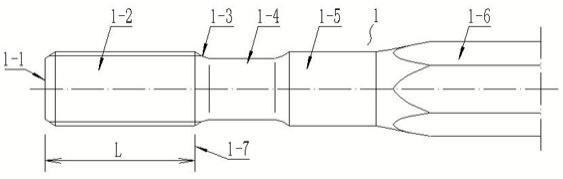
1.本发明涉及一种凿岩钎具,尤其涉及一种带退刀槽螺纹钎杆改进结构。
背景技术:2.冲击式凿岩钎具通常由钎杆通过螺纹与钎头裤体连接而成。在凿岩过程中,钎杆、钎头裤体受力情况比较复杂、恶劣,容易造成钎具失效,影响钎具寿命。其中,钎杆外螺纹段发生断裂是钎杆失效的主要形式。经过试验、分析,造成钎杆断裂的主要原因如下:当受到弯矩作用时钎杆会绕弯曲支点发生弯曲,而最大弯曲应力的作用点通常位于距离该弯曲支点右端8~20
㎜
处的钎杆上。当钎杆外螺纹段的长度大于钎头裤体螺纹盲孔深度时,弯曲支点发生在与内螺纹起始端对应配合的外螺纹处;当钎杆外螺纹段的长度小于钎头裤体螺纹盲孔深度时,弯曲支点则发生在外螺纹尾端。由于传统钎杆的螺纹段长度均远远大于钎头裤体的螺纹盲孔深度,因此最大弯曲应力会作用在钎杆的外螺纹段上,与螺纹沟槽处的热应力形成叠加,最终导致钎杆易在距离弯曲支点8~20
㎜
处的外螺纹段发生断裂。
技术实现要素:3.针对现有技术存在的上述缺陷,本发明旨在提供一种结构简单、不易断裂的带退刀槽螺纹钎杆改进结构。
4.为了实现上述目的,本发明采用以下技术方案:它包括前段部位具有外螺纹段的钎杆本体;在外螺纹段与杆体之间有退刀槽,该退刀槽与外螺纹段之间通过圆弧面光滑过渡连接;外螺纹段前端面至外螺纹尾端的距离l小于钎头裤体的螺纹盲孔深度h;螺纹盲孔深度h与外螺纹段前端面至外螺纹尾端的距离l的差值a为2~6
㎜
。
5.外螺纹段的前端有导向段,导向段端面至外螺纹尾端的距离l1小于钎头裤体的螺纹盲孔深度h;螺纹盲孔深度h与导向段端面至外螺纹尾端的距离l1的差值a均为2~6
㎜
。
6.与现有技术比较,本发明由于采用了上述技术方案,因此具有以下优点:1)由于在钎杆外螺纹段的尾端设置退刀槽,并且将螺纹盲孔深度h与外螺纹段前端面至外螺纹尾端的距离l的差值a控制在2~6
㎜
,因此能够使最大弯曲应力作用于退刀槽区域,从而可避免最大弯曲应力与外螺纹沟槽处的热应力形成叠加,进而改善了钎杆在弯曲支点附近的受力状况,减轻了钎杆的弯曲程度、降低了钎杆在弯曲支点附近断裂的几率。
7.2)在距离弯曲支点附近用退刀槽替代外螺纹(或外螺纹缓慢收刀段),不仅避免最大弯曲应力与螺纹沟槽处热应力形成叠加,而且还可减少螺纹的车削长度、改善螺纹加工条件和加工质量、提高钎杆加工效率、降低加工成本。
附图说明
8.图1是本发明实施例的结构示意图;图2是本发明另一个实施例的结构示意图;
图3是具有内螺纹退刀槽的钎头裤体结构示意图;图4是不具有内螺纹退刀槽的钎头裤体结构示意图;图5是本发明其中一个实施例与钎头裤体配合的结构示意图;图6是本发明另外一个实施例与钎头裤体配合的结构示意图;图7是具有退刀槽的传统钎杆与钎头裤体配合的结构示意图;图8是不具有退刀槽的传统钎杆与钎头裤体配合的结构示意图;图9是将本发明与钎头裤体配合,并进行弯曲应力模拟试验所得到的应力分布图;图10是将传统钎杆与钎头裤体配合,并进行弯曲应力模拟试验所得到的应力分布图。
9.图中:钎杆本体1、外螺纹段前端面1-1、外螺纹段1-2、圆弧面1-3、退刀槽1-4、过渡段1-5、杆体1-6、外螺纹尾端1-7、导向段端面1-8、导向段1-9、最大弯曲应力作用区域1-10、外螺纹缓慢收刀区域1-11,钎头裤体2、孔底2-1、螺纹盲孔2-2、螺纹盲孔端口2-3。
具体实施方式
10.下面结合附图和具体的实施例对本发明作进一步说明。
11.实施例1如图1所示:钎杆本体1的前段部位具有外螺纹段1-2、后段部位具有杆体1-6,在外螺纹段1-2与杆体1-6之间有退刀槽1-4,该退刀槽与外螺纹段1-2之间通过圆弧面1-3光滑过渡连接。外螺纹段前端面1-1至外螺纹尾端1-7的距离l小于与之配合的钎头裤体2的螺纹盲孔深度h。
