筒16使挖掘工具14与路基12接合。基部固持器18被稳固地附接至滚筒16并且凭借中间工具固持器(未示出)可以偏离旋转方向成角度地固持挖掘工具14,使得挖掘工具14以优选的角度接合路基12。在一些实施例中,挖掘工具14的柄部(未示出)可旋转地放置在工具固持器内,尽管这对于包括超硬冲击尖端的挖掘工具14来说不是必要的。
35.图2和图3示出了现有技术挖掘工具14。挖掘工具14包括钢支撑体22和总体上为钟形的冲击尖端20。支撑体包括主体部分24和从主体部分24中心地延伸的柄部26。冲击尖端20位于在支撑体22的一个端部中设置的圆形凹部27内。这意味着钢支撑体22的边缘始终包围金属碳化物冲击尖端20。被定位在圆形凹部27内的典型地被设置为薄的圆形盘的铜焊材料(未示出)将冲击尖端20稳固地结合至支撑体22。挖掘工具14凭借柄部26和包围柄部26的弹簧套筒28以已知的方式可附接至驱动机构,例如道路铣削机。弹簧套筒28使挖掘工具14与工具固持器之间能够进行相对旋转。
36.在使用中,如图4中所显示,钢支撑体22比碳化物冲击尖端20侵蚀速度更快,特别是在铜焊附近。由于磨损,该区域中钢的体积在使用中逐渐减小。最终,支撑体22不再能足以支撑冲击尖端20,冲击尖端20脱落,从而过早地终止冲击尖端20的使用寿命。
37.现在转向图5至图10,根据本发明的挖掘工具的第一实施例总体上以100指示。挖掘工具100包括中心轴线102、冲击尖端104以及支撑体106。弹簧套筒28对于本发明来说不是必要的并且可以省去。挖掘工具100围绕其中心轴线102对称。如在图6中最佳地看到的,冲击尖端104在非平面界面108处结合至支撑体106。显著地,界面108包括同轴且环形的两个界面表面110、112。
38.支撑体106包括中心突出部或销114,该中心突出部或销114被第一环形结合表面116包围并且径向地向外延伸进入该第一环形结合表面116(见图7)。在该实施例中,中心突出部114是凸台(boss)并且包括圆柱形主体部分114a。然而,可以设想中心突出部114的其他形状和轮廓,比如圆锥形突出部、或截头圆锥形突出部、或半球形突出部。圆柱形主体部分114a的直径优选地为大约5mm,但是可以在3mm至10mm的范围内。圆柱形主体部分114a的高度h1优选地为大约2.5mm,但是可以在1mm至5mm的范围内。中心突出部114可以由弓形凹口118底切。凹口提供了附加的体积,铜焊材料可以流入该附加的体积中,并且该附加的体积帮助有助于扩大铜焊区域。
39.第一环形结合表面116藉由肩部122连接至径向外部第二环形结合表面120。在图7中,肩部122先是弓形的,然后是直线形的。该肩部122被定位在第一环形结合表面116与第二环形结合表面120中间。而如图7中所示,第一环形结合表面116和第二环形结合表面120垂直于中心轴线102布置,肩部122与中心轴线102成锐角θ布置。角θ介于10度与30度之间,并且优选地为约20度。
40.第一环形结合表面116和第二环形结合表面120在轴向上分开、即呈阶梯式(stepped),使得第一环形结合表面116在轴向上位于中心突出部114与第二环形结合表面120中间。第二环形结合表面120可以替代地在轴向上位于中心突出部114与第一环形结合表面116中间,这虽然是可行的,但并不是优选的布置,因为在冲击尖端104中可能需要更多(而不是更少)的碳化物材料。
41.如图8中所示的,冲击尖端104在一个端部处包括中心凹部124,该中心凹部124用于接纳支撑体106的中心突出部114。凹部124的内部构型是部分半球形、部分圆柱形的,但也可以是其他形状。在早期的生产阶段期间,中心突出部114和凹部124的作用是确保冲击尖端104与支撑体106在初步组装中的良好的相对位置。在预烧结阶段,它们还在压制期间协助提高生坯(green body)的密度。然而,它们对于本发明不是必要的,因为它们不直接有助于增加焊接强度,因此,可以将它们省去。无论在冲击尖端中是否包括突出部114和凹部124,重要的是第一环形界面表面110和第二环形界面表面112在轴向上在某种程度上间隔开。
42.冲击尖端104进一步包括第三环形结合表面126,该第三环形结合表面包围中心凹部124并且从该中心凹部124径向地向外延伸。冲击尖端104还包括连接至第三环形结合表面126的径向外部第四环形结合表面128。
43.如在图8和图9中最佳地看到的,多个凹坑129从第四环形结合表面128突出。凹坑129围绕中心纵向轴线102等角度地(equi
