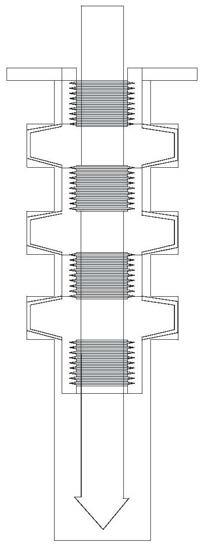
1.本发明涉及锚杆回收技术领域,尤其涉及一种多段自适应膨胀锚杆回收 方法。
背景技术:2.边坡加固工程中锚杆支护是最为常见的一种边坡支护方式,目前国内外 相关技术较为成熟,但锚杆仅作为一种临时支护设施,工程竣工后,锚杆被 大量地废弃在土体中,不仅会对邻近工程的施工造成不利影响,而且资源浪 费、污染严重,与地下空间及建筑用地越来越紧张的趋势相悖,因此近几年 国家和地方出台相关政策规定建筑用地红线,锚杆遗留问题亟待解决。为了 解决这一问题,国外较早提出了可回收锚杆的理念并推出相关产品,国内起 步较晚但发展速度较快。目前的膨胀锚杆无法回收设计这样的回收机制和方 法。因此需要设计相应的膨胀锚杆,然后使用完后对膨胀锚杆进行回收。
技术实现要素:3.本发明的目的在于提供一种多段自适应膨胀锚杆回收方法,解决现有锚 杆无法回收的技术问题。该回收方法针对特别设计的多段自适应膨胀锚杆进 行回收。
4.一种多段自适应膨胀锚杆回收方法,从锚杆壳的中间孔放入扩大钻头, 扩大钻头在锚杆壳内正转,破除锚杆壳管内和底部的水泥浆,然后扩大钻头 反转清除底部混凝土碎料,把拉张装置扭入锚杆壳内将锚杆壳向下拉直,然 后锚杆壳没有土体的横向阻力,将锚杆壳取出,完成回收。
5.进一步地,扩大钻头的外径与锚杆壳的内径大小相等。
6.进一步地,锚杆壳内部设置为空心结构,锚杆壳内注入混凝土,锚杆壳 设置在土体的钻孔内,锚杆壳包括若干段内螺纹段和若干段膨胀段,两段内 螺纹段之间设置有一段膨胀段,锚杆壳的两端均设置内螺纹段,锚杆壳安装 进土体内后,膨胀段向外拉张与土体紧密贴合,与土体锚固。
7.进一步地,膨胀段设置为空管结构,侧壁上设置有若干个注浆孔,注浆 孔设置为椭圆形结构或者圆形结构。
8.进一步地,锚杆壳注浆时,将设置的注浆机构拧入锚杆壳内,注浆机构 内部设置为空心结构,包括螺纹保护段和注浆段,螺纹保护段和注浆段相间 设置,注浆段上设置有注浆漏孔,螺纹保护段与锚杆壳的内螺纹段螺纹设置, 螺纹保护段的长度与内螺纹段相同,将水泥浆从注浆机构内部空心壳体注入, 水泥浆从注浆漏孔流到锚杆壳的膨胀段的内部,并从注浆孔流到外部土体, 注浆完后,待水泥浆从浆体变为固体后,时间为1
‑
2小时,将注浆机构拧出, 然后拧入螺杆。根据膨胀段的数量,设置注浆段数量,每个注浆段和膨胀段 相契合。
9.进一步地,拉张装置包括前端旋转板、前端主杆、前端螺纹、后端旋转 板、后端旋转杆、后端主杆和后端螺纹,前端旋转板设置在前端主杆的一端, 前端螺纹设置在前端主杆另一端的侧壁上,前端主杆中间开设有通孔,后端 旋转杆穿过通孔,后端旋转板设置在
前端主杆的一端,后端主杆设置在前端 主杆的另一端,后端主杆的大小与前端主杆的大小相同,后端螺纹设置在后 端主杆上。
10.进一步地,拉张装置拉直锚杆壳的具体过程为:将后端主杆拧入锚杆壳 最底部的内螺纹段内,然后把前端主杆的前端螺纹拧在倒数第二段内螺纹段 上,然后固定端旋转板,同时把前端主杆固定,用力向下压后端旋转板,使 得后端主杆带最底部的内螺纹段向底部运动,拉直最底部的内螺纹段与倒数 第二段内螺纹段之间的膨胀段,依次同理后端主杆拧入锚杆壳倒数第二段的 内螺纹段内,然后把前端主杆的前端螺纹拧在倒数第三段内螺纹段上,拉直 倒数第二段的内螺纹段与倒数第三段内螺纹段之间的膨胀段,依次拉直整根 锚杆壳。
