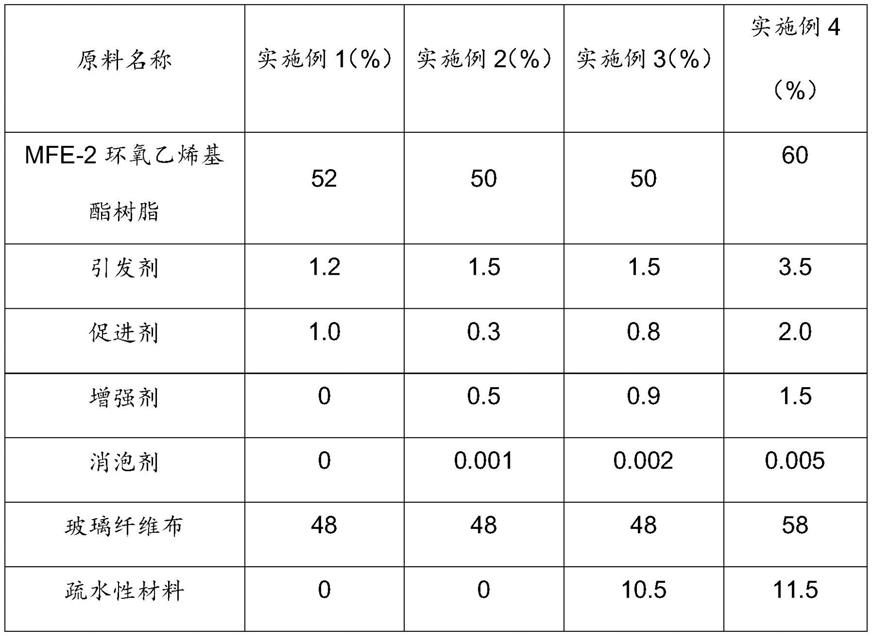
1.本技术属于混凝土结构防腐蚀技术领域,具体涉及悬浮隧道管段混凝土防腐蚀材料及防腐蚀方法。
背景技术:2.由于在深海地区建造桥梁存在诸多不能解决的技术问题,水中悬浮隧道作为跨越海峡、海湾等深海地区的新型交通结构,可解决深海地区交通建造技术难题。与沉管隧道和海底深埋隧道相比,悬浮隧道平面位置的选取和竖直深度的选择都有较大的余地,且不受海底地貌、水文地质条件等影响。因此,水中悬浮隧道正受到越来越多的关注。由于海水对悬浮隧道管段钢筋混凝土具有较强的腐蚀作用,需采取高耐久性的防腐材料进行防腐蚀处理,对悬浮隧道管段材料进行防护,以保证悬浮隧道至少具有120年的高耐久性防腐寿命,从而保证悬浮隧道安全运行。同时,海底悬浮隧道管段还面临洋流、潮流海浪等的冲刷作用,防腐层的力学性能和耐磨性能均具有较高要求。因此,需开发满足悬浮隧道管段混凝土的防腐蚀方法。
3.近年来,玻璃钢包覆防腐技术在海洋环境下的防腐处理和修复中得到了越来越多的应用,但玻璃钢防腐蚀材料存在与混凝土基层粘结强度差及耐久性寿命不足等技术问题。此外,由于悬浮隧道还受到海底较强的水流冲刷作用,海底水生物会大量生长富集在悬浮隧道管段表面,因此还应解决玻璃钢的抗水流冲击和水生物附着等技术问题。
技术实现要素:4.针对上述现有技术的缺点或不足,本技术要解决的技术问题是提供悬浮隧道管段混凝土防腐蚀材料及防腐蚀方法,本技术采用有机硅材料提高管段混凝土耐久性,并提高玻璃钢与管段混凝土的粘结性能;采用高强和高耐久性玻璃钢防护海水对管段冲刷和腐蚀;在玻璃钢表面采用疏水性材料,减缓水流冲刷和水生物富集,从而提高了悬浮隧道管段混凝土的防腐蚀性。
5.为解决上述技术问题,本技术通过以下技术方案来实现:
6.本技术提出了悬浮隧道管段混凝土防腐蚀材料,包括:基层材料、中间层材料以及表层材料,所述基层材料采用有机硅材料,所述中间层材料采用高强和高耐久性玻璃钢,所述表层材料采用疏水性材料。
7.可选地,上述的悬浮隧道管段混凝土防腐蚀材料,其中,所述有机硅材料为烷基硅醇类水性有机硅材料,有机硅材料有效成分与水的质量比为1:0.5,在混凝土中的渗透深度不小于2.5mm;吸水率小于0.001mm/min
1/2
,氯化物吸收量降低效果大于96%。
8.可选地,上述的悬浮隧道管段混凝土防腐蚀材料,其中,所述玻璃钢采用多层玻璃纤维布以及多层胶衣。进一步优选地,在本技术中,优选地采用至少五层玻璃纤维布以及至少六层胶衣。
9.可选地,上述的悬浮隧道管段混凝土防腐蚀材料,其中,所述玻璃纤维布为无碱玻
璃纤维布,厚度为0.2-0.4mm;
10.和/或,所述胶衣由树脂、引发剂、促进剂、增强剂以及消泡剂组成,所述树脂、所述引发剂、所述促进剂、所述增强剂以及所述消泡剂的质量比为(50-60):(1.5-3.5):(0.3-2.0):(0.5-1.5):(0.001-0.005);
11.可选地,上述的悬浮隧道管段混凝土防腐蚀材料,其中,所述树脂为环氧乙烯基酯树脂;
12.和/或,所述引发剂为过氧化甲乙酮;
13.和/或,所述促进剂为异辛酸钴;
14.和/或,所述增强剂为平均粒径30-50nm的碳酸钙;
15.和/或,所述消泡剂为聚醚类消泡剂。
16.可选地,上述的悬浮隧道管段混凝土防腐蚀材料,其中,所述玻璃钢的厚度为3.0-4.0mm。
17.可选地,上述的悬浮隧道管段混凝土防腐蚀材料,其中,所述玻璃钢15d龄期的弯曲强度大于250mpa,玻璃钢抗拉强度大于120mpa,玻璃钢30d龄期吸水率不大于0.1%。
18.可选地,上述的悬浮隧道管段混凝土防腐蚀材料,其中,所述疏水性材料采用复合纳米sio2和纳米tio2氟类聚合物,涂膜厚度为0.3-0.7mm,涂膜的水接触角大于150