‑
angularly)布置。在该实施例中,由于有6个凹
坑,因而相邻的凹坑之间间隔的角度φ为60度。在第四环形结合表面128上可以布置任何数量的凹坑。凹坑有助于在冲击尖端104与支撑体106之间产生大约为0.3mm的小间隙g1。凹坑进一步增大了冲击尖端104的表面区域,铜焊粘结在该表面区域上,从而又使结合的抗剪强度进一步增强。
44.类似于支撑体106,第二所述肩部130连接冲击尖端104的第三环形结合表面126和第四环形结合表面128。
45.在该实施例中,第一肩部122和第二肩部130是平面的。然而,它们不必一定是平面的。重要的是第一环形界面表面110与第二环形界面表面112之间的结构链接延伸了冲击尖端104与支撑体106之间的界面的长度,但如何实现不一定重要。例如,结构链接可以简单地是在环形界面表面110、112之一上的倒角、或替代性地是圆角。
46.冲击尖端104的第三环形结合表面126与支撑体106的第一环形结合表面116面向彼此,但是除了可选的一些凹坑129之外,它们彼此不邻接。另外,冲击尖端104的第四环形结合表面128与支撑体106的第二环形结合表面120面向彼此,但是除了一些凹坑129之外,它们彼此不邻接。冲击尖端104和支撑体106由在第一肩部122与第二肩部130处测量到的大约0.2mm的间隙g2分开。间隙g2为铜焊材料(未示出)提供空间,使铜焊材料位于冲击尖端104与支撑体106之间。类似地,间隙g3也为附加的铜焊材料(未示出)提供空间,使铜焊材料位于冲击尖端104与支撑体106之间。对于组装,铜焊作为环或环形物提供,从而对于本发明需要间隙g1和间隙g3的两个环。然而,铜焊一旦被加热就熔化并且流动。铜焊从g1处的铜焊外环沿间隙g2朝向g3处的铜焊内环芯吸(wick up),以进一步增加铜焊结合的长度。这显著地增加了结合的强度。可行地,可以设置两个以上的环形界面表面。
47.冲击尖端104包括保护裙部132。在该实施例中,裙部132包绕中心凹部124、第三环形结合表面126以及第二肩部130。当被结合至支撑体106时,裙部132还包绕突出部114、第一环形结合表面116以及第一肩部122。裙部132在第二环形结合表面120和第四环形结合表面128交会处周向地终止、与支撑体106大致对齐。裙部132的直径(见图10)为至少25mm。优选地,直径在25mm与40mm之间,包括两个端值。这种总体布置是重要的,因为这意味着冲击尖端104中相同体积的碳化物材料为钢支撑体106提供更大的保护。一定体积的碳化物材料被简单地重新分配至最需要该材料的地方,无额外成本。值得注意地,当直径处于范围的上限时,冲击尖端104在支撑体106上径向地向外突出,从而对挖掘工具100提供更多的防磨损的侧保护。
48.在该实施例中,同轴且环形的两个界面表面110、112具有径向上测量的不同宽度。然而,可以设想界面表面110、112可以替代性地具有相同的宽度。优选的是,径向环形外界面表面112的宽度比径向环形内界面表面110的宽度更小,这促使铜焊材料径向地向内流动,从而促进改善的接合强度。径向环形内界面表面110的外径为大约15mm,宽度为大约5mm。径向环形外界面表面112的外径为大约25mm,宽度在3mm与7mm之间。径向环形外界面表面112的内径在17mm与22mm(例如25mm
‑
3mm=22mm)之间。
49.为清楚起见,径向环形内界面表面110包括第一环形结合表面116和第三环形结合表面126。径向环形外界面表面112包括第二环形结合表面120和第四环形结合表面128。
50.在与中心凹部124相对的端部处,冲击尖端104具有工作表面134,该工作表面134
具有圆形的几何形状,其可以是圆锥形、半球形、圆顶形、截头形或其组合。在本发明的范围内可以设想其他形式的尖端,比如在侧向截面中是六边形、四边形和八边形的尖端。
51.如在图10中最佳地看到的,整个冲击尖端104总体上为钟形。工作表面134延伸进入冲击尖端104的圆柱形第一主体表面136并且与该第一主体表面136共线(co
‑
linear)。第一主体表面136进而延伸进入冲击尖端104的弯曲的第二主体表面138并且与该第二主体表面138共线。第一主体表面136和第二主体表面138两者是连续且未中断的,在其中没有凹陷的任何外部凹槽。类似地,支撑体106也不具有任何种类的外部凹槽。