11.进一步地,破除锚杆壳底部的水泥浆的深度为锚杆壳所有膨胀段长度之 和。
12.进一步地,将锚杆壳取出的具体过程为:将螺杆拧入锚杆壳内,然后将 锚杆壳的外端与螺杆固定为一体,然后出力往外拔,螺杆对锚杆壳内部进行 连接性保护,锚杆壳完整被取出,然后拧开螺杆,回收到完整的锚杆壳。
13.本发明采用了上述技术方案,本发明具有以下技术效果:
14.本发明通过使用扩大钻头清楚混凝土,然后使用拉张装置一节一节的把 锚杆壳拉直,不仅可以优先的保证锚杆壳全部回收出来,同时还能保证了锚 杆壳的完整性,从而可以重复的利用锚杆壳,不仅实现回收,还实现重复利 用,具有非常的推广意义,一个行业的变革,
附图说明
15.图1为本发明放入扩大钻头破除混凝土结构示意图。
16.图2为本发明锚杆膨胀外壳结构示意图。
17.图3为本发明拉张装置剖面图。
18.图4为本发明钻头清除混凝土结构示意图。
19.图5为本发明注浆机构结构示意图。
20.图中标号:1
‑
锚杆壳;1.1
‑
可拆卸圆盘;1.2
‑
内螺纹段;1.3
‑
膨胀段;1.4
‑ꢀ
注浆孔;1.5
‑
压力传感器;1.6
‑
弯曲软角位移传感器;2
‑
拉张装置;2.1
‑
前端旋 转板;2.2
‑
前端主杆;2.3
‑
前端螺纹;2.4
‑
后端旋转板;2.5
‑
后端旋转杆;2.6
‑ꢀ
后端主杆;2.7
‑
后端螺纹;3
‑
注浆机构;3.1
‑
螺纹保护段;3.2
‑
注浆段;3.3
‑
注 浆漏孔;5
‑
钻头。
具体实施方式
21.为使本发明的目的、技术方案及优点更加清楚明白,举出优选实施例, 对本发明进一步详细说明。然而,需要说明的是,说明书中列出的许多细节 仅仅是为了使读者对本发明的一个或多个方面有一个透彻的理解,即便没有 这些特定的细节也可以实现本发明的这些方面。
22.一种多段自适应膨胀锚杆回收方法,如图1所示,从锚杆壳1的中间孔 放入扩大钻头,扩大钻头在锚杆壳1内正转,破除锚杆壳1的膨胀段1.3管内 和底部的水泥浆,然后扩大钻头反转清除底部混凝土碎料,把拉张装置扭入 锚杆壳1内将锚杆壳1向下拉直,然后锚杆壳1没有土体的横向阻力,将锚 杆壳1取出,完成回收。扩大钻头的外径与锚杆壳1的内径大
小相等。防止 扩大钻头对对螺纹造成损伤,又能把混凝土清除干净。
23.本发明实施例中,如图2所示,锚杆壳1内部设置为空心结构,锚杆壳1 内注入混凝土,锚杆壳1设置在土体的钻孔内,锚杆壳1包括若干段内螺纹 段1.2和若干段膨胀段1.3,两段内螺纹段1.2之间设置有一段膨胀段1.3,锚 杆壳1的两端均设置内螺纹段1.2,锚杆壳1安装进土体内后,膨胀段1.3向 外拉张与土体紧密贴合,与土体锚固。膨胀段1.3设置为空管结构,侧壁上 设置有若干个注浆孔1.4,注浆孔1.4设置为椭圆形结构。锚杆壳1的前端设 置有可拆卸圆盘1.1与锚杆壳1的前端连接,可拆卸圆盘1.1的直径比锚杆壳 1的直径大。