°
。
19.其中,在本技术中,管段混凝土强度等级为c40-c100。
20.本技术另一方面还提出了的悬浮隧道管段混凝土防腐蚀材料的防腐蚀方法,包括以下步骤:
21.制备玻璃钢;
22.清理悬浮隧道混凝土管段材料表面,配制有机硅材料,在混凝土管段材料表面涂刷有机硅材料;
23.配置疏水性材料,并在所述玻璃钢表面喷涂所述疏水性材料。
24.可选地,上述的防腐方法,包括:按配比称取引发剂、增强剂和消泡剂依次加入树脂中搅拌均匀,再边搅拌边加入促进剂,待搅拌均匀后得到胶衣;将搅拌均匀的胶衣,涂刷在模具成型面上并铺放玻璃布;重复上述铺层操作,直到达到设计厚度,然后进行固化脱模;
25.和/或,清理悬浮隧道混凝土管段材料表面灰尘和油污等有害物质,配制水性有机硅材料,在混凝土表面涂刷有机硅材料,铺覆玻璃钢,并施加一定力,使玻璃钢与管段混凝土牢固粘结;
26.和/或,配制复合纳米sio2和纳米tio2氟类聚合物疏水性材料,在玻璃钢表面,喷涂所述疏水性材料。
27.与现有技术相比,本技术具有如下技术效果:
28.本技术针对玻璃钢树脂与混凝土基层粘结力差,易导致脱落等技术问题,采用环保性水性有机硅材料,解决玻璃钢常规树脂与混凝土粘结力差的技术问题,可有效提高玻璃钢与管段混凝土粘结,并充分发挥玻璃钢保护作用;疏水性材料具有良好疏水效果,减缓水流对悬浮隧道管段的冲击,避免海洋生物富积,有效保护混凝土管段。
29.本技术中,水性有机硅材料采用水作为溶剂,无挥发性有机溶剂,避免了常规油性有机硅材料对人体和环境的危害,水性有机硅材料可浸渍到混凝土内部,渗透深度不小于
2.5mm,可有效提升混凝土耐久性。
30.本技术采用纳米碳酸钙填充玻璃钢孔隙,采用聚醚消泡剂排除玻璃钢中气泡,显著提高玻璃钢强度和耐久性,具有良好的抗压强度和抗弯强度等力学性能,可抵抗悬浮隧道受外界冲击,保护混凝土管段,有效提升悬浮隧道管段的韧性和抗冲击性能,且具有较高耐久性,获得高强和高耐久性玻璃钢。
31.本技术采用水性有机硅材料、玻璃钢和疏水性材料叠加作用,可有效提升悬浮隧道管段混凝土耐久性,保证不低于120年防腐蚀寿命,其中水性有机硅材料不低于30年防护作用,玻璃钢不低于80年防护作用,疏水性材料不低于10年防护作用,克服了常规玻璃钢包覆技术耐久性不足的技术缺陷。
32.本技术的水性有机硅材料、玻璃钢和疏水性材料具有可施工性好、高强、抗冲击性能高和高耐久性等技术特点,可用于悬浮隧道管段材料等高耐久性防腐蚀领域,具有良好的经济效益和社会效益。
具体实施方式
33.下面将对本技术实施例中的技术方案进行清楚、完整地描述,显然,所描述的实施例仅仅是本技术一部分实施例,而不是全部的实施例。基于本技术中的实施例,本领域普通技术人员在没有做出创造性劳动前提下所获得的所有其他实施例,都属于本技术保护的范围。
34.1.本实施例涉及的试验方法如下:
35.(1)玻璃钢弯曲强度按照国家标准《纤维增强塑料弯曲性能试验方法》(gb/t 1449-2005)相关规定进行。
36.(2)玻璃钢拉伸强度按照国家标准《纤维增强塑料拉伸性能试验方法》(gb/t 1447)相关规定进行。
37.(3)玻璃钢吸水率按照国家标准《纤维增强塑料吸水性试验方法》(gb/t 1462)相关规定进行。
38.(4)玻璃钢与混凝土正拉强度按照国家标准《混凝土结构加固设计规范》(gb/t 50367-2006)中附录f进行。
39.(5)水性有机硅渗透深度、吸水率和氯化物吸收量降低效果按照《海港工程混凝土结构防腐蚀技术规范》(jtj275-2000)相关规定执行。
40.2.实施例原材料
41.(1)mfe-2环氧乙烯基酯树脂;
