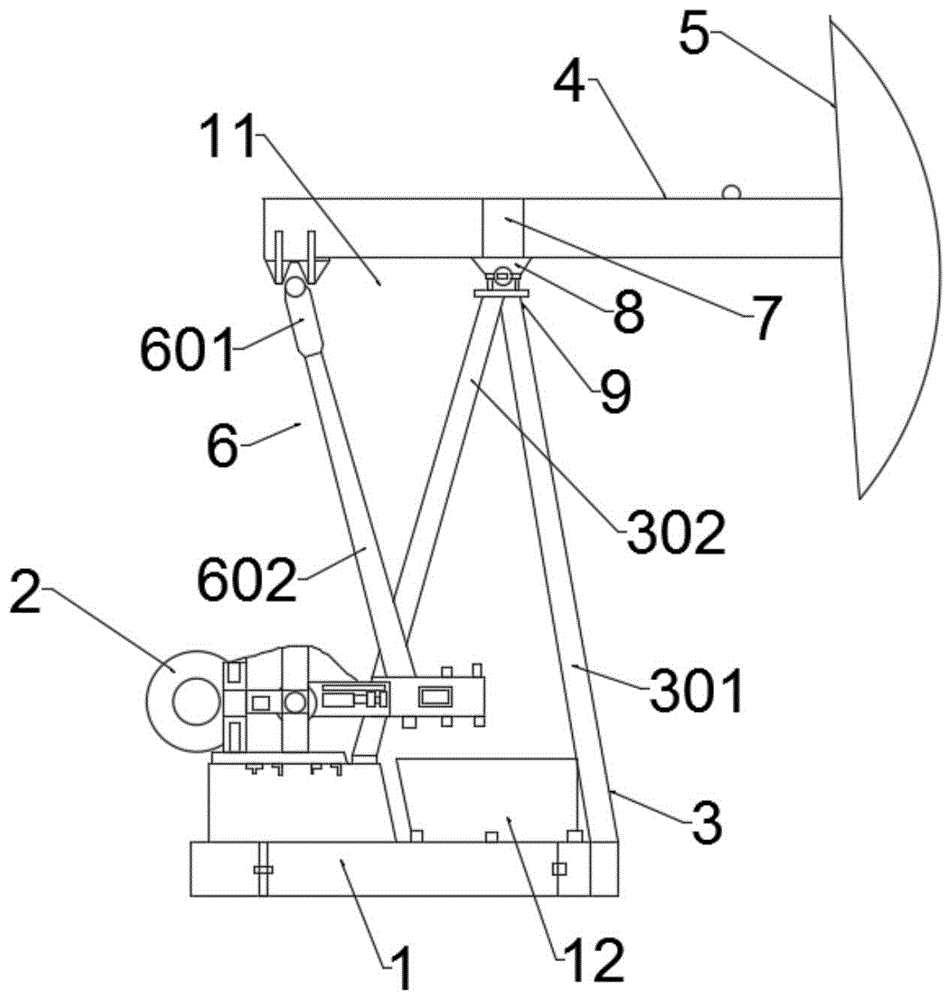
本实用新型涉及抽油机
技术领域:
,具体涉及一种大冲程游梁式抽油机。
背景技术:
:石油作为世界主要能源之一,随着汽车等制造工业的发展,对石油制品的需求量越来越大,因此对采油设备的需求也越来越高。但世界各地地质差异万千,因此对采油设备也提出了不同的性能要求。目前世界采油设备主要分为游梁式抽油机和塔架式抽油机,游梁式抽油机主要应用于中小冲程(240in.及以下),塔架式应用于长冲程(240in.以上)。因此,长冲程的抽油机中没有游梁式的应用,主要都是采用塔架式。但是在实际应用中发现,游梁式抽油机的可靠性比塔架式高百分之五十,且游梁式抽油机的制造成本比塔架式低百分之三十到百分之五十。其主要在于:如图2所示,游梁式抽油机冲程大小主要与a值和h值有关,冲程越大,a值和h值也越大,同样井口载荷的情况下,所有结构件受力就越不理想(受力大于材料强度,或出现应力集中,而造成结构件开裂),如若通过改变其他值改善受力状态,会造成运动特性很差(传力比很低,效率就很低)。因此图中的各个值的最佳匹配,既能使的传力比较高且平稳,又能满足运动性能(完成大冲程),还要结构强度能满足且经济,然而由于曲柄连杆机构的特点,这些要求是相互矛盾的,因此一直限制了游梁式抽油机在长冲程方向的发展。技术实现要素:本实用新型的目的在于提供一种大冲程游梁式抽油机,以解决现有技术中的技术问题。为解决上述技术问题,本实用新型具体提供下述技术方案:一种大冲程游梁式抽油机,包括底座和固定安装在所述底座一端的驱动机构,在所述底座另一端通过支架机构设置有游梁,在所述游梁的前端安装有驴头,且在所述游梁的后端通过连杆与所述驱动机构连接,所述游梁上滑动安装有中座,所述中座和支架机构的连接处通过应力弧贴片连接,所述支架机构包括顶端通过铰接件连接的前支架和后支架,所述前支架和所述后支架的另一端均滑动安装在所述底座两侧。进一步地,设定:a为所述驴头至所述中座的距离;c为所述中座至所述游梁后端的距离;i为所述驱动机构转动中心至所述中座在所述底座上投影之间的距离;p为所述连杆的长度;h为所述中座至所述底座之间的距离;g为所述驱动机构转动中心至所述底座之间的距离;r为所述驱动机构的转动半径;所述a=5791~7395毫米,所述c=3050~3611毫米,所述i=3050~3569毫米,所述p=5759~7386毫米,所述h=8636~10838毫米,所述g=2819~3643毫米,所述r=1524~2047毫米。进一步地,所述游梁式抽油机通过试凑法调整所述距离、长度和转动半径并通过动力学仿真计算输出所述游梁式抽油机的动态特征曲线,并依据所述动态特征曲线的反馈再次调整所述距离、长度和转动半径直至所述动态特征曲线达到最佳。进一步地,所述游梁通过连杆与所述驱动机构的曲柄连接形成曲柄连杆结构,所述游梁和支架机构通过调整所述距离、长度和转动半径形成大冲程的游梁结构,所述曲柄连杆结构和所述应力弧贴片以及支架机构配合大冲程的游梁结构,所述连杆包括分别与所述游梁铰接的底杆和与所述驱动机构铰接的传动杆,所述传动杆通过内置在所述传动杆内的伸缩杆与所述底杆连接,且所述伸缩杆和所述底杆之间也为铰接。进一步地,所述应力弧贴片沿着所述游梁的长轴方向向两端呈弧形延伸。进一步地,所述铰接件两侧均设置有延伸柱,所述前支架和所述后支架分别套设在所述铰接件两侧的延伸柱上,所述前支架和所述后支架在所述底座上沿着游梁的长轴方向活动安装以调整所述前支架和所述后支架之间的夹角。