52.在该实施例中,冲击尖端104由烧结金属碳化物材料构成。在一些实施例中,支撑体106包括烧结金属碳化物材料,该烧结金属碳化物材料的断裂韧度至多约17mpa.m
1/2
、至多约13mpa.m
1/2
、至多约11mpa.m
1/2
或甚至至多约10mpa.m
1/2
。在一些实施例中,支撑体106包括烧结金属碳化物材料,该烧结金属碳化物材料的断裂韧度至少约8mpa.m
1/2
或至少约9mpa.m
1/2
。在一些实施例中,支撑体106包括烧结金属碳化物材料,该烧结金属碳化物材料的横向抗裂强度至少约2,100mpa、至少约2,300mpa、至少约2,700mpa或甚至至少约3,000mpa。
53.在一些实施例中,支撑体106包括烧结碳化物材料,该烧结碳化物材料包括具有平均尺寸至多8微米或至多3微米的金属碳化物颗粒。在一个实施例中,支撑体106包括烧结碳化物材料,该烧结碳化物材料包括具有平均尺寸至少0.1微米的金属碳化物颗粒。
54.在一些实施例中,支撑体106包括烧结金属碳化物材料,该烧结金属碳化物材料包括至多13重量百分比、至多约10重量百分比、至多7重量百分比、至多约6重量百分比或甚至至多3重量百分比的金属粘合剂材料、比如钴(co)。在一些实施例中,支撑体106包括烧结金属碳化物材料,该烧结金属碳化物材料包括至少1重量百分比、至少3重量百分比或至少6重量百分比的金属粘合剂。
55.现在转向图11至图18,示出了根据本发明的挖掘工具和/或冲击尖端的替代性实施例。所有这些实施例的共同之处在于它们包括超硬钻头,如在下文解释的。使用相同的附图标记来表示与参考第一实施例描述的特征相似的特征,并且为简洁起见,省略了另一个描述。
56.图11至图16的总体上以200指示的挖掘工具包括中心轴线102、冲击尖端202以及支撑体106。与第一实施例相同,挖掘工具200围绕其中心轴线102对称。冲击尖端202如第一实施例一样总体上为钟形并且以大约为100度的角β(例如,见图15)径向地向外扩张。冲击尖端202具有最接近支撑体106的近端204和相反的远端206。冲击尖端202在近端204处的构型与第一实施例相同。冲击尖端202在远端206处的构型显著地不同并且在下文中描述。
57.如图12中所示,冲击尖端202包括结合至主体部分210的超硬钻头208。主体部分210的直径(例如,见图15)优选地大约为12mm。超硬钻头208与主体部分210之间的结合由常规铜焊材料提供。
58.如在图17中最佳地看到的,超硬钻头208包括超硬体积212和基底214。超硬体积212被烧结结合至基底214的远端。超硬体积212包括多晶金刚石(pcd)材料,但替代性地可以包括多晶cbn(pcbn)材料。超硬体积的工作表面可以以已知的方式是尖形的、圆形的或截头形的。因此,超硬体积总体上可以是半球形或圆锥形或棱锥形或类似的。在申请人自己的ep 2795062 b1、gb 2490795 a、wo 2014/0491432 a2和wo 2018/162442 a1中给出了超硬
体积的示例。
59.超硬钻头的整体形状可以为总体上圆形、总体上矩形、总体上棱锥形、总体上圆锥形、总体上不对称形或它们的组合。
60.基底214通常是圆柱形的并且典型地包括烧结金属碳化物。该烧结金属碳化物的材料可以是与第一实施例中的冲击尖端的材料相同。超硬体积212与基底214之间的界面可以是平面的或非平面的。
61.基底214包括一体的基部216。在图11至图16中,基部216具有圆锥形构型,该圆锥形构型在远离基底214的界面的方向上径向地向内渐缩,并且在弯曲的顶体(apex)以恒定的半径终止。圆锥体的最大高度h1大约为2.3mm。基部216还包括烧结金属碳化物。
62.在图17中,基部216具有截头圆锥形构型,该截头圆锥形构型在远离基底214的界面的方向上径向地向内渐缩,并且邻接平面的端面。
63.在两个实施例中,冲击尖端202的远端206被对应成形,以接纳超硬钻头208的基部216。冲击尖端202包括用于接纳超硬钻头208的凹部218。显著少于50%的体积的超硬钻头208被接纳在冲击尖端202中。取决于实施例,凹部218的构型是倒(截头形)圆锥体。
64.这种配合布置的目的是要增加超硬钻头208与主体部分210之间的铜焊结合的长度,因而提高整个冲击尖端202的抗剪强度。在凹部218的底部为铜焊材料提供了0.1mm的非常小的间隙g4。如图16中所示的圆锥体的角α典型地大约为120度。圆锥体的最大内部直径(即在基部处)大约为9.4mm。圆锥体的最大高度h2大约为2.4mm。