24.本发明实施例中,如图5所示,锚杆壳1注浆时,将设置的注浆机构3 拧入锚杆壳1内,注浆机构3内部设置为空心结构,包括螺纹保护段3.1和注 浆段3.2,螺纹保护段3.1和注浆段3.2相间设置,注浆段3.2上设置有注浆漏 孔3.2,螺纹保护段3.1与锚杆壳1的内螺纹段1.2螺纹设置,螺纹保护段3.1 的长度与内螺纹段1.2相同,将水泥浆从注浆机构3内部空心壳体注入,水泥 浆从注浆漏孔3.2流到锚杆壳1的膨胀段1.3的内部,并从注浆孔1.4流到外 部土体。注浆完后,待水泥浆从浆体变为固体后,时间为1
‑
2小时,将注浆机 构3拧出,然后拧入螺杆。注浆的时候采用专用的注浆结构,对准注浆孔, 向外注浆,防止浆液污染内部螺纹,后面张拉杆无法扭入,或者改为螺纹相 匹配的钻头。
25.本发明实施例中,如图3所示,拉张装置包括前端旋转板2.1、前端主杆 2.2、前端螺纹2.3、后端旋转板2.4、后端旋转杆2.5、后端主杆2.6和后端螺 纹2.7,前端旋转板2.1设置在前端主杆2.2的一端,前端螺纹2.3设置在前端 主杆2.2另一端的侧壁上,前端主杆2.2中间开设有通孔,后端旋转杆2.5穿 过通孔,后端旋转板2.4设置在前端主杆2.2的一端,后端主杆2.6设置在前 端主杆2.2的另一端,后端主杆2.6的大小与前端主杆2.2的大小相同,后端 螺纹2.7设置在后端主杆2.6上。
26.本发明实施例中,拉张装置拉直锚杆壳1的具体过程为:将后端主杆2.6 拧入锚杆壳1最底部的内螺纹段1.2内,然后把前端主杆2.2的前端螺纹2.3 拧在倒数第二段内螺纹段1.2上,然后固定端旋转板2.1,同时把前端主杆2.2 固定,用力向下压后端旋转板2.4,使得后端主杆2.6带最底部的内螺纹段1.2 向底部运动,拉直最底部的内螺纹段1.2与倒数第二段内螺纹段1.2之间的膨 胀段1.3,依次同理后端主杆2.6拧入锚杆壳1倒数第二段的内螺纹段1.2内, 然后把前端主杆2.2的前端螺纹2.3拧在倒数第三段内螺纹段1.2上,拉直倒 数第二段的内螺纹段1.2与倒数第三段内螺纹段1.2之间的膨胀段1.3,依次 拉直整根锚杆壳1。破除锚杆壳1底部的水泥浆的深度为锚杆壳1所有膨胀段 1.3长度之和。通过把底部的混凝土破除,预留够长的位置给锚杆壳1伸长, 同时可以存掉落的粉碎混凝土。根据膨胀段1.3的数量,设置注浆段3.2数量, 每个注浆段3.2和膨胀段相契合。
27.本发明实施例中,将锚杆壳1取出的具体过程为:将螺杆拧入锚杆壳1 内,然后将锚杆壳1的外端与螺杆固定为一体,然后出力往外拔,螺杆对锚 杆壳1内部进行连接性保护,锚杆壳1完整被取出,然后拧开螺杆,回收到 完整的锚杆壳1。螺杆对锚杆壳1进行保护,防止在拉出的时候出现断裂, 出现部分无法回收的情况,同时在拉直时,膨胀段1.3没有出现断裂时,可以 在重复利用。
28.多段自适应膨胀锚杆施工方法,包括如下步骤:
29.步骤1:根据膨胀锚杆外壳的长度采用钻头在围岩上钻与膨胀锚杆外壳 相适应的锚杆孔。当膨胀锚杆需要回收时,钻好直线孔后,再使用扩大头式 钻头在钻好的直线孔内
间隔钻扩大孔,扩大孔与膨胀锚杆外壳的膨胀段膨胀 后相契合。