12.使用时,将本实施例的钎杆本体1与图3中的钎头裤体2配合拧紧(参见图5),外螺纹段前端面1-1与螺纹盲孔2-2(带有内螺纹退刀槽)的孔底2-1保持接触、利于钎杆均匀传递打击力。从图5可以看出,外螺纹尾端1-7位于钎头裤体2的螺纹盲孔2-2内。当受到弯矩作用时,钎杆本体1会在外螺纹尾端1-7处发生弯曲,而最大弯曲应力作用区域1-10位于退刀槽1-4内。为了保证钎杆本体1与钎头裤体2稳固连接,同时也为了避免钎杆本体1弯曲时压迫钎头裤体2而导致螺纹盲孔端口2-3胀裂,应保证外螺纹尾端1-7至螺纹盲孔端口2-3的距离a等于螺纹盲孔深度h与外螺纹段前端面1-1至外螺纹尾端1-7的距离l的差值为2~6
㎜
;即a=h-l=2~6
㎜
。
13.实施例2在基本结构与实施例1相同的基础上,本发明还可以采用如图2所示的结构:外螺纹段1-2的前端有与之连为一体的导向段1-9,导向段端面1-8至外螺纹尾端1-7的距离l1小于螺纹盲孔深度h。
14.使用时,将本实施例的钎杆本体1与图4中的钎头裤体2配合拧紧(参见图6),外螺纹段前端面1-1与螺纹盲孔2-2(带有内螺纹退刀槽)的孔底2-1保持接触、利于钎杆均匀传递打击力。从图6可以看出,外螺纹尾端1-7位于钎头裤体2的螺纹盲孔2-2内。当受到弯矩作用时,钎杆本体1会在外螺纹尾端1-7处发生弯曲,而最大弯曲应力作用区域1-10位于退刀槽1-4内。为了保证钎杆本体1与钎头裤体2稳固连接,同时也为了避免钎杆本体1弯曲时压迫钎头裤体2而导致螺纹盲孔端口2-3胀裂,应保证外螺纹尾端1-7至螺纹盲孔端口2-3的距
离a等于螺纹盲孔深度h与导向段端面1-8至外螺纹尾端1-7的距离l1的差值为2~6
㎜
;即a=h-l1=2~6
㎜
。
15.在上述两实施例中,为了便于加工,杆体1-6与退刀槽1-4之间还可以通过过渡段1-5连接。
16.对照例1将具有退刀槽的传统钎杆本体1与图3中的钎头裤体2配合拧紧时(参见图7),外螺纹段1-2从螺纹盲孔2-2的右端向外延伸出一段距离b=l-h>20
㎜
。当受到弯矩作用时,钎杆本体1会在螺纹盲孔端口2-3处发生弯曲,而最大弯曲应力作用区域1-10位于外螺纹段1-2的延伸段区域内,最大弯曲应力会与螺纹沟槽处的热应力发生叠加,从而增大了钎杆弯曲程度,导致钎杆易在应力叠加处发生断裂。
17.对照例2将不具有退刀槽的传统钎杆本体1与图4中的钎头裤体2配合拧紧时(参见图8),外螺纹段1-2从螺纹盲孔2-2的右端向外延伸一段距离b=l
1-h>20
㎜
。当受到弯矩作用时,钎杆本体1会在螺纹盲孔端口2-3处发生弯曲,而最大弯曲应力作用区域1-10位于外螺纹缓慢收刀区域1-11内,最大弯曲应力会与螺纹沟槽处的热应力发生叠加,从而增大了钎杆弯曲程度,导致钎杆易在应力叠加处发生断裂。
18.以下是将实施例1或实施例2中的本发明钎杆,对照例1或对照例2中的传统钎杆置于固定圆筒内(模拟钎头裤体与外螺纹连接后在一个固定的圆筒内受力,圆筒最大直径不超过钎杆外径10
㎜
)所进行的受力弯曲模拟对比实验:其中,所述裤体螺纹盲孔的深度h为76
㎜
,本发明钎杆外螺纹长度l为72
㎜
,a=h-l=4
㎜
,实验结果见图9;所述裤体螺纹盲孔的深度h为76
㎜
,传统钎杆外螺纹长度l1>h,b=l
1-h>20
㎜
,实验结果见图10。
19.从图9中可以看出,最大弯曲应力分布于距离钎杆前端面80
㎜
附近(距离弯曲支点8
㎜
),最大弯曲应力为59.233mpa,落在退刀槽1-4区域内。从图10中可以看出,最大弯曲应力分布于距离钎杆前端面100
㎜
附近,距离弯曲支点24
㎜
;最大弯曲应力为36.297mpa,落在外螺纹的延伸段区域。
20.从上述模拟实验可以看出,本发明钎杆的抗弯强度相对于传统钎杆而言可提高58%左右。
21.以下是分别采用实施例1或实施例2中的本发明钎杆,相同规格的对照例1或对照例2中的传统钎杆针对同一岩石所进行的矿山凿岩对比试验,测试数据见表1。
22.表1:使用寿命对比 本发明钎杆传统钎杆提高比钻凿寿命(米)3261.52286.942.6%试验结果表明,本发明钎杆在内外螺纹弯曲支点附近的断裂现象明显减少;使用寿命可提高42.6%,与模拟实验结论一致。