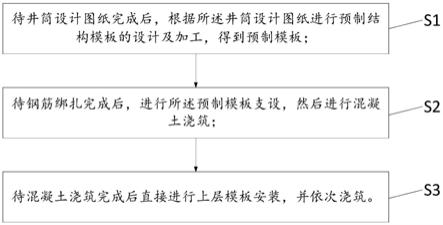
1.本发明涉及矿井建设技术领域,尤其涉及一种基于结构模板的套壁施工方法。
背景技术:2.立井套壁施工,因其具有良好的防水性能和受力条件,在立井施工中得到广泛应用。现有立井井筒套壁施工工艺主要有滑模和倒模两种施工方法。
3.滑模施工是利用自带顶升装置的大模板,在钢筋绑扎结束后进行混凝土浇筑,并通过顶升装置使模板上升,做到连续施工。该施工工艺优点是连续浇筑不产生接茬缝,缺点是混凝土出模强度低,快速施工难以控制施工质量。倒模施工主要是利用多套金属组合小模板,在钢筋绑扎完成后依次进行支模、浇筑混凝土,待下层模板内混凝土达到一定强度后拆除小模板,并将进行重复施工,该施工工艺因其出模混凝土强度较高,井壁成型质量较好得到广泛应用。但其存在拆运模板、多层吊盘作业和炸模风险,安全事故时有发生,《煤矿安全规程》也对其施工进度做了较为严格的限定。两种施工工艺其速度都受到相应工艺条件限制,都难以加快施工效率。
技术实现要素:4.本发明的目的在于提供一种基于结构模板的套壁施工方法,旨在解决现有技术中的立井套壁施工效率慢的技术问题。
5.为实现上述目的,本发明采用的一种基于结构模板的套壁施工方法,包括如下步骤:待井筒设计图纸完成后,根据所述井筒设计图纸进行预制结构模板的设计及加工,得到预制模板;
6.待钢筋绑扎完成后,进行所述预制模板支设,然后进行混凝土浇筑;
7.待混凝土浇筑完成后直接进行上层模板安装,并依次浇筑。
8.其中,预制结构模板的设计及加工包括:
9.确定所述预制结构模板尺寸及内预埋管线、预留洞口、预留灯槽和预埋传感器的定位尺寸。
10.其中,预制结构模板的设计及加工还包括:
11.根据施工进度计划对所述结构模板自身强度和连接强度进行计算。
12.其中,所述根据施工进度计划对所述结构模板自身强度和连接强度进行计算,具体步骤为:
13.首先根据混凝土重力密度、初凝时间、浇灌速度、施工温度信息计算新浇混凝土对模板侧向压力;
14.然后再根据振捣和倾倒附加荷载,计算总荷载;
15.最后根据总荷载和模板形状、尺寸、材质,验算强度是否满足施工要求。
16.其中,预制结构模板的设计及加工还包括:
17.对预制结构模板的选材厚度、连接强度、预留及预埋位置进行优化。
18.其中,对预制结构模板的连接强度、预留及预埋位置进行优化的具体标准为:
19.预埋管线需避开牛腿位置,并考虑管线预埋对井壁模板强度的影响;
20.模板间的连接需满足强度、刚度及密封性要求。
21.其中,在预制模块设计及加工后,将预制模块进行分层,每层分为若干块模块进行预制,在每层模块预制完成后进行预组装。
22.本发明的一种基于结构模板的套壁施工方法,钢筋绑扎完成后,进行所述预制模板支设,然后进行混凝土浇筑,混凝土浇筑完成后直接进行上层模板安装,并依次浇筑,不拆除模板,让模板与结构稳定结合并成为其组成部分。结构模板在结构中主要起预埋造型、初始支撑和后期辅助受力的作用,后浇混凝土起主要受力作用,通过上述施工方法,不需要拆除模板,可提高施工进度,加快施工速率。
附图说明
23.为了更清楚地说明本发明实施例或现有技术中的技术方案,下面将对实施例或现有技术描述中所需要使用的附图作简单地介绍,显而易见地,下面描述中的附图仅仅是本发明的一些实施例,对于本领域普通技术人员来讲,在不付出创造性劳动的前提下,还可以根据这些附图获得其他的附图。
24.图1是本发明的基于结构模板的套壁施工方法的步骤流程图。
具体实施方式
25.下面详细描述本发明的实施例,所述实施例的示例在附图中示出,其中自始至终相同或类似的标号表示相同或类似的元件或具有相同或类似功能的元件。下面通过参考附图描述的实施例是示例性的,旨在用于解释本发明,而不能理解为对本发明的限制。
26.在本发明的描述中,需要理解的是,术语“长度”、“宽度”、“上”、“下”、“前”、“后”、“左”、“右”、“竖直”、“水平”、“顶”、“底”“内”、“外”等指示的方位或位置关系为基于附图所示的方位或位置关系,仅是为了便于描述本发明和简化描述,而不是指示或暗示所指的装置或元件必须具有特定的方位、以特定的方位构造和操作,因此不能理解为对本发明的限制。此外,在本发明的描述中,“多个”的含义是两个或两个以上,除非另有明确具体的限定。