30.确定膨胀锚杆外壳的长度过程为:根据土体需要总共拉拔力,然后根据 设置膨胀锚杆数量,算出每个膨胀锚杆需要的拉拔力,然后分析每一节膨胀 段的受力,拉拔力除以每一节膨胀段的受力得到膨胀段的节数,得到膨胀锚 杆外壳的长。
31.膨胀锚杆外壳还包括压力传感器1.5和弯曲软角位移传感器1.6,压力传 感器1.5和弯曲软角位移传感器1.6均设置在膨胀段1.3的外侧,压力传感器 1.5检测膨胀段1.3的外侧受到土体的压力大小,弯曲软角位移传感器1.6用 于检测膨胀段1.3伸张情况。还包括数据检测装置,数据检测装置上设置有检 测接口,所有的压力传感器1.5和弯曲软角位移传感器1.6均通过导线伸出锚 杆壳1的前端,并设置数据采集口,数据采集口上设置有防水盒盖,不检测 时将防水盒盖盖合设置,在安装和回收膨胀锚杆时,使用数据检测装置检测 膨胀段1.3的受力数据和伸张情况。
32.步骤2:将锚杆膨胀外壳放入锚杆孔内,锚杆头处加固压板,并把拉张 装置拧进锚杆膨胀外壳内,转动拉张装置,对锚杆外壳进行加压,使得膨胀 段膨胀,与周围岩土贴合,将螺杆取出。
33.拉张装置的具体工作过程为:把前端主杆2.2上的前端螺纹2.3与锚杆壳 1入口处的第一个内螺纹段1.2螺纹连接,然后把后端主杆2.6上的后端螺纹 2.7拧到与第二螺纹段1.2螺纹连接,然后固定前端旋转板2.1,把后端旋转板 2.4往外拉,第一个内螺纹段1.2与第二螺纹段1.2之间的膨胀段1.3发生膨胀 契合到扩大孔内,同理把所有的膨胀段1.3拉到膨胀,通过测算后端旋转板 2.4往外拉的距离,进准把内螺纹段1.2拉在两个扩大孔之间。
34.步骤3:将混凝土浇灌到锚杆膨胀外壳内,混凝土填充膨胀段的膨胀处, 混凝土凝固后与土体形成横向阻力。膨胀段1.3设置为空管结构,侧壁上设置 有若干个注浆孔1.4,注浆孔1.4设置为椭圆形结构。一开始为椭圆形结构, 当出现拉张时,会变为圆形结构,使得混凝土更好的从注浆孔1.4流出外部与 土体更好的结合。内螺纹段1.2的外部设置为封闭结构,内部设置有内螺纹, 内螺纹段1.2的厚度比膨胀段1.3的厚度厚。内螺纹段1.2设置更厚,是为了 避免安装和拉伸的时候出现变形的情况。
35.使用完后,如需要回收时,从中孔放入扩大钻头,扩大钻头在锚杆壳1 内正转,破除管内水泥浆,到达锚杆壳1底部后反转清除底部混凝土,破除 底部灌注的水泥浆,然后扭入回收螺杆到螺纹末尾段,向下敲击,一边敲击 一边使用数据检测装置对压力传感器1.5和弯曲软角位移传感器1.6进行检 测,查看各段膨胀段1.3的握裹力和弯曲程度数据,使得膨胀结构重新恢复平 直,拔出锚杆。
36.上述步骤1中分析每一节膨胀段的受力的具体过程为:
37.膨胀锚杆则是依靠中间锚固段侧壁摩阻力、膨胀截面锚固侧壁摩阻力以 及土体对膨胀头端面的阻力三种形式来传递分散荷载,可将其分为n段进行 力学性能分析,n为正整数。因此一段变截面抗拔力由三部分组成:
38.t=t1+t2+t
d
ꢀꢀꢀꢀꢀꢀꢀꢀꢀꢀꢀꢀꢀꢀꢀꢀꢀꢀꢀꢀꢀꢀ
(1)
39.式中:t1为l1段普通非膨胀锚固段侧壁摩阻所提供的抗拔力:
40.t1=πd1l1τ
f
ꢀꢀꢀꢀꢀꢀꢀꢀꢀꢀꢀꢀꢀꢀꢀꢀꢀꢀꢀꢀꢀꢀꢀꢀ
(2)
41.式中:d1和l1为锚杆非膨胀锚固段直径和长度,τ