42.(2)189不饱和聚酯树脂;
43.(3)e44环氧树脂;
44.(4)引发剂为过氧化甲乙酮;
45.(5)促进剂为异辛酸钴;
46.(6)增强剂为平均粒径为30纳米的碳酸钙;
47.(7)消泡剂为聚醚类消泡剂;
48.(8)玻璃纤维布为ewr400无碱玻璃纤维布;
49.(9)疏水性材料为复合纳米sio2和纳米tio2氟类聚合物,涂膜厚度为0.5mm;
50.(10)玻璃钢与混凝土正拉强度试验的混凝土强度等级为c60。
51.3.玻璃钢性能
52.3.1实例玻璃钢配合比
53.玻璃钢配合比如表1所示。
54.表1实施例1-实施例4玻璃钢配比
[0055][0056]
3.2玻璃钢的性能测试结果
[0057]
玻璃钢性能测试结果如下表2所示。
[0058]
表2玻璃钢性能测试结果及抗氯离子渗透寿命
[0059][0060][0061]
从上述表2的测试结果可知,掺入纳米碳酸钙和消泡剂的实施例2的玻璃钢的弯曲强度和拉伸强度明显高于实施例1,且吸水率和氯离子扩散系数明显低于实施例1,抗氯离
子渗透寿命大于80年。此外,玻璃钢表面采用疏水性材料,实施例3和实施例4的弯曲强度和拉伸强度进一步增加,吸水率和氯离子扩散系数进一步降低,抗氯离子渗透寿命大于90年。
[0062]
4.玻璃钢与混凝土粘结强度
[0063]
上述采用表1所示的实施例2中的玻璃钢,分别采用mfe-2环氧乙烯基酯树脂、189不饱和聚酯树脂、e44环氧树脂和水性有机硅材料作为玻璃钢与混凝土的粘结材料,开展玻璃钢与混凝土正拉粘结强度试验,测试结果如下述表3所示。
[0064]
表3玻璃钢与混凝土正拉粘结强度
[0065][0066][0067]
从上述表3可以看出,采用水性有机硅材料时,玻璃钢与混凝土正拉强度明显高于mfe-2环氧乙烯基酯树脂、189不饱和聚酯树脂和e44环氧树脂,可有效保证玻璃钢与管段混凝土粘结,充分发挥玻璃钢作用。
[0068]
5.水性有机硅测试结果
[0069]
水性有机硅测试结果如表4所示。
[0070]
表4水性有机硅材料性能
[0071][0072]
在本实施例中,所采用的水性有机硅材料的渗透深度为3.0mm,吸水率为0.0008mm/min
1/2
,氯化物吸收量降低效果可达97%,抗氯离子渗透寿命为35年。
[0073]
本实施例悬浮隧道管段防腐蚀方法的主要工艺如下:
[0074]
首先,在工厂制作玻璃钢制品,按配比称取引发剂、增强剂和消泡剂依次加入树脂中搅拌均匀,再边搅拌边加入促进剂,待搅拌均匀后得到胶衣;清理好或经过表面处理的模具成型面上涂抹脱模剂,待充分干燥好后,将搅拌均匀的胶衣,涂刷在模具成型面上,随后在其上铺放裁剪好的玻璃布,并浸透树脂、排除气泡。重复上述铺层操作,直到达到设计厚度,然后进行固化脱模。
[0075]
然后,清理悬浮隧道混凝土管段材料表面灰尘和油污等有害物质,配制水性有机硅材料,在混凝土表面涂刷有机硅材料,保证混凝土管段充分浸润,待20-30min后,涂刷第二遍有机硅材料,立即铺覆玻璃钢材料,并施加一定力,使玻璃钢与管段混凝土牢固粘结。
[0076]
最后,配制复合纳米sio2和纳米tio2氟类聚合物疏水性材料,在玻璃钢表面,喷涂疏水性材料,其中,喷涂厚度优选地控制在0.3-0.7mm。
[0077]
本技术采用水性有机硅材料、玻璃钢和疏水性材料复合防腐蚀技术,提出防护达到120年防腐蚀技术方法,可有效满足悬浮隧道管段材料的需要。
[0078]
以上实施例仅用以说明本技术的技术方案而非限定,参照较佳实施例对本技术进行了详细说明。本领域的普通技术人员应当理解,可以对本技术的技术方案进行修改或等同替换,而不脱离本技术技术方案的精神和范围,均应涵盖在本技术的权利要求范围内。