65.冲击尖端202的弓形侧壁201在远端206处倒角,从而在凹部18的外围边缘、即直径的测量位置终止。侧壁201的倒角部分203的深度h2大约为1.3mm。
66.在挖掘工具200的又另一个实施例中,冲击尖端202与超硬钻头208之间的界面是平面的而不是总体上圆锥形的。图18中示出了对应的冲击尖端202a。冲击尖端202的远端206具有平坦的圆形端面220。冲击尖端202的所有其他特征与先前所描述的特征保持相同。
67.两个环形界面表面110、112提供了改善的焊接强度,保护裙部132为支撑工具106提供了改善的保护,两者结合在一起使挖掘工具100在使用中具有极其优异的性能。值得注意地,冲击工具100的使用工作寿命(其可以根据时间、切割或刨削的长度、操作的次数等来测量)被延长。当还包括中心突出部114和凹部134的布置时,通过碳化物材料的重新分配和很少的额外成本可以实现这种优异的性能。
68.将简单地解释本文中所使用的某些概念和术语。
69.如本文所使用的,挖掘工具用于对主体(例如地质层、岩石、路面、建筑结构)、或其他主体(作为非限制性示例,包括或包含岩石、煤、钾(potash)或其他地质材料、或混凝土、或沥青)进行机械粉碎(或破碎)。如本文所使用的,对主体进行粉碎或破碎可以包括碎裂、切割、铣削、刨削或从主体上移除材料片。挖掘工具可以联接至驱动装置以驱动该挖掘器(pick)针对要粉碎的主体,其中,挖掘工具中包括的冲击尖端被驱动以撞击主体。在一些示例中,驱动装置可以包括可旋转滚筒,多个挖掘工具联接至该可旋转滚筒。一些挖掘工具可以用于采掘操作或用于地下钻孔;例如,挖掘工具可以用来采煤或钾、或用来在油气抽取操作中钻入地下。一些挖掘器可以用于铣削道路表面、例如包括沥青或混凝土的道路表面。
70.合成和天然金刚石、多晶金刚石(pcd)材料、立方氮化硼(cbn)以及多晶cbn(pcbn)材料是超硬材料的示例。如本文所使用的,pcbn材料包括立方氮化硼(cbn)颗粒,这些颗粒
分散在包括金属或陶瓷材料或主要由金属或陶瓷材料构成的基材内。如本文所使用的,多晶金刚石(pcd)材料包括多个金刚石颗粒的聚合体,其大部分直接彼此相互键合,并且其中,金刚石的含量至少约为pcd材料的80体积%。金刚石颗粒之间的间隙可以至少部分地以填充材料填充、或者这些空隙基本上可以是空的,该填充材料可以包括用于合成金刚石的催化剂材料。如本文所使用的,用于合成金刚石的催化剂材料能够在合成或天然金刚石处于热力学稳定的温度和压力下促进合成金刚石颗粒的生长和/或促进合成或天然金刚石颗粒的直接交互生长。用于金刚石的催化剂材料的示例是铁(fe)、镍(ni)、钴(co)和锰(mn)、以及包括这些材料的某些合金。超硬材料的其他示例可以包括某些复合材料,这些复合材料包括由包括陶瓷材料(比如碳化硅(sic))、或烧结碳化物材料(比如钴键合wc材料)的基材保持在一起的金刚石颗粒或cbn颗粒。例如,某些sic键合金刚石材料可以包括分散在sic基材(该基材可以包含少量非sic形式的硅(si))中的至少约30体积%的金刚石颗粒。
71.如本文所使用的,经烧结的多晶超硬材料是在通过烧结形成的同一过程中被结合至基底时
‘
烧结结合’的多晶超硬材料。多晶超硬材料(比如pcd或pcbn)可以分别通过在至少约2gpa、至少约4gpa或至少约5.5gpa的超高压、以及至少约1,000℃或至少约1,200℃的高温下烧结包括金刚石颗粒或cbn颗粒的原材料而形成。原材料(该原材料还可以包括非超硬相或材料)可以在与基底的表面接触的情况下被烧结,使得经烧结的多晶材料在烧结过程期间被烧结结合至基底。烧结过程可以包括使从基底熔化的烧结材料渗入到超硬颗粒的前聚合体内的该多个超硬颗粒中。来自基底的粘合或烧结材料在经烧结的超硬体积内可以是明显的,和/或包括来自基底的材料的相或化合物可以存在于邻近结合边界的超硬体积内,和/或包括来自超硬体积的材料的相或化合物可以存在于邻近结合边界的基底的体积中。例如,基底可以包括钴烧结的碳化钨,并且包括钨(w)和/或钴(co)的相或化合物可以存在于超硬体积中;和/或超硬材料可以包括金刚石,并且存在高碳(c)含量的相或化合物可以存在于基底中;和/或超硬材料可以包括cbn,并且包括硼(b)和/或氮(n)的相或化合物可以存在于基底中。在一些示例中,从基底侵入超硬体积的co(所谓的
‘
羽状物’)可以存在于结合边界处。