进一步地,设定所述中座的铅垂线为中心线,所述前支架和所述中心线之间的夹角为0-10°,所述后支架和所述中心线之间的夹角为0-16°本实用新型与现有技术相比具有如下有益效果:本实用新型通过设置应力弧贴片以及优化支架机构的不同步滑动来调整其与铰接件与投影点连线的夹角来降低应力集中,从而为将曲柄连杆机构应用于大冲程的游梁式抽油机服务。附图说明为了更清楚地说明本实用新型的实施方式或现有技术中的技术方案,下面将对实施方式或现有技术描述中所需要使用的附图作简单地介绍。显而易见地,下面描述中的附图仅仅是示例性的,对于本领域普通技术人员来讲,在不付出创造性劳动的前提下,还可以根据提供的附图引伸获得其它的实施附图。图1为本实用新型实施例的结构示意图;图2为本实用新型游梁式抽油机结构原理图;图3为本实用新型中应力弧贴片的结构示意图;图4为本实用新型中支架机构和中心线夹角示意图。图中的标号分别表示如下:1-底座;2-驱动机构;3-支架机构;4-游梁;5-驴头;6-连杆;7-中座;8-应力弧贴片;9-延伸柱;301-前支架;302-后支架;601-底杆;602-传动杆。具体实施方式下面将结合本实用新型实施例中的附图,对本实用新型实施例中的技术方案进行清楚、完整地描述,显然,所描述的实施例仅仅是本实用新型一部分实施例,而不是全部的实施例。基于本实用新型中的实施例,本领域普通技术人员在没有做出创造性劳动前提下所获得的所有其他实施例,都属于本实用新型保护的范围。如图1所示,本实用新型提供了一种大冲程游梁式抽油机,包括底座1和固定安装在所述底座1一端的驱动机构2,在所述底座1另一端通过支架机构3设置有游梁4形成游梁式结构,在所述游梁4的前端安装有驴头5,且在所述游梁4的后端通过连杆6与所述驱动机构2连接形成曲柄连杆结构。在本实施方式中,通过在所述底座1另一端通过支架机构3设置有游梁4形成游梁式结构,并通过在所述游梁4的后端通过连杆6与所述驱动机构2连接形成曲柄连杆结构,即首次将曲柄连杆机构(四连杆)的原理在大冲程(240in,即6.1m以上)游梁式抽油机上应用。其中,驱动机构包括电动机,电动机通过皮带与减速器连接,减速器通过曲柄轴连接有连杆6。在现有技术中,游梁式抽油机主要应用于中小冲程(240in.及以下),塔架式应用于长冲程(240in.以上)。因此,长冲程的抽油机中没有游梁式的应用,主要都是采用塔架式。其原因主要是考虑传力比和结构件的受力强度问题。为了进一步说明上述问题,如图2所示,首先设定:a为所述驴头5至所述中座7的距离;c为所述中座7至所述游梁4后端的距离;i为所述驱动机构2转动中心至所述中座7在所述底座1上投影之间的距离;p为所述连杆6的长度;h为所述中座7至所述底座1之间的距离;g为所述驱动机构2转动中心至所述底座1之间的距离;r为所述驱动机构2的转动半径。游梁式抽油机冲程大小主要与a值和h值有关,冲程越大,a值和h值也越大,同样井口载荷的情况下,所有结构件受力就越不理想(受力大于材料强度,或出现应力集中,而造成结构件开裂),如若通过改变其他值改善受力状态,会造成运动特性很差(传力比很低,效率就很低)。因此图中的各个值的最佳匹配,既能使的传力比较高且平稳,又能满足运动性能(完成大冲程),还要结构强度能满足且经济,然而由于曲柄连杆机构的特点,这些要求是相互矛盾的,因此一直限制了游梁式抽油机在长冲程方向的发展。