f
为非膨胀锚固段土体与 锚固筋侧壁之间的摩阻强度;
42.t2为锚杆膨胀锚固段侧壁摩阻所提供的抗拔力:
43.t2=πd2l2τ
fd
ꢀꢀꢀꢀꢀꢀꢀꢀꢀꢀꢀꢀꢀꢀꢀꢀꢀꢀꢀꢀꢀꢀ
(3)
44.其中d2和l2为锚杆非膨胀锚固段直径和长度,τ
fd
为非膨胀锚固段土体与锚 固筋侧壁之间的摩阻强度;
45.td为土体对膨胀端面的正压力所提供的抗拔力:
[0046][0047]
式中:σ
d
为土体作用于变截面上的正压力强度,与膨胀端的埋深、膨胀 端前土体情况以及锚杆的工作状态有关;
[0048]
膨胀锚杆位移与轴力分析过程为:
[0049]
根据剪切位移法,竖向受荷锚杆体周围土的变形可理想的视作同心圆柱 体,根据弹性理论写出土体竖向平衡微分方程:
[0050][0051]
锚杆体受荷后,锚杆体处剪应力τ
rz
的增大远大于σ
z
,取
[0052][0053]
式中,r0为锚杆的半径,τ0为锚杆侧边剪应力,
[0054]
方程的解为:
[0055][0056]
由几何方程,剪切变形为:
[0057][0058]
其中u
s
为径向位移,s为土体竖向位移,略去物理方程为:
[0059][0060]
得到
[0061][0062]
方程的解为:
[0063][0064]
即:
[0065][0066]
其中r
m
为有效影响半径,g为土体的剪切模量,τ(z)为z位置处的锚杆侧摩阻 力;r0为锚杆半径;r
m
为影响半径;r
m
为锚杆侧土剪切变形可忽略的范围, r
m
=χ1χ2l1(1
‑
ν
s
),χ1、χ2为土体不均匀程度经验系数,ν
s
为土体泊松比,r为 与锚杆中心轴的距离,
[0067]
根据锚杆与土接触面的位移协调条件,对于等截面锚杆,可得到的锚杆 侧摩阻力为:
[0068][0069]
对微分单元受力静力平衡条件:
[0070][0071]
式中:u
p
为锚杆周长,τ
ν
(z)为锚杆侧深度z处摩阻力,q(z)为锚杆深度z处轴 力,
[0072]
微单元的弹性压缩为:
[0073][0074]
式中,和a
p
分别为锚杆的弹性模量和横截面积代入式(13)可得:
[0075][0076]
令其中k
v
为锚杆侧土体弹簧刚度,
[0077]
可得锚杆微分方程为:
[0078][0079]
解的位移和轴力为:
[0080]
s(z)=ae
αz
+be
‑
αz
ꢀꢀꢀꢀꢀꢀꢀꢀꢀꢀꢀꢀꢀꢀꢀꢀꢀꢀꢀꢀꢀꢀꢀ
(17)
[0081]
q(z)=
‑
ae
p
a
p
αe
αz
+be
p
a
p
αe
‑
αz
ꢀꢀꢀꢀꢀꢀꢀꢀꢀꢀꢀꢀꢀꢀꢀꢀꢀ
(18)
[0082]
其中c1、c1为常数,可由锚杆体边界条件确定,将上式用矩阵表示:
[0083][0084]
膨胀变截面锚杆锚固力分成三部分,第一部分为细截面杆体l1段与土体 的摩阻力,第二部分为粗截面杆体l2段与土体的摩阻力,第三部分为变截面 处的端阻力,
[0085]
对于变截面锚杆,在采用剪切位移法进行轴力及位移的推导时,将变截 面锚杆分两段即l1段和l2段,忽略变截面引起的锚杆周围土体位移场的影 响,分别应用前述等截面锚杆杆体位移及杆体轴力解,将变截面处的端阻力 和位移连续简化为边界条件,