27.请参阅图1,本发明提供了一种基于结构模板的套壁施工方法,包括如下步骤:
28.s1:待井筒设计图纸完成后,根据所述井筒设计图纸进行预制结构模板的设计及加工,得到预制模板;
29.s2:待钢筋绑扎完成后,进行所述预制模板支设,然后进行混凝土浇筑;
30.s3:待混凝土浇筑完成后直接进行上层模板安装,并依次浇筑。
31.在本实施方式中,本发明通过将模板与结构合二为一,让模板成为结构的一部分,钢筋绑扎完成后,进行所述预制模板支设,然后进行混凝土浇筑,混凝土浇筑完成后直接进行上层模板安装,并依次浇筑,不拆除模板,让模板与结构稳定结合并成为其组成部分。结构模板在结构中主要起预埋造型、初始支撑和后期辅助受力的作用,后浇混凝土起主要受力作用,通过上述施工方法,不需要拆除模板,可提高施工进度,加快施工速率。另外在钢筋绑扎完成的步骤前,还包括:对井壁进行凿毛处理。以此进一步提升后续套壁的施工质量。
32.通过以上施工方法,不需要拆除模板,可提高施工进度,同时避免多层吊盘作业提
高安全性。结构模板在井上加工容易实现其良好成型质量和设计强度。结构模板内可根据实际需要进行造型、预留洞口、预埋线管、设置灯槽,并可以预埋传感器实时检测井筒受力变形情况。
33.由于不拆除模板进行翻倒、原吊盘满足施工条件无需下挂两层辅助吊盘;不拆除模板不需要考虑混凝土初凝强度可加快施工速度,预计可以提高施工速度60%以上。实现管线预埋,可以减少井筒直径,预计可以节省投资5%左右。实现井壁亮化及检测数字化,可以缩短检修时间提高检修效率50%以上,并可以提高井筒安全性。
34.预制结构模板的设计及加工包括:
35.确定所述预制结构模板尺寸及内预埋管线、预留洞口、预留灯槽和预埋传感器的定位尺寸。
36.预制结构模板的设计及加工还包括:
37.根据施工进度计划对所述结构模板自身强度和连接强度进行计算,具体为:首先根据混凝土重力密度、初凝时间、浇灌速度、施工温度信息计算新浇混凝土对模板侧向压力;然后再根据振捣和倾倒附加荷载,计算总荷载;最后根据总荷载和模板形状、尺寸、材质,验算强度是否满足施工要求,确保其能支撑混凝土侧压力。
38.预制结构模板的设计及加工还包括:对预制结构模板的选材厚度、连接强度、预留及预埋位置进行优化。对预制结构模板的连接强度、预留及预埋位置进行优化的具体标准为:预埋管线需避开牛腿位置,并考虑管线预埋对井壁模板强度的影响;模板间的连接需满足强度、刚度及密封性要求。对预制结构模板的选材厚度、连接强度、预留及预埋位置进行优化的具体标准还包括:灯带设置要避开安装位置,并均匀布置,照度满足检修需求;
39.对预制结构模板的选材厚度、连接强度、预留及预埋位置进行优化的具体标准还包括:当需要预留洞口时,模板强度需要进行单独计算,且预埋管线避开预留洞口处,其中预埋管线要避开牛腿位置,并考虑管线预埋对井壁模板强度的影响,必要时需要进行补强。模板间连接要满足强度、刚度及密封性要求,可用u型螺栓加凹凸槽的形式。灯带设置要避开安装位置,并尽量均匀布置,照度满足检修需要。当需要有留洞口时,模板强度需要进行单独计算,且预埋管线尽量避开预留洞口处。
40.在预制模块设计及加工后,将预制模块进行分层,每层分为若干块模块进行预制,在每层模块预制完成后进行预组装。其中,由于井筒套壁施工高度一般百米到几百米不等,需要进行分层施工,按照以往经验,为施工方便,兼顾施工速度,一般情况下每层模板高度为1—1.2m不等。在每层模板中又要分为若干块(有限作业空间吊装和安装方便),在井筒掘进期间,根据确定的井壁模板形状,构件预制顺序是从下往上按层进行,每层又分为若干块进行预制,以此检查其连接精度避免漏浆、检验其连接强度避免其涨模。同时检查其预埋管线接口、预留灯槽、预留洞口和预埋传感器位置定位准确性,确保功能实现。根据需要可以在表面进行涂装、彩化。
41.以上所揭露的仅为本发明一种较佳实施例而已,当然不能以此来限定本发明之权利范围,本领域普通技术人员可以理解实现上述实施例的全部或部分流程,并依本发明权利要求所作的等同变化,仍属于发明所涵盖的范围。