在本实用新型中,所述游梁4通过连杆6与所述驱动机构2的曲柄连接形成曲柄连杆结构,所述游梁4和支架机构3通过调整所述距离、长度和转动半径形成大冲程的游梁结构,所述曲柄连杆结构和所述应力弧贴片8以及支架机构3配合大冲程的游梁结构。将曲柄连杆机构应用于大冲程的游梁式抽油机中,以提高其可靠性,并降低制造成本,具体地:所述游梁式抽油机通过试凑法调整所述距离、长度和转动半径并通过动力学仿真计算输出所述游梁式抽油机的动态特征曲线,并依据所述动态特征曲线的反馈再次调整所述距离、长度和转动半径直至所述动态特征曲线达到最佳。在本实施方式中,为了使得连杆6能够适应支架机构3的长度以及角度变化,连杆6的长度可以根据实际需求适应性的发生变化。具体地:所述连杆6包括分别与所述游梁4铰接的底杆601和与所述驱动机构2铰接的传动杆602,所述传动杆602通过内置在所述传动杆602内的伸缩杆与所述底杆601连接,且所述伸缩杆和所述底杆601之间也为铰接。其中,伸缩杆为常规的伸缩结构,如双套杆的伸缩结构,但是需要说明的是,该伸缩结构需要配合锁定结构使用,即伸缩杆在调整长度时可以在任意长度进行锁定。在本实施方式中,各个尺寸值优化如下:a(mm)c(mm)i(mm)p(mm)h(mm)g(mm)r(mm)5791~73953050~36113050~35695759~73868636~108382819~36431524~2047在本实用新型中,仅仅依据参数的优化并不能够实现将曲柄连杆机构应用于大冲程的游梁式抽油机的目的。因此,进一步地,如图1和图3所示,所述游梁4上滑动安装有中座7,所述中座7和支架机构3的连接处通过应力弧贴片8连接,所述支架机构3包括顶端通过铰接件连接的前支架301和后支架302,所述前支架301和所述后支架302的另一端均滑动安装在所述底座1两侧。采用应力弧贴片8连接中座7和支架机构3,降低中座7的受力,提高疲劳强度。具体地,所述应力弧装置8包括与支架机构3连接的轴承座801和与所述中座7连接的贴片体802;所述轴承座801的剖面呈梯形,且所述轴承座801和所述贴片体802之间通过弧形延展体803连接,所述轴承座801、弧形延展体803和所述贴片体802为一体化结构。主要原因在于,大冲程游梁抽油机会造成a值很大,因此游梁受力状态差,出现应力集中,大大降低结构寿命,本实用新型采用应力弧结构,释放应力集中,根据实验证明:应力由310mpa降低为98mpa。第二方面,所述铰接件两侧均设置有延伸柱9,所述前支架301和所述后支架302分别套设在所述铰接件两侧的延伸柱9上,所述前支架301和所述后支架302在所述底座1上沿着游梁4的长轴方向活动安装以调整所述前支架301和所述后支架302之间的夹角。设定所述中座7的铅垂线为中心线,优化支架前后腿角度,改善支架受力状态,提高可靠性,通过试凑法不断调整前后腿角度进行动力学和有限元分析,直到满足强度要求,其中,如图4所示,前支架301和中心线之间的夹角为10°,而后支架302和中心之间的夹角为16°。综合上述,在本实用新型中主要是通过设置应力弧贴片8以及优化前支架301和后支架302的不同步滑动来调整其与铰接件和投影点连线中心线的夹角来降低应力集中,从而为将曲柄连杆机构应用于大冲程的游梁式抽油机服务。以上实施例仅为本申请的示例性实施例,不用于限制本申请,本申请的保护范围由权利要求书限定。本领域技术人员可以在本申请的实质和保护范围内,对本申请做出各种修改或等同替换,这种修改或等同替换也应视为落在本申请的保护范围内。当前第1页12