[0086]
第一段边界条件为:
[0087]
当z=0时,p1(0)=p;当z=l1时,p1(l1)=t;
[0088]
式中:t为第一端锚杆在变截面处的轴力
[0089]
第二段边界条件为:
[0090]
当z=l1时,p2(l1)=t
‑
t
d
;当z=l时,p2(l)=q;
[0091]
式中:l=l1+l2为锚杆微段长度,td为变截面处土体的端阻力, 变截面锚杆l1段与l2段在变截面处的位移连续条件
[0092]
s1(l1)=s2(l1)
ꢀꢀꢀꢀꢀꢀꢀꢀꢀꢀꢀꢀꢀꢀꢀꢀꢀꢀꢀ
(20)
[0093]
将第一段边界条件代入式(18)得
[0094]
‑
e
p1
a
p1
α1(a1‑
b1)=p
ꢀꢀꢀꢀꢀꢀꢀꢀꢀꢀꢀꢀꢀꢀꢀꢀꢀꢀꢀ
(21)
[0095][0096]
将第二段边界条件代入式(18)得
[0097][0098][0099]
第一段与第二段的连续条件式(20)可表示为:
[0100][0101]
联立式(21)、(22)、(23)、(24)、(25)可得系数a1、a2、b1、 b2可计算出第一段锚杆位移和轴力的解析式,代入式(12)可得第一段锚杆 与第二段锚杆侧摩阻力,进而可得第一二段抗拔力;
[0102]
锚杆变截面处膨胀端面应力计算:
[0103]
在锚杆变截面上端取一土体微单元作为考察对象,以锚杆轴线方向为z 轴,为竖直方向,水平方向分别为x轴,则土体被压缩的极限状态下,
[0104]
极限状态下土体单元的各个方向的应力表达式:
[0105]
σ
x
=k0γl1+ξσ
t
ꢀꢀꢀꢀꢀꢀꢀꢀꢀꢀꢀꢀ
(26)
[0106]
σ
y
=k0γl1+ξσ
t
ꢀꢀꢀꢀꢀꢀꢀꢀꢀꢀꢀꢀ
(27)
[0107]
σ
z
=γl1+σ
t
ꢀꢀꢀꢀꢀꢀꢀꢀꢀꢀꢀꢀꢀꢀꢀ
(28)
[0108]
式中:σ
t
为锚杆拉力在土体单元z方向上产生的应力增量,k0为变截面上 端土的静止土压力系数,可按计算;ξ为锚杆发生位移时变截 面上端土反映挤土效应的侧压力系数,可按经验公式ξ=(0.5~0.95)k
a
计算(与 变截面处土体的硬度有关,对较坚硬的土体可取0.95,对软土建议取0.5), 此外和分别为变截面上端土体的主动和被动 土压力系数,其中c、为土体的粘聚力、内摩擦角;
[0109]
土体单元达到极限状态时,σ
z
为最大主应力σ1,σ
x
为最小主应力σ3,根 据摩尔库伦强度理论有
[0110]
[0111]
联立以上得
[0112][0113]
当锚杆变截面处土体各点均达到极限应力状态下时,变截面处的竖向压应力 所提供的极限抗拔力:
[0114][0115]
对于整段锚杆,可根据每段锚杆间的连续条件,结合锚底和锚头得边界 条件,锚底轴力为0,锚头轴力为已知,计算出整段锚杆的荷载传递函数;
[0116]
因此变截面锚杆抗拔力计算公式为:
[0117]
t=t1+t2+t
d
。
[0118][0119]
以上所述仅是本发明的优选实施方式,应当指出,对于本技术领域的普 通技术人员来说,在不脱离本发明原理的前提下,还可以作出若干改进和润 饰,这些改进和润饰也应视为本发明